Хитрости при сварке профильной трубы для начинающих
Хитрости при сварке профильной трубы для начинающихПрофильная труба очень популярный металлопрокат. Она используется для сборки самых различных металлоконструкций. А поскольку сварка признана одним из лучших способов соединения металлов, то, без неё никак не обойтись.
Какие трудности при сварке профильной трубы возникают? Во-первых, очень часто при нагреве профильную трубу ведёт намного больше, чем обычную, круглую трубу. В результате меняется геометрия всей конструкции, что приводит к серьёзным деформациям.
Во-вторых, на углах профильной трубы в месте сварочного шва возникает серьёзное напряжение, что нередко приводит к разрывам соединения. Также, просвет профильной трубы внутри может быть заплавлен металлом, и это важно учитывать, если нужно, чтобы изделие оставались пустотелым внутри.
Как правильно варить профильную трубу? Какими хитростями пользуются опытные сварщики?
Технология сварки профильной трубы
Само собой разумеется, что успех проделанной работы зависит не только от правильности выбора расходных материалов, настроек инвертора, и некоторых других особенностей сварки. Варить профильную трубу лучше на небольших токах, чтобы сильно не расплавлять металл. Ни о какой газовой сварке речи идти и не может, только ручная дуговая сварка.
Электроды можно использовать диаметром 2-3 мм. Для каждого из них выбирается свой определённый сварочный ток. Для электродов диаметром до 2 мм, значения сварочного тока должны быть не более 50 ампер. Если используются электроды 3 мм, то сварочный ток должен быть выше, но не более чем 100 ампер.
В большинстве случаев ток для сварки выбирается экспериментальным путём. Здесь все зависит не столько от инвертора, сколько от рабочего напряжения в электросети.
При этом многое зависит и от качества подготовительных работ. Поэтому для начала следует осуществить подготовку перед сваркой.
- Подогнать профильную трубу по размерам металлоконструкции.
Сделать подрезку и подгонку деталей. Резать трубу рекомендуется болгаркой или сабельной пилой, но никак не при помощи сварочного аппарата.
- Важно выровнять стыки профильных труб и максимально подогнать их. Обычно именно из-за этого и ведёт всю конструкцию. Также следует уделить должное внимание подготовке и очистке металла от ржавчины. Кромки труб должны быть ровными, а зазор между ними — минимальным.
- Только после этого свариваемые детали нужно уложить и зафиксировать точно так, как они и будут находиться в готовой конструкции.
Снимать струбцины или магнитные крепежи можно только после того, как сварка будет завершена, а стыки полностью остынут.
Хитрости сваривания профильной трубы
Итак, все подготовлено, и конструкция из профильной трубы уложена должным образом. Теперь можно приступать к свариванию деталей.
Для этого сначала:
Рекомендуется прихватить профильную трубу в нескольких местах, и только потом полностью обваривать. Обычно пяти точек на гранях вполне достаточно, чтобы зафиксировать конструкцию. Наплавляя металл в одном месте больше, а в другом меньше, можно добиться выравнивание деталей. Также, контролировать положение можно не слишком сильным постукиванием молотка по заготовке.
Затем необходимо проварить стыки профильных труб, таким образом, чтобы на них образовался ровный, и не слишком высокий валик из расплавленного металла.
При этом важно следить за тем, чтобы плавились лишь кромки заготовок, а металл не стекал вниз. Для этого ведём короткую дугу, таким образом, чтобы металл не слишком сильно расплавлялся. Сразу же разрываем её и постепенно двигаемся по стыку.
Если варится толстостенная труба, то, рекомендуется использовать сварку в несколько проходов. При этом второй проход следует выполнять в противоположном направлении предыдущему проходу.
Поделиться в соцсетях
Почему от сварки может искривиться и погнуться металл | Ручная дуговая сварка
Друзья всех приветствую. Сегодняшняя статья будет полезна тем, кто только начал знакомство со сваркой, или вот вот собирается это сделать. А рассмотрим мы такую важную и интересную тему, почему сварка тянет и деформирует металл. Многие хоть раз слышали такие выражения-потянуло от сварки, повело сваркой, почему это происходит?
Для наглядного примера мы возьмем несколько железок-два уголка толщиной 8мм, пластину 140 на 150мм толщиной 2мм и профильную трубу 20 на 40мм также толщиной 2мм. И на эти железки мы будем накладывать сварочные швы.
Для начала сварим толстые уголки и посмотрим что получилось. Мы видим, что если положить это сварное соединение на ровную плоскость трубы, то будет визуально видно, что эти уголки немного потянуло вверх в сторону сварочного шва.
Далее наложим несколько швов на пластину и посмотрим результат. Пластину закрутило и деформировало.
Теперь проведем эксперимент с профильной трубой. Наложим на ее поверхность со стороны 40мм пять поперечных сварочных швов. Глянем что будет? Даже такая вещь, как профильная труба изогнулась дугой вверх, по направлению к сварочным швам.
Все эти примеры произошли по таким причинам. Получилась усадка наплавленного металла. Простым языком это явление происходит таким образом-когда идет процесс сварки, сварочная ванна и уже сформировавшийся за ней шов имеют большую температуру. Затем расплавленный метал начинает остывать, становиться более плотным и резко уменьшаться в обьеме. Происходит растягивающие напряжения в соседних со швом частях металла. Говоря простым языком сварочный шов как бы стягивает к себе близкие участки металла-тянет одеяло на себя! Вот так в двух словах можно обьяснить это явление, из-за которого и происходят сварочные деформации.
Жалко испорченный кусок трубы? Мне тоже. И поэтому мы переворачиваем его вверх горбом и накладываем уже 6 швов-на 1 больше чам на противоположной стороне. Затем все швы шлифуем до основания трубы-конечно когда они остынут. И получилось чудо-наша труба вновь распрямилась и ее можно будет использовать на легких неответственных конструкциях. Мы использовали знание о деформации от сварки себе с пользой.
Мы не будем в рамках сегодняшней статьи описывать как избежать негативных последствий деформаций от сварки- эта тема обширна, и мы ее будем рассматривать в будущих статьях. Просто сегодня такой ликбез про деформации от сварки.
Надеюсь статья была полезной! Если ты решил самостоятельно осваивать Ручную дуговую сварку, то просто кликай на этот текст, чтобы перейти на главную страницу канала, где можно сразу подписаться и выбрать для себя наиболее интересные статьи!видео-инструкция как сварить своими руками, особенности калиток, ворот, цена, фото
Сварка профильных труб своими руками является куда более сложной задачей, чем это может показаться на первый взгляд. На самом деле даже человеку, хорошо владеющему сварочным аппаратом, придется очень постараться, чтобы получить надежную конструкцию, соответствующую заданным габаритам. Что уже говорить о новичках, которые только осваивают эту технологию?
Однако справиться с таким заданием все же можно, и кроме практики (без нее никуда!) для обеспечения приемлемого результата необходима фундаментальная теоретическая подготовка.
Монтировать такие детали можно несколькими способами
Особенности процесса
Плюсы профильной трубы
Преимущества материала позволяют возводить самые сложные конструкции
Достоинства профилированных стальных изделий в качестве сырья для сварных конструкций вполне очевидны:
- Во-первых, трубы производятся по стандартным размерам, что существенно облегчает их совмещение, особенно при торцевом соединении.
- Широкий ассортимент сечений позволяет подобрать детали для любой конструкции. Так что если мы захотим, например, сварить ворота из профильных труб, то без труда найдем элементы и для стоек, и для каркаса, и для заполнения.
- Еще один плюс – равномерная толщина металла
.Это очень важно именно при сварке, поскольку во много определяет надежность шва.
- Наконец, очень удобным является то, что работать нам придется с уже выровненной кромкой и достаточно гладкими поверхностями. При производстве профильной трубы существуют достаточно строгие допуски, и обычно отклонения не превышают долей миллиметра.
Обратите внимание!
Все эти преимущества характерны в первую очередь для изделий, которые были произведены в заводских условиях согласно ГОСТу и по установленному сортаменту.
Профильная труба кустарного изготовления (например, вальцованная из круглой заготовки) обычно имеет значительно большие отклонения по размерам, и потому при монтаже ведет себя непредсказуемо.
Комбинация круглых и профилированных деталей также возможна
Основные затруднения
Однако сам процесс сварки труб квадратного и прямоугольного сечения включает целый ряд нюансов:
- Во-первых, при нагреве изделия изменяется его конфигурация, зачастую куда сильнее, чем у круглой трубы. Часто это приводит к тому, что вся конструкция деформируется, причем направление и степень деформации определяется размещением и количеством сварных швов.
- Во-вторых, при торцевом соединении возможно образование областей повышенного напряжения на углах. Связано это со сложностью формирования на этих участках валиков из расплавленного металла и неравномерным прогревом.
- Кроме того, такая методика монтажа может привести к частичному перекрытию просвета трубы раскаленным и затем застывшим металлом. Если вам важно, чтобы детали оставались пустотелыми – учитывайте такую возможность.
Чтобы деталь не «повело», ее нужно фиксировать
Естественно, настоящих мастеров эти сложности обычно не останавливают. Так что после внимательного изучения технологии и отработки навыков на практике варить профиль можно «на ура».
Методика работы
Подготовка конструкций
Успех мероприятия во многом зависит от того, насколько качественно мы к нему подготовимся.
Перед тем, как сварить калитку из профильной трубы, стоит выполнить такие операции:
- Для начала подбираем детали с необходимой длиной и сечением. Подрезку по размеру стоит делать с помощью пилы по металлу, а не сварочного аппарата – так кромки получатся более ровными, и в дальнейшем нам будет куда проще с ними работать.
Станок для порезки
- Далее – выравниваем все трубы. Обычно именно на участках с кривизной деталь начинает «вести» при нагреве.
- После этого очищаем соединяемые участки от ржавчины, зачищая их до блеска либо металлической щеткой, либо шлифовальной машинкой.
- Если необходимо – выравниваем кромки таким образом, чтобы при совмещении двух элементов зазор был минимальным. Чем тщательнее будет проведена эта операция, тем меньше сил мы затратим собственно при сварке.
- Далее укладываем все элементы в том положении, в котором они будут находиться в готовой конструкции. При выполнении сварных работ желательно дополнительно фиксировать монтируемые детали, чтобы они не деформировались и не смещались относительно друг друга. Снимать фиксацию стоит только после остывания сварного шва.
Подготовка элементов конструкции
Дуговая сварка
Итак, детали готовы к работе, можно начинать их монтаж. И здесь могут использоваться две методики: электрическая или газовая сварка. Ниже мы подробно рассмотрим их обе.
Подбор оптимального электрода очень важен
Для электрической дуговой сварки нам понадобится сварочный аппарат. Цена подобных устройств довольно велика, потому стоит приобретать его лишь тогда, когда вы планируете работать с металлом более-менее регулярно. Для разовой работы желательно взять аппарат в аренду, тем более что возможностей для этого обычно хватает.
Следующий момент – подбор электрода и режима работы. Здесь на помощь придет такая таблица:
Толщина стенки трубы, мм | Диаметр электрода, мм | Ток на аппарате, А |
2 и менее | 1,5 – 1,6 | |
2 – 3 | 2 | 40 – 80 |
2 – 3 | 2,5 | 60 – 100 |
3 – 4 | 3 | 80 – 100 |
4 – 6 | 4 | 120 – 200 |
6 – 8 | 5 | 175 – 250 |
10 – 24 | 5 – 6 | 220 – 300 |
до 50 | до 8 | 300 – 400 |
Совет!
Данные значения носят рекомендательный характер, потому перед началом работы следует выполнить тестовую сварку на небольших отрезках трубы с целью проверки качества полученного шва.
Сам процесс соединения выполняем так:
- Детали фиксируем на сварочном столе или на вспомогательных приспособлениях.
- В нескольких местах выполняем точечную сварку, «прихватывая» трубы друг к другу. Обычно хватает фиксации в четырех – пяти точках на всех гранях трубы.
Точечная фиксация по углам
- После завершения прихватки контролируем положение деталей. При необходимости ударами молотка исправляем позиционирование.
- Далее начинаем проваривать стыки соединяемых труб, формируя на каждом валик из расплавленного металла, который затем оформится в виде сварного шва.
- При этом дугу ведем таким образом, чтобы кромки труб успевали расплавиться, но сам металл не проседал в полость изделия.
Работа на месте
- Толстостенные трубы свариваем в несколько приемов, постепенно соединяя все слои металла. При этом каждый следующий проход делаем в направлении, противоположном предыдущему: так мы обеспечим закрепление оптимальной структуры металла.
Совет!
После выполнения каждой операции контролируем геометрию изделия: длинные трубы обычно начинает «вести» именно после сваривания длинных швов, когда на поверхности металла формируются большие области напряжения.
Сварные швы (на фото) требуют зачистки
После завершения работы даем конструкции остыть, а затем приступаем к зачистке сварного шва. В дальнейшем эти участки требуют максимально качественной защиты от коррозии, поскольку металл, подвергнутый воздействию высоких температур, ржавеет значительно быстрее.
Газовая сварка
Инструкция по сварному соединению профильных труб с применением газовой горелки будет, естественно, довольно сильно отличаться:
Присадочные прутки
- Подготовку выполняем по той же схеме, что и при дуговой сварке.
- Перед началом работы покрываем все стыкуемые поверхности порошковым флюсом, который будет способствовать упрочнению шва.
- Готовим присадочную проволоку: оптимально, если по составу она будет совпадать с металлом, из которого изготовлена труба.
Далее начинаем соединение.
Делать это можно двумя способами:
- Для тонкостенных деталей подойдет шов «справа налево». При этом горелкой мы проводим по свариваемым кромкам, а проволоку-присадку подаем впереди горелки. За счет равномерного расплавления присадки и кромок обеспечивается формирование аккуратного и при этом надежного шва.
Схема движения пламени горелки справа налево
- Трубы со стенкой более 5 мм обрабатываем слева – направо. Пламя горелки направляем на сваренную зону, а присадку подаем за горелкой. В этом случае все процессы проходят гораздо быстрее, так что скорость работы возрастает. С другой стороны, шов получается не таким ровным и требует доработки после остывания.
Как и в случае с электросваркой, на каждом этапе контролируем положение деталей. Если отмечается хоть малейшая деформация, тут же выравниваем конструкцию и обеспечиваем более прочную фиксацию.
После остывания труб зачищаем швы абразивом и наносим на них антикоррозионное покрытие.
Вывод
Конечно, даже достаточно подробного ответа на вопрос о том, как варить профильную трубу, недостаточно для успешного применения знаний на практике. Чтобы результат вышел хотя бы удовлетворительным, стоит внимательно изучить видео в этой статье, а затем опробовать представленные там методики на небольших образцах, желательно под руководством опытного наставника. Только так вы сможете освоить данную технологию монтажа на достаточно высоком уровне.
Ферма из профильной трубы
Фермы из профильной трубы на загородных участках в основном используются для строительства всевозможных навесов. Они отличаются от других конструкций прочностью, долговечностью, небольшим весом, возможностью устройства перекрытий большой длины.
Строительные фермы можно купить уже готовые и собрать их на месте установки, но чаще всего они изготавливаются своими руками из металлического профиля. В этом случае вы можете сделать фермы любого размера, любой длины и количества элементов, и стоимость всей конструкции будет дешевле, чем если покупать готовые.
Недостатком изготовления ферм из профильной трубы своими руками является высокая продолжительность и трудозатратность работ. Нужно будет очистить от ржавчины, нарезать, приварить и покрасить большое количество металлических элементов.
На нашем загородном участке мы тоже решили сделать навес из поликарбоната. В качестве опор будем использовать металлические столбы, для усиления конструкции изготовим и приварим к ним фермы из профильной трубы.
Первым делом рассчитаем количество и размер профильной трубы, необходимой для изготовления опор навеса и самих ферм. Для стоек нам понадобится профиль размером 60 на 60 мм, для устройства верхнего пояса фермы — труба 40 на 40 мм, для раскосов и нижнего пояса – 20 на 40 мм. Толщину стенок трубы лучше использовать не менее 3 мм. Толстый металл легче сваривать, более тонкие стенки часто прожигаются насквозь, для их сварки требуется определённая сноровка.
Итак, часть металла купили на базе, другая часть у нас осталась от возведения забора. Садовым буром просверлим в земле отверстие на глубину 1 м, установим в него трубу нужной длины размером 60 на 60 мм, выровняем её по уровню и зальём цементным раствором, смешанным с щебнем.
Таким же образом установим ещё три столба. Всего забетонировали 4 опоры на одной стороне. Чтобы установить их на одинаковой высоте, мы использовали гидроуровень.
Отступим 2,5 м от первой линии столбов и установим ещё 4 опоры, только высотой на 50 см меньше предыдущих. Навес у нас будет односкатный, поэтому мы сделали первые стойки выше вторых. На этих опорах будет держаться крыша навеса. Чтобы крыша и стойки выдержали массу снега, который будет на ней собираться в зимний период, их необходимо усилить. Самый распространённый вариант для этих целей – сделать фермы и приварить их между столбами.
Переходим к изготовлению фермы. Параллельная четырёхугольная строительная ферма выглядит вот так.
Начнём с верхнего пояса. Возьмём трубу 40 на 40, отрежем её по длине, равной расстоянию между первым столбом и последним, и приварим электросваркой к верхней части каждой опоры. Верхний пояс готов.
Дальше используем профильную трубу 40 на 20, измерим расстояние между соседними стойками и отрежем её болгаркой. Отступим от верхнего пояса вниз 20 см и на этом уровне приварим кусок трубы к опорам, расположив её плашмя. Если нет помощника, один конец трубы можно закрепить, поставив под него подпорку, а второй держать свободной от держака сварочного аппарата рукой. Горизонталь нижнего пояса проконтролируем строительным уровнем.
Так же приварим ещё две профильные трубы между опорами.
Теперь между верхним и нижним поясами фермы нужно приварить раскосы. Именно за счёт них достигается прочность конструкции. Если стропила положить просто на верхний пояс, без фермы, то под тяжестью снега труба деформируется и навес разрушится.
Раскосы привариваются между поясами под углом 45 градусов. Сначала возьмём транспортир и определим угол наклона, сделав на трубе отметку. Потом прислоним к этому месту кусок трубы 20 на 40 и проведём на нём карандашом в месте предполагаемого реза. Болгаркой отрежем лишний металл.
По такому шаблону сделаем нужное число отрезков.
Нам осталось приварить их к поясам фермы. Сначала раскосы прихватывается к трубам небольшими точками, чтобы они держались на конструкции.
Лучше начать сваривать их с двух сторон попеременно. Когда прихватили все трубы, после этого их можно обваривать со всех сторон. Делается это для того, чтобы ферму не повело и она не изменила своих геометрических свойств. Особенно важно соблюдать эту последовательность, если вы свариваете ферму на земле и её пояса жестко не закреплены между опорами.
Соседние раскосы располагаются друг от друга на небольшом расстоянии. По их середине проводят условные линии, эти линии должны пересекаться в высшей точке верхнего пояса и низшей нижнего.
Приварим раскосы между всеми опорами будущего навеса. Работа эта кропотливая и долгая по времени. Но научиться варить металл самому необходимо: во-первых, это умение всегда пригодится в ведении домашнего хозяйства, а во-вторых, вы сэкономите большую сумму денег, ведь профессиональные сварщики берут оплату за каждый шов. Представьте, какое количество сварных швов нужно сделать при изготовлении строительной фермы и сколько это будет стоить.
Первая ферма для навеса готова. Точно так же начнём делать вторую ферму. Здесь тоже сначала приварим верхний пояс.
По совету бывалых сварщиков вместо упоров для поддержки одной стороны трубы удобнее использовать струбцину. Маску сварщика лучше купить с автоматическим затемнением, особенно начинающим.
В итоге, после продолжительной работы, у нас получилось 2 строительные фермы для навеса.
Крышу мы будем устанавливать на деревянные стропила, уложив их на стойки с фермами. Чтобы прикрепить доски к верхнему поясу, мы используем металлические уголки. Возьмём кусок уголка с толщиной стенки 4 мм и болгаркой нарежем его на несколько коротких отрезков.
Дрелью просверлим в них по два отверстия.
Приварим уголки к верхним поясам ферм через 60 см друг от друга. В последствии, установив стропила, мы прикрутим их двумя саморезами к каждому уголку.
Опоры с фермами под навес готовы, осталось покрасить их краской для металлических поверхностей.
Когда краска высохнет, приступим к устройству обрешётки под поликарбонат. Если статья понравилась, поделитесь ей в соцсетях.
ВИДЕО
Приспособления для сварки под прямым углом, острым или тупым
От качества сварочных работ зависит надежность металлических конструкций. Поэтому предусмотрены государственные стандарты, которые регулируют сварочные процессы.
Например, ГОСТ 23518-79 определяет, какими должны быть соединения деталей, сваренных в среде защитных газов, каким образом производить сварку под острым или тупым углом. В зависимости от используемого газа, типа электрода, присадки, устанавливаются требования к процессу сварки.
Для соблюдения технологии применяют приспособления, которые не дают деталям изменить свое положение, облегчая работу сварщика. Такие приспособления помогают выдерживать прямой угол или любой другой.
Наклон электрода
Чтобы сварить детали под прямым или острым углом, необходимо уметь правильно перемещать электрод. В процессе сварки конец электрода расплавляется вместе с обмазкой, которая выделяет защитные газы и частично превращается в шлак, также защищающий сварочную ванну от атмосферного кислорода.
Необходимо обеспечивать постоянное покрытие ванны жидким шлаком, иначе не получится качественный сварочный шов. Металл в жидком состоянии должен находиться не менее трех секунд, которые требуются для выделения вредных газов.
При этом необходимо перемещать электрод вдоль шва, делая сложные вращательные или зигзагообразные движения концом электрода. Добиться такого контроля над сваркой можно только при правильном угле наклона электрода. Но угол наклона нужен не только для контроля хода сварки. С помощью него можно воздействовать на характеристики сварного шва.
Сварка углом вперед делает глубину провара меньше, в то время как ширина увеличивается. Это можно использовать при сварке металлов малой толщины. При этом способе кромки хорошо проплавляются, скорость сварки повышается.
При сварке углом назад провар становится глубже, а шов выше, но ширина уменьшается. Кромки прогреваются недостаточно, поэтому вероятны непровар и образование пор.
Но умение варить недостаточно для получения качественного сварного шва. Иногда требуется определенное его положение в пространстве, чтобы получился добротный шов.
А это достигается применением особых приспособлений, которые фиксируют свариваемые детали в пространстве так, как необходимо сварщику. Например, при электрошлаковой сварке требуется располагать шов вертикально.
При производстве сварочных работ очень часто требуется закрепить соединяемые детали между собой так, чтобы сварщик мог сделать свою работу. Если изделия тяжелые, сложной формы, то без специальных приспособлений не обойтись.
В небольших мастерских распространение получили устройства универсального типа, способные фиксировать собранное изделие перед сваркой и менять его положение в процессе работ. Они бывают установочные и закрепляющие.
Установочно-закрепляющие механизмы
Более практичны в использовании механизмы, которые выполняют сразу обе функции – закрепляют и устанавливают заготовку в необходимом положении. При этом деталь просто устанавливают в приспособление и зажимают. Дальше идет сваривание заготовок.
Наиболее простое устройство по конструкции – это приспособление для сварки перпендикулярно соединяемых изделий. Основу устройства монтируют на сварочном столе.
Если это большие изделия, то изготавливают решетчатую раму и располагают ее в горизонтальной плоскости. На ее поверхности укладывают свариваемые изделия под прямым углом друг к другу. Для этого на плоскости имеются направляющие в виде уголков.
Если требуется сварить под прямым углом одно или несколько изделий, то можно их зафиксировать с помощью винтовых фиксаторов (струбцин). Любые соединения под прямым углом проще начать варить на сварочном столе.
При укладке на стол получают гарантировано правильное расположение деталей в одной плоскости. Угловая прямоугольная струбцина помогает выдержать прямой угол между деталями. Детали прихватывают в нескольких местах сваркой, после чего целое изделие можно повернуть так, как нужно для следующей операции.
При сваривании объемных изделий необходимо делать поворотные фиксаторы,. Это ускоряет монтаж и выемку изделия.
Самодельный фиксатор
Если заготовки небольшие, то приспособление для закрепления их под углом 90 ° можно сделать самостоятельно из подручного материала. Нужно взять металлический уголок, полоса (два отрезка) и две струбцины. Чтобы выставить прямой угол, нужен будет угольник, другой инструмент не потребуется.
Длина уголков может быть любой. Полоса приваривается под углом 45 градусов к каждому уголку таким образом, чтобы они образовывали равнобедренный прямоугольный треугольник.
Причем уголки (катеты) до вершины треугольника не доходят на несколько сантиметров. Это позволит в дальнейшем спокойно варить стержни или профильные трубы в месте стыка. Если нужно, то к уголкам можно приварить и струбцины. Они будут жестко фиксировать свариваемые изделия.
Для того чтобы конструкцию не повело, сначала необходимо прихватить ее в четырех местах и только затем проваривать полностью. Полученное приспособление при закреплении его на столе прослужит не один год.
Применение магнитов
При сварке в домашних условиях удобно пользоваться магнитными фиксаторами. Они бывают электромагнитными и на основе постоянных магнитов. Электромагниты применяются больше на производстве. Для бытовых нужд и мелких производств удобны фиксаторы на постоянных магнитах. Они компактны, могут устанавливаться где угодно, некоторые имеют переменный угол фиксации.
Наиболее простыми по конструкции и распространенными являются магнитные угольники. Достаточно приложить угольник к свариваемой детали одной плоскостью, и соответственно расположить вторую деталь, чтобы получить надежное закрепление под прямым углом.
Остается прихватить детали в нескольких местах. После этого полностью приваривают изделие. Без прихватки магнитные угольники не выдержат температурных деформаций при сварке.
Кроме угольников существуют универсальные магнитные приспособления. Они могут фиксировать свариваемые изделия во многих положениях.
Как пример, можно рассмотреть устройство MagTab. Приспособление имеет две основные плоскости с магнитами. Угол между плоскостями меняется, поэтому приспособление можно закрепить на цилиндрической, ровной поверхности или в любом углу.
Предусмотрено еще две плоскости, к которым крепят детали. Плоскости расположены под прямым углом и имеют возможность смещаться относительно основания. Это дает возможность устанавливать свариваемое изделие в том положение, которое необходимо.
Если есть в наличие мощные постоянные магниты, особенно из неодима, то можно самостоятельно сделать подобные устройства. При использовании магнитных фиксаторов нужно учитывать, что они теряют свою силу под воздействием высокой температуры, поэтому нужно избегать их перегрева.
Соединение труб
Сварочные работы часто используют, когда нужно соединить трубопроводы. При этом нередко возникает вопрос, а как приварить одну трубу к другой трубе перпендикулярно.
Если используются профильные трубы прямоугольного или квадратного сечения, то все очень просто. В месте соединения, в той трубе, к которой будет приварена другая, необходимо сделать вырез под сечение врезаемого изделия.
После этого их нужно установить в угловую струбцину и зажать винтом, или в любое другое приспособление, обеспечивающее перпендикулярное соединение деталей. Затем производится прихватка в нескольких местах и потом только проваривается все вкруговую.
При сварке круглых труб все происходит точно так же. Только дополнительно в торце привариваемой трубы делают вырез с радиусом, совпадающим с радиусом основной трубы. Это обеспечивает хороший стык, что позволит получить качественный шов.
Для соединения под прямым углом пластиковых труб часто применяют переходники. Деталь так и называется – угол 90 °. Она позволяет быстро и легко обеспечить точность угла поворота.
5 полезных идей для сварщика
Выполняя сварку нужно добиваться надежности, точности и аккуратности соединения. Рассмотрим 5 идей, пользуясь которыми удастся достигнуть максимально качественного результата.
Сварка труб разного диаметра под прямым углом
Если нужно приварить под прямым углом к торцу толстой трубы тонкую, следует отметить маркером на большей из них примыкание меньшей.

Затем на ней делается фигурный вырез по разметке.
Полученные в результате рожки прорезаются вдоль на несколько сегментов.
После такой подготовки вкладывается тонкая труба, и сегменты загибаются ударами молотка, обжимая ее.
Далее они завариваются, как и стык между трубами.
В результате получается очень надежное и аккуратное соединение. Данным способом можно воспользоваться при сварке уличного турника, брусьев и т.д.
Изгиб П-образного профиля или швеллера
При необходимости согнуть П-образный профиль нужно разрезать его боковую сторону в точке изгиба, затем сделать еще 2 таких же разреза с шагом равным его ширине.
Далее профиль переворачивается дном кверху, и его центральный разрез удлиняется до второй боковины. После этого нужно вырезать диагональ, как на фото, и согнуть его. Этим способом можно сгибать как небольшой швеллер, так и оцинкованный профиль для монтажа гипсокартона.
Соединение деталей на электрозаклепки
При сваривании различных деталей, особенно тонкостенных, чтобы металл не повело вместо сплошного шва можно делать точечную сварку. Для этого в одной из деталей сверлится минимум 2 сквозных отверстия.
Подготовленная деталь прикладывается по месту, и приваривается электродом через отверстия. В результате получается некоторое подобие заклепок. Такое соединение практически исключает, что деталь поведет при сварке, к тому же оно вполне надежное.
Самодельная малка
Чтобы точно переносить величину углов из одной конструкции на свариваемые заготовки используется специальный инструмент малка. Обычно такое приспособление крайне хлипкое, поэтому лучше его сделать самому, чем покупать. Для этого берется 2 одинаковых отрезка стальной полосы и маленькая вставка из нее же, но срезанная с одной стороны под углом.
Вставка размещается между двумя заготовками, и они свариваются между собой. Далее из полосы делается линейка с продольным пропилом посредине.
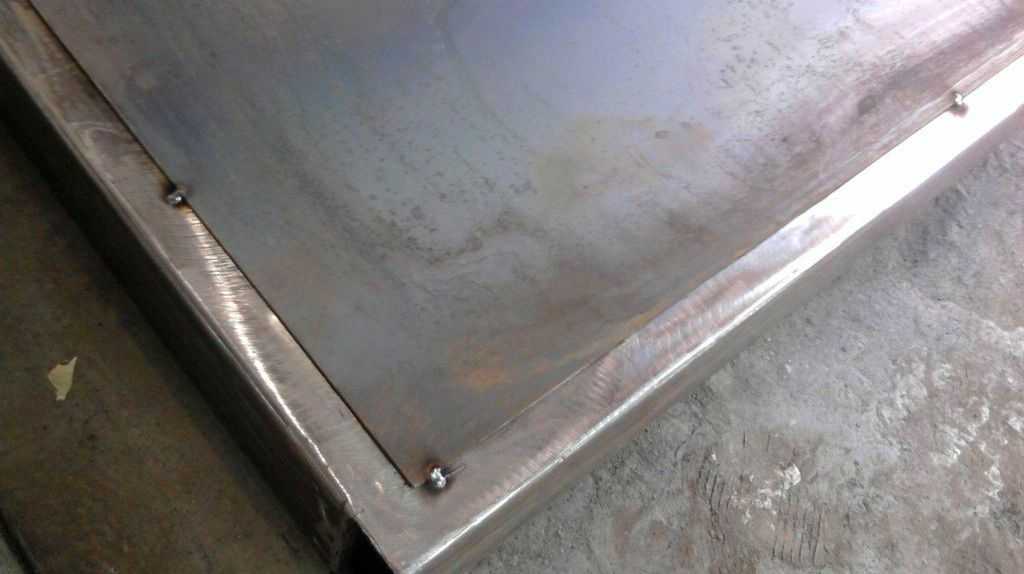
Для использования малки нужно ослабить гайку, выставить стороны под нужный угол, уперевшись в него, после чего зажать ее обратно. Далее инструмент применяется как шаблон.
Надежное соединение полосы и трубы под прямым углом
Чтобы приварить полосу к трубе нужно сначала прорезать в ней болгаркой паз соответствующей длины и ширины.
Затем в него вставляется полоса и обваривается. При таком соединении ее уже не вырвет под нагрузкой.
Смотрите видео
Деформации при сварке и способы их избежать
Деформации при сварке и способы их избежатьЧтобы вы не варили, толстый уголок или тонкую профильную трубу, во время сварки на металл воздействуют большие температуры. Вследствие этого металл может повести, простыми словами деформировать.
Особенно деформации подвержены тонкостенные изделия из металла и некоторые виды сталей. Меры по предотвращению деформаций при сварке могут быть разными, как и их эффективность в целом.
Как избежать деформаций при сварке
Сварка — это всегда высокая температура, которая заставляет металл плавиться. Однако тепло, которое используется для расплавления сварочной ванны, уходит далеко за её пределы. И если металл тонкий или его надежно не закрепить, то возможно появление деформаций.
Одним из самых эффективных способов, который позволяет избежать деформации при сварке, это сварка в так называемых «кондукторах». Кондукторы для сварки, это специальные приспособления, которые дают возможность жестко зафиксировать свариваемое изделие.
При этом важно учитывать ожидаемую деформацию металла в зоне нагрева. Если металл повело в одну сторону, достаточно начать варить с другой, чтобы его выгнуло обратно. Такой способ подхода даёт возможность заранее предугадать появление деформации, и использовать метод предварительного (обратного) изгиба.
Как варить широкие листы металла, чтобы не повело
Наиболее предпочтительный способ, в данном случае, это предварительный изгиб листов металла, в противоположную сторону деформации. Точно таким же способом предотвращают деформации при сварке тавровых, а также двутавровых соединений.
Немного иным способом, является техника обратноступенчатой сварки. В данном случае сварное соединение осуществляется в два слоя, и каждый из них выполняется в разных направлениях. Например, первый шов накладывается слева направо, а второй сварочный шов, наоборот.
Простыми словами, каждый последующий слой наплавленного металла должен вызывать противоположное напряжение от предыдущего слоя. Кроме всего перечисленного, существуют и иные приемы отвести излишнее тепло из зоны сварки.
Например, отвод тепла струёй воды или при помощи медных подкладок. При этом важно понимать, что воду для охлаждения металла во время сварки можно использовать не во всех случаях. При сварке некоторых изделий, быстрое охлаждение металла может только усугубить положение, и привести к большим проблемам, чем деформация.
Самым распространенными являются холодные трещины, которые появляются из-за резкого охлаждения сварного шва. Поэтому к данной рекомендации нужно относиться осторожно.
Не менее действенным способом избежать деформаций, является предварительный прогрев заготовок перед сваркой. В таком случае получится избежать резкого перепада температур. В любом случае, следует знать, что если сварка ведётся при пониженной температуре, то прогрев металла перед свариванием является обязательной процедурой.
Ну а если деталь и повело, конечно же, не слишком толстую, до 3 мм толщиной, то ее выравнивание выполняют при помощи молотка. Что же касается изделий большей толщины, то их ровняют посредством гидравлического пресса.
10 советов, которые могут улучшить ваши сварочные навыки
Этот краткий курс практических указателей адаптирован к потребностям любой фермы в ремонте металла.
1. Режимы Glob или Spray для толстой стали
Большинство фермеров могут не осознавать, что регулировка напряжения, силы тока и скорости подачи проволоки на сварочных аппаратах может обеспечить режимы передачи, точно настроенные для толстого металла. По словам Карла Хоэса из Lincoln Electric, ограничивающим фактором для режимов шарового или распыления является то, что они могут использоваться только на «металле толщиной ⅛ дюйма и толще и только при выполнении плоских и горизонтальных угловых швов».
Шаровая передача (короткая дуга): Напряжение, сила тока и скорость подачи выше, чем в стандартном режиме короткого замыкания. Это приводит к тому, что большие шарики проволоки выходят из конца проволоки и попадают в сварочную ванну. Этот режим обеспечивает сварку глубокого проплавления на толстом материале, но при этом образуется много брызг.
Распылительная дуга: Вольты, токи и скорость подачи проволоки выше, чем в шаровом режиме. Он производит поток крошечных капель расплава, которые разбрызгиваются по дуге от проволоки к металлу.Для истинного распыления вам потребуется газ, богатый аргоном. Распылительная дуга позволяет использовать проволоку большого диаметра, поэтому осаждается много металла, и получается бусинка великолепного вида. Его можно использовать только для плоских или горизонтальных угловых швов; лужа очень жидкая. Обязательно замените сопло вашего пистолета на устройство длиной около 3 дюймов или больше.
2. Очистить от примесей
«Фермеры обычно не могут должным образом подготовить металл перед сваркой», — говорит Джон Лейснер из Miller Electric.«Это включает удаление краски, ржавчины, грязи и других поверхностных загрязнений, но это также означает шлифовку трещин». Лейснер легко понимает, что подготовка металла — это последнее, о чем вы думаете, когда требуется ремонт сварного шва в разгар сезона или во время кормления скота.
«Я не говорю, что зона ремонта должна быть абсолютно нетронутой», — говорит он, добавляя, что сварные швы алюминия являются исключением (см. Совет № 6 по сварке алюминия). «По крайней мере, ударьте по месту ремонта проволочной щеткой с электроприводом, чтобы удалить ржавчину и грязь.”
Очистка удаляет загрязнения, которые попадают в металл во время сварки; если они останутся, они поставят под угрозу ремонт. Если очистка невозможна, избегайте ремонта с помощью сварочного аппарата MIG. «Используйте сварочный аппарат и стержень 6011. Кроме того, снизьте скорость движения. Это дает время пузырькам газа выкипеть из расплавленного сварного шва до того, как эти примеси улавливаются внутри сварного шва », — говорит он.
Водород сварочный враг №1
Водород — это наихудшая примесь, разрушающая сварные швы.Поскольку водород повсюду (в воде, грязи, ржавчине, краске, навозе, смазке), он представляет собой серьезную проблему для сварщиков. Что можно сделать, чтобы сбить водород? Чистый, чистый и еще чистый. «Водород, наряду с высоким остаточным напряжением и чувствительной к трещинам сталью, может привести к растрескиванию через несколько часов или дней после сварки», — говорит Хоуз из Lincoln Electric. «Высокопрочные стали (обычно используемые в почвообрабатывающих орудиях), толстые металлические секции и ограниченные детали более подвержены водородному растрескиванию».
3.Правила угла, направления и скорости
Одним из удивительных аспектов сварки является то, что даже начинающий сварщик может добиться успеха. Однако Хоуз и Лейснер предупреждают, что существуют некоторые жесткие правила, обеспечивающие длительный ремонт сваркой.
Тяни или толкай: Здесь правило простое. «Если при этом образуется шлак, вы тянете», — говорит Лейснер. Другими словами, вы перетаскиваете стержень или проволоку при сварке с помощью устройства для сварки стержневой или флюсовой проволокой. В противном случае вы будете проталкивать проволоку сваркой в среде инертного газа (MIG).
Рабочий угол: При сварке проволокой держите пистолет под углом от 10 ° до 15 ° в направлении, в котором продвигается сварной шов. При сварке штангой поддерживайте угол подъема от 20 ° до 30 ° в направлении протягивания. При сварке углового (тройникового) шва держите пруток или проволоку (независимо от процесса сварки) под углом 45 ° между двумя металлическими частями.
Расстояние между дугами: Отрегулируйте скорость движения так, чтобы сварочная дуга оставалась в пределах одной трети сварочной ванны. Для сварки проволокой (сердечник или MIG) соблюдайте рабочее расстояние от до ½ дюйма.При сварке штангой соблюдайте расстояние ⅛ дюйма между концом стержня и заготовкой. «Длина дуги не должна превышать диаметр сердечника электрода», — говорит Лейснер.
Скорость: Наблюдайте за сварочными лужами и гребнем (где затвердевает расплавленный металл). По словам Хоэза, при сварке проволокой (MIG или флюсовой сердцевиной) гребень должен находиться примерно на дюйма позади проволочного электрода. При слишком низкой скорости движения образуется широкий выпуклый борт с неглубоким проникновением, что также приводит к отложению слишком большого количества металла.С другой стороны, слишком высокая скорость перемещения создает неглубокий сварной шов, который дает узкий и сильно выпуклый валик. Большинство скоростей движения для различных шарниров значительно ниже 40 дюймов в минуту.
4. Выбор газа MIG
Для сварки MIG предпочтительным надежным защитным газом является 100% углекислый газ (co²). Он экономичен и позволяет получать сварные швы с глубоким проваром.
Тем не менее, есть время инвестировать в более дорогие защитные газы, которые включают:
- 75% аргона и 25% co² для получения красивых сварных швов (при 100% co² образуется много брызг) и для сварки при высоких значениях силы тока.
- 85% аргона и 15% co² для сварки толстолистовой стали или металла с большим количеством прокатной окалины или ржавчины.
- 90% аргона и 10% co² для сварки распылением, а также для тяжелых или толстых металлических секций.
- 100% аргон или смесь аргона и гелия для сварки алюминия.
- 90% аргона, 7,5% гелия и 2,5% co² для сварки нержавеющей стали.
5. Список покупок сельскохозяйственных электродов
Множество проданных проводов и стержней затрудняет выбор электродов.Лейснер и Хоуз приводят этот список покупок сельскохозяйственных электродов, которые подходят для большинства ремонтных работ.
Проволока для сварки MIG: Хороший общий диаметр проволоки для сварки MIG составляет 0,035 (наиболее распространенный) или 0,045 дюйма. Но учитывайте 0,025 дюйма при сварке тонких материалов толщиной дюйма или меньше. Причина в том, что проволока меньшего диаметра обеспечивает более стабильную сварку при меньшем токе, что обеспечивает меньшую силу дуги и меньшую склонность к прожиганию металла.
Проволока с флюсовым сердечником: Одной из самых популярных проволок с флюсовым сердечником является E71T-1, поскольку «она хороша для сварки в нерабочем положении (вертикальная, потолочная), обеспечивает быстрое застывание шлака и высокую скорость наплавки», — говорит Лейснер.«Если вы выполняете сварку в неправильном положении (потолочный сварной шов), вы можете использовать проволоку E71T-8», — говорит Хоуз. Если вы свариваете металл с покрытием или оцинкованный металл (например, ножку с зернистостью), используйте проволоку E71T-14, потому что у нее есть сердечники, которые взрываются в дуге. Это приводит к улетучиванию стальных покрытий, таким образом, сводя к минимуму растрескивание и пористость сварных швов. Все эти проволоки обеспечивают более высокую производительность наплавки, чем стержневые электроды, и их шлак удаляется легче.
Электрод-стержень: Пруток общего назначения — это электрод 6011, говорит Лейснер, поскольку он обеспечивает хороший проникающий сварной шов. По его словам, для более толстого материала, который «требует более глубокого проплавления, используйте электрод 6010».
«Если вы свариваете более тонкую заготовку там, где вам нужно меньше проплавления, перейдите на электрод 6013». Самый распространенный размер стержня — ⅛ дюйма. «Используйте стержень большего диаметра для более толстого металла и стержень меньшего диаметра для более тонкого металла», — советует Хоуз.
6. Сварка алюминия
Растущее присутствие алюминия в сельскохозяйственном оборудовании вызывает необходимость ремонта металла.Хорошая новость заключается в том, что любой сварщик может обрабатывать алюминий, и этому процессу относительно легко научиться. Но есть некоторые правила, которым вы должны следовать, — говорит Хоуз. Эти правила включают:
Купите приводные ролики с U-образной канавкой, которые поддерживают проволоку, но не сминают ее. Держите регулировку ведущего ролика на незакрепленной стороне.
Замените прокладку кабеля на тефлоновую, нейлоновую или аналогичную прокладку.
Используйте только аргон или аргон-гелий.
Выберите алюминиевую присадочную проволоку диаметром 3/16 или 1/6 дюйма.Эти большие провода легче протянуть вниз по кабелю пистолета.
Используйте контактный наконечник примерно на 0,0115 дюйма больше диаметра проволоки.
Удалите жир, масло, навоз или грязь с помощью органического растворителя, такого как ацетон, слабого щелочного раствора, такого как сильное мыло, или обезжиривателя на основе цитрусовых. Избегайте сильных щелочных или кислотных чистящих средств.
Почистите ремонт, используя новую проволочную щетку из нержавеющей стали (используется только при сварке алюминия), чтобы удалить окисленный алюминий, который естественным образом появляется на поверхности металла.Оксиды алюминия плавятся при 3700 ° F, в то время как основной металл плавится при 1200 ° F. Оксиды на ремонтной поверхности препятствуют проникновению присадочного металла.
Разогрейте ремонт до 230 ° F. чтобы минимизировать растрескивание. Делайте прихваточные швы в начале и в конце ремонта, чтобы облегчить предварительный нагрев и предотвратить деформацию.
Используйте короткий пистолет и прямой кабель. Если вы много занимаетесь сваркой алюминия, подумайте о покупке пистолета для катушки.
Вдавите в сварной шов, чтобы уменьшить загрязнение и улучшить покрытие защитным газом.
Сварка горячая и быстрая, используя более высокие значения силы тока и напряжения, а также скорости хода сварного шва, чтобы предотвратить прожог.
Заполните кратер сварного шва в конце сварного шва. Кратеры — основная причина растрескивания сварных швов алюминия, предупреждает Хоуз. Чтобы заполнить кратер, продолжайте подавать проволоку в конце сварного шва, изменив направление движения назад над сварным швом примерно на 1 дюйм.
7. Секретарь ремонта высокопрочной стали
.
По словам Хоэза, производители все чаще обращаются к использованию трудно свариваемых металлов, таких как высокопрочная сталь, особенно в почвообрабатывающих орудиях, чтобы уменьшить их вес.При ремонте высокопрочной стали очень важно подготовиться, предварительно удалив всю ржавчину, краску, жир и влагу, чтобы добраться до оголенного металла. Затем перед сваркой предварительно нагрейте место ремонта.
«Чем выше содержание углерода в стали (обычно используется в высокопрочных сталях), тем больше требуется предварительного нагрева», — говорит Хоуз. «Предварительный нагрев необходим для предотвращения растрескивания после сварки». При ремонте высокопрочных сталей используйте электрод с малым диаметром и низким содержанием водорода, например стержень 7018, добавляет Лейснер.Наконец, сохраняйте низкую скорость сварочного хода; это сохраняет сварочную ванну в расплавленном состоянии, давая возможность пузырькам газообразного водорода закипеть. В результате получается более качественный сварной шов.
8. Почему трескаются сварные швы?
Hoes говорит, что сварные швы трескаются по одной или нескольким из следующих причин:
- Перед сваркой не зашлифовать трещины до дна.
- Формование бусин меньшего размера. Сварные швы всегда должны быть немного шире, чем глубина.
- Формирование вогнутых или полых бусинок.Такие сварные швы могут привести к растрескиванию середины валика. Сварные швы всегда должны быть выпуклыми или горбатыми.
- Неспособность правильно очистить ремонт. Если после ремонта оставить ржавчину, краску, жир, грязь или влагу, в сварной шов попадет водород, который может вызвать растрескивание.
- Без предварительного нагрева перед сваркой. Это особенно необходимо, когда свариваемая сталь имеет более высокое содержание углерода или сплава.
- Избегайте использования электродов с низким содержанием водорода для ремонта трудно свариваемых сталей (с высоким содержанием углерода или сплава).
- Невозможность заполнить кратеры в конце сварного шва.
- Неправильное усиление ремонта сварного шва.
- Не накладывать первый валик на многопроходные сварные швы достаточного размера, плоской или выпуклой формы. Это препятствует растрескиванию до тех пор, пока не будут добавлены более поздние бусинки для поддержки.
Лейснер говорит, что жесткие детали более склонны к растрескиванию. Если возможно, приваривайте к свободному концу таких деталей и оставляйте зазор 1/32 дюйма между пластинами для свободного движения усадки при остывании сварного шва.Очистите каждую бусину, пока она еще горячая, чтобы снять напряжение.
9. Сварка вне позиции
Гравитация — ваш враг при работе вне позиции, поэтому противодействуйте ее эффектам (особенно при сварке проволокой), используя немного меньшее напряжение и меньшую скорость подачи проволоки, чтобы создать меньшую лужу, — говорит Хоуз. По словам Лейснера, изменение полярности на противоположную для концентрации тепла на кончике электрода приводит к более холодной сварке, что позволяет сварочной ванне остывать быстрее и предотвращать ее стекание. Вот еще несколько советов от обоих экспертов по сварке в нерабочем положении:
Горизонтальные сварные швы: Уменьшите рабочий угол до 0 ° или 15 °, а затем продолжайте сварку в стабильном темпе, чтобы сварочная ванна оставалась на месте.
Вертикальные сварные швы: Сварку из стали толщиной 3/16 дюйма и более выполняйте нисходящим движением. Однако это движение может быть проблемой; сварочная ванна может опередить дугу и стать изолятором, уменьшая проплавление. На стали толщиной 1/16 дюйма и более сваривайте восходящим движением из стороны в сторону, перемещая дугу справа в центр, а затем влево, чтобы создать треугольник.
Сварные швы над головой: Уменьшите силу тока и двигайтесь быстро, чтобы сварочная ванна оставалась узкой.Используйте круговые движения и взмахи, чтобы сварочная лужа не вылилась из сварного шва.
10. Когда усиливать
Усиление ремонта сваркой «определенно необходимо, если трещина находится в месте, где вы не можете подготовить ее поверхность для сварки», — говорит Лейснер. «Всегда укрепляйте точки, подверженные высоким нагрузкам, например, петли складного оборудования».
Усиление также необходимо, если деталь сломалась более одного раза в том же месте или рядом с тем же местом, что и предыдущий ремонт, добавляет Хоуз.
При армировании обязательно скосите кромки под углом 30 °, где новый металл встречается со старым. Это обеспечивает лучшее проплавление.
Для более тяжелых участков материала оставьте небольшой участок (пространство) внизу стыка. Для этого сначала скосите края, а затем отшлифуйте нижнюю часть скоса до толщины никеля.
Вот последний совет по усилению. «Материал толщиной более дюйма обычно следует сваривать за несколько проходов», — говорит Лейснер.
Наконечники для размагничивания трубы, чтобы сделать возможной сварку
В: Мы обнаружили, что некоторые трубы, прибывшие на строительную площадку, не выдерживают сварного шва, потому что они намагничены. Как лучше всего размагнитить трубу, чтобы можно было ее сварить?
A: Это довольно распространенная проблема, которая возникает, когда отрезки трубы сталкиваются друг с другом в процессе транспортировки. Магнетизм приводит к возникновению магнитной дуги — явления, которое возникает при сварке постоянным током (DC), когда дуга тянется к одной стороне сварного соединения во время корневого прохода.Это отклонение дуги часто может быть серьезным и вызывать дефекты сварного шва, которые необходимо устранить.
У вас есть несколько вариантов, если вы подозреваете, что ваш материал намагничен. Можно полностью удалить магнетизм, но для этого потребуется дорогостоящее оборудование. Вы также можете определить степень магнитного притяжения с помощью манометра, прежде чем размещать катушку размагничивания вокруг трубы, но этот тип оборудования не всегда может быть доступен.
Один из распространенных методов, которые я использовал на трубопроводах в нефтегазовой промышленности, — это создание магнитной катушки с рабочим кабелем.Я оборачиваю кабель вокруг трубы три-шесть раз, примерно на половину диаметра трубы от сварной канавки на противоположной стороне от направления дуги. Затем я кладу от нескольких to до 1 дюйма. прихваточные швы вокруг сварного шва. Используя ток в нижнем диапазоне рекомендованного, я делаю корневой проход с короткой длиной дуги в зависимости от размера и типа моего электрода. Если дуга все еще возникает, я пытаюсь намотать рабочий кабель в противоположном направлении.
Наконец, поскольку дуга возникает при сварке постоянным током, попробуйте переключиться на переменный ток (AC), чтобы нанести начальный сварной шов.Затем снова переключитесь на постоянный ток для оставшейся части сварного шва.
Какой бы метод вы ни использовали, обязательно обращайте пристальное внимание на сварочную ванну, поддерживайте короткую длину дуги и удаляйте все отложения шлака после каждого валика. Вы — первая линия проверки и должны знать о качестве своей работы.
Руководство по сварке алюминия: советы и методы
Алюминий — легкий, мягкий, малопрочный металл, который легко лить, ковать, обрабатывать, формовать и сваривать.
Если он не легирован специальными элементами, он подходит только для низкотемпературных применений.
Алюминий легко соединяется сваркой, пайкой и пайкой.
Во многих случаях алюминий соединяют с другими металлами с помощью обычного оборудования и технологий. Однако иногда может потребоваться специальное оборудование или методы.
Сплав, конфигурация соединения, требуемая прочность, внешний вид и стоимость являются факторами, определяющими выбор процесса.У каждого процесса есть определенные преимущества и ограничения.
Цвет
Алюминий имеет цвет от светло-серого до серебристого, очень яркий при полировке и тусклый при окислении.
Характеристики
Излом в алюминиевых профилях показывает гладкую яркую структуру. Алюминий не дает искр при испытании на искру и не показывает красный цвет до плавления. На расплавленной поверхности мгновенно образуется тяжелая пленка белого оксида.
Алюминий легкий и сохраняет хорошую пластичность при отрицательных температурах.Он также обладает высокой устойчивостью к коррозии, хорошей электрической и теплопроводностью, а также высокой отражательной способностью как к теплу, так и к свету.
Чистый алюминий плавится при 1220ºF (660ºC), тогда как алюминиевые сплавы имеют приблизительный диапазон плавления от 900 до 1220ºF (482-660ºC). При нагревании до диапазона сварки или пайки цвет алюминия не меняется.
Сочетание легкости и высокой прочности делает алюминий вторым по популярности свариваемым металлом.
Однопроводная сварка алюминия MIGАлюминий против сварки стали
Одна из причин, по которой алюминий отличается от стали при сварке, заключается в том, что он не приобретает цвета по мере приближения к температуре плавления до тех пор, пока не поднимется выше точки плавления, после чего он станет тускло-красным.
При пайке алюминия горелкой используется флюс. Флюс будет плавиться, когда температура основного металла приблизится к требуемой температуре. Сначала высыхает флюс и плавится по мере того, как основной металл достигает правильной рабочей температуры.
При сварке горелкой в кислородно-ацетиленовой или кислородно-водородной среде поверхность основного металла сначала плавится и приобретает характерный влажный и блестящий вид. (Это помогает узнать, когда достигаются температуры сварки.) При сварке газовой вольфрамовой дугой или газовой металлической дугой цвет не так важен, потому что сварка завершается до того, как прилегающая область плавится.
Расплавленный алюминиевый наполнитель
Правильное добавление алюминиевого наполнителя в расплавленную сварочную ваннуСварочные свойства и сплавы
Алюминий и алюминиевые сплавы удовлетворительно свариваются металлической дугой, угольной дугой и другими процессами дуговой сварки. Чистый алюминий можно сплавить со многими другими металлами для получения широкого диапазона физических и механических свойств.
Способы, с помощью которых легирующие элементы упрочняют алюминий, используются в качестве основы для классификации сплавов на две категории: нетермообрабатываемые и термически обрабатываемые.Деформируемые сплавы в виде листов и пластин, труб, экструдированных и катаных профилей и поковок имеют одинаковые характеристики соединения независимо от формы.
Алюминиевые сплавы также производятся в виде отливок в виде песка, постоянной формы или литья под давлением. Практически одинаковые методы сварки, пайки или пайки используются как для литого, так и для кованого металла.
Литье под давлением не нашли широкого применения там, где требуется сварная конструкция. Однако они были склеены и в некоторой степени припаяны.Последние разработки в области вакуумного литья под давлением улучшили качество отливок до такой степени, что их можно удовлетворительно сваривать для некоторых применений.
Основным преимуществом использования процессов дуговой сварки является то, что дуга дает высококонцентрированную зону нагрева.
По этой причине предотвращается чрезмерное расширение и деформация металла.
Алюминий обладает рядом свойств, которые отличают сварку от сварки сталей.Это: покрытие поверхности оксидом алюминия; высокая теплопроводность; высокий коэффициент теплового расширения; низкая температура плавления; и отсутствие изменения цвета при приближении температуры к температуре плавления.
Нормальные металлургические факторы, применимые к другим металлам, применимы и к алюминию.
Алюминий — это активный металл, который реагирует с кислородом воздуха, образуя твердую тонкую пленку оксида алюминия на поверхности.
Температура плавления оксида алюминия составляет приблизительно 3600 ° F (1982 ° C), что почти в три раза выше точки плавления чистого алюминия (1220 ° F (660 ° C)).Кроме того, эта пленка оксида алюминия поглощает влагу из воздуха, особенно когда она становится толще.
Влага является источником водорода, который вызывает пористость алюминиевых сварных швов. Водород также может поступать из масла, краски и грязи в зоне сварного шва. Это также происходит из-за оксидов и посторонних материалов на электроде или присадочной проволоке, а также из основного металла. Водород попадает в сварочную ванну и растворяется в расплавленном алюминии. Когда алюминий затвердевает, он будет удерживать гораздо меньше водорода.
Водород не выделяется во время затвердевания. При высокой скорости охлаждения свободный водород остается внутри сварного шва и вызывает пористость. Пористость в зависимости от количества снижает прочность и пластичность сварного шва.
Сварочные стержни
Алюминий для сварки палкой (алюминиевые сварочные стержни) доступны с толщиной примерно 1/8 дюйма стали. Это отличный выбор для ремонта резервуаров и трубопроводов в полевых условиях. Также хороший выбор при работе в ветреную погоду.Это не для точной работы.
Обратной стороной использования алюминиевых сварочных стержней является необходимость значительного количества практики. Также существует проблема с потоком. флюс сильно горит и его трудно удалить. Он также прожигает краску.
Существуют превосходные альтернативы алюминиевым сварочным стержням, такие как сварка с подачей проволоки.
Нумерация алюминиевого сплава
Разработано много алюминиевых сплавов. Важно знать, какой сплав будет свариваться. Система четырехзначных чисел была разработана Aluminium Association, Inc., для обозначения различных типов деформируемых алюминиевых сплавов.
Эта система групп сплавов выглядит следующим образом:
- 1XXX серия . Это глинозем с чистотой 99% или выше, которые используются в основном в электрической и химической промышленности.
- 2XXX серии . Медь является основным сплавом в этой группе, который обеспечивает чрезвычайно высокую прочность при надлежащей термообработке. Эти сплавы не обладают такой хорошей коррозионной стойкостью и часто плакируются чистым алюминием или алюминием из специальных сплавов.Эти сплавы используются в авиастроении.
- 3ХХХ серия . Марганец является основным легирующим элементом в этой группе, который не поддается термической обработке. Содержание марганца ограничено примерно 1,5%. Эти сплавы обладают средней прочностью и легко обрабатываются.
- 4XXX серии . Кремний является основным легирующим элементом в этой группе. Его можно добавлять в количествах, достаточных для значительного снижения температуры плавления, и он используется для пайки сплавов и сварочных электродов.Большинство сплавов этой группы не поддаются термообработке.
- 5XXX серии . Магний является основным легирующим элементом этой группы, представляющей собой сплавы средней прочности. Они обладают хорошими сварочными характеристиками и хорошей устойчивостью к коррозии, но объем холодных работ следует ограничивать.
- 6XXX серии . Сплавы этой группы содержат кремний и магний, что делает их пригодными для термической обработки.
Эти сплавы обладают средней прочностью и хорошей коррозионной стойкостью.
- 7XXX серии . Цинк является основным легирующим элементом в этой группе. Магний также входит в состав большинства этих сплавов. Вместе они образуют термически обрабатываемый сплав очень высокой прочности, который используется для изготовления корпусов самолетов.
Очистка
Поскольку алюминий имеет большое сродство к кислороду, на его поверхности всегда присутствует пленка оксида. Эта пленка должна быть удалена перед любой попыткой сварить, припаять или припаять материал. Также необходимо предотвратить его образование во время процедуры соединения.
При подготовке алюминия к сварке, пайке или пайке соскоблите эту пленку острым инструментом, проволочной щеткой, наждачной бумагой или аналогичными средствами. Использование инертных газов или обильное нанесение флюса предотвращает образование оксидов в процессе соединения.
Алюминий и алюминиевые сплавы нельзя очищать каустической содой или чистящими средствами с pH выше 10, так как они могут вступать в химическую реакцию.
Пленку оксида алюминия необходимо удалить перед сваркой. Если его не удалить полностью, мелкие частицы нерасплавленного оксида будут задерживаться в сварочной ванне и вызовут снижение пластичности, отсутствие плавления и, возможно, растрескивание сварного шва.
Оксид алюминия можно удалить механическим, химическим или электрическим способом. Механическое удаление включает соскоб острым инструментом, наждачной бумагой, проволочной щеткой (нержавеющая сталь), опиливание или любой другой механический метод.
Химическое удаление можно выполнить двумя способами. Один из них заключается в использовании чистящих растворов, травильных или нетравильных. Типы без заедания следует использовать только при запуске с относительно чистыми деталями и вместе с другими очистителями на основе растворителей.Для лучшей очистки рекомендуются растворы для травления, но их следует использовать с осторожностью.
При использовании окунания настоятельно рекомендуется горячее и холодное ополаскивание. Растворы типа травления — щелочные растворы. Время нахождения в растворе необходимо контролировать, чтобы не произошло слишком сильного травления.
Химическая очистка
Химическая очистка включает использование сварочных флюсов. Флюсы используются для газовой сварки, пайки и пайки. Покрытие покрытых алюминиевых электродов также сохраняет флюсы для очистки основного металла.Каждый раз, когда используется очистка травлением или очистка флюсом, флюс и щелочные травильные материалы должны быть полностью удалены из зоны сварки, чтобы избежать коррозии в будущем.
Электрическая система удаления оксидов
В системе удаления оксидов электричества используется катодная бомбардировка. Катодная бомбардировка происходит во время полупериода сварки вольфрамовым электродом на переменном токе, когда электрод является положительным (обратная полярность).
Это электрическое явление, при котором оксидное покрытие стирается, чтобы получить чистую поверхность.Это одна из причин, почему дуговая сварка вольфрамовым электродом на переменном токе так популярна для сварки алюминия.
Поскольку алюминий настолько активен химически, оксидная пленка немедленно начинает преобразовываться. Время нарастания не очень быстрое, но сварные швы следует выполнять после очистки алюминия в течение не менее 8 часов для качественной сварки. Если наступит более длительный период времени, качество сварного шва снизится.
Теплопроводность
Алюминий обладает высокой теплопроводностью и низкой температурой плавления.В зависимости от сплава, он проводит тепло в три-пять раз быстрее, чем сталь.
Алюминий необходимо нагреть больше, даже если температура плавления алюминия вдвое меньше, чем у стали. Из-за высокой теплопроводности для сварки более толстых секций часто используется предварительный нагрев. Если температура слишком высока или период времени слишком большой, прочность сварного соединения как в термообработанных, так и в закаленных сплавах может снизиться.
Предварительный нагрев алюминия не должен превышать 400ºF (204ºC), и детали не должны выдерживаться при этой температуре дольше, чем необходимо.Из-за высокой теплопроводности в процедурах следует использовать высокоскоростные сварочные процессы с большим тепловложением. И газовая вольфрамовая дуга, и газовая дуга с металлической дугой удовлетворяют этому требованию.
Высокая теплопроводность алюминия может быть полезной, поскольку сварной шов очень быстро затвердевает, если тепло отводится от сварного шва очень быстро. Наряду с поверхностным натяжением это помогает удерживать металл шва в нужном положении и делает практичную сварку вольфрамовой дугой и дуговой сваркой металлическим электродом во всех положениях.
Тепловое расширение алюминия в два раза больше, чем у стали. Кроме того, алюминиевые сварные швы уменьшаются в объеме примерно на 6 процентов при затвердевании из расплавленного состояния. Это изменение размера может вызвать деформацию и растрескивание.
Сварка алюминиевых листов
Для сварки алюминиевых листов из-за сложности управления дугой, стыковые и угловые швы трудно производить на листах толщиной менее 1/8 дюйма (3,2 мм). При сварке пластины тяжелее 1/8 дюйма (3,2 мм) соединение, подготовленное со скосом 20 градусов, будет иметь прочность, равную прочности сварного шва, выполненного кислородно-ацетиленовым процессом.
Этот сварной шов может быть пористым и не подходить для герметичных соединений с жидкостями или газами. Однако дуговая сварка металла особенно подходит для тяжелых материалов и используется для обработки листов толщиной до 2-1 / 2 дюйма (63,5 мм).
Настройки тока и полярности
Настройки тока и полярности зависят от типа электродов каждого производителя. Используемая полярность должна быть определена путем пробного соединения выполняемых соединений.
Подготовка кромки плиты
В целом конструкция сварных соединений для алюминия вполне соответствует конструкции сварных соединений для стальных соединений. Однако из-за более высокой текучести алюминия под сварочной дугой следует помнить о некоторых важных общих принципах. При использовании алюминиевого листа меньшей толщины предпочтительнее меньшее расстояние между канавками, когда разбавление сварного шва не имеет значения.
Управляющим фактором является совместная подготовка. Специально разработанная V-образная канавка отлично подходит там, где сварка может выполняться только с одной стороны и где требуется гладкий проникающий валик. Эффективность этой конкретной конструкции зависит от поверхностного натяжения и должна применяться ко всем материалам размером более 1/8 дюйма.(3,2 мм) толщиной.
Дно специальной V-образной канавки должно быть достаточно широким, чтобы полностью вместить корневой проход. Это требует добавления относительно большого количества присадочного сплава для заполнения канавки.
Превосходный контроль проплавления и получение прочных корневых швов. Эта подготовка кромки может использоваться для сварки во всех положениях. Это устраняет трудности, связанные с прожогом или проплавлением в положениях при перегреве и горизонтальной сварке. Он применим ко всем свариваемым основным сплавам и всем присадочным сплавам.
Сварка алюминия MIG
Полностью автоматическая однопроволочная сварка MIGГазовая дуговая сварка (MIG) (GMAW)
Этот быстрый, адаптируемый процесс используется с постоянным током обратной полярности и инертным газом для сварки алюминиевых сплавов большой толщины в любом положении, от 1/016 дюйма (1,6 мм) до нескольких дюймов. TM 5-3431-211-15 описывает работу типичного сварочного аппарата MIG.
Защитный газ
Необходимо принять меры для обеспечения максимальной эффективности газовой защиты.Для сварки алюминия используются аргон, гелий или смесь этих газов. Аргон дает более плавную и стабильную дугу, чем гелий. При определенном токе и длине дуги гелий обеспечивает более глубокое проникновение и более горячую дугу, чем аргон.
Напряжение дуги выше у гелия, и данное изменение длины дуги приводит к большему изменению напряжения дуги. Профиль валика и характер проплавления алюминиевых швов, выполненных аргоном и гелием, различаются. У аргона профиль шарика уже и выпуклее, чем у гелия.Схема проникновения показывает глубокий центральный разрез.
Гелий дает более плоский и широкий валик и более широкий рисунок проникновения под валиком. Смесь примерно 75 процентов гелия и 25 процентов аргона обеспечивает преимущества обоих защитных газов без нежелательных характеристик ни одного из них.
Диаграмма проникновения и контур валика показывают характеристики обоих газов. Стабильность дуги сравнима с аргоном. Угол наклона пистолета или горелки более важен при сварке алюминия в инертном защитном газе.Рекомендуется передний угол хода 30 °.
Наконечник электродной проволоки должен быть больше алюминия. В Таблице 7-21 приведены технологические схемы сварки алюминия дуговой газовой сваркой.
Сварка алюминия GMAW
Алюминиевый шов, выполненный методом GMAW. Сварщик «укладывает валик» из расплавленного металла, который становится сварным швом без шлака.Техника для сварки алюминия
Проволока электрода должна быть чистой. Дуга зажигается, когда электродная проволока выступает примерно на 1/2 дюйма.(12,7 мм) от чашки.
Часто используется метод зажигания дуги примерно на 1,0 дюйма (25,4 мм) перед началом сварки, а затем быстрое подведение дуги к начальной точке сварки, изменение направления движения и продолжение обычной сварки. В качестве альтернативы дуга может быть зажжена за пределами сварной канавки на начальном выступе.
При окончании или прекращении сварки аналогичная практика может сопровождаться изменением направления сварки на противоположное и одновременным увеличением скорости сварки для уменьшения ширины ванны расплава до разрыва дуги.Это помогает предотвратить кратеры и растрескивание кратеров. Обычно используются вкладки стока.
Установив дугу, сварщик перемещает электрод вдоль стыка, сохраняя угол переда от 70 до 85 градусов относительно работы.
Обычно предпочтительнее использовать струны из бисера. Следует следить за тем, чтобы угол переда не изменялся или не увеличивался по мере приближения к концу сварного шва. Скорость движения дуги контролирует размер валика.
При сварке алюминия этим процессом важно поддерживать высокие скорости перемещения.При сварке одинаковой толщины угол между электродом и рабочим углом должен быть одинаковым с обеих сторон сварного шва.
При сварке в горизонтальном положении наилучшие результаты достигаются, если направить пистолет немного вверх. При сварке толстых листов с тонкими пластинами полезно направлять дугу в сторону более тяжелого участка.
Небольшой угол обратной стороны иногда бывает полезен при сварке тонких секций с толстыми. Корневой проход стыка обычно требует короткой дуги для обеспечения желаемого проплавления.При последующих проходах можно использовать дугу немного большей длины и более высокое напряжение дуги.
Оборудование подачи проволоки для сварки алюминия должно быть хорошо отрегулировано для обеспечения эффективной подачи проволоки. Используйте лайнеры нейлонового типа в кабельных сборках. Для алюминиевой проволоки и размера электродной проволоки необходимо выбрать соответствующие приводные ролики.
Продеть алюминиевую проволоку чрезвычайно малого диаметра через длинные кабельные сборки пистолета сложнее, чем стальную проволоку. По этой причине для электродных проволок малого диаметра используются катушки-пистолеты или недавно разработанные пистолеты с линейным двигателем подачи.
Требуются пистолеты с водяным охлаждением, кроме слаботочной сварки. Для сварки алюминия используются как источник питания постоянного тока (CC) с согласованным механизмом подачи проволоки с измерением напряжения, так и источник питания постоянного напряжения (CV) с механизмом подачи проволоки постоянной скорости. Кроме того, механизм подачи проволоки с постоянной скоростью иногда используется с источником питания постоянного тока.
В целом, система CV предпочтительнее при сварке тонких материалов и использовании электродной проволоки любого диаметра. Это обеспечивает лучшее зажигание и регулировку дуги.Система CC предпочтительна при сварке толстого материала с использованием электродной проволоки большего диаметра.
Качество сварки с этой системой кажется лучше. Источник постоянного тока с умеренным падением напряжения от 15 до 20 вольт на 100 ампер и механизм подачи проволоки с постоянной скоростью обеспечивают наиболее стабильную подводимую мощность к сварному шву и высочайшее качество сварки.
Конструкция сварного соединения алюминия
Кромки могут быть подготовлены к сварке распиловкой, механической обработкой, круговым строганием, фрезерованием или дуговой резкой.
Полностью автоматическая однопроволочная сварка алюминия методом MIG
Пример сварки алюминия: присадочная проволока: AA 5183 (AlMg4,5Mn) 2,4 мм Основной материал: AA 5356 (AlMg5) Размер: 500 x 150 x 15 мм (предварительный нагрев не допускается) Защитный газ: Ar70 / He30 Скорость сварки: 60/40 см / мин Положение сварки: 1 G Двухслойный второй слой> осциллирующийГазовая вольфрамо-дуговая сварка (GTAW)
Меры предосторожности
Процесс газовой вольфрамовой дуговой сварки (TIG) используется для сварки более тонких профилей алюминия и алюминиевых сплавов.При использовании этого процесса следует упомянуть несколько мер предосторожности.
- Переменный ток рекомендуется для универсальных работ, так как он обеспечивает половину цикла очищающего действия. В Таблице 7-22 приведены графики процедуры сварки для использования процесса на разной толщине для получения различных сварных швов. Сварка переменным током, обычно с высокой частотой, широко используется как в ручном, так и в автоматическом режиме. Следует строго соблюдать процедуры, и особое внимание следует уделять типу вольфрамового электрода, размеру сварочного сопла, типу газа и расходу газа.
При ручной сварке длина дуги должна быть небольшой и равной диаметру электрода. Вольфрамовый электрод не должен выступать слишком далеко за конец сопла. Вольфрамовый электрод следует содержать в чистоте. Если он случайно коснулся расплавленного металла, его необходимо восстановить.
- Сварка алюминия Следует использовать источники сварочного тока, предназначенные для дуговой сварки вольфрамовым электродом. Новое оборудование обеспечивает программирование, предварительную и последующую подачу защитного газа, а также пульсирование.
- Сварка алюминия Для автоматической или машинной сварки можно использовать отрицательный электрод постоянного тока (прямая полярность). Очистка должна быть чрезвычайно эффективной, поскольку катодная бомбардировка не помогает. При использовании отрицательного электрода постоянного тока можно получить чрезвычайно глубокое проникновение и высокие скорости. В Таблице 7-23 приведены графики процедуры сварки для отрицательной сварки электродом постоянного тока.
- В качестве защитных газов для сварки алюминия используются аргон, гелий или их смесь. Аргон используется с меньшим расходом.Гелий увеличивает проникновение, но требуется более высокая скорость потока. При использовании присадочной проволоки она должна быть чистой. Оксид, не удаленный с присадочной проволоки, может содержать влагу, которая создает полярность в наплавленном шве.
Ручная сварка алюминия MIG
Ручная сварочная горелка с «квазиподобной» геометрией соединения Диаметр проволоки: AA 5183 (1,6 мм) Основной материал: AA 6061 (AlMgSi) Толщина: 15 ммСварка на переменном токе
Характеристики процесса
Сварка алюминия методом газовой вольфрамо-дуговой сварки на переменном токе дает эффект очистки от оксидов.
В качестве защитного газа используется аргон. Лучшие результаты достигаются при сварке алюминия переменным током с использованием оборудования, предназначенного для создания сбалансированной волны или равного тока в обоих направлениях.
Дисбаланс приведет к потере мощности и снижению очищающего действия дуги. Характеристики стабильной дуги — это отсутствие щелчков или трещин, плавное зажигание дуги и притяжение добавленного присадочного металла к сварочной ванне, а не склонность к отталкиванию.Стабильная дуга приводит к меньшему количеству включений вольфрама.
Ручная сварка алюминия MIG
Техника для сварки алюминия
Для ручной сварки алюминия переменным током электрододержатель удерживается в одной руке, а присадочный стержень, если он используется, — в другой. Первоначальная дуга зажигается на пусковом блоке для нагрева электрода.
Затем дуга разрывается и снова зажигается в суставе. Этот метод снижает вероятность появления включений вольфрама в начале сварки. Дуга удерживается в начальной точке до тех пор, пока металл не станет жидким и не образуется сварочная ванна.
Создание и поддержание подходящей сварочной ванны очень важно, и сварка не должна продолжаться перед лужей.
Если требуется присадочный металл, он может быть добавлен к передней или передней кромке бассейна, но с одной стороны от центральной линии. Обе руки двигаются в унисон с легкими движениями вперед и назад вдоль сустава. Вольфрамовый электрод не должен касаться присадочного стержня.
Горячий конец присадочного стержня не должен выниматься из аргонового экрана.Необходимо поддерживать короткую длину дуги, чтобы обеспечить достаточное проплавление и избежать подрезов, чрезмерной ширины сварного шва и, как следствие, потери контроля проплавления и контура сварного шва.
Одно правило — использовать длину дуги, приблизительно равную диаметру вольфрамового электрода. При разрыве дуги в кратере сварного шва могут возникнуть усадочные трещины, что приведет к дефектному сварному шву.
Этот дефект можно предотвратить, постепенно увеличивая длину дуги и добавляя в кратер присадочный металл.Затем быстро разорвите и повторно зажгите дугу несколько раз, добавляя в кратер дополнительный присадочный металл, или используйте педаль для уменьшения тока в конце сварного шва. Прихватывание перед сваркой помогает контролировать деформацию.
Прихваточные швы должны быть достаточного размера и прочности, перед сваркой на концах должны быть вырезаны сколы или конусность.
Расчет сварных швов
Конструкции соединений применимы к процессу газовой вольфрамо-дуговой сварки с небольшими исключениями.Неопытным сварщикам, которые не могут поддерживать очень короткую дугу, может потребоваться более широкая подготовка кромок, прилегающий угол или расстояние между стыками.
Соединения могут быть сплавлены с помощью этого процесса без добавления присадочного металла, если сплав основного металла также является удовлетворительным присадочным сплавом. Кромочные и угловые сварные швы выполняются быстро без добавления присадочного металла и имеют хороший внешний вид, но при этом очень важно их точное прилегание.
Прямая полярность постоянного тока
Характеристики процесса
Этот процесс с использованием гелиевых и торированных вольфрамовых электродов полезен для многих автоматических сварочных операций, особенно при сварке тяжелых профилей.Поскольку существует меньшая склонность к нагреванию электрода, для заданного сварочного тока можно использовать электроды меньшего размера. Это будет способствовать сохранению узкого валика сварного шва.
Использование постоянного тока прямой полярности (dcsp) обеспечивает больший подвод тепла, чем при использовании переменного тока. В сварочной ванне выделяется больше тепла, поэтому она становится глубже и уже.
Методы
Для зажигания дуги следует использовать ток высокой частоты. Запуск от касания приведет к загрязнению вольфрамового электрода.Нет необходимости образовывать лужу, как при сварке на переменном токе, поскольку плавление происходит в момент зажигания дуги. Следует позаботиться о том, чтобы дуга зажгла в зоне сварки, чтобы предотвратить нежелательную маркировку материала.
Используются стандартные методы, такие как отводные язычки и ножные регуляторы нагрева. Они полезны для предотвращения или заполнения кратеров, для регулировки силы тока при рабочем нагреве и для корректировки изменения толщины сечения. При сварке постоянным током горелка постоянно перемещается вперед.Присадочная проволока равномерно подается в переднюю кромку сварочной ванны или укладывается на стык и плавится по мере продвижения дуги.
Во всех случаях кратер должен быть заполнен до точки над валиком сварного шва, чтобы исключить кратерные трещины. Размер галтели можно регулировать, варьируя размер присадочной проволоки. DCSP адаптируется к ремонтным работам. Предварительный нагрев не требуется даже для тяжелых секций, а зона термического влияния будет меньше с меньшими искажениями.
Конструкции сварных соединений алюминия
Для ручного dcsp концентрированное тепло дуги дает отличное закрепление корня.Поверхность корня может быть толще, канавки уже, а нарост можно легко контролировать, варьируя размер присадочной проволоки и скорость перемещения.
Сварка прямоугольным переменным током (TIG)
Методы
Для зажигания дуги следует использовать ток высокой частоты. Запуск от касания приведет к загрязнению вольфрамового электрода. Нет необходимости образовывать лужу, как при сварке на переменном токе, поскольку плавление происходит в момент зажигания дуги. Следует позаботиться о том, чтобы дуга зажгла в зоне сварки, чтобы предотвратить нежелательную маркировку материала.
Используются стандартные методы, такие как отводные язычки и ножные регуляторы нагрева. Они полезны для предотвращения или заполнения кратеров, для регулировки силы тока при рабочем нагреве и для корректировки изменения толщины сечения. При сварке постоянным током горелка постоянно перемещается вперед.
Присадочная проволока равномерно подается в переднюю кромку сварочной ванны или укладывается на стык и плавится по мере продвижения дуги. Во всех случаях кратер следует заполнить до точки над валиком сварного шва, чтобы устранить трещины кратера.
Размер скругления можно регулировать, варьируя размер присадочной проволоки. DCSP адаптируется к ремонтным работам. Предварительный нагрев не требуется даже для тяжелых секций, а зона термического влияния будет меньше с меньшими искажениями.
Конструкции сварных соединений алюминия
Для ручного dcsp концентрированное тепло дуги дает отличное закрепление корня. Поверхность корня может быть толще, канавки уже, а нарост можно легко контролировать, варьируя размер присадочной проволоки и скорость перемещения.
Сварка металло-дуговой сваркой в защитных оболочках
В процессе дуговой сварки металлическим электродом в защитных слоях используется электрод с покрытием из твердого флюса или экструдированного флюса.Покрытие электродов аналогично покрытию обычных стальных электродов. Покрытие из флюса обеспечивает газовый экран вокруг дуги и лужи расплавленного алюминия, а также химически объединяет и удаляет оксид алюминия, образуя шлак.
При сварке алюминия процесс довольно ограничен из-за разбрызгивания дуги, неустойчивого управления дугой, ограничений на тонкий материал и коррозионного действия флюса, если он не удаляется должным образом.
Экранированная углеродно-дуговая сварка
Для соединения алюминия можно использовать процесс дуговой сварки в среде защитного угля.Для этого требуется флюс, и он дает сварные швы такого же внешнего вида, прочности и структуры, что и сварные швы, полученные при кислородно-ацетиленовой или кислородно-водородной сварке. Сварка в среде защитного угля производится как вручную, так и автоматически.
Угольная дуга используется в качестве источника тепла, а присадочный металл подается от отдельного присадочного стержня. После сварки необходимо удалить флюс; в противном случае возникнет сильная коррозия.
Ручная дуговая сварка в среде защитного угля обычно ограничивается толщиной менее 3/8 дюйма.(9,5 мм), выполненная тем же способом, что и при ручной дуговой сварке других материалов углем. Подготовка швов аналогична той, что используется при газовой сварке. Используется стержень, покрытый флюсом.
Сварка на атомарном водороде
Этот процесс сварки заключается в поддержании дуги между двумя вольфрамовыми электродами в атмосфере газообразного водорода.
Процесс может быть ручным или автоматическим с процедурами и методами, близкими к тем, которые используются при кислородно-ацетиленовой сварке.
Поскольку водородный экран, окружающий основной металл, исключает кислород, для объединения или удаления оксида алюминия требуется меньшее количество флюса.Увеличивается видимость, меньше флюсовых включений, наплавляется очень прочный металл.
Сварка шпилек
Приварку алюминиевых шпилек можно выполнять с помощью обычного оборудования для дуговой сварки шпилек, используя либо разряд конденсатора, либо разряд конденсатора с вытяжкой.
Обычный процесс дуговой приварки шпилек можно использовать для приваривания алюминиевых шпилек диаметром от 3/16 до 3/4 дюйма (от 4,7 до 19,0 мм).
Пистолет для приварки алюминиевых шпилек немного модифицирован за счет добавления специального адаптера для контроля защитных газов высокой чистоты, используемых во время цикла сварки.Дополнительный вспомогательный элемент управления для контроля врезания шпильки по завершении цикла сварки существенно повышает качество сварки и снижает потери от разбрызгивания.
Используется обратная полярность: электрод-пистолет положительный, а деталь — отрицательный. Небольшой цилиндрический или конусообразный выступ на конце алюминиевой шпильки инициирует дугу и помогает установить большую длину дуги, необходимую для сварки алюминия.
Процессы
Процессы приварки шпилек неэкранированного конденсатора или разрядки конденсатора с натянутой дугой используются с алюминиевыми шпильками от 1/16 до 1/4 дюйма(От 1,6 до 6,4 мм) диаметром.
Конденсаторная сварка использует низковольтную электростатическую накопительную систему, в которой энергия сварочного шва накапливается при низком напряжении в конденсаторах с высокой емкостью в качестве источника питания. В процессе приварки шпильки конденсаторным разрядом небольшой наконечник или выступ на конце шпильки используется для зажигания дуги.
В процессе приварки шпилек с разрядом протянутой дуги используется шпилька с заостренным или слегка закругленным концом. Для зажигания дуги не требуется зубчатый наконечник или выступ на конце шпильки.В обоих случаях цикл сварки аналогичен обычному процессу приварки шпилек. Однако использование выступа на основании шпильки обеспечивает наиболее стабильную сварку.
Короткое время горения дуги в процессе разряда конденсатора ограничивает плавление, что приводит к неглубокому проникновению в заготовку. Минимальная толщина алюминиевой заготовки, которая считается практичной, составляет 0,032 дюйма (0,800 мм).
Электронно-лучевая сварка
Электронно-лучевая сварка — это процесс соединения плавлением, при котором заготовка бомбардируется плотным потоком высокоскоростных электронов, и практически вся кинетическая энергия электронов при ударе преобразуется в тепло.
Электронно-лучевая сварка обычно проводится в вакуумированной камере. Размер камеры является ограничивающим фактором для размера сварного изделия. Обычные дуговые и газовые нагреватели плавятся чуть больше, чем поверхность. Дальнейшее проникновение происходит исключительно за счет отвода тепла во всех направлениях от этого пятна расплавленной поверхности. Зона слияния расширяется по мере необходимости.
Электронный луч способен к настолько интенсивному локальному нагреву, что почти мгновенно испаряет отверстие по всей толщине стыка.Стенки этого отверстия расплавляются, и по мере того, как отверстие перемещается по стыку, все больше металла на продвигающейся стороне отверстия расплавляется. Это дефект вокруг отверстия отверстия и затвердевает вдоль задней стороны отверстия, чтобы сделать сварной шов.
Интенсивность луча можно уменьшить, чтобы получить частичное проникновение с такой же узкой конфигурацией. Электронно-лучевая сварка обычно применяется для кромочных, стыковых, угловых, сквозных и точечных сварных швов. Присадочный металл используется редко, кроме наплавки.
Сварка сопротивлением
Способы контактной сварки алюминия (точечная, шовная и оплавление) важны при производстве алюминиевых сплавов. Эти процессы особенно полезны при соединении высокопрочных термообрабатываемых сплавов, которые трудно соединить сваркой плавлением, но которые могут быть соединены методом контактной сварки практически без потери прочности.
Естественное оксидное покрытие алюминия имеет довольно высокое и непостоянное электрическое сопротивление.Чтобы получить точечные или шовные сварные швы максимальной прочности и однородности, обычно необходимо уменьшить это оксидное покрытие перед сваркой.
Сварка Точечная сварка
Сварные швы с одинаково высокой прочностью и хорошим внешним видом зависят от стабильно низкого поверхностного сопротивления между рабочими местами. В большинстве случаев перед точечной или шовной сваркой алюминия необходимо выполнить некоторые операции по очистке.
Подготовка поверхности к сварке обычно заключается в удалении жира, масла, грязи или идентификационной маркировки, а также в уменьшении и улучшении консистенции оксидной пленки на поверхности алюминия.Удовлетворительное качество точечной сварки в процессе эксплуатации в значительной степени зависит от конструкции соединения.
Точечные сварные швы всегда должны выдерживать поперечные нагрузки. Однако, когда можно ожидать растяжения или комбинированных нагрузок, следует провести специальные испытания для определения фактической прочности соединения при эксплуатационной нагрузке. Прочность точечной сварки при прямом растяжении может варьироваться от 20 до 90 процентов прочности на сдвиг.
Сварка швов
Шовная сварка алюминия и его сплавов очень похожа на точечную сварку, за исключением того, что электроды заменены колесами.
Пятна, оставленные аппаратом для шовной сварки, могут перекрываться, образуя газонепроницаемое или непроницаемое для жидкости соединение. Регулируя синхронизацию, машина для шовной сварки может производить точечную сварку с равномерным интервалом, равную по качеству той, которая производится на обычной машине для точечной сварки, и с большей скоростью. Эта процедура называется точечной сваркой или прерывистым швом.
Сварка алюминия оплавлением
Все алюминиевые сплавы можно соединять оплавлением. Этот процесс особенно подходит для выполнения стыковых или угловых соединений между двумя частями одинакового поперечного сечения.Он был адаптирован для соединения алюминия с медью в виде стержней и трубок. Полученные таким образом соединения выходят из строя за пределами области сварного шва при приложении растягивающих нагрузок.
Газовая сварка алюминия
Газовая сварка алюминия выполнялась с использованием пламени как ацетилена, так и водорода. В любом случае требуется абсолютно нейтральное пламя. В качестве присадочного стержня используется флюс. Этот процесс также не слишком популярен из-за низкого тепловложения и необходимости удаления флюса.
Электрошлаковая сварка
Электрошлаковая сварка используется для соединения чистого алюминия, но неэффективна для сварки алюминиевых сплавов.Сварка под флюсом используется в некоторых странах, где нет инертного газа.
Другие процессы
Большинство процессов сварки в твердом состоянии, включая сварку трением, ультразвуковую сварку и холодную сварку, используются для алюминия. Алюминий также можно соединять пайкой и пайкой. Пайка может выполняться большинством методов пайки. Используется наполнитель из сплава с высоким содержанием кремния.
Для дополнительного чтения
Газовая сварка алюминия
Пайка алюминия
Подробнее о сварке алюминия методом TIG
Применение при сварке фланцев | Простое описание различных типов.Звоните для консультации
Сварка фланцев — процесс и оборудование
Наиболее часто используемые типы фланцев в соотв. согласно ASME B16.5: приварная шейка, надевание, сварка внахлест, соединение внахлест, резьбовой и глухой фланец. Ниже вы найдете краткое описание и определение каждого типа.
Прочитав эту статью, посетите TWI, где можно найти множество примеров из практики различных исследований по сварке фланцев.
Фланец под приварную шейку
Легко узнаваемая длинная коническая ступица фланца с приварной шейкой обеспечивает решающее усиление соединения для приложений, связанных с высоким давлением, отрицательными и / или повышенными температурами, или в случаях, когда соединение будет испытывать определенную нагрузку.
Конус на этом типе фланца обеспечивает плавный переход / перемещение напряжения от толщины фланца к толщине стенки трубы или фитинга и полезен в условиях повторяющегося изгиба, вызванного линейным расширением или другими переменными силами.
Эрозия на стыке и напряжение стыка также уменьшаются за счет внутреннего отверстия этих фланцев, которое совпадает с внутренним диаметром сопряженной трубы или фитинга, что не приводит к ограничению потока. Это также предотвращает турбулентность в суставе и снижает эрозию.
Они также легко поддаются рентгенографии для обнаружения дефектов.
Этот тип фланца будет приварен к трубе или фитингу с одним полным проваром, V-образным швом (стыковой сваркой).
Фланец с приварной шейкой может также называться коническим фланцем ступицы или фланцем с высокой ступицей, а также существует версия, известная как фланец с длинной приварной шейкой, похожий на стандартный фланец с приварной шейкой, но удлиненный, часто используемый в качестве сопла для бочка или столбик.
Фланец скольжения
По сравнению с фланцами с приварной шейкой фланец не такой прочный, его расчетная прочность при внутреннем давлении примерно на две трети меньше, а срок службы составляет примерно одну треть.Однако они имеют низкую стоимость материалов и простую установку, поэтому лучше подходят для приложений с низким давлением с небольшим риском утечки.
Некоторые другие преимущества надвижных фланцев состоят в том, что они не требуют большого продольного пространства в линии для монтажа. Кроме того, их гораздо легче выровнять с широким диапазоном доступных диаметров, и, наконец, они не требуют точных разрезов в трубе.
Без шейки, на которую должна опираться труба, необходимо выполнить двойную сварку соединения с трубой, используя 2 угловых шва с внешней стороны, а также с внутренней стороны фланца.
Недостаток накладок на фланец заключается в том, что сначала всегда нужно сваривать трубу, а затем только фитинг. Например, нельзя использовать комбинацию фланца и колена или фланца и тройника, потому что эти фитинги не имеют прямого конца. Они не подходят для соединений высокого давления или там, где должны использоваться опасные материалы.
Фланец для приварки внахлест
Фланцы, приваренные внахлест, изначально были разработаны для использования на малогабаритных трубопроводах высокого давления, их статическая прочность равна скольжению на фланцах, но их усталостная прочность на 50% выше, чем у фланцев, приваренных двойным сварным швом.
Перед сваркой необходимо создать пространство от 1/16 дюйма до 1/8 дюйма между фланцем или фитингом и трубой, это необходимо для расширения трубы на внутренней стороне сварного шва и уменьшения остаточного напряжения, поэтому предотвращение растрескивания сварного шва на фитинге.
Соединение с трубой выполняется 1 угловым сварным швом с внешней стороны фланца.
ASME B31.1 1998 127.3 Подготовка к сварке (E) Узел сварки внахлест говорит:
При сборке соединения перед сваркой труба или трубка должны быть вставлены в муфту на максимальную глубину, а затем вынуты примерно на 1/16 дюйма ( 1.6 мм) от контакта между концом трубы и буртиком муфты.
Преимущества использования фланцев, приваренных раструбом, заключаются в том, что сварной шов находится снаружи трубы, поэтому он не проникает в отверстие трубы. Нет необходимости подготавливать фаску перед сваркой, также фланец, приваренный муфтой, может заменить фланец с резьбой и минимизировать любые риски утечки.
Недостатком фланца является необходимость в зазоре, который необходимо сделать. Во-первых, требуются высококвалифицированные сварщики, чтобы сделать зазор 1/16 дюйма.Во-вторых, компенсационный зазор увеличивает риск растрескивания, особенно на антикоррозионных трубах, таких как нержавеющая сталь. Коррозионные проблемы будут вызваны трещинами между трубой и фланцем, что приведет к повышенному техническому обслуживанию. В некоторых процессах использование этого фланца также недопустимо.
Фланец внахлест
Фланцыдля соединения внахлест имеют все те же общие характеристики, что и другие упомянутые нами фланцы, однако у них нет выступа, они соединены с «заглушкой» для соединения внахлест.
Эти фланцы почти идентичны накладным фланцам, за исключением изогнутого радиуса в отверстии для размещения фланцевой части заглушки, которая затем скользит по трубе. Затем трубу обычно приваривают к заглушке, чтобы обеспечить свободное движение фланца соединения внахлест.
Их прочность аналогична прочности скольжения на фланце, а их усталостная долговечность составляет всего лишь одну десятую от усталостной прочности фланцев с приварной шейкой, поэтому они подходят для использования при низком давлении.
Фланцы с соединением внахлестимеют определенные преимущества:
- Свобода поворота вокруг трубы облегчает совмещение противоположных отверстий под болты фланца, облегчая демонтаж там, где может потребоваться частый осмотр и очистка.
- Отсутствие контакта с жидкостью в трубе позволяет использовать недорогие фланцы из углеродистой стали с трубами, устойчивыми к коррозии, что может привести к значительной экономии средств.
- В системах, которые быстро разрушаются или подвержены коррозии, фланцы можно использовать для повторного использования.
Заглушка
окурок End всегда будет использоваться с внахлестом фланцевых применением в качестве опорного фланца, однако они также могут быть использованы с скольжением на фланцах.
доступны почти для всех диаметров труб. Есть 3 различных типов доступных, А, В и С.
Тип A может быть обработан в соответствии со стандартными внахлестку опорным фланцем, типа В предназначен для использования со стандартным скольжением на фланец и типа C могут быть использован либо с соединение внахлест или накладка на фланец.
Размеры и допуски на размеры определены в стандарте ASME B.16.9. Легкие коррозионно-стойкие заглушки (фитинги) определены в MSS SP43.
Фланец с резьбой
Основным преимуществом фланца с резьбой является то, что не требуется сварка соединения с трубой, так как это делается с помощью соответствующей резьбы. Однако иногда герметичный сварной шов также применяется в сочетании с резьбовым соединением фланца.
Резьбовые фитинги сегодня используются почти исключительно для труб меньшего диаметра, примерно до 4.00 ″, однако большинство размеров и номинальных значений давления все еще доступны.
Фланец или фитинг с резьбой подходят только для применений, в которых используется большая толщина стенки из-за наличия резьбы. Система труб с тонкими стенками не имеет места для нарезания резьбы. Пример толщины и нанесения ниже:
ASME B31.3 Руководство по трубопроводам гласит:
Если стальная труба имеет резьбу и используется для работы с паром при давлении выше 250 фунтов на квадратный дюйм или для подачи воды выше 100 фунтов на квадратный дюйм с температурой воды выше 220 ° F, труба должна быть бесшовной и иметь по крайней мере равную толщину. к приложению 80 ASME B36.10.
Доступны два типа фланцев с резьбой: один используется для уплотнения двух концов трубы с помощью прокладки для линз и уплотнительной поверхности, которые до недавнего времени в основном использовались при производстве аммиака. Другой тип — более стандартная установка, уплотненная двумя фланцевыми уплотняющими поверхностями. Доступны два типа облицовки фланца с резьбой: один — с выступом, а другой — с кольцевым соединением.
Диапазон оборудования для фланцевой сварки: вращатели для труб, позиционеры для сварки, а также головные и задние бабки для позиционирования при сварке труб.
Если вам нужна помощь в выборе подходящего сварочного оборудования для вашего сварочного проекта, свяжитесь с нами.
Дефекты / несовершенства сварных швов — включения шлака
Описаны характерные особенности и основные причины дефектов шлака.
Идентификация
Шлак обычно представляет собой удлиненные линии, непрерывные или прерывистые по длине сварного шва. Это легко определить на рентгенограмме. Рис. 1. Включения шлака обычно связаны с процессами флюса, т.е. MMA, FCA и дугой под флюсом, но они также могут возникать при сварке MIG.
Нажмите здесь, чтобы увидеть наши последние подкасты по технической инженерии на YouTube .Причины
Поскольку шлак является остатком покрытия из флюса при сварке MMA, он в основном является продуктом раскисления в результате реакции между флюсом, воздухом и поверхностным оксидом. Шлак захватывается сварным швом, когда два соседних сварных валика осаждаются с недостаточным перекрытием и образуется пустота. При нанесении следующего слоя уловленный шлак не расплавляется.Шлак также может попасть в полости в многопроходных сварных швах из-за чрезмерного подреза в носке сварного шва или неровного профиля поверхности предыдущих прогонов сварного шва, Рис. 2.
Поскольку оба они влияют на легкость удаления шлака, на риск дефектов шлака влияет
- Тип покрытия флюсом
- Сварочная техника
Тип и конфигурация соединения, положение сварки и ограничения доступа — все это влияет на риск образования дефектов шлака.
Тип покрытия флюсом
Одна из основных функций флюсового покрытия при сварке — это образование шлака, который будет свободно течь по поверхности сварочной ванны, защищая его от окисления. Поскольку шлак влияет на рабочие характеристики ММА-электрода, его поверхностное натяжение и скорость замерзания могут быть не менее важными свойствами. Для сварки в плоском и горизонтальном / вертикальном положениях предпочтительным является относительно вязкий шлак, поскольку он дает гладкий профиль сварного шва, с меньшей вероятностью захватывается и при затвердевании обычно легче удаляется.При вертикальной сварке шлак должен быть более текучим, чтобы вытекать к поверхности сварочной ванны, но иметь более высокое поверхностное натяжение, чтобы поддерживать сварочную ванну и быстро замерзать.
Состав флюсового покрытия также играет важную роль в риске образования шлаковых включений из-за его влияния на форму сварного шва и легкости удаления шлака. Сварочная ванна с низким содержанием кислорода будет иметь высокое поверхностное натяжение, приводящее к выпуклому сварному шву с плохим смачиванием основного металла.Таким образом, окисляющий флюс, содержащий, например, оксид железа, создает сварочную ванну с низким поверхностным натяжением с более вогнутым профилем валика сварного шва и способствует смачиванию основного металла. Высокосиликатный флюс дает стекловидный шлак, часто саморазлагающийся. Флюсы с содержанием извести образуют налипший шлак, который трудно удалить.
Простота удаления шлака для основных типов флюсов:
- Рутиловые или кислотные флюсы — большие количества оксида титана (рутила) с некоторыми силикатами.Уровень кислорода в сварочной ванне достаточно высок, чтобы получить плоский или слегка выпуклый сварной шов. Текучесть шлака определяется содержанием фторида кальция. Покрытия без фтора, предназначенные для сварки в плоском положении, создают гладкие профили валика и легко удаляются шлаки. Более жидкий фторидный шлак, предназначенный для позиционной сварки, удалить труднее.
- Основные флюсы — высокая доля карбоната кальция (известняк) и фторида кальция (фторошпар) во флюсе снижает содержание кислорода в сварочной ванне и, следовательно, ее поверхностное натяжение.
Шлак более жидкий, чем шлак с рутиловым покрытием. Быстрое замерзание также способствует сварке в вертикальном и верхнем положениях, но шлаковое покрытие удалить труднее.
Следовательно, риск включения шлака значительно выше при использовании основных флюсов из-за присущего им выпуклого профиля сварного шва и сложности удаления шлака с подошв сварного шва, особенно при многопроходных сварных швах.
Сварочная техника
Сварочная техника играет важную роль в предотвращении образования шлаковых включений.Манипуляции с электродами должны обеспечивать соответствующую форму и степень перекрытия сварных швов, чтобы избежать образования карманов, в которых может скапливаться шлак. Таким образом, правильный размер электрода для подготовки шва, правильный угол к заготовке для хорошего проплавления и гладкий профиль сварного шва — все это важно для предотвращения уноса шлака.
При многопроходной вертикальной сварке, особенно с использованием основных электродов, необходимо позаботиться о расплавлении любых оставшихся мелких шлаковых карманов и минимизации подрезов.При использовании переплетения небольшая задержка на крайних краях переплетения будет способствовать сплавлению боковых стенок и созданию более плоского профиля сварного шва.
Слишком высокий ток в сочетании с высокой скоростью сварки также приведет к подрезу боковой стенки, что затрудняет удаление шлака.
Очень важно удалить весь шлак перед нанесением следующего цикла. Это можно сделать между прогонами путем шлифовки, легкого скалывания или чистки проволочной щеткой. Инструменты для очистки должны быть идентифицированы для различных материалов, например, стали или нержавеющей стали, и разделены.
При сварке сложными электродами, в стыковых стыках с узкими клиновыми швами или когда шлак задерживается из-за подрезов, может потребоваться шлифовка поверхности сварного шва между слоями, чтобы обеспечить полное удаление шлака.
Лучшие практики
Для предотвращения включения шлака можно использовать следующие методы:
- Используйте методы сварки для получения гладких сварных швов и соответствующей сварки между прогонами, чтобы избежать образования карманов для захвата шлака.
- Используйте правильный ток и скорость движения, чтобы избежать подрезания боковой стенки, что затруднит удаление шлака
- Удаляйте шлак между прогонами, уделяя особое внимание удалению шлака, застрявшего в щелях.
- Используйте шлифовку при сварке сложных стыковых соединений, в противном случае для удаления шлака может быть достаточно обработки проволочной щеткой или небольшого скола.
Стандарты приемки
Включения шлака и флюса являются линейными дефектами, но поскольку они не имеют острых краев по сравнению с трещинами, они могут быть разрешены определенными стандартами и правилами. Пределы для стали указаны в BE EN ISO 5817: 2007 для трех уровней качества.
Статья подготовлена Биллом Лукасом с помощью Джин Мазерс и Колин Эйлинс.
Эта статья Job Knowledge изначально была опубликована в Connect, сентябрь / октябрь 1999 г.Он был обновлен, поэтому веб-страница больше не отражает в точности печатную версию.
Welding — SteelConstruction.info
Сварка — это основная деятельность на заводе-изготовителе, которую осуществляют квалифицированные специалисты, работающие в системе управления качеством сварки под контролем ответственного координатора сварки. Он используется для подготовки стыков к подключению в магазине и на месте, а также для крепления других приспособлений и фурнитуры. На заводе-изготовителе для разных видов деятельности используются разные методы сварки.
По сути, в процессе сварки используется электрическая дуга для выработки тепла для плавления основного материала в соединении. Отдельный присадочный материал, поставляемый в качестве расходуемого электрода, также плавится и соединяется с основным материалом, образуя расплавленную сварочную ванну. По мере того, как сварка продолжается вдоль соединения, сварочная ванна затвердевает, сплавляя основной металл и металл сварного шва. Для заполнения стыка или нарастания сварного шва до проектного размера может потребоваться несколько проходов или проходов.
Welding
(Изображение любезно предоставлено William Haley Engineering Ltd.)
[вверх] Принципы дуговой сварки металлом
Терминология области сварного шва
Сварка — это сложное взаимодействие физических и химических наук. Правильное определение металлургических требований и разумное практическое применение являются предпосылкой для успешной сварки плавлением.
В процессе дуговой сварки металлическим электродом используется электрическая дуга для выработки тепла для плавления основного материала в соединении.Отдельный присадочный материал, поставляемый в качестве расходуемого электрода, также плавится и соединяется с основным материалом, образуя расплавленную сварочную ванну. Сварочная ванна подвержена атмосферному загрязнению и, следовательно, нуждается в защите во время критической фазы замерзания жидкости и твердого тела. Защита достигается либо за счет использования защитного газа, за счет покрытия бассейна инертным шлаком, либо за счет комбинации обоих действий.
В процессах с защитным газом от удаленного источника поступает газ, который подается на сварочную дугу через горелку или горелку.Газ окружает дугу и эффективно исключает атмосферу. Точный контроль необходим для поддержания подачи газа с соответствующей скоростью потока, так как слишком большое количество может вызвать турбулентность и засасывать воздух, а также может быть настолько же вредным, насколько и слишком маленьким.
В некоторых процессах используется флюс, который плавится в дуге для образования шлакового покрытия, которое, в свою очередь, покрывает сварочную ванну и защищает ее во время замерзания. Шлак также затвердевает и самораспускается или легко удаляется легким скалыванием. Действие плавления флюса также создает газовый экран для защиты.
По мере того, как сварка продолжается вдоль соединения, сварочная ванна затвердевает, сплавляя основной металл и металл сварного шва. Для заполнения стыка или нарастания сварного шва до проектного размера может потребоваться несколько проходов или проходов.
Тепло от сварки вызывает металлургические изменения в основном материале, непосредственно примыкающем к границе или линии плавления. Эта область изменения известна как зона термического влияния (HAZ). Общая терминология, используемая в области сварного шва, проиллюстрирована справа вверху.
Сварочные операции требуют надлежащего технологического контроля со стороны компетентных сварщиков, чтобы гарантировать достижение проектных характеристик, минимизировать риск дефектных соединений, вызванных плохим качеством сварки, и предотвратить образование склонных к образованию трещин микроструктур в ЗТВ.
[вверху] Типы сварных соединений
Большинство конструкционных сварных соединений выполняется на заводе-изготовителе и описывается как стыковые или угловые швы. Сварка на месте также возможна, и руководство по вопросам сварки на месте доступно в GN 7.01.
[вверх] Стыковые сварные швы
Макрос клиновидного стыкового шва
(Изображение любезно предоставлено Mabey Bridge Ltd.)
Стыковые сварные швы обычно представляют собой стыковые соединения катаных профилей или стыковые соединения листов на стенках и фланцах, чтобы приспособиться к изменению толщины или восполнить доступный материал по длине. Положения этих стыковых швов допускаются при проектировании, хотя ограничения доступности материалов или схемы монтажа могут потребовать согласования различных или дополнительных сварных швов.Тройники, приваренные встык, могут потребоваться, если при поперечных соединениях возникают значительные нагрузки или усталость.
Стыковые швы — это сварные швы с полным или частичным проплавлением, выполняемые между материалами со скошенными или скошенными кромками. Стыковые швы с полным проплавлением предназначены для передачи всей прочности сечения. Как правило, эти соединения можно сваривать с одной стороны, но по мере увеличения толщины материала желательна сварка с обеих сторон, чтобы уравновесить эффекты деформации, с операцией обратной строжки и / или обратной шлифовки в процессе для обеспечения целостности корень шва.Односторонние стыковые сварные швы с подкладными полосами из керамической или прочной стали обычно используются для соединения больших площадей пластин (например, стальных пластин настила) и там, где есть закрытые коробчатые секции, трубы или элементы жесткости, к которым можно получить доступ для сварки только с одного сторона. Расчетная толщина горловины определяет глубину проплавления, необходимую для швов с частичным проплавлением. Обратите внимание, что соображения усталости могут ограничивать использование сварных швов с частичным проплавлением, особенно на мостах. Руководство по подготовке к сварке доступно в GN 5.01.
Следует приложить все усилия, чтобы избежать стыковой сварки приспособлений из-за затрат, связанных с подготовкой, временем сварки, более высоким уровнем квалификации сварщиков и более строгими и трудоемкими требованиями к испытаниям. Кроме того, стыковые швы имеют тенденцию иметь большие объемы наплавленного металла шва; это увеличивает эффект усадки сварного шва и приводит к более высокому уровню остаточных напряжений в соединении. Чтобы уравновесить усадку и распределить остаточное напряжение, минимизируя таким образом деформацию, необходима тщательная последовательность сварочных операций.
Иногда бывает необходимо обработать стыковые сварные швы заподлицо по причинам усталости, или для улучшения дренажа стальных балок, устойчивых к атмосферным воздействиям, или для улучшения режима испытаний. Следует избегать зачистки заподлицо только по эстетическим соображениям, потому что трудно обработать поверхность, чтобы она соответствовала смежной поверхности после прокатки, и результат часто более визуально заметен, чем исходный сварной шов. Кроме того, шлифование представляет собой дополнительную опасность для здоровья и безопасности, которую лучше избегать, насколько это возможно. Правка стыковых швов до гладкой поверхности обычно не требуется для строительных стальных конструкций, поскольку обычно они не подвержены усталости.
- Пример обработанного стыкового шва с гладкой поверхностью и сливными пластинами
(изображения любезно предоставлены Mabey Bridge Ltd.)
[вверх] Угловые швы
Макрос однопроходного углового сварного шва
(Изображение любезно предоставлено Mabey Bridge Ltd.)
В большинстве сварных соединений в зданиях и мостах используются угловые швы, обычно в форме тройника. Обычно они включают в себя концевую пластину, ребро жесткости, подшипники и соединения распорок с прокатными секциями или плоскими балками, а также соединения стенки с фланцами на самих пластинчатых балках. Их относительно просто подготовить, сварить и испытать в обычных конфигурациях, при этом главным соображением является сборка стыков.
В S275 полная прочность сталей также развивается в угловых сварных швах и сварных швах с частичным проплавлением с вышележащими угловыми швами при условии, что такие сварные швы симметричны, выполнены с использованием правильных расходных материалов, а сумма сварных швов равна толщине элемента, который сварные швы стыкуются.
Размеры сварных швов должны быть указаны на чертежах проекта вместе с любыми специальными требованиями по классификации усталости. BS EN ISO 22553 [1] предписывает правила использования символов для детализации сварных соединений на чертежах.
Обращается внимание на тот факт, что в традиционной британской практике для определения размера углового сварного шва обычно используется длина ветви, но это не универсально: в европейской практике используется толщина горловины и BS EN 1993-1-8 [2] дает требования относительно размера горла, а не длины ноги. Проектировщик должен быть осторожен, чтобы убедиться, что ясно, какой размер указан, и что все стороны должны знать, что было указано.
[вверх] Процессы
Важными факторами, которые подрядчик по изготовлению металлоконструкций следует учитывать при выборе процесса сварки, являются способность выполнять проектные требования и, с точки зрения производительности, скорость наплавки, которая может быть достигнута, а также рабочий цикл или эффективность процесса. (Эффективность — это отношение фактического времени сварки или дуги к общему времени, в течение которого сварщик или оператор занят выполнением сварочной задачи.Общее время включает настройку оборудования, очистку и проверку выполненного шва.)
Ниже описаны четыре основных процесса сварки, которые регулярно используются при производстве стальных конструкций в Великобритании. Номера процессов определены в BS EN ISO 4063 [3] . Различные варианты этих процессов были разработаны для соответствия методикам и возможностям отдельных производителей, и другие процессы также имеют место для конкретных приложений, но выходят за рамки данной статьи.
[вверх] Металлоактивная газовая сварка (МАГ), процесс 135
Сварка MAG
(Изображение любезно предоставлено Kiernan Structural Steel Ltd.)
MAG-сварка сплошным проволочным электродом — это наиболее широко используемый процесс с ручным управлением для заводских производственных работ; иногда ее называют полуавтоматической сваркой или сваркой CO 2 . Сплошной проволочный электрод из сплошной проволоки пропускается через устройство подачи проволоки к «пистолету», который обычно удерживает и управляет оператором. Питание подается от источника выпрямителя или инвертора по соединительным кабелям к устройству подачи проволоки и кабелю горелки; электрическое подключение к проводу осуществляется через контактный наконечник на конце пистолета. Дуга защищена защитным газом, который направляется в зону сварки через кожух или сопло, окружающее контактный наконечник. Защитные газы обычно представляют собой смесь аргона, диоксида углерода и, возможно, кислорода или гелия.
Хорошая производительность наплавки и рабочий цикл можно ожидать от процесса, который также можно механизировать с помощью простых моторизованных тележек. Газовая защита может быть сдута сквозняками, что может вызвать пористость и возможные вредные металлургические изменения в металле сварного шва.Таким образом, этот процесс лучше подходит для заводского производства, хотя он используется на месте, где могут быть предусмотрены эффективные укрытия. Он также более эффективен в плоском и горизонтальном положениях; Сварные швы в других положениях наплавляются с более низкими параметрами напряжения и силы тока и более подвержены дефектам плавления.
Металлоактивная газовая сварка (МАГ), процесс 135
Металлоактивная газовая сварка (MAG), процесс 135
MAG-сварка электродом с флюсовой сердцевиной, процесс 136 представляет собой разновидность, в которой используется то же оборудование, что и MAG-сварка, за исключением того, что плавящийся проволочный электрод имеет форму трубки малого диаметра, заполненной флюсом.Преимущество использования этих проволок состоит в том, что можно использовать более высокие скорости наплавки, особенно при сварке в вертикальном положении (между двумя вертикальными поверхностями) или в верхнем положении. Наличие тонкого шлака помогает преодолевать силу тяжести и позволяет наносить сварные швы в местах с относительно высокими током и напряжением, тем самым снижая вероятность дефектов плавления. Добавки флюса также влияют на химию сварного шва и, таким образом, улучшают механические свойства соединения.
[вверху] Ручная дуговая сварка металлом (MMA), процесс 111
Этот процесс остается наиболее универсальным из всех сварочных процессов, но его использование в современной мастерской ограничено.Трансформаторы переменного тока, выпрямители постоянного тока или инверторы подают электроэнергию по кабелю на электрододержатель или клещи. Проволочный электрод с флюсовым покрытием (или «стержень») вставляется в держатель, и сварочная дуга возникает на кончике электрода, когда он ударяется о заготовку. На острие электрода плавится, образуя ванну расплава, которая сплавляется с основным материалом, образуя сварной шов. Флюс также плавится, образуя защитный шлак и создавая газовый экран, предотвращающий загрязнение сварочной ванны по мере ее затвердевания.Добавки флюса и сердечник электрода используются для влияния на химический состав и механические свойства сварного шва.
Обычно используются электроды с основным покрытием, контролируемым водородом. Эти электроды необходимо хранить и обращаться с ними в соответствии с рекомендациями производителя расходных материалов, чтобы сохранить их низкие водородные характеристики. Это достигается либо путем использования сушильных шкафов и подогреваемых колчанов для хранения и обработки продукта, либо путем приобретения электродов в герметичных упаковках, специально разработанных для поддержания низкого уровня водорода.
Недостатками процесса являются относительно низкая скорость осаждения и высокий уровень отходов, связанных с непригодными концевыми штырями электродов. Тем не менее, он остается основным процессом для сварки на стройплощадке и для труднодоступных мест, где громоздкое оборудование не подходит.
Ручная дуговая сварка металлом (MMA), процесс 111
Ручная дуговая сварка металлом (MMA), процесс 111
[вверх] Дуговая сварка под флюсом (SAW), процесс 121
Оперативная сварка под флюсом
(Изображение любезно предоставлено Mabey Bridge Ltd.)
Это, вероятно, наиболее широко используемый процесс для сварки угловых швов перемычки между стенкой и фланцем и стыковых стыковых швов на толстой пластине для получения отрезков фланца и стенки. В процессе процесса непрерывный провод подается через контактный наконечник, где он обеспечивает электрический контакт с мощностью от выпрямителя, в зону сварки, где он изгибается и образует ванну расплава. Сварочная ванна заполняется флюсом, подаваемым из бункера. Флюс, непосредственно покрывающий расплавленную сварочную ванну, плавится, образуя шлак и защищая сварной шов во время затвердевания; излишки флюса собираются и повторно используются.По мере остывания шва шлак замерзает и отслаивается, оставляя высококачественные профильные швы.
Этот процесс по своей природе более безопасен, чем другие процессы, так как дуга полностью покрывается во время сварки, отсюда и термин дуга под флюсом. Это также означает, что требования к личной защите меньше. Высокая производительность наплавки — особенность процесса, поскольку он обычно механизируется на портальных установках, тракторах или другом специализированном оборудовании. Это позволяет контролировать параметры и дает рекомендации по точному размещению сварных швов.
Сварка под флюсом (SAW), процесс 121
Сварка под флюсом (SAW), процесс 121
[вверх] Приварка шпилек методом вытяжной дуги, способ 783
Композитные мосты требуют приваривания соединителей со срезными шпильками к верхнему фланцу пластинчатых или коробчатых балок и в других местах, где требуется композитное воздействие стали на бетон, например.грамм. на интегральных абатментах. В зданиях композитные балки требуют приварки соединителей срезных шпилек к элементам либо непосредственно к верхнему фланцу, либо чаще через постоянный настил из оцинкованной стали на композитных полах, где верхний фланец балки остается неокрашенным.
Приварка шпильки к балке моста
(Изображение любезно предоставлено Mabey Bridge Ltd.)Сварка сквозных шпилек
(Изображение любезно предоставлено Structural Metal Decks Ltd.)
Метод приварки шпилек известен как процесс с натянутой дугой, и требуется специальное оборудование в виде мощного выпрямителя и специального пистолета. Шпильки загружаются в пистолет, и при электрическом контакте с изделием концевые дуги сгибаются и плавятся. Продолжительность дуги рассчитывается так, чтобы между концом шпильки и основным материалом установилось расплавленное состояние. В нужный момент пистолет погружает шпильку в сварочную ванну.Керамическая манжета окружает шпильку для защиты и поддержки сварочной ванны, стабилизации дуги и формовки смещенной сварочной ванны для формирования сварной манжеты. Когда сварной шов затвердевает, обойма отслаивается. У удовлетворительных сварных швов обычно есть ровная, яркая и чистая буртика, полностью охватывающая шпильку.
Приварка шпилек методом вытяжной дуги 783
[вверху] Спецификации процедуры сварки
Чертежи детализируют конструктивную форму, выбор материала и указывают сварные соединения.Подрядчик по изготовлению металлоконструкций выбирает методы сварки каждой конфигурации стыка, обеспечивающие требуемые характеристики. Прочность, вязкость разрушения, пластичность и усталость являются важными металлургическими и механическими свойствами, которые необходимо учитывать. Тип соединения, положение сварки, производительность и требования к ресурсам влияют на выбор подходящего процесса сварки.
Выбранный метод представлен в спецификации процедуры сварки (WPS), в которой подробно описывается информация, необходимая для инструктирования и руководства сварщиками, чтобы обеспечить повторяемость характеристик для каждой конфигурации соединения.Пример формата WPS показан в Приложении A стандарта BS EN ISO 15609-1 [4] . Подрядчики по изготовлению металлоконструкций могут иметь свой собственный корпоративный шаблон, но все они включают важную информацию, позволяющую передать сварщику надлежащие инструкции.
Необходимо подкрепить WPS свидетельством об удовлетворительных испытаниях процедуры в виде протокола аттестации процедуры сварки (WPQR), подготовленного в соответствии с BS EN ISO 15614-1 [5] . Введение этого стандарта гласит, что испытания процедуры сварки, проведенные в соответствии с прежними национальными стандартами и спецификациями, не аннулируются при условии их технической эквивалентности; Для этого могут потребоваться дополнительные тесты.Основные подрядчики по изготовлению металлоконструкций в Великобритании прошли предварительную квалификацию сварочных работ, позволяющих производить удовлетворительные сварные швы в большинстве конфигураций стыков, которые могут встретиться в сталелитейном строительстве и в мостовой промышленности.
В случаях, когда данные предыдущих испытаний не имеют отношения к делу, необходимо провести испытание процедуры сварки, чтобы установить и подтвердить пригодность предлагаемого WPS.
Руководство по стандартным спецификациям процедуры сварки для стальных конструкций доступно в публикации BCSA No.58/18.
[вверх] Процедура испытаний
BS EN ISO 15614-1 [5] описывает условия проведения испытаний процедуры сварки и пределы действия в пределах квалификационных диапазонов, указанных в стандарте. Координатор сварки подготавливает предварительную спецификацию процедуры сварки (pWPS), которая является первоначальным предложением для проведения испытания процедуры. Для каждой конфигурации стыка, будь то стыковой или угловой шов, учитывается марка и толщина материала, а также ожидаемые допуски посадки, которые могут быть достигнуты на практике.Выбор процесса определяется методом сборки, положением сварки и тем, является ли механизация жизнеспособным предложением для повышения производительности и обеспечения постоянного качества сварки. Размеры подготовки швов зависят от выбора процесса, любых ограничений доступа и толщины материала.
Расходные материалы выбираются из соображений совместимости с марками материалов и достижения указанных механических свойств, в первую очередь с точки зрения прочности и ударной вязкости. Для сталей марки S355 и выше используются продукты с водородным контролем.
Риск водородного растрескивания, пластинчатого разрыва, растрескивания при затвердевании или любой другой потенциальной проблемы оценивается не только с целью проведения испытания, но и для предполагаемого применения процедуры сварки в проекте. Соответствующие меры, такие как предварительный или последующий нагрев, включены в pWPS.
Контроль искажений обеспечивается правильной последовательностью сварки. При необходимости вводятся обратная строжка и / или обратное шлифование для достижения целостности корневого шва.
Приведены диапазоны сварочного напряжения, тока и скорости для определения оптимальных условий сварки.
Допустимые диапазоны групп материалов, толщины и типа соединения в пределах спецификации тщательно рассматриваются, чтобы максимально использовать pWPS. Подготавливают испытательные пластины достаточного размера для извлечения образцов для механических испытаний, включая образцы для любых дополнительных испытаний, указанных или необходимых для повышения применимости процедуры.
Пластины и pWPS предъявляются сварщику; испытание проводится в присутствии эксперта (обычно из независимого проверяющего органа), и ведется запись фактических параметров сварки вместе с любыми необходимыми изменениями процедуры.
Завершенные испытания передаются независимому эксперту для визуального осмотра и неразрушающего контроля в соответствии с таблицей 1 Стандарта. Удовлетворительные испытательные пластины затем отправляются на разрушающий контроль, опять же в соответствии с таблицей 1. Неразрушающие методы контроля, как правило, включают ультразвуковой контроль для объемного контроля и контроль магнитных частиц для выявления дефектов поверхности.
Пример испытательного образца процедуры сварки
(Изображение любезно предоставлено Mabey Bridge Ltd.)
Существует ряд дополнительных стандартов, детализирующих подготовку, обработку и испытания всех типов образцов для разрушающих испытаний. Обычно специализированные лаборатории организуют подготовку образцов для испытаний и проводят фактические механические испытания и составление отчетов. Типичные образцы для стыкового сварного шва пластины включают испытания на поперечное растяжение, испытания на поперечный изгиб, испытания на удар и образец для макроисследования, на котором проводится испытание на твердость.Для испытаний на удар минимальные требования к поглощению энергии и температура испытания обычно такие же, как и для основного материала в соединении. Целесообразно проверить все сварочные процедуры до предела возможного применения, чтобы избежать повторения подобных испытаний в будущем.
Завершенные результаты испытаний заносятся в протокол аттестации процедуры сварки (WPQR), утверждаемый экзаменатором. Типичный формат показан в Приложении B стандарта BS EN ISO 15614-1 [5] .
Существует дополнительное общее требование, касающееся испытаний процедуры сварки, согласно которому, если грунтовки для краски должны быть нанесены на работу до изготовления, они должны наноситься на образец материала, используемого для испытаний. На практике требуется тщательный контроль толщины краски, чтобы избежать дефектов сварки.
BS EN ISO 14555 [6] описывает метод процедуры испытания соединителей шпилек, приваренных дуговой сваркой. Стандарт включает требования к испытаниям, необходимым для подтверждения целостности сварных швов шпилек, а также устанавливает требования к производственным испытаниям для контроля приваривания шпилек в процессе.Допускается также квалификация, основанная на предыдущем опыте, и большинство подрядчиков по изготовлению стальных конструкций могут предоставить доказательства, подтверждающие это.
Дополнительное руководство по испытаниям процедуры сварки доступно в GN 4.02.
[вверх] Водородный крекинг
Растрескивание может привести к хрупкому разрушению соединения с потенциально катастрофическими последствиями. Водородное (или холодное) растрескивание может происходить в области основного металла, прилегающей к границе плавления сварного шва, известной как зона термического влияния (HAZ).Разрушение металла сварного шва также может быть вызвано определенными условиями. Механизмы, вызывающие отказ, сложны и подробно описаны в специальных текстах.
Рекомендуемые методы предотвращения растрескивания водородом / HAZ описаны в BS EN 1011-2 [7] , приложение C. Эти методы определяют уровень предварительного нагрева для изменения скорости охлаждения, что дает время водороду для миграции на поверхность. и ускользнуть (особенно если поддерживается в виде пост-нагревания после завершения соединения) вместо того, чтобы застревать в жестких, напряженных зонах.Предварительный нагрев не препятствует образованию микроструктур, подверженных образованию трещин; он просто снижает один из факторов, водород, так что растрескивания не происходит. Предварительный нагрев также снижает термический шок.
Подставки для предварительного нагрева
(Изображение любезно предоставлено Mabey Bridge Ltd.)
Одним из параметров, необходимых для расчета предварительного нагрева, является погонная энергия. Заметным изменением в стандарте является отказ от термина «энергия дуги» в пользу тепловложения для описания энергии, вводимой в сварной шов на единицу длины прогона.Расчет подводимого тепла основан на сварочном напряжении, токе и скорости движения и включает коэффициент теплового КПД; формула подробно описана в BS EN 1011-1 [8] .
Высокая устойчивость и повышенные значения углеродного эквивалента, связанные с более толстыми листами и более высокими марками стали, могут потребовать более строгого контроля процедур. Опытные подрядчики по изготовлению металлоконструкций могут выполнить эту дополнительную операцию и соответственно учесть ее.
BS EN 1011-2 [7] подтверждает, что наиболее эффективной гарантией предотвращения водородного растрескивания является снижение поступления водорода в металл шва из сварочных материалов.Процессы с изначально низким водородным потенциалом эффективны как часть стратегии, так же как и принятие строгих процедур хранения и обращения с электродами с водородным контролем. Данные и рекомендации поставщиков расходных материалов служат руководством для обеспечения минимально возможных уровней водорода для типа продукта, выбранного в процедуре.
Дополнительные информативные приложения к BS EN 1011-2 [7] описывают влияние условий сварки на ударную вязкость и твердость в зоне термического влияния и дают полезные советы по предотвращению растрескивания при затвердевании и разрыва пластин.
Дополнительное руководство по крекингу водородом / HAZ доступно в GN 6.04.
[вверх] Квалификация сварщика
Квалифицированный сварщик
(Изображение предоставлено Mabey Bridge Ltd.)
BS EN 1090-2 [9] требует, чтобы сварщики имели квалификацию в соответствии с BS EN ISO 9606-1 [10] . Этот стандарт предписывает испытания для аттестации сварщиков в зависимости от процесса, расходных материалов, типа соединения, положения сварки и материала.Сварщики, прошедшие успешные испытания процедуры, автоматически получают одобрение в пределах квалификационных диапазонов, установленных стандартом. Сварщики должны быть аттестованы в соответствии с BS EN ISO 14732 [11] , когда сварка полностью механизирована или автоматическая. В этом стандарте особое внимание уделяется проверке способности оператора настраивать и настраивать оборудование до и во время сварки.
Квалификация сварщика ограничена по времени и требует подтверждения действительности в зависимости от продолжительности работы, участия в работе соответствующего технического характера и удовлетворительной работы.Продление квалификации сварщика зависит от зарегистрированных подтверждающих свидетельств, демонстрирующих продолжающуюся удовлетворительную работу в пределах исходного диапазона испытаний, и доказательства должны включать либо объемные разрушающие испытания, либо разрушающие испытания. Успех всех сварочных операций зависит от персонала, имеющего соответствующую подготовку и регулярного контроля компетентности посредством инспекций и испытаний.
[вверх] Инспекция и испытания
BS EN 1090-2 [9] устанавливает объем проверки до, во время и после сварки и дает критерии приемки, связанные с классом исполнения.Большинство испытаний являются неразрушающими; Разрушающие испытания проводятся только на отводных плитах.
[вверх] Неразрушающий контроль
Магнитный контроль частиц (MPI) сварного шва
(Изображение любезно предоставлено Mabey Bridge Ltd.)
Неразрушающий контроль проводится в соответствии с принципами BS EN ISO 17635 [12] . Для стальных конструкций основными методами являются визуальный контроль после сварки (см. GN 6.06), магнитопорошковый контроль (обычно сокращенно MPI или MT) для поверхностного контроля сварных швов (см. GN 6.02) и ультразвуковой контроль (UT) для подповерхностного контроля сварных швов (см. GN 6.03). Радиографические испытания также упоминаются в BS EN 1090-2 [9] . Радиография требует строгого контроля за здоровьем и безопасностью; это относительно медленно и требует специального оборудования. Использование этого метода в стальных конструкциях снизилось по сравнению с более безопасным и портативным оборудованием, связанным с UT.Безопасные запретные зоны необходимы на работах и на месте во время проведения рентгенографии. Однако рентгенографию можно использовать для уточнения природы, размеров или степени множественных внутренних дефектов, обнаруженных ультразвуком.
Технические специалисты с признанной подготовкой и квалификацией в соответствии с BS EN ISO 9712 [13] требуются для всех методов неразрушающего контроля.
BS EN 1090-2 [9] требует, чтобы все сварные швы подвергались визуальному контролю по всей их длине.С практической точки зрения сварные швы следует визуально осматривать сразу после сварки, чтобы гарантировать своевременное устранение очевидных дефектов поверхности.
Дальнейшие требования к неразрушающему контролю основаны на эксплуатационных методах и требуют более строгого исследования первых пяти соединений новых технических требований к процедуре сварки, чтобы установить, что процедура способна производить сварные швы соответствующего качества при внедрении в производство. Затем указываются дополнительные неразрушающие испытания, основанные на типах соединений, а не на конкретных критических соединениях.Цель состоит в том, чтобы опробовать различные сварные швы в зависимости от типа соединения, марки материала, сварочного оборудования и работы сварщиков и, таким образом, поддерживать общий мониторинг производительности.
Если указано частичное или процентное обследование, руководство по выбору продолжительности испытания дано в BS EN ISO 17635 [12] ; при обнаружении недопустимых разрывов площадь исследования соответственно увеличивается.
BS EN 1090-2 [9] также включает в таблицу минимальное время выдержки перед дополнительным неразрушающим контролем на основе размера сварного шва, подводимой теплоты и марки материала.
Признавая, что там, где требования к усталостной прочности более обременительны и требуется более строгая проверка, BS EN 1090-2 [9] действительно предусматривает спецификацию выполнения проекта для определения конкретных соединений для более высокого уровня проверки вместе с объемом и метод тестирования.
Для класса EXC3 критерием приемлемости дефектов сварного шва является уровень качества B стандарта BS EN ISO 5817 [14] . Там, где необходимо достичь повышенного уровня качества для удовлетворения конкретных требований к усталостной прочности, BS EN 1090-2 [9] дает дополнительные критерии приемлемости с точки зрения категории деталей в BS EN 1993-1-9 [15] для расположения сварного шва.
Как правило, дополнительные критерии приемки практически не достижимы при обычном производстве. Стандартные испытания процедуры сварки и квалификационные испытания сварщика не оцениваются по требованиям этого уровня. Там, где необходимо достичь такого уровня качества, требования должны быть сосредоточены на соответствующих деталях соединения, чтобы подрядчик имел возможность подготовить спецификации процедуры сварки, квалифицировать сварщиков и разработать соответствующие методы контроля и испытаний.
Неразрушающий контроль
[наверх] Разрушающий контроль
В стандарте BS EN 1090-2 [9] нет требований о проведении разрушающих испытаний поперечных соединений в натяжных фланцах. Тем не менее, объем для определения конкретных соединений для проверки позволит в спецификации проекта испытать, например, образцы от «стекающих» пластин, прикрепленных к встроенным стыковым сварным швам. Дополнительно производственные испытания могут быть указаны для: марок стали выше S460; угловые швы, в которых используются характеристики глубокого проплавления сварочного процесса; для мостовидных ортотропных настилов, где требуется макросъемка для проверки проплавления сварного шва; и на соединениях ребер жесткости с соединительными пластинами.
[вверх] Производственные испытания приварки шпилек
Испытание на изгиб приварной шпильки
(Изображение любезно предоставлено Mabey Bridge Ltd.)
Сварные шпильки для соединителей, работающих на сдвиг, исследуются и испытываются в соответствии с BS EN ISO 14555 [6] . В стандарте подчеркивается необходимость контроля процесса до, во время и после сварки. Предпроизводственные испытания используются для подтверждения процедуры сварки и, в зависимости от области применения, включают испытания на изгиб, испытания на растяжение, испытания на крутящий момент, макросъемку и радиографическое обследование.
Производственные испытания сварных швов также требуются для приварки шпилек с дугой протяжки. Они должны выполняться производителем до начала сварочных работ на конструкции или группе аналогичных конструкций и / или после определенного количества сварных швов. Каждое испытание должно состоять как минимум из 10 сварных шпилек и быть испытано / оценено в соответствии с требованиями BS EN ISO 14555 [6] . Количество необходимых тестов должно быть указано в спецификации контракта.
[вверх] Качество сварки
Влияние дефектов на характеристики сварных соединений зависит от приложенной нагрузки и свойств материала.Эффект также может зависеть от точного расположения и ориентации дефекта, а также от таких факторов, как рабочая среда и температура. Основное влияние дефектов сварного шва на эксплуатационные характеристики стальных конструкций заключается в повышении риска разрушения из-за усталости или хрупкого разрушения.
Типы дефектов сварки можно разделить на одну из нескольких общих рубрик:
- Трещины.
- Плоские дефекты, кроме трещин, например непробиваемость, отсутствие плавления.
- Включения шлака.
- Пористость, поры.
- Поднутрения или дефекты профиля.
Трещины или плоские дефекты, проникающие через поверхность, потенциально являются наиболее серьезными. Включения вкрапленного шлака и пористость вряд ли станут причиной разрушения, если только они не будут чрезмерными. Подрезание обычно не является серьезной проблемой, если не существует значительных растягивающих напряжений поперек стыка.
Путем выбора класса исполнения в BS EN 1090-2 [9] устанавливаются критерии приемки, при превышении которых дефект считается дефектом.
Если дефекты обнаружены в результате осмотра и испытаний во время производства, вероятно, потребуется обработка после сварки (см. GN 5.02) или другие меры по исправлению положения, хотя во многих случаях конкретный дефект может быть оценен по концепции « пригодность для цели ». Такое принятие зависит от фактических уровней напряжения и значимости усталости на месте. Это вопрос быстрой консультации между подрядчиком по изготовлению металлоконструкций и проектировщиком, поскольку, если это приемлемо, можно избежать дорогостоящего ремонта (и возможности появления дополнительных дефектов или деформации).
Руководство по контролю качества сварных швов и контролю сварных швов доступно в BCSA № 54/12 и GN 6.01.
[вверх] Список литературы
- ↑ BS EN ISO 22553: 2019, Сварка и родственные процессы. Символическое изображение на чертежах. Сварные соединения. BSI.
- ↑ BS EN 1993-1-8: 2005, Еврокод 3. Проектирование стальных конструкций. Дизайн стыков, BSI
- ↑ BS EN ISO 4063: 2010, Сварка и родственные процессы. Номенклатура процессов и ссылочные номера, BSI
- ↑ BS EN ISO 15609-1: 2019, Технические требования и квалификация процедур сварки металлических материалов.Спецификация процедуры сварки. Дуговая сварка, BSI
- ↑ 5,0 5,1 5,2 BS EN ISO 15614-1: 2017 + A1: 2019, Технические требования и квалификация процедур сварки металлических материалов. Проверка процедуры сварки. Дуговая и газовая сварка сталей и дуговая сварка никеля и никелевых сплавов, BSI
- ↑ 6,0 6,1 6,2 BS EN ISO 14555: 2017, Сварка. Дуговая сварка металлических материалов, BSI
- ↑ 7.0 7,1 7,2 BS EN 1011-2: 2001, Сварка. Рекомендации по сварке металлических материалов. Дуговая сварка ферритных сталей, BSI
- ↑ BS EN 1011-1: 2009, Сварка. Рекомендации по сварке металлических материалов. Общее руководство по дуговой сварке, BSI
- ↑ 9,0 9,1 9,2 9,3 9,4 9,5 9,6 9,7 9,8 BS EN 1090-2: 2018, Изготовление металлоконструкций и алюминиевых конструкций.Технические требования к стальным конструкциям, BSI
- ↑ BS EN ISO 9606-1: 2017 Квалификационные испытания сварщиков. Сварка плавлением. Стали, BSI
- ↑ BS EN ISO 14732: 2013. Сварочный персонал. Квалификационные испытания сварщиков и наладчиков механизированной и автоматической сварки металлических материалов BSI
- ↑ 12,0 12,1 BS EN ISO 17635: 2016, Неразрушающий контроль сварных швов. Общие правила для металлических материалов, BSI
- ↑ BS EN ISO 9712: 2012.Неразрушающий контроль. Квалификация и аттестация персонала по неразрушающему контролю, BSI
- ↑ BS EN ISO 5817: 2014, Сварка. Соединения, сваренные плавлением из стали, никеля, титана и их сплавов (за исключением лучевой сварки). Уровни качества для выявления недостатков, BSI
- ↑ BS EN 1993-1-9: 2005, Еврокод 3. Проектирование стальных конструкций. Усталость, BSI
[вверх] Ресурсы
- Стальные здания, 2003 г. (Публикация № 35/03), BCSA
- Стальные мосты: практический подход к проектированию для эффективного изготовления и строительства, 2010 г. (Публикация №51/10), BCSA
- Национальная спецификация на стальные конструкции (7-е издание), 2020 г. (Публикация № 62/20), BCSA
- Типовые спецификации процедуры сварки металлоконструкций — Второе издание, 2018 г. (Публикация № 58/18), BCSA
- Высокопрочные стали для применения в конструкциях: Руководство по изготовлению и сварке, 2020 г. (Публикация № 62/20), BCSA
- Руководство по контролю сварных швов металлоконструкций, 2012 г. (Публикация № 54/12), BCSA
- Хенди, К.Р.; Ильес, округ Колумбия (2015) Steel Bridge Group: Рекомендации по передовой практике в строительстве стальных мостов (6-й выпуск). (P185). SCI
[вверху] Дополнительная литература
- Руководство проектировщика металлоконструкций (7-е издание), 2011 г., глава 26 — Сварные швы и проектирование для сварки, Институт стальных конструкций.
[вверху] См. Также
Полуавтомат для контурной обработки сварных швов. Заключительный отчет (технический отчет)
Шоу, К.P. Полуавтомат для контурной обработки кромок сварного шва. Заключительный отчет . США: Н. П., 1983.
Интернет. DOI: 10,2172 / 5942271.
Shaw, C. P. Полуавтоматическое оборудование для контурной обработки сварных швов. Заключительный отчет . Соединенные Штаты. https://doi.org/10.2172/5942271
Шоу, К.П. Пт.
«Полуавтоматы для контурной обработки сварных швов. Заключительный отчет». Соединенные Штаты. https://doi.org/10.2172/5942271. https://www.osti.gov/servlets/purl/5942271.
@article {osti_5942271,
title = {Полуавтоматическое оборудование для контурной обработки сварных швов. Заключительный отчет},
author = {Шоу, К. П.},
abstractNote = {Цель заключалась в разработке машины, которая могла бы обрабатывать наплавленные сварные швы до допусков поверхности, которые повышают надежность ультразвукового контроля, необходимого для атомных электростанций.Изготовлены и испытаны три внешних токарных станка с микропроцессорным управлением. Эти устройства можно запрограммировать на создание гладкого контура - подходящего для требуемого ультразвукового контроля - через сварные швы трубы, даже если трубы не круглые, концентрические или не одного диаметра. Окончательные модели были успешно испытаны в лабораторных условиях, а самая последняя версия позволила коснуться как горизонтальных, так и вертикальных швов в смоделированных полевых условиях. Последние прототипы обеспечивают чистоту поверхности со среднеквадратичным отклонением 250 микродюймов или лучше при осевой скорости подачи 0.010 дюймов на оборот и окружная скорость подачи 2,5 дюйма в секунду или четыре оборота в минуту на 12-дюймовой трубе из нержавеющей стали.
Добавить комментарий