Как приварить бутылку к листу стали — Безумные идеи
на форуме ОСТМетал,прочитал вот такую басню:
Тем сварщикам, которые считают, что достигли вершин мастерства ПОСВЯЩАЕТСЯ.
Расскажу легенду нашего монтажного управления.
Лет …дцать назад работал у нас некий сварщик. Назовем его Сан Саныч. Отличался Сан Саныч не только своей рассудительностью и заслуженным уважением коллег по цеху, но и качественной сваркой металлов и не только…
Когда происходил Новый Год, на работе неизменно появлялись бутылки «Советского» шампанского.
После традиционного распития содержимого, начиналось шоу. Монтажники начинали канючить: «Сан Саныч, привари бутылку!».
Невозмутимый Сан Саныч брал пустую бутылку из под пенного напитка, сгребал в кулак несколько электродов (обычных УОНИ), подмастерья волокли в закуток (от посторонних глаз) обрезок листа потолще, и Сан Саныч уединялся с держаком и маской.
Через некоторое время, уважаемый Волшебник Голубого Огня выносил из закутка бутылку шампанского, ПРИВАРЕННУЮ к стальному листу вкруговую.
История правдива, потому что рассказана она ныне здравствующими ветеранами монтажа, которые и были теми самыми заводилами: «Сан Саныч, Привари бутылку!».
Уважаемые современники — попробуйте догнать дедов! Удачи! .
P.S. С обычными бутылками можете не экспериментировать. Ничего не выйдет. Нужна бутылка из под шампанского.
P.P.S. Про методы «РУЧНОЙ дуговой сварки покрытыми электродами» типа:
«ногой»,
«вообще не касаясь держака»
говорить не буду, потому как эти способы «ручной» сварки знают все.
Во всяком случае монтажники — точно
Кто не знает, ВНИМАТЕЛЬНО прочитайте в любом учебнике по сварочному делу раздел «Техника ручной сварки». После прочтения, подключите фантазии грамм на 250, и Вы легко научитесь варить любым из вышеизложенных способов. :sorry:
Я вот до сих пор не могу вкурить,в чём тут юмор,и возможно ли ваще сие действо с положительным результатом(признаюсь чесно ,сам не пробывал…)
Как сделать отверстие в дне стеклянной бутылки. Как просверлить стеклянную бутылку в домашних условиях видео
- — пневматический пистолет;
- — дрель с алмазным или закаленным стальным сверлом;
- — скипидар;
- — серная кислота;
- — вода;
- — песок или глина;
- — шаблон из дерева, пенопласта, стекла, металла или другого материала;
- — наждачный порошок.
Инструкция
Самый быстрый способ: возьмите с хорошо заряженным баллоном. Встаньте на расстоянии нескольких метров, тщательно прицельтесь и выстрелите в бутылку. Вылетевший шарик пробьет бутылку из- насквозь, не разбив ее. Учтите, что отверстий будет два, причем довольно маленького диаметра.
Чтобы просверлить в бутылке отверстие нужного диаметра, сначала приготовьте приспособление для надежной фиксации посуды, например, коробку, в которой она будет плотно сидеть.
Чтобы просверлить отверстие в стеклянной бутылке стальным сверлом, перед употреблением нагрейте его добела и смочите в серной кислоте.
Чтобы просверлить отверстие большого диаметра, возьмите трубку из цветного металла (алюминий, латунь, медь, бронза) длиной 2,5-5 см и используйте ее в качестве сверла. К стеклу прикрепите кружок из пенопласта, стекла, дерева, металла или другого материала нужного диаметра, в него будет упираться трубка при сверлении. Насыпьте в открытый конец трубки смоченный водой наждак и медленно сверлите, на небольших оборотах. Следите, чтобы наждачная паста всегда была между краями трубки и стеклом.
Если вы хотите обойтись без сверления, возьмите глину или мелкий песок. Тщательно отмойте поверхность от жира и грязи при помощи ацетона, спирта или бензина. Насыпьте мокрый песок или глину, размешанную до тестообразного состояния, в виде горки высотой около 10 мм. Сделайте воронку палочкой или другим инструментом, при этом диаметр просвечивающего стекла внутри ямки должен соответствовать диаметру желаемого отверстия. Расплавьте в металлической баночке свинец, олово или другой припой, залейте его в полученной лунку. Отверстие получится с гладкими краями, но учите, что этот способ подходит для стекла не толще 3 мм.
Сегодня мы делаем новогодний светильник. Для этого понадобится несколько простых вещей. Самое главное – нужно решить, как просверлить стеклянную бутылку. Способ подойдет тот, который доступен в домашних условиях.
В принципе, проделать дырку в стеклянной бутылке удастся и простым сверлом. Обычным по металлу, твердосплавным победитовым наконечником. Специальным по керамике. Но мы выбираем самый лучший вариант – это сверло с алмазным напылением. Так как диаметр его 12 мм, мы другим сверлом того же размера делаем отверстие в деревянной планки. Это будет направляющая. Алмазное сверло не имеет центра и работать им без предварительной подготовки обрабатываемой поверхности тяжело. Как видим, отверстие вышло идеальным.
Берем стеклянную винную бутылку. Из обычного пластилина делаем формочку для воды. Она будет охлаждать сверло. Сверху накладываем шаблон и фиксируем малярной лентой. Теперь направляющие никуда не денется с ее помощью удобно удерживать бутылку на столе. Заполняем буду практически доверху. Начинаем сверления на маленьких оборотах. Отверстие просто идеальное для домашних условий. Небольшие сколы остались от того, что не ослабил давление до минимума.
Края тут не опасны, но всё равно пройдёмся наждачной бумагой. Резиновая пробка, чтобы провод не терся о край стекла.
В данном примере использовались лампочки накаливания, поэтому температура в бутылке достигла почти 100 градусов, это за полчаса. Опасная штука! Вытащив пробку, мастер надеялся увеличить вентиляцию, но это не помогло. Температура не спадала. Неужели сказки не будет? Не переживайте! Ее спасут современные технологии. Старые гирлянды пойдут кому-нибудь на подарок. А мы будем использовать современные светодиодные. Хотя такие же китайские, как прежние. В ту же бутылку заправляем их. Всё работает. Термометр показывает 23 градуса. Выставляем режим постоянного свечения и оставляем на полчаса. Через некоторое время температура поднялась всего на несколько градусов. Крепим регулятор на двухсторонний скотч для удобства. Всё. Сказке быть! Порекомендуйте это видео друзьям, может быть им тоже захочется увидеть подобную красоту.
Как просверлить бутылку простым сверлом
Как сделать отверстие в стеклянной бутылке
Здравствуйте, мои дорогие друзья! Роман с тобой, как обычно. Было два вопроса: один – как сделать отверстие в стеклянной бутылке, а второй – как разрезать стеклянную бутылку. Я отвечу на второй вопрос чуть позже, так как я провожу эксперименты и ищу наиболее удобный способ сделать это.
Давайте начнем отвечать на первый вопрос. Вот бутылка вина. Я сделал такую подставку с простыми деревянными перилами заранее. Это поможет избежать перемещения бутылки при сверлении отверстия. Если вы не можете сделать такую стойку, вы можете вырыть яму в земле, положить два кирпича или два скота, это зависит от вашего воображения. Первое, что нам нужно сделать, это обернуть бумажный скотч вокруг бутылки рядом с местом отверстия.
Мы собираемся использовать простую дрель, конечно, лучше использовать отвертку, так как она имеет низкую скорость вращения и нам не нужна высокая скорость вращения для сверления стекла. Сверло простое, без пыли из карбида вольфрама.
Это сверло 8,2 мм, сталь Р6М5. Давайте начнем. Важно не сильно нажимать на дрель, потому что стекло может треснуть, и мы не сможем его обработать. Итак, позвольте мне показать вам, что мы получили. Как видите, стекло начало сверлиться.
Важно также добавить немного воды в отверстие, чтобы не перегреть дрель и стеклянную бутылку.
Ну, мы сделали дыру.
Давайте удалим скотч и посмотрим, что у нас там. У нас есть такая дыра. Если вы посмотрите поближе, вы заметите небольшие трещины внутри, это вызвано избыточным давлением сверла в конце. Если вы контролируете нажатие сверла, особенно в конце сверления, когда отверстие почти сделано, вы получите идеальное отверстие.
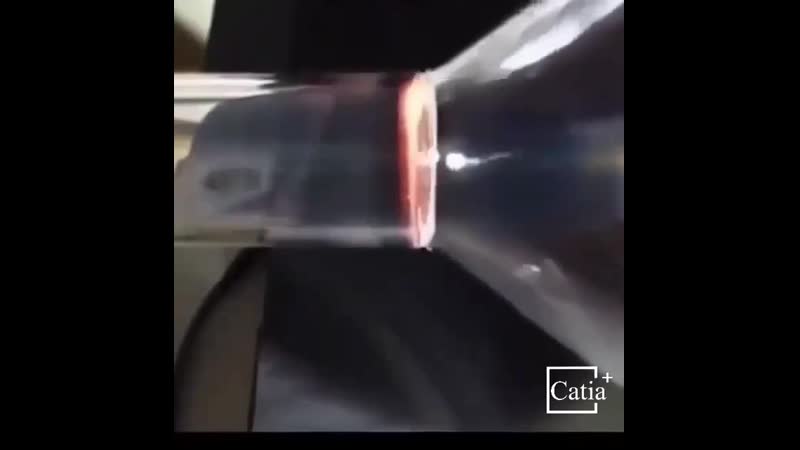
Источник: crazyinvent.com
Металлическое кольцо в бутылке с колой: сверлим бутылку
Это то, что называется Невозможный объект.
Эти типы объектов не являются буквально невозможными, конечно, так как все они так или иначе созданы.
Эти вещи являются осязаемыми иллюзиями, которые можно держать и проверять вблизи. Кажется, они не поддаются логике и кажутся «невозможными». Они отлично подходят для подарков, интересны для обсуждения и представляют собой интересную задачу.
Предмет, который я здесь сделал, представляет собой цельнометаллическое кольцо толщиной 1/4 дюйма через два отверстия в горловине бутылки для кокса. На бутылке или кольце нет видимых швов.
Шаг 1: Видео
Это было вдохновлено большим проектом Джека Хоувелинга на YouTube, где он помещает деревянное кольцо в бутылку с колой: Невозможное кольцо через стеклянную бутылку.
Я задавался вопросом, как трудно было бы создать в основном то же самое, но с металлическим кольцом вместо дерева.
Я сделал видео процесса создания. Проверьте это, если вы заинтересованы:
Шаг 2: Что вам нужно
Шаг 3: Обезжиривание кольца
Первое, что я сделал, положил оцинкованное кольцо в уксус до полного растворения покрытия.
Это важно, потому что, хотя вы можете технически сваривать покрытие, оно выделяет токсичный газ, который чрезвычайно опасен.
Таким образом, это самый простой способ сделать такие детали оборудования, как этот, безопасными для сварки.
Я купил это кольцо в местном хозяйственном магазине. У них также были никелированные кольца, которые имеют более блестящий и почти желтоватый оттенок, но это покрытие не может быть растворено в уксусе. Общее эмпирическое правило – никогда не сваривать сквозные покрытия. Так что, что вы не можете безопасно растворить, вы должны размолоть до голого металла.
Шаг 4: Просверлите отверстия в бутылке
Крышка от бутылки была очень осторожно поднята из нескольких точек, чтобы снять ее, не деформируя. Таким образом, мы можем добавить это позже. Затем я выпил колу.
Я установил доску на своем сверлильном станке, к которой я зажал бутылку кока-колы.
Доска была прикреплена к моему столу для сверлильного станка, и бутылка с распылителем использовалась, чтобы держать зону бурения влажной.
Сверло было настроено на более низкую скорость, и в верхней части горлышка бутылки было сделано два отверстия с использованием стеклянного
сверла 5/16 дюйма. Вам нужно идти довольно медленно и позволить буровому долоту удалять лишь немного за раз,
Шаг 5: Вырезать кольцо
Металлическое кольцо разрезали пополам с помощью переносной ленточной пилы.
Шаг 6: Отверстия в горлышке бутылки
Я использовал алмазную шлифовку в своем вращающемся инструменте, чтобы отшлифовать внутренние края отверстий в бутылке, чтобы кольцо могло свободно проходить и вращаться вверх и вниз, не застревая.
Это было сделано с частыми туманами воды от пульверизатора.
Шаг 7: Приварить кольцо
Половинки колец были прикреплены к моему металлическому сварочному столу, одна половина проходила через отверстия в бутылках.
Затем кольцо было приварено несколькими небольшими точечными сварками вокруг обоих соединений.
Шаг 8: Подготовить кольцо
Используя твердосплавную шлифовальную насадку в своем вращающемся инструменте, я тщательно шлифовал сварные швы, чтобы придать форму кольца.
Затем я заточил все вокруг кольца и намеренно сделал его немного грубым, чтобы придать всему виду довольно изношенный вид.
Шаг 9: Отполировать кольцо
Некоторая автомобильная полировка металла использовалась с парой тряпок, чтобы быстро полировать и полировать металлическое кольцо вручную.
Шаг 10: Вымыть бутылку
Стеклянная бутылка — отличная основа для многих творческих проектов. Она смотрится интересно и стильно. Но, в отличие от пластика, разрезать ее без профессиональных инструментов, кажется, совсем непросто… Только не для тех, кто знаком с этим невероятным способом!
Вам понадобится:
- Бутылка из стекла
- Паяльник
- Маркер
Шаг 1: Подготовьтесь к резке
При помощи перманентного маркера наметьте контур будущего отверстия. Если ваш проект допускает свободную форму прорези, постарайтесь разместить ее так, чтобы хотя бы одна сторона приходилась на сгиб стекла. Так разрезать будет намного проще, чем по прямой поверхности. Закрепите бутылку неподвижно. Удобнее всего это сделать так, как показано на фото.
Шаг 2: Начинаем разрезать
Для того, чтобы аккуратно расколоть стекло, приложите паяльник к началу линии по сгибу бутылки и подержите несколько секунд. Затем переместите паяльник на несколько миллиметров. В этот момент стекло должно треснуть. Если трещины не образовалось, вернитесь паяльником обратно. Медленно продвигайтесь по линии, трещина на стекле должна образовываться по мере движения паяльника. Если в какой-то момент стекло перестает разрезаться, нагрейте противоположный край трещины.
Шаг 3: Поворот трещины
Дойдя до угла, аккуратно переверните паяльник, чтобы он следовал по намеченной линии. Лучше всего получится образовать ровный угол именно в месте перегиба стекла. В некоторых случаях стекло может треснуть неровно, поэтому нужно быть готовым к тому, что отверстие придется сделать несколько шире. Или просто иметь в запасе еще одну бутылку. Безусловно, такой способ резки не подойдет для образования очень мелких отверстий.
Шаг 4: Вопрос с углами
В некоторых случаях, при разрезе перпендикулярных отрезков, угол образуется самостоятельно. Просто потренируйтесь на разных бутылках, и со временем обретете нужную сноровку.
Шаг 5: Завершаем резку
В какой-то момент, трещина может остановится и не двигаться по привычной схеме. В некоторых случаях по нижнему краю отверстия может образоваться две разные трещины, которые не сходятся в одну. Помогайте паяльником, и при необходимости, надавите на стекло с внутренней стороны бутылки, поместив в нее ручку ножа или отвертки.
Шаг 6: Достаем лишнее
Аккуратно вынимаем отрезанную часть бутылки. Если боитесь порезаться о край стекла, используйте перчатки. Если все пошло по плану, получится вырезать именно ту деталь, которую нарисовали изначально.
Шаг 7: Другие отверстия, которые можно сделать этим же методом
Если вам нужно сделать отверстие в стеклянной бутылке, то вам нет необходимости покупать специальное оборудование. Это можно сделать в домашних условиях своими руками . Сверлить можно как обычной дрелью, так и шуруповерт.
Предпочтительнее использовать шуруповерт, так как у него меньше оборотов (для сверления стекла больших оборотов не нужно). Рекомендуется использовать сверло с победитовыми вставками, но если его нет, то можно взять обычное сверло для работ по металлу, например, в данной инструкции используется сверло диаметром 8.2 мм из стали П6М5. Не верьте тем, кто говорит, что нужно использовать только победитовые сверла и обычными ничего не получится. Сейчас мы в этом убедимся.
Как сделать отверстие в стеклянной бутылке, можно узнать, просмотрев видео:
Итак, чтобы просверлить отверстие в бутылке вам понадобится:
— Сама бутылка, например, из-под вина;
— Подставка для бутылки, чтобы бутылка не каталась при сверлении отверстия;
— Бумажный скотч;
— Обычная дрель или шуруповерт;
— Обычное сверло;
— Вода для охлаждения;
— Сверла
— И шприц.
Необходимо зафиксировать бутылку от вращения. Для этого заранее была изготовлена подставка из обычных деревянных брусков: двух длинных и двух коротких, скрепив их между собой гвоздями. Если нет возможности сделать такую подставку, то можно сделать небольшое углубление в земле, если сверлить будете на улице, или поставить по бокам два кирпича или что-нибудь другое. В общем это уже зависит от вашего воображения.
Первое, что нужно сделать — это намотать бумажный скотч (несколько слоёв) вокруг бутылки примерно там, где планируется сделать отверстие. После этого ставим метку на скотче фломастером — центр будущего отверстия.
Самое главное при сверлении отверстия сильно не надавливать на дрель, так как стекло может потрескаться и бутылка будет испорчена.
Приступаем к работе
Сверлим поэтапно, в перерывах добавляя в отверстие несколько капель воды из шприца. Это нужно для того, чтобы не перегревалось и сверло, и стеклянная бутылка.
Чтобы не было трещинок с внутренней стороны бутылки, необходимо следить за нажимом и не передавливать дрель, особенно в конце работы.
Когда сверло прошло насквозь, нужно аккуратно рассверлить отверстие, совершая лёгкие вращательные движения. Это сделает срез отверстие более гладким.
Очень оригинальные светильники получаются из фигурных и цветных стеклянных бутылок от напитков. Предпринятые в свое время несколько попыток просверлить бутылки заканчивались неудачами. Способы сверления стекла попадались какие-то экзотические и заканчивались обычно длинной трещиной в стекле от места сверления. А вот если использовать специальное сверло по стеклу все получилось. Для сверления красивой прямоугольной бутылки от неплохого напитка приобретено сверло с твердосплавной вставкой (
Особенности сверления стеклянной бутылки
1. Закрепленное в электродрели сверло строго перпендикулярно направляем к точке сверления бутылки и с небольшим нажимом ждем появления первых крошек стекла.
Сверло для стекла
2. Сверлить на максимальных оборотах не надо, сверло боится перегрева.
3. Каждые 20-25 секунд сверление прекращать и удалять стеклянную крошку. Заодно и наконечник сверла охладится.
4. При проходе кончиком сверла толщины стекла звук сверления несколько изменится и следует снизить подачу сверла (нажим) до минимума.
5. После сквозного прохода сверлом толщины стекла, промываем бутылку в проточной воде.
6. При сверлении лучше соблюдать меры техники безопасности — работать в перчатках,очках и средствах защиты органов дыхания.
Таким способом своими руками было успешно просверлено несколько стеклянных бутылок из которых были сделаны оригинальные ночники с питанием от сети 220 вольт.
- Дизайн интерьера, декор (63)
- Часы, панно и другие мелочи для дома (52)
- Декупаж (39)
- Делаем сами (37)
- Мастер-классы по декору разные. (37)
- Шитье, печворк, аксессуары (31)
- Стекло, витраж, роспись (29)
- Полезные советы для дома (29)
- Книги и журналы по декору (27)
- Бумага, квиллинг.
(19)
- Свет, лампы, светильники. (19)
- Лепка, пластика, фимо (17)
- Полезные ссылки (17)
- Новая жизнь старых вещей (15)
- Материалы для творчества (15)
- Уроки рисования и росписи (10)
- Домашним любимцам пушистым и хвостатым. (8)
- Зеленый уголок в доме. Цветы и растения. (8)
- Мыло своими руками (5)
- Свечи (5)
- Батик, роспись по ткани (4)
Меня часто спрашивают КАК сделать дырочку в бутылке для создания основания лампы.
Вот короткий мастер класс, как это делаю я.
* Патрон для лампы E14
* электрический шнур с выключателем
* Матовая ЭНЕРГОСЕБЕГАЮЩАЯ лампочка с цоколем Е14, мощностью 7-8W
* Перка для металла
* Cверло для стекла и керамики
* Баночка с водой
Меня часто спрашивают, как сделать дырочку для шнура в бутылке.
Для этого надо приобрести в хозяйственном магазине специальное сверло по стеклу и керамике. Для Отверстия, я использую сверло перо №6 или №8.
Так же Вам понадобиться дрель или шуруповерт.
Вот несколько фоток с теми материалами, которые Вам понадобятся.
Берем бутылку и обматываем место, где будет расположена дырочка малярным скотчем 2-3 раза.
Вот что должно получиться:
Сначала делаете отверстие, потом декорируете бутылку, потом собираете все вместе.
Теперь несколько слов про патроны для лампочек.
Патроны бывают двух видов «без юбочки» и с «юбочкой». Нам нужны патроны с юбочкой и крепежным кольцом.
Теперь берем крышку от бутылки (меня не было свободной, так что в качестве примера взята обычная крышка).
Выводим шнур сквозь горлышко бутылки.
Соединяем шнур и патрон.
Продеваем патрон сквозь дырку в крышке. Нижняя «юбочка» патрона не даст крышке спадать. Для надежности по кругу юбочки капаем из клея пистолета и крепим крышку к юбочке.
Закрываем бутылку крышкой. Все наш патрон надежно закреплен.
Верхним прижимным кольцом, Вы впоследствии прикрепить абажур к патрону.
Ваша фантазия по декорированию, бутылки и абажров остается в ваших руках! Творите и у Вас все обязательно получится!
Поделись статьей:
Похожие статьи
Самоделкин: сентября 2013
Своими руками туалетное мыло можно красить двумя различными способами:а) В горячую мыльную массу вливают водные растворы основных и кислых красящих веществ, при постоянном помешивании. Для этого способа окраски годятся также растворяющиеся в жиру красящие вещества, которые размешиваются с маслом. Все красящие вещества не должны быть подвержены действию квасцов.
б) Сухое мыло нарезают на маленькие кусочки (стружки) и обрабатывают на месильной машине вместе с растворенными в воде или растертыми с маслом основными и кислыми красящими веществами. Этот способ допускает применение нерастворимых смолистых цветных лаков. Таким образом выделываются мраморные мыла.
Красящие вещества, употребляемые для подкраски туалетного мыла, могут быть весьма различны. Главные условия, которым они должны удовлетворять: быть достаточно прочными, хорошо смешиваться с мылом и не оказывать вредного влияния на кожу. Такие краски могут быть разделены на две группы: растворимые и нерастворимые. Первые заслуживают предпочтения перед последними уже потому, что не оставляют после себя нерастворимый порошкообразный осадок; кроме того, растворимые краски распределяются в мыле легче и равномернее нерастворимых.
Красный цвет. Для прозрачного мыла — алканин, фуксин, эозин.
Для непрозрачного мыла — киноварь, сурик.
Желтый цвет. Для прозрачного мыла — экстракт куркумы и пикриновая кислота.
Для непрозрачного мыла — хромовая желтая краска.
Оранжевый цвет составляется из смеси красных и желтых красящих веществ.
Зеленый цвет. Для прозрачного мыла — зеленый анилин или же смесь индико-кармина и пикриновой кислоты.
Для непрозрачного мыла — хромовая зеленая краска.
Фиолетовый цвет составляется из метилфиолета или из смеси красной краски и индиго-кармина.
Коричневый цвет — из светлой или темной коричневой анилиновой краски или жженого сахара.
Нерастворимые краски применяются в виде тонкого порошка, которым посыпают стружки, поступающие в ящик строгальной машины. Затем на обсыпанные стружки накладывают новый слой стружек, которые вновь посыпают краской и т. д. Когда все мыло таким образом подготовлено, стружки размешивают и пропускают через месильную машину для получения однородно-окрашенной массы.
плитку, дерево, стекло, металл, трубы, бетон
Угловая шлифовальная машина, которую все называют болгаркой, может не только шлифовать, но и резать различные материалы с помощью специальных кругов. Но, чтобы умело пользоваться этими возможностями, необходимо иметь знания и опыт.
Содержание статьи:
Как правильно держать болгарку
У многих есть болгарка, но большинство людей не знают — как правильно ею пользоваться и как ее держать. Это приводит не только к браку в работе, но и к тяжелым травмам. Болгарка это довольно опасный электроинструмент.
Круг должен быть установлен рисунком вверх и зажат специальной гайкой.
Человек с ведущей правой рукой держит болгарку за рукоять правой рукой. При этом круг должен располагаться с левой стороны машины, а защитный кожух должен сверху закрывать его. Вращение идет так, что во время резки искры летят на рабочего. Если у болгарки заклинит круг и болгарка вырвется из рук, то она пойдет не на резчика, а в противоположную сторону.
Левая рука удерживает машину за рукоять, которая вворачивается в резьбовое отверстие на корпусе. Их там несколько для специальных случаев использования, но верное положение рукояти только верхнее.
Такое положение машины требует применять защитные средства. Для защиты глаз и открытой части лица – это защитные очки, а еще лучше – защитная маска. Чтобы защитить открытые части тела от искр и мелких осколков в процессе резки, необходимо надевать костюм из плотного материала.
Как ровно резать
Чтобы ровно отрезать что-то болгаркой, необходимо выполнить правильную разметку. Например, пред тем как отрезать кусок трубы необходимо нанести маркером или тонким мелом размер. Затем берем лист бумаги с ровным краем и на поставленной метке обворачиваем трубу. У нас получится бумажная труба поверх металлической. Граница бумаги и будет точной траекторией, по которой предстоит отпилить часть трубы.
Для этих целей можно использовать и строительный скотч, которым проще обмотать трубу и закрепить его. По краю бумаги или скотча прочерчиваем линию реза. Снимаем бумагу, заживаем трубу в тиски и режем болгаркой.
Подобным образом можно резать уголок, профиль или лист. Не надо только забывать, что во время резки нельзя менять положение машины. Перекос круга приведет к заклиниванию или поломке. Не следует чрезмерно нажимать на круг, особенно тонкий. Деформация немедленно отразится кривизной. Машина должна сама въедаться в материал, ее только надо придерживать.
Ровность реза зависит и от правильного подбора круга. Сложно добиться ровной траектории, отрезая часть толстостенной трубы тонким кругом.
Как вырезать болгаркой круг
Иногда бывает необходимым вырезать на листе металла круг, а кроме болгарки никакого инструмента нет. Для этого размечаем круг на выбранном участке белым маркером или тонким мелом. Линия реза должна быть на внешней стороне круга, чтобы не уменьшить его.
Болгарку устанавливаем не перпендикулярно листу, а под углом. Причем, болгарка будет склоняться к центру круга. На небольшой скорости делаем предварительный контурный рез. И контурный, и основной рез необходимо выполнять короткими движениями, перемещая положение круга вдоль контура.
Аналогично можно поступать, работая с другими материалами. Чтобы вырезать болгаркой круг в плитке под трубу, необходимо сделать разметку на обратной стороне плитки. Затем взять болгарку и сделать внутри размеченного круга прорези по хорде на расстоянии 4-5 мм один от другого.
Затем плитка разворачивается под прямым углом, и делаются прорези перпендикулярные прежним. Во время резки кусочки плитки будут выкрашиваться, но внутри очерченного круга. Оставшиеся зубчики можно зашлифовать болгаркой сначала с лицевой стороны.
Естественно получится срез косой, с расширением к тыльной стороне. Но этот край можно понемногу захватывать плоскогубцами и выкрашивать. В завершение операции зашлифовывается тыльная сторона отверстия. Здесь потребуется аккуратность, внимание и терпение.
Как резать болгаркой без сколов плитку и керамогранит
Чтобы обойтись без сколов во время резки плитки ее необходимо смачивать в воде. Это будет своевременно снижать температуру, которая является причиной разрушения. Таким путем можно не только разрезать плитку, но и вырезать необходимые фрагменты. Другой способ заключается в применении отрезного круга по камню. Такой круг не дает трещин и сколов.
Немного сложнее обстоит дело с керамогранитом. Керамогранит несколько толще обычной плитки и прочнее ее. Ручной плиткорез очень быстро тупится, не достигнув результата. Поэтому распилить керамогранит можно кругом по камню.
По вычерченной лини реза делаем контурный надрез. Затем другой, третий. До тех пор, пока не прорезанная толщина материала будет меньше прорезанной. Сдвигаем плитку керамогранита на край стола и резким, но не очень сильным движением надламываем.
Как пилить без пыли
Любая пыль вредна для здоровья человека. Во время ремонта или строительства она оседает везде. Убирать ее потом и долго, и довольно трудно. Но главное – ее невозможно убрать из организма. Для того чтобы работать без пыли необходимо сделать небольшое и недорогое приспособление для болгарки.
Это приспособление очень похоже на медицинскую капельницу. В обычную пластиковую бутылку объемом 1,5 – 2,0 литра заводим трубочку от капельницы. На ней оставляем только регулятор. В защитном кожухе болгарки делаем отверстие по диаметру этой трубочки. В это отверстие вставляем другую такую же трубочку.
Соединяем эти две трубочки, наливаем в бутылку воду и открываем ее подачу на круг. После первого примерного реза регулируем подачу воды, которая должна гасить всю выделяющуюся при резке пыль.
С таким приспособлением можно обрабатывать бетон, кирпич и много других материалов, которые при разрушении выделяют большое количество пыли.
Как правильно пилить или резать болгаркой
Различные материалы ведут себя по-разному во время обработки болгаркой. Одни сразу перегреваются и ломаются, другие деформируются, третьи вообще не хотят поддаваться обработке. Все тонкости работы с болгаркой трудно знать, но практика требует знать хоть что-то.
Режем плитку тротуарную, кафельную, керамогранит
Для резки тротуарной плитки болгаркой потребуется специальный круг с алмазной насечкой. На плитке делается разметка, и по этой разметке делается надрез почти до половины радиуса круга. Если болгарка с большим кругом, то за один проход можно перерезать плитку сразу на всю глубину. Главное чтобы она была не больше радиуса круга. Если радиус круга недостаточен, то плитка переворачивается и делается встречный рез.
Кафельная плитка без сколов лучше обрабатывается отрезным кругом для камня. На плитку наносится линия, по которой делается контурный рез. Затем глубина постепенно увеличивается. Когда прорезанная часть станет больше, плитку кладут на край стола и переламывают по линии. Неровности и шероховатости можно потом подработать.
Керамогранит хорошо обрабатывается кругом для камня. Технология резки ничем не отличается от технологии резки кафельной плитки.
Режем болгаркой древесину
По сравнению с другими строительными материалами дерево всегда было и остается самым податливым в обработке. Для болгарки налажен выпуск самых разнообразных дисков для резки древесины.
Самый обычный диск, к виду которого мы давно привыкли на циркулярной пиле. Главная особенность подбора такого диска заключается в том, что должны совпадать расчетные скорости болгарки и диска. Только в таком случае обрезать получается ровно и без горения древесины.
Такой диск легко режет древесину в любом направлении, но традиционно предпочитает резать поперек. Легко режется не только сырая древесина, но и сучки деревьев. Удобно распускать доски на брусья или планки. Для большого объема такой работы болгарку необходимо закрепить стационарно. Получится полная аналогия циркулярной пилы.
Очень просто обрабатываются и прессованные древесные материалы любой плотности. А, если необходимо разрезать деревянную панель с набитыми гвоздями, то и для такой работы выпускается диск. Он не боится встречи с гвоздями. Этот универсальный диск изготавливается из карбида вольфрама фирмой Bosh. Маркируется диск Bosh Carbide Wheel. Выпускаются размерами 76, 115 и 125 мм.
Болгарка по кирпичу, бетону, бетонному кольцу
Резка кирпича и бетона выполняется с помощью специальных кругов для камня. Кирпич режется легко, главное правильно его закреплять перед резкой и не применять свою ногу в качестве струбцины.
Практически без проблем режется бетонная плита или бетон. Но вот бетонное кольцо некоторые проблемы создает. Не сам бетон, а вложенная в него стальная арматура. Круг в болгарке испытывает большую нагрузку во время бетона, а арматура наносит ему вред.
Чтобы укоротить кольцо на определенную величину, делают рез с наружной части кольца. Потом кувалдой разбивают срезанную часть, а выступающую арматуру режут кругом для металла.
Профнастил, металл и листовой металл
Болгарка изначально была предназначена для резки и шлифовки металла, поэтому резать любой металл – это ее стихия. Для листового металла разной толщины подбираем определенной толщины круг, выбираем скорость вращения и выполняем рез по вычерченным линиям. На подходе к крайней точке реза надо немного утопить болгарку, чтобы граница реза не имела скоса.
По такой технологии можно вырезать разные геометрические фигуры из листа металла. Чтобы вырезать квадрат или прямоугольник, надо вычертить на листе размеры. Устанавливаем круг болгарки за границу квадрата и делаем прорез металла. Когда все четыре стороны прорезаны, вырезаем уголки.
Не вызывает трудностей резка профнастила. Рез начинают с любого края или в середине, если это требуется. Единственное замечание – при резке тонкого металла с обратной стороны образуется рваный срез. Чтобы избежать травмирования и для чистоты выполнения работы, этот срез лучше прошлифовать.
Резка болгаркой труб и газовых баллоновТруба большого диаметра, как и газовый баллон не являются каким-то исключением в работе болгарки. Трубу большого диаметра можно представить, как лист металла. Сложность представляет резка баллона, в котором остался след газа или конденсат. Это очень опасно возможным взрывом.
Чтобы обезопасить резку баллона, необходимо выкрутить вентиль. Это сделать сложно, потому что со временем резьба срастается намертво. В таком случае необходимо приварить баллон за подставку, которая находится в нижней его части, к массивной плите или раме.
На приваренном баллоне проще вывернуть вентиль. В освободившееся отверстие заливают воду до перелива, а затем приступают к резке болгаркой. Резка баллона не отличается от резки трубы большого диаметра.
Резка стекла
Для болгарки нет проблем при резке стекла. Для данной операции можно использовать самый дешевый круг по керамике. Делается легкий контурный рез, а затем он углубляется. Прорезанное стекло выкладывается на край стола и переламывается.
Резку болгаркой стеклянных труб можно рассмотреть на примере резки обычной стеклянной бутылки. Бутылку закладывают в раздвинутые тиски или вкладывают между двух деревянных брусков. Понемногу проворачивая ее, делают рез болгаркой. Бутылку вращают до тех пор, пока ненужная часть просто отпадет.
Как разрезать шифер без болгарки
Если отсутствует болгарка, то разрезать лист шифера можно с помощью обычной ножовки. Лучше для этих работ подойдет ножовка с мелкими зубьями и небольшим разводом. В крайнем случае, можно применить и ножовочное полотно от ножовки по металлу, и просто нож.
Главное правильно распределять силы и нагрузку на лист, чтобы избежать сколов и поломки шифера. Волновой шифер режется несколько сложнее, а лист плоского листового шифера резать просто любым инструментом.
Что можно сделать из подшипников своими руками
Что можно сделать из подшипника? » Изобретения и самоделки
Крутой станок из Подшипника своими руками!
Я покажу что можно сделать из подшипника и старых металлических обрезков , очередная самоделка превзошла все мои ожидания.
Кондуктор должен быть идеальной формы, как улиточка завитушка., ровный круг с выходом, как спирали от комаров, только меньше колец. А у вас кондуктор с углами и овальный поэтому завитки получились яйцевидной формы. Попробуйте сделать другой кондуктор, из подошвы под жд рельсы, куда гвозди в шпалу забивают. Только кондуктор сделайте в форме капли с изогнутым хвостиком, и вырезать проще, и плавные формы смотрятся лучше, даже если там будет один завитокИсточник
Как сделать сверло из подшипника для сверления каленой стали
Каленую и твердую сталь берет далеко не каждое сверло. В связи с этим при необходимости просверлить обойму подшипника, клинок ножа или другие закаленные изделия возникают трудности. Для их решения можно сделать самодельное сверло, справляющееся со сложными задачами.
Материалы:
- шарик из-под подшипника;
- саморез.
Изготовление сверла
Нужно подобрать шарик соответствующий диаметру требуемого отверстия. Его можно взять из нового или старого отработанного подшипника. Для быстрого извлечения подшипник лучше обмотать в ткань и разбить молотком. Тряпка не позволит шарикам разлететься по мастерской.
В качестве основания сверла будет применяться обычный черный саморез по дереву. Главное, чтобы его длины хватило для нужной глубины сверления. Шляпка самореза обтачивается, чтобы ее диаметр стал немного меньше, чем шарик.
В тисках зажимается небольшая гаечка, на которую выставляется шарик. Гайка используется как временная подставка, поэтому качество ее резьбы и состояние граней не имеет значения.
К шарику приставляется головка самореза и они свариваются вместе.
Выступающую за диаметр шарика сварку нужно сточить на наждаке. При этом саморез важно поворачивать, чтобы получить цилиндр без углов.
Затем шарик перетачивается под спиральное сверло. Если нужно сверлить плитку, то ему придается форма пера.
Получив нужную форму, сверло закаляется. Шарик после сварки и проточки теряет твердость, поэтому ее нужно восстановить. Для этого кончик сверла греется газовой горелкой до оранжевого цвета и погружается в масло на несколько секунд. При этом сам шуруп и сварку охлаждать не нужно, чтобы они не стали хрупкими.
После закалки наконечник сверла окончательно затачивается. Делать это на отпущенном металле до закалки не следует, поскольку тогда качество режущей кромки будет хуже.
Полученное сверло хорошо сверлит практически любой твердый металл, будь то обойма подшипника или напильник. Главное его не переохлаждать. Если нет под рукой масла, то нужно подливать в отверстие хотя бы воду.
При сверлении очень толстых стальных пластин, чтобы не мучатся с постоянным охлаждением, можно положить резиновое кольцо вокруг накерненной точки и подлить в него воды. Жидкость будет удерживаться за счет поверхностного натяжения и постоянно охлаждать сверло.
Смотрите видео
sdelaysam-svoimirukami.ru
Как самому сделать нож из подшипника, который будет не хуже магазинного
Сегодня, я расскажу вам на что способен нож из подшипника и как его сделать-это безумная мысль, которая не давала мне уснуть эту ночь, так как все делают ножи из напильников, потому что они очень прочные.
И сегодня я расскажу вам, кое-что новое и не заезженное, а именно нож из Подшипника.
И так приступим, для начала нам нужен сам подшипник.
А именно та деталь, которую вы видите слева от себя.
После чего мы идем к тискам зажимаем и пилим.
Потом немного ее разгибаем и ложим в печь.
После чего мы выпрямляем деталь с помощью молотка, после того как деталь выпрямлена, мы идем к станку делаем разметку с помощью заранее подготовленного трафарета и начинаем вырезать.
После того как мы все вырезали с помощью болгарки ее нужно отполировать и выполнить термическую обработку в печи +-700-900 градусов.
После чего мы должны поймать температуру в 200 градусов и опустить нож в воду, после чего закинуть в масло.
Потом мы должны зажать заготовку в тисках и обработать нож напильником.
И после этих всех манипуляций проводим отпуск, если его не сделать, то нож будет очень хрупким и разобьется как стекло, если уронишь.
Отпуск нужно проводить в 150 градусах в печи. Ложимся спать и на утро достаем. По сути сам клинок уже готов.
Делаем, какую хотите рукоять. Можно не париться сходить в магазин купить термопластик (он быстро плавится и принимает любое положение). Но мы сделаем из дерева.
Насаживаем клинок на дерево, после чего обрабатываем и придаем форму рукояти.
Ну в принципе все, нож готов. Кому интересно сталь, которая используется в изготовлении подшипников ШХ15-ну что я могу про нее сказать, она долго держит заточку и достаточно прочная.
Если все правильно сделать можно и ветки рубить и разделывать тушки, что хотите в общем. Главное ни где не накосячить.
Такой нож не хуже, того что вы купите в магазине, а наоборот лучше, так как близок к сердцу. HRC будет ниже 60, примерно 56-57.
Источник
Универсальный круглогиб из подшипников своими руками
Давно хотели реализовать приспособление для прокатки металлического профиля, арматуры, полосы и прута в круг. И вот делая внеплановую уборку гаража отрыли подшипники, уголок 40 мм и полумуфты.
Конструкцию решили делать простую, приспособленную под обычные тиски. Первым делом сделали раздвижную станину из уголка на металлических втулках-направляющих. К ней приварили задний ступичный подшипник от Лады-Калины. Это будет основой для ручки прокатного станка.
Чтобы механизм справлялся с широкими пластиками его удлинили в два раза, расхомутав немного трубы от старого домкрата. Далее запрессовав полумуфты в подшипники, наметили места сварки. Приварили и установили подшипники на свои места. Вот и весь станок!
Ручку в итоге все-таки удлинили. На стальном пруте убедились что вся эта штуковина надежна и реально работает. Много полезного можно теперь намудрить… НО! Есть что добавить… Покрасить можно всегда в любой цвет! Но, если серьезно, думаю сделать паз болгаркой по радиусу ступичного подшипника, где-то по середине. Напротив наших сдвоенных. Это для лучшей фиксации прута, арматуры и профильного прута. Как раз прут будет ложиться в насечки с двух сторон и лучше фиксироваться при прокатке. Так же сделаю ребра жесткости на уголке, дабы все было по-мощнее. Все размеры на фото. Все как делали подробно в видео. Может у кого возникнут мысли по доп улучшению данного изделия.
Запись пользователя KAS6russiangarag из сообщества Сделай Сам на DRIVE2
Источник
Сообщества › Сделай Сам › Блог › Универсальный круглогиб из подшипников своими руками.
Полный размер
Давно хотели реализовать приспособление для прокатки металлического профиля, арматуры, полосы и прута в круг. И вот делая внеплановую уборку гаража отрыли подшипники, уголок 40 мм и полумуфты.
Конструкцию решили делать простую, приспособленную под обычные тиски.
Первым делом сделали раздвижную станину из уголка на металлических втулках-направляющих. К ней приварили задний ступичный подшипник от Лады-Калины. Это будет основой для ручки прокатного станка.
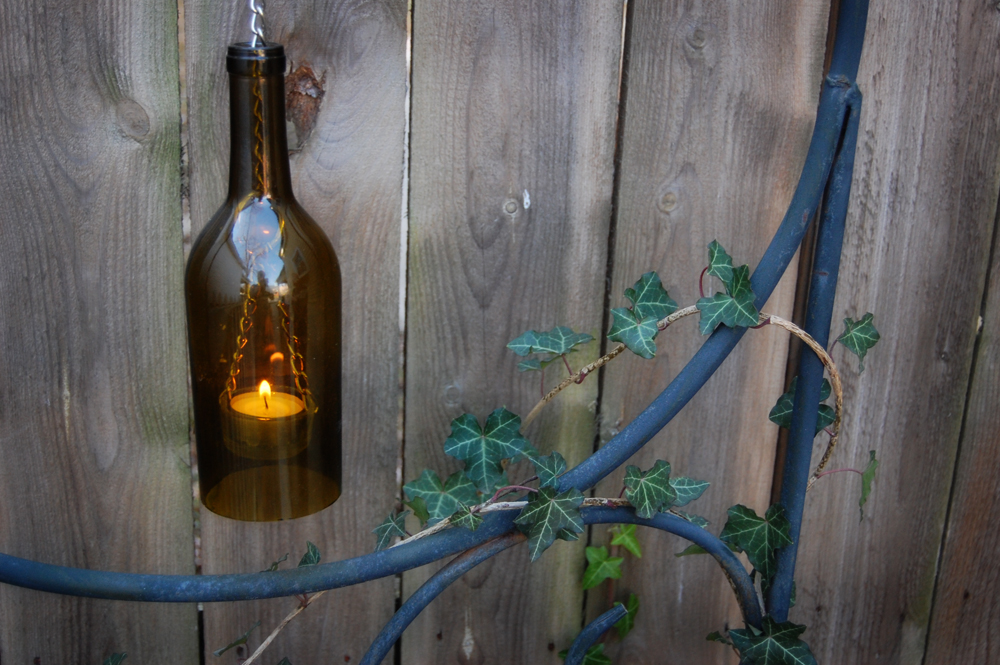
Что бы механизм справлялся с широкими пластиками его удлинили в два раза, расхомутав немного трубы от старого домкрата.
Далее запресовав полумуфты в подшипники, наметили места сварки. Приварили и установили подшипники на свои места. Вот и весь станок!
Ручку в итоге все-таки удлинили. Протестив круглогиб на стальном пруте, убедились что вся эта штуковина надежна и реально работает.
Много полезного можно теперь намудрить…
НО! Есть что добавить… Покрасить можно всегда в любой цвет…)))! Но, если серьезно, думаю сделать паз болгаркой по радиусу ступичного подшипника, где-то по середине. Напротив наших сдвоенных. Это для лучшей фиксации прута, арматуры и профильного прута. Как раз прут будет ложиться в насечки с двух сторон и лучше фиксироваться при прокатке.
Так же сделаю ребра жесткости на уголке, дабы все было по-мощнее. Все размеры на фото. ВСЕМ СПАСИБО! Все как делали подробно в видео может у кого возникнут мысли по доп улучшению данного изделия.
Полный размер
Полный размер
Полный размер
Полный размер
Полный размер
Полный размер
Полный размер
Полный размер
Полный размер
Полный размер
Полный размер
18 ноября 2019 в 16:32 Метки: кольцегиб, круглогиб, станок своими руками, станок из подшипника, холодная ковка
Что можно сделать из старых подшипников
SAMODELKI. ONLINE
Что можно сделать из старых подшипников
Это нужно иметь в каждом доме/Everyone should have this at home
(2018-02-11 19:49:44)
Смотреть
5 полезных идей и советов / 5 useful life hacks
(2018-02-11 07:00:00)
Смотреть
Железо — Металл, ЗАЩИЩАЮЩИЙ ЗЕМЛЮ
(2018-02-10 14:31:11)
Смотреть
ПЕРЕЗАЛИВ Как сделать РУКИ ИЗ БАЛЛИСТИЧЕСКОГО ГЕЛЯ Изготовление формы и разные составы геля
(2018-02-09 19:49:24)
Смотреть
Самое полезное приспособление для сварки
(2018-02-09 10:43:12)
Смотреть
15 способов УБРАТЬ РЖАВЧИНУ в домашних условиях
(2018-02-07 15:03:37)
Смотреть
5 простых идей и советов которые вам пригодятся / 5 useful life hacks
(2018-02-07 07:00:00)
Смотреть
Супер мощный Power Bank — своими руками
(2018-02-06 19:04:39)
Смотреть
Самодельная Wi-Fi пушка Мощная антенна для ВайФай сигнала своими руками
(2018-02-05 16:58:53)
Смотреть
Самодельная ик паяльная станция из автомобильного прикуривателя
(2018-02-04 12:36:07)
Смотреть
Минералы за МИЛЛИОНЫ ЕВРО Зачем они нужны?
(2018-02-03 14:32:32)
Смотреть
Что можно сделать из старых подшипников
(2018-02-02 17:12:46)
Смотреть
5 простых идей и советов которые вам пригодятся / 5 useful life hacks
(2018-02-02 07:00:01)
Смотреть
Система защиты для LI-ION своими руками.
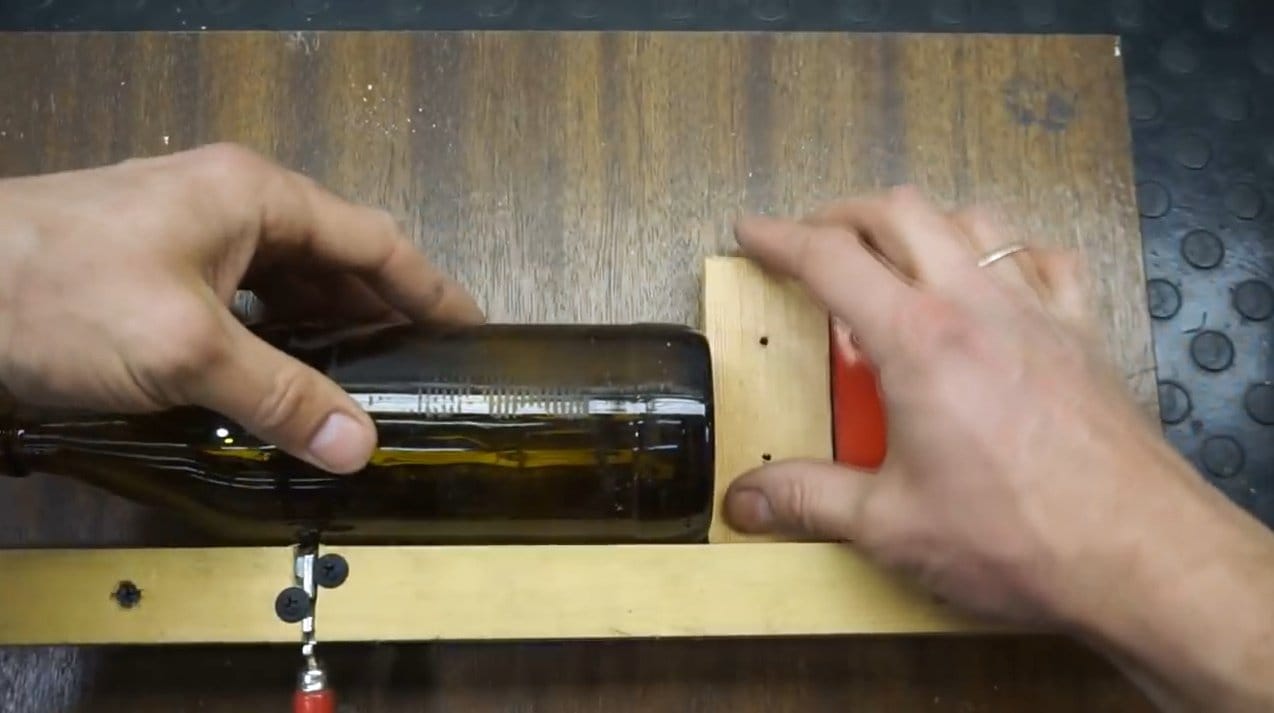
(2018-02-01 18:05:56)
Смотреть
Плата защиты LI-ION — КАК ЭТО РАБОТАЕТ?
(2018-01-27 20:15:36)
Смотреть
Керамика за 120 Евро? Для чего она нужна?
(2018-01-27 15:58:55)
Смотреть
Нереально крутые самоделки. Сделай и себе эти простые приспособления.
(2018-01-27 09:00:01)
Смотреть
Сделай и себе этот простой и нужный инструмент
(2018-01-26 17:48:07)
Смотреть
СОЛНЕЧНЫЙ РЕЗАК НЕРЕАЛЬНАЯ МОЩЬ ДЛЯ САМОДЕЛЬНОГО КОНЦЕНТРАТОРА Гиперболоид Игорь Белецкий
(2018-01-26 15:25:49)
Смотреть
Как разрезать стеклянную бутылку/банку ВДОЛЬ
(2018-01-26 14:05:33)
Смотреть
Prev12…414243…8081Next
Copyright 2018
Приспособление из большого подшипника
Часто в мастерских лежат без дела старые инструменты и материалы, из которых могут получиться замечательные вещи. Эта публикация как раз об идее использования такого подручного материала для пользы делу.
С помощью большого подшипника можно сделать полезный станок, который нужен любому мастеру.
Для самоделки нужен подшипник значительного размера, весовая шайба, уголок и прутки. В качестве основного инструмента будет использован сварочный аппарат.
Весовая шайба не является базовым элементом, ее можно заменить и другой подходящей деталью. Основная механическая нагрузка в подвижной системе принадлежит нашему подшипнику. В этом самая соль этой полезной модели.
Сначала нужно просверлить два отверстия в детали, которую изготовим из шайбы.
После этого возьмем подшипник и приделаем к нему сваркой два рожка из прутков.
С их помощью будет крепиться элемент из уголка.
К уголку присоединим в указанном порядке шпильки.
Пропустим действия, которые можно посмотреть на видео ниже.
В результате сделали гибочный станок для сложных фигур из полос, прутков, арматуры и др.
Ход работы над изготовлением станка и его испытания в ролике канала TeraFox
Гибочный станок из подшипника своими руками
При армировании фундаментов или кладки стен требуется заложить арматуру, которую перед этим нужно согнуть. Сделать это быстро и ровно получится только на гибочном станке. Это простое и компактное устройство, которое можно сделать своими руками. Также оно будет полезно для сгибания не толстых прутков для различных поделок.Материалы:
- большой подшипник можно заклинивший;
- длинный болт М12 или толще;
- 3 гайки М12;
- удлиненная гайка М12;
- стальная полоса как минимум 60х10 мм или пластина.
Изготовление гибочного станка
В качестве толкателя и гибочной опоры станка будут использоваться кольца крупного подшипника с наружным диаметром от 100 мм. Его внешняя обойма разрезается пополам.
Одна из ее половин приваривается на стальную полосу, как на фото.

Часть внутреннего кольца вырезается по ширине гайки, которая затем в него уваривается.
Перед этим нужно убрать ее резьбу, прогнав через нее сверло. Нужно, чтобы болт проходил сквозь нее не накручиваясь.
Далее нужно обточить грани еще у 2-х гаек, придав им округлую форму.
На болт накручивается длинная гайка, затем короткая со снятыми гранями. Его конец продевается через расширенную гайку, вваренную во внутреннее кольцо подшипника. Затем на него наворачивается оставшаяся узкая обточенная гайка.
Чтобы гайки без граней не откручивались, их нужно обварить. Перед этим они поджимаются, чтобы кольцо не шаталось относительно болта.
На обратной стороне стальной полосы с полукольцом нужно приварить небольшой флажок. За него в дальнейшем будет удобно зажимать станок в тисках.
Затем полоса переворачивается и к ее противоположному от полукольца краю приваривается механизм с болтом. Сварка делается только на длинной гайке. Таким образом, при вращении болта толкающее кольцо будет двигаться в сторону упорного полукольца.

Как пользоваться
Станок зажимается в тисках за сделанный внизу флажок. Между кольцами закладывается арматура. Для движения толкателя на упор, необходимо вращать винт гаечным ключом. Арматура при этом не выскакивает, поскольку удерживается за счет проточки на кольце подшипника. По мере вкручивания болта прут сгибается на необходимый угол.
Несмотря на небольшие размеры станка, его способностей достаточно для легкого сгибания тонких прутков и арматуры диаметром до 6 мм. Более толстый прокат, при качественной сварке станка, также ему не повредит. Для удобства можно приварить к шляпке болта вороток, чтобы не пользоваться гаечным ключом.
Смотрите видео
Как быстро сделать корпус для подшипника
При работе над самодельным устройством в наличии может оказаться подшипник по диаметру меньше уже существующего гнезда или опоры.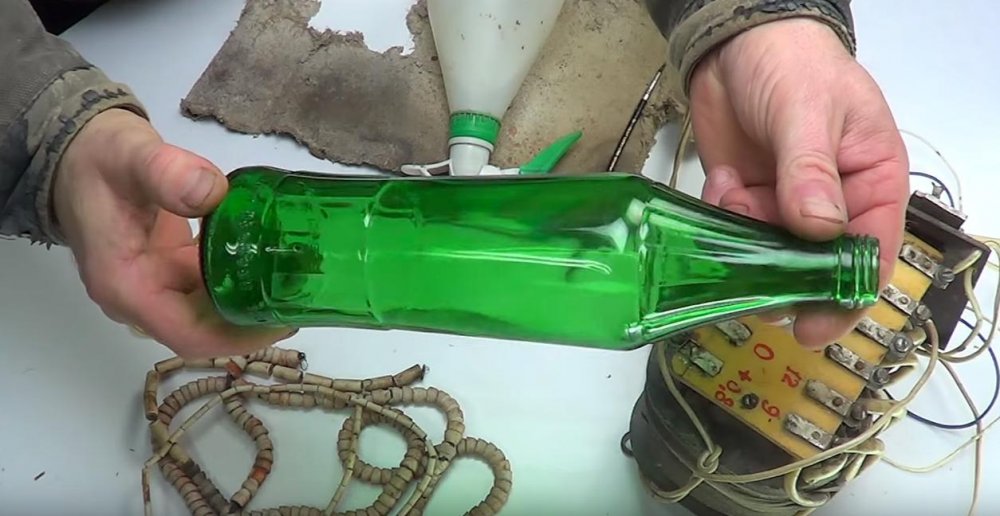
Для реализации предстоящей задумки нужно иметь некоторый опыт работы с металлом, совершенно простые, доступные и недорогие материалы, а также вполне стандартное оборудование и инструменты. Конечно, нельзя забывать и об индивидуальных средствах защиты: очках, перчатках и т. д.
Понадобится
Следует не забывать о том, что даже стандартный подшипник – прецизионное изделие. Поэтому так важны точность измерения и аккуратность разметочных операций, чтобы подшипник не оказался слишком зажат или имел бы зазор при монтаже в корпус. В первом случае он быстро выйдет из строя, во втором – не будет держаться на месте.
Для успешной работы мы должны иметь в наличии:
- отрезок трубы необходимого диаметра и толщины стенки;
- угольник и штангенциркуль;
- маркер;
- маятниковую пилу;
- сверлильный станок;
- болгарку;
- сварочное оборудование;
- цилиндрическую стальную оправку;
- тиски, наковальню и молоток.
Порядок изготовления корпуса подшипника из круглой трубы
Тщательно размечаем соответствующую под данный подшипник по диаметру и толщине стенки трубу на два кольца, равные по ширине имеющемуся подшипнику.
На маятниковой пиле по разметке нарезаем кольца.
На одном из них проводим две параллельные линии перпендикулярно торцам, на расстоянии, полученном из предварительного расчета.
На другом кольце наносим четыре точки по центру кольца равномерно по окружности.
Вырезаем участок кольца между двумя линиями разметки и зачищаем места реза болгаркой.
На сверлильном станке выполняем по меткам четыре сквозных отверстия на втором кольце.
Немного сжимаем кольцо с вырезом, слегка ударяя молотком по его концам. Запрессовываем с помощью молотка разрезное кольцо в целое с четырьмя отверстиями на боковой стороне.
Насаживаем на цилиндрическую оправку с входного конца наши запрессованные друг в друга кольца, ударяя по ним молотком по кругу, пока они не окажутся на формирующем участке оправки и разрезное кольцо равномерно без зазоров не примкнет к внутренней поверхности наружного кольца.
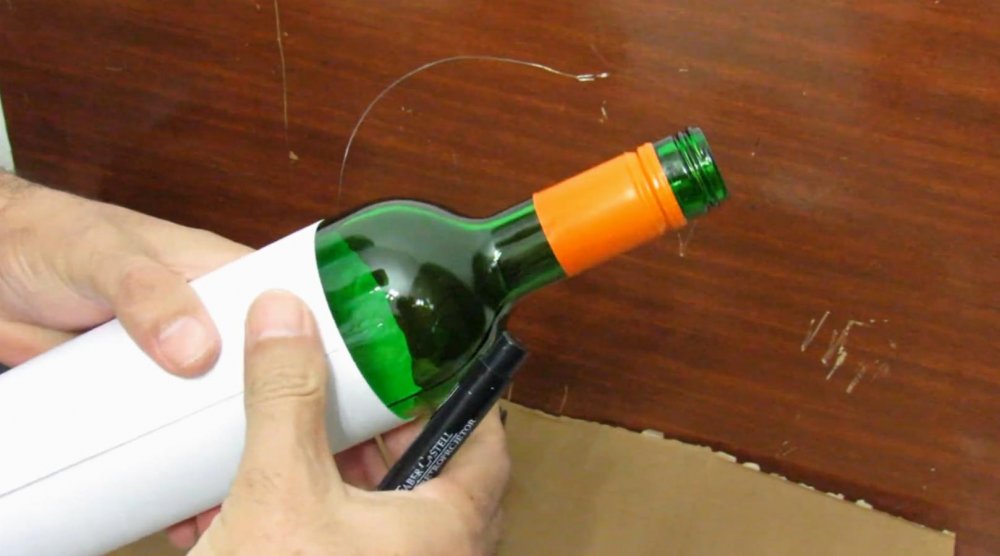
Используя ранее просверленные отверстия во внешнем кольце, привариваем его к внутреннему.
Легкими ударами молотка по торцу подшипника устанавливаем его в наш самодельный корпус.
Теперь остается лишь подшипник в корпусе закрепить в гнезде или опоре.
Теперь корпус можно приварить куда угодно и покрасить.
Смотрите видео
Нож из обоймы подшипника, вариант 1
Всем здравствуйте в куче металлического хлама нашел 4 куска от обоймы подшипника и решил сделать из них 4 небольших ножа. Сталь подшипника в основном из ШХ10, ШХ15, а подшипник диаметром от 200 мм из ШХ20. У меня подшипник из ШХ15.
Уже ни один нож делал из подшипников разного диаметра из разных сталей, так что думаю затруднений не будет. Главное правило ковки ножа из подшипника — это температура нагрева заготовки, ведь эта сталь не любит перегрева, и по этому я лучше не до грею чем, перегрею сталь.
Нагреваю до вишневого цвета и начинаю ковать при нанесении удара, если чувствую, что сталь становится упругой, то сразу же немного подогреваю заготовку и продолжаю ковать. Вот и все с теорией, приступаю к ковке ножа из обоймы подшипника.
После обжига заготовки начинаю выпрямлять на наковальне, после выравнивания нагреваю до вишнёвого цвета и начинаю ковать лезвие ножа, нанося скользкие удары, вытягивая от обуха, но лезвия ножа. Нагревать нужно аккуратно, чтобы не перегреть металл, иначе все испортим.
После вытяжки лезвие на обухе 2 мм, а на острие 1 мм я ковал лезвие сразу в готовый вид так, что после ковки буду сразу закаливать нож.
После ковки лезвия приступаю к формировке хвостовика, ручку ножа я решил сделать декоративную кованую ручку. Нагреваю и начинаю ковать хвостовик формой квадрата. После 3 или 4‐х нагревов вытягиваю хвостовик до нужной длины. Нагреваю еще раз, далее зажимаю в тисках, и держав за хвостовик, начинаю закручивать и за два раза закручиваю, как нужно мне. Нагреваю, а затем загибаю ручку под удобный хват, вот и все с ковкой.
Теперь можно и закаливать нож. Нагреваю до того момента пока магнит не перестанет прилипать к ножу, и окунаю в подогретое минеральное автомасло. После закалки оставляю на выключенном горне, пусть остывает будет как отпуск. Вот и все теперь приступаю к слесарке.
Ручку решил оставить как есть, чтобы видно было ковку. На Гриндере, на 120 бумаге, шлифую ручку до малозаметных рисок. Далее на станке формирую форму клинка по шаблону. Металл берется тяжело, но спасает что клинок нужно просто отшлифовать, ведь я сразу отковал нужную толщину. Спустя пол часа я наконец-то закончил шлифовать на станке. Зажимаю нож струбциной и шлифую вручную. К сожалению у меня нет мелкой бумаги, осталось только 60, 100 и 120, а еще 400ка так, что до блеска пока не получится отшлифовать. А травить в кислоте не охота. Вот и все нож готов.
Длина от кончика до конца рукояти 185 мм, длина клинка 103 мм. Нож получился небольшим, но удобным.
Некоторые сейчас будут тролить, типа страшный и из стали го.., а скажу так, что человек от обезьяны отличается тем, что он хотя бы что-то делать старается, а не лежит на диване и строчит некрасивый комментарий, типа я лучше могу, к счастью даже такие комментарии приносят 0.5 монет хоть немного польза.
Сталь ШХ15 — да не спорю не из лучших, но эту марку стали можно найти хоть где даже под диваном, но у нее есть и свои плюсы если не перегревать ее, то она менее поддается ржавчине, но нужно не забывать что любой нож требует ухода.
Вот и все моя статья подошла к концу. Любая вещь, сделанная своими руками, лучше чем фраза я могу лучше. Всем спасибо и до новых Самоделок друзья.
Доставка новых самоделок на почту
Получайте на почту подборку новых самоделок. Никакого спама, только полезные идеи!
*Заполняя форму вы соглашаетесь на обработку персональных данных
Становитесь автором сайта, публикуйте собственные статьи, описания самоделок с оплатой за текст.
Как сделать сверло из подшипника для сверления каленой стали
Каленую и твердую сталь берет далеко не каждое сверло. В связи с этим при необходимости просверлить обойму подшипника, клинок ножа или другие закаленные изделия возникают трудности. Для их решения можно сделать самодельное сверло, справляющееся со сложными задачами.
Материалы:
- шарик из-под подшипника;
- саморез.
Изготовление сверла
Нужно подобрать шарик соответствующий диаметру требуемого отверстия. Его можно взять из нового или старого отработанного подшипника. Для быстрого извлечения подшипник лучше обмотать в ткань и разбить молотком. Тряпка не позволит шарикам разлететься по мастерской.
В качестве основания сверла будет применяться обычный черный саморез по дереву. Главное, чтобы его длины хватило для нужной глубины сверления. Шляпка самореза обтачивается, чтобы ее диаметр стал немного меньше, чем шарик.
В тисках зажимается небольшая гаечка, на которую выставляется шарик.

К шарику приставляется головка самореза и они свариваются вместе.
Выступающую за диаметр шарика сварку нужно сточить на наждаке. При этом саморез важно поворачивать, чтобы получить цилиндр без углов.
Затем шарик перетачивается под спиральное сверло. Если нужно сверлить плитку, то ему придается форма пера.
Получив нужную форму, сверло закаляется. Шарик после сварки и проточки теряет твердость, поэтому ее нужно восстановить. Для этого кончик сверла греется газовой горелкой до оранжевого цвета и погружается в масло на несколько секунд. При этом сам шуруп и сварку охлаждать не нужно, чтобы они не стали хрупкими.
После закалки наконечник сверла окончательно затачивается. Делать это на отпущенном металле до закалки не следует, поскольку тогда качество режущей кромки будет хуже.
Полученное сверло хорошо сверлит практически любой твердый металл, будь то обойма подшипника или напильник.

При сверлении очень толстых стальных пластин, чтобы не мучатся с постоянным охлаждением, можно положить резиновое кольцо вокруг накерненной точки и подлить в него воды. Жидкость будет удерживаться за счет поверхностного натяжения и постоянно охлаждать сверло.
Смотрите видео
пошаговая инструкция по изготовлению своими руками
На чтение 11 мин. Просмотров 447 Опубликовано
Русские умельцы ножевого дела, никогда не ищут лёгких путей. Потому что это – для многих хобби и увлечение. Бывает, что из простого занятия, получается настоящий небольшой бизнес. Но в большинстве своём, для людей это всё же, это отдых и отвлечение от повседневной жизни. Каждый человек, определяет свой досуг сам. Любители ковать, довольно часто изготавливают свои изделия из необычных вещей, например: нож из подшипника. Очень интересный и непростой процесс.
Плюсы и минусы ножа из подшипника
Многие обыватели скажут, что зачем этим заниматься, когда можно пойти в магазин и прикупить себе парочку замечательных клинков. Но мы же, им не указываем, как проводить своё время. Так что если неинтересно, идём на другой ресурс, а здесь будет статья, содержащая в себе немало полезной информации особенно для новичков. Потому что изложение планируется в пошаговом ракурсе.
Мы уже писали о том, что «идеального ножа» на всё случаи жизни, не существует. И это правда, но стремиться к идеалу нужно всегда. Поэтому попробуем выделить положительные и отрицательные стороны клинка из подшипника. Чтобы знать, что получится в результате правильной обработки металла.
Сталь подшипника изначально предназначена для высоких нагрузок, по этой причине она отличается пластичностью и однородностью при нагреве. А в итоге получается изделие с жёсткостью от 61 до 64 единиц по шкале Роквелла. И главное – высочайшая износостойкость клинка. Единственным минусом можно назвать, хрупкость во время обработки. Очень важно, правильно выполнить закалку, а ковку «на холодную», вообще, исключить.
Как сделать нож из подшипника своими руками
Понятно, что в данном деле без ковки никак не обойтись. Нужно обязательно распрямить обойму изделия. Знатоки таких вещей, разделяются на два лагеря, какую часть лучше выбрать для работы: внутреннюю или внешнюю. Однозначного ответа нет, но многие утверждают, что внутреннее кольцо состоит из лучшей стали. Подкрепляя свои слова, тем, что эта часть несёт на себе большую нагрузку.
Но, как бы там ни было, новичку однозначно без разницы. Для начала нужно, чтобы хоть что-то получилось и не треснуло во время закалки. Для нормальной работы потребуется свой, определённый набор инструментов. Ну и главное – кузница.
Требующиеся материалы и инструменты
У совсем «зелёного» новичка вряд ли есть необходимый инструмент, поэтому им нужно обзавестись. Что-то можно изготовить самостоятельно, а другое только купить. Но опять же, покупной инструмент позволительно заменить аналогичным более простым, но увеличится время изготовления. Если нет в планах, заниматься кузнечным и ножевым делом, покупать что-либо, конечно, бессмысленно, если только мелочи. Материалы потребуются следующие:
- подшипник, желательно в разобранном состоянии;
- деревянный брусок, для изготовления рукояти;
- стержни для заклёпок, лучше из латуни;
- эпоксидный клей или похожий по свойствам заменитель;
- масло или воск для пропитки рукояти;
- малярный скотч, листок бумаги, карандаш, маркер.
С материалами не очень сложно и всё доступно. А вот что касаемо инструмента, обратите внимание, как уже говорилось выше, если не найдётся профессионального, пробуйте заменить на более доступные варианты. Их мы также укажем для ясности:
- металлические тиски, зажимы, струбцины;
- УШМ (болгарка) с набором различных дисков;
- горн или муфельную печь, которую можно изготовить самостоятельно;
- сверлильный станок или дрель с набором свёрл;
- бумага наждачная разной зернистости;
- полировальная машина, можно УШМ с полировочным кругом;
- духовой шкаф газовой плиты, для отпуска металла;
- наковальня и два молота разного веса, один – 6 кг, второй – 1,5-2 кг;
- ленточная шлифмашина или опять УШМ с абразивным кругом;
- электролобзик или просто ножовка с мелкими зубцами;
- сварочный аппарат;
- комплект для травления или гравёр (это по желанию).
Большинство этих предметов можно заменить аналогами. Что касается муфельной печи и горна, эти хитрые конструкции можно изготовить своими руками (читайте в статье «Закалка ножа в домашних условиях»).
Подготовка детали к ковке и обработка подшипника
Допустимы к изготовлению ножа из подшипника, любые экземпляры с рабочих машин и двигателей. Если он достался вам в собранном состоянии, самым лучшим способом получить из него заготовку, будет распил «болгаркой». Для этого зажимаем изделие в тиски и при помощи УШМ делаем разрез под углом.
Это делается для одной простой цели, в будущем будет проще ковать остриё и носик клинка. Затем при помощи слесарных инструментов, требуется разогнуть, насколько получится верхнюю обойму. Внимание! Ни в коем случае не стучать молотком, иначе загубите деталь, не начав с ней работать. Вынуть все ненужные части и можно приступать к следующему этапу.
Для полноценной работы, тем более для новичков, обязательно надо сделать эскиз на бумаге будущего клинка. Учесть толщину заготовки и её длину, вернее, то что в результате должно получиться. Чертёж должен содержать в себе всю информацию по размерам, в том числе и рукояти. Для клинков из такого материала лучше использовать накладной метод монтажа рукояти из двух половинок дерева, закреплённых с помощью заклёпок. Чертёж упростит задачу во много раз.
Отжиг и ковка обоймы подшипника
В верхней обойме подшипника чаще всего используется сталь ШХ15, но для точных характеристик, можно воспользоваться справочниками. Маркировка металла иногда присутствует на самих изделиях. Соответственно каждая марка стали ведёт себя по-разному во время ковки и закалки. В наш эксперимент попал экземпляр именно тот, что указан выше.
Такую сталь, нужно подвергать обязательному отжигу, процесс происходит таким образом. В соответствии со справочником, буквы «ШХ», обозначают – подшипниковую сталь с легированием хромом. Отжиг её производится при температуре 800 °С, со снижением её со скоростью 10-20 град/час. Вся эта информация свободно доступна в интернете, пользуйтесь обязательно.
Многим людям, плохо знакомым с ковкой, будет сложно работать с кузнечными клещами. Для упрощения этой задачи к заготовке приваривается пруток. Деталь укладывается в печь и разогревается до 900-1100 °С, выглядеть она будет темно-жёлтой. Но лучше пользоваться лазерным термометром. Если его нет, пробуем сталь магнитом, заготовка не магнитится – значит, разогрев достиг определённой точки Кюри.
При достижении этого значения можно постепенно начинать ковку. Для начала маленьким молотом аккуратно выпрямляем деталь. Всегда контролируйте температуру, лучше подстраховаться и нагреть её, чем на холодную просто разрушить. Следующим приступает к работе большой молот. Проковку нужно выполнять по всем правилам:
- несильными ударами молота, с середины детали «сгоняем» метал в сторону, формируя, таким образом, спуски;
- работа над остриём, немного отличается от общего принципа, носик клинка аккуратно подгоняем к острию;
- обязательна оттяжка заготовки по длине для хвостовика;
- выполнив всё верно, обух будет не более 2 мм.
Вдруг вам вообще не захочется ковать, достаточно просто выпрямить деталь, и остальное можно сточить на шлифовальной машине. Но учтите, потеря в ширине и длине клинка, и сам процесс ковки придаёт металлу дополнительную жёсткость.
По окончании ковочного процесса обязательно требуется провести «нормализацию» стали. Нагреваем заготовку до 900 °С, вынимаем из печи и оставляем на воздухе остывать.
Обдирочные и шлифовальные работы с заготовкой
Всё, что было выполнено в процессе ковки, можно назвать «черновой» работой. Теперь предстоит привести деталь в соответствующий вид. Срежьте при помощи УШМ пруток. На шлифовальном станке, или ленточной машине не сильно прижимая, аккуратно нужно снять весь нагар с металла.
Таким образом, уйдут все неровности и поверхность станет блестящей. Не увлекайтесь этим процессом, дабы не снять лишнего с заготовки. Хотя после этой процедуры, в руках у вас уже будет практически клинок.
Перенос контуров с шаблона на клинок
Дошло дело и до эскиза, который мы выполняли в самом начале. Может случиться так, что чертёж не совпадёт с реальностью. Грустить, тут нет смысла, ведь это черновой вариант. Его надо вырезать и приложить на клинок, а есть смысл, даже приклеить на время любым бумажным клеем.
Чертеж ножа для изготовления из подшипника.Теперь деталь можно закрепить в тиски, и при помощи «болгарки», абразивным кругом доводим клинок до нужного вам вида, попутно, срезая все задиры и неровности. Единственным минусом может быть, металл нагреется, и бумага сгорит. Поэтому прежде чем её приклеивать, надо процарапать все контуры с эскиза. Задача не из лёгких, но это просто необходимо.
Во время вырезания образа клинка нельзя допускать перегревания детали, даже небольших участков. Поливайте водой заготовку. По окончании работ можно переходить к следующему этапу.
Заточка и шлифовка
В самом начале изготовления ножа вы должны были задуматься: для каких целей он создаётся. Так как заточка для каждого типа изделия абсолютно разная. Но первым делом нужно вывести спуски.
Заострять внимание на них не будем, но запомните: главное в спусках – это симметричность. Только после их выведения, можно приниматься за заточку клинка, но сначала шлифовка. Её можно производить на шлифмашине или при помощи УШМ со специальным кругом. Затем в хвостовике просверливаются два-три несквозных отверстия для крепления рукояти. Во время закалки может случиться неприятность, если просверлить отверстия полностью.
Закалка и отпуск клинка
Очень важный момент, особенно для новичков. Согласно справочнику, температура закалки стали – 830 °С. Разогреть печь, до заданной отметки поможет термометр. Если его нет в наличии, следует воспользоваться одним из способов:
- самый простой и распространённый, проверять магнитом, как только не «прилипает» клинок к нему – цель достигнута;
- следующий очень интересный, посыпать деталь солью, её отметка плавления в 800 °С, значит осталось ещё немного;
- и способ для «прожжённых» профессионалов – цвет заготовки становится светло-красный.
Все способы действенны, но точнее термометра нет ничего. А в данном случае очень важна точность. Нагрев до нужной точки, клинок вынимается и опускается в масло с выдержкой 1 минута на 1 мм толщины изделия. Масло можно использовать практически любое: растительное, минеральное, машинное отработанное или трансформаторное.
Закалка лезвия ножа.Предварительно его нужно подогреть до 50 °С, это необходимо для хорошего обволакивания погружаемого изделия. Производя такие работы, будьте аккуратны, наденьте защитные очки и перчатки, есть вероятность разбрызгивания масла. Не нужно шевелить клинком, когда он находится в погружении.
После охлаждения заготовки пришёл момент для отпуска стали. Процедура ослабит напряжение в структуре кристаллической решётки металла, возникшее при ковке и закалке. В справочнике указанна температура в 150 °С и время 1,5 часа. Разогрев духовой шкаф кухонной газовой плиты, помещаем туда клин на нужное время.
Очистка клинка
После всех проведённых манипуляций, грубой очистки на гриндере, на клинке останутся тонкие, мелкие царапины. Убирать их надо вручную используя наждачную бумагу. Обрабатывать нужно начиная с зерна 400 перпендикулярно царапинам.
Затем переходим к 600-ому зерну и заканчиваем 800-ым. Добиться зеркального блеска, можно использовав пасту ГОИ или специальные шлифовальные смеси.
Подготовка накладок и сборка ножа
Материалов для изготовления рукояти, довольно широкий выбор: различные металлы, пластмассы, кожа, обмотка бечёвкой и прочие варианты. Но многие мастера любят работать именно с древесиной, она часто подчёркивает уникальность клинка и его красоту.
Принцип накладной рукояти довольно прост, и надёжнее, чем другие способы крепления. После отпуска металла можно насверлить отверстия в хвостовике окончательно. А также приготовить брусок:
- Примерить к хвостовику, разметить и придать форму близкую к его размерам.
- Зажав деталь в тиски, разрезать вдоль, строго пополам;
- Для устранения зазоров внутренние части половинок ошкуривают наждачкой.
- Делается разметка в соответствии с отверстиями на хвостовике, и насверливаются в дереве.
- Следующим этапом, можно поступить по-разному, проще всего заклепать ручку клёпками.
- На точильном станке или гриндере обработать рукоять окончательно, под нужную форму вместе с хвостовиком.
- В заключении дерево обрабатывают наждачкой с мелким зерном и пропитывают специальными масляными растворами или покрывают лаком. Зависит от сорта древесины.
Для доведения дела до окончательного варианта можно смастерить ещё и ножны. Но это уже другая и довольно обширная тема. Весь описанный процесс, для новичка может показаться очень сложным. Но люди, занимающиеся этим постоянно, изготавливают такие ножи, словно на конвейере. Так что не расстраиваться при случайных ошибках, продолжать работать, пробовать. И результат не заставит себя долго ждать. Удачи в начинаниях!
ИзготовлениеКак сделать нож из косы своими руками
СледующаяИзготовлениеМонтаж рукояти ножа своими руками
Как вырезать в бутылке дырку.

Очень оригинальные светильники получаются из фигурных и цветных стеклянных бутылок от напитков. Предпринятые в свое время несколько попыток просверлить бутылки заканчивались неудачами. Способы сверления стекла попадались какие-то экзотические и заканчивались обычно длинной трещиной в стекле от места сверления. А вот если использовать специальное сверло по стеклу все получилось. Для сверления красивой прямоугольной бутылки от неплохого напитка приобретено сверло с твердосплавной вставкой (
Особенности сверления стеклянной бутылки
1. Закрепленное в электродрели сверло строго перпендикулярно направляем к точке сверления бутылки и с небольшим нажимом ждем появления первых крошек стекла.
Сверло для стекла
2. Сверлить на максимальных оборотах не надо, сверло боится перегрева.
3. Каждые 20-25 секунд сверление прекращать и удалять стеклянную крошку. Заодно и наконечник сверла охладится.
4. При проходе кончиком сверла толщины стекла звук сверления несколько изменится и следует снизить подачу сверла (нажим) до минимума.
5. После сквозного прохода сверлом толщины стекла, промываем бутылку в проточной воде.
6. При сверлении лучше соблюдать меры техники безопасности — работать в перчатках,очках и средствах защиты органов дыхания.
Таким способом своими руками было успешно просверлено несколько стеклянных бутылок из которых были сделаны оригинальные ночники с питанием от сети 220 вольт.
- Дизайн интерьера, декор (63)
- Часы, панно и другие мелочи для дома (52)
- Декупаж (39)
- Делаем сами (37)
- Мастер-классы по декору разные. (37)
- Шитье, печворк, аксессуары (31)
- Стекло, витраж, роспись (29)
- Полезные советы для дома (29)
- Книги и журналы по декору (27)
- Бумага, квиллинг. (19)
- Свет, лампы, светильники. (19)
- Лепка, пластика, фимо (17)
- Полезные ссылки (17)
- Новая жизнь старых вещей (15)
- Материалы для творчества (15)
- Уроки рисования и росписи (10)
- Домашним любимцам пушистым и хвостатым.
(8)
- Зеленый уголок в доме. Цветы и растения. (8)
- Мыло своими руками (5)
- Свечи (5)
- Батик, роспись по ткани (4)
Меня часто спрашивают КАК сделать дырочку в бутылке для создания основания лампы.
Вот короткий мастер класс, как это делаю я.
* Патрон для лампы E14
* электрический шнур с выключателем
* Матовая ЭНЕРГОСЕБЕГАЮЩАЯ лампочка с цоколем Е14, мощностью 7-8W
* Перка для металла
* Cверло для стекла и керамики
* Баночка с водой
Меня часто спрашивают, как сделать дырочку для шнура в бутылке.
Для этого надо приобрести в хозяйственном магазине специальное сверло по стеклу и керамике. Для Отверстия, я использую сверло перо №6 или №8.
Так же Вам понадобиться дрель или шуруповерт.
Вот несколько фоток с теми материалами, которые Вам понадобятся.
Берем бутылку и обматываем место, где будет расположена дырочка малярным скотчем 2-3 раза.
Вот что должно получиться:
Сначала делаете отверстие, потом декорируете бутылку, потом собираете все вместе.
Теперь несколько слов про патроны для лампочек.
Патроны бывают двух видов «без юбочки» и с «юбочкой». Нам нужны патроны с юбочкой и крепежным кольцом.
Теперь берем крышку от бутылки (меня не было свободной, так что в качестве примера взята обычная крышка).
Выводим шнур сквозь горлышко бутылки.
Соединяем шнур и патрон.
Продеваем патрон сквозь дырку в крышке. Нижняя «юбочка» патрона не даст крышке спадать. Для надежности по кругу юбочки капаем из клея пистолета и крепим крышку к юбочке.
Закрываем бутылку крышкой. Все наш патрон надежно закреплен.
Верхним прижимным кольцом, Вы впоследствии прикрепить абажур к патрону.
Ваша фантазия по декорированию, бутылки и абажров остается в ваших руках! Творите и у Вас все обязательно получится!
Сегодня мы делаем новогодний светильник. Для этого понадобится несколько простых вещей. Самое главное – нужно решить, как просверлить стеклянную бутылку. Способ подойдет тот, который доступен в домашних условиях.
В принципе, проделать дырку в стеклянной бутылке удастся и простым сверлом. Обычным по металлу, твердосплавным победитовым наконечником. Специальным по керамике. Но мы выбираем самый лучший вариант – это сверло с алмазным напылением. Так как диаметр его 12 мм, мы другим сверлом того же размера делаем отверстие в деревянной планки. Это будет направляющая. Алмазное сверло не имеет центра и работать им без предварительной подготовки обрабатываемой поверхности тяжело. Как видим, отверстие вышло идеальным.
Берем стеклянную винную бутылку. Из обычного пластилина делаем формочку для воды. Она будет охлаждать сверло. Сверху накладываем шаблон и фиксируем малярной лентой. Теперь направляющие никуда не денется с ее помощью удобно удерживать бутылку на столе. Заполняем буду практически доверху. Начинаем сверления на маленьких оборотах. Отверстие просто идеальное для домашних условий. Небольшие сколы остались от того, что не ослабил давление до минимума.
Края тут не опасны, но всё равно пройдёмся наждачной бумагой. Резиновая пробка, чтобы провод не терся о край стекла. Аккуратно сверлим с двух сторон, чтобы обеспечить точное сверление. Разрезаем с одной стороны два отверстия. Гирлянду заправляем внутри. Пробку одеваем на провод и вставляем в отверстие. Тут начинается новогодняя сказка… И проблемы…
В данном примере использовались лампочки накаливания, поэтому температура в бутылке достигла почти 100 градусов, это за полчаса. Опасная штука! Вытащив пробку, мастер надеялся увеличить вентиляцию, но это не помогло. Температура не спадала. Неужели сказки не будет? Не переживайте! Ее спасут современные технологии. Старые гирлянды пойдут кому-нибудь на подарок. А мы будем использовать современные светодиодные. Хотя такие же китайские, как прежние. В ту же бутылку заправляем их. Всё работает. Термометр показывает 23 градуса. Выставляем режим постоянного свечения и оставляем на полчаса. Через некоторое время температура поднялась всего на несколько градусов. Крепим регулятор на двухсторонний скотч для удобства. Всё. Сказке быть! Порекомендуйте это видео друзьям, может быть им тоже захочется увидеть подобную красоту. Подписывайтесь на канал стройхак на youtube. Смотрите видеоролик, с станет ясно, как мастеру удалось просверлить аккуратно стеклянную винную бутылку, используя алмазный инструмент в домашних условиях.
Как просверлить бутылку простым сверлом
Как сделать отверстие в стеклянной бутылке
Здравствуйте, мои дорогие друзья! Роман с тобой, как обычно. Было два вопроса: один – как сделать отверстие в стеклянной бутылке, а второй – как разрезать стеклянную бутылку. Я отвечу на второй вопрос чуть позже, так как я провожу эксперименты и ищу наиболее удобный способ сделать это.
Давайте начнем отвечать на первый вопрос. Вот бутылка вина. Я сделал такую подставку с простыми деревянными перилами заранее. Это поможет избежать перемещения бутылки при сверлении отверстия. Если вы не можете сделать такую стойку, вы можете вырыть яму в земле, положить два кирпича или два скота, это зависит от вашего воображения. Первое, что нам нужно сделать, это обернуть бумажный скотч вокруг бутылки рядом с местом отверстия. Например, мы завернем это здесь. Затем нанесите отметку на место бурения.
Мы собираемся использовать простую дрель, конечно, лучше использовать отвертку, так как она имеет низкую скорость вращения и нам не нужна высокая скорость вращения для сверления стекла. Сверло простое, без пыли из карбида вольфрама.
Это сверло 8,2 мм, сталь Р6М5. Давайте начнем. Важно не сильно нажимать на дрель, потому что стекло может треснуть, и мы не сможем его обработать. Итак, позвольте мне показать вам, что мы получили. Как видите, стекло начало сверлиться.
Важно также добавить немного воды в отверстие, чтобы не перегреть дрель и стеклянную бутылку.
Ну, мы сделали дыру.
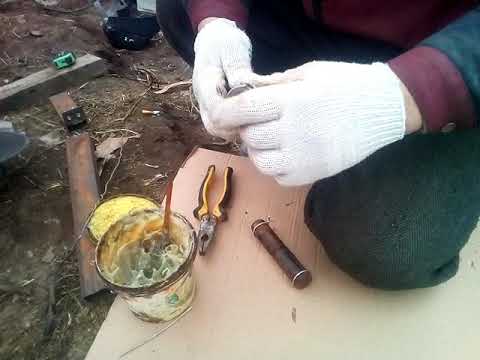
Давайте удалим скотч и посмотрим, что у нас там. У нас есть такая дыра. Если вы посмотрите поближе, вы заметите небольшие трещины внутри, это вызвано избыточным давлением сверла в конце. Если вы контролируете нажатие сверла, особенно в конце сверления, когда отверстие почти сделано, вы получите идеальное отверстие. Таким образом, вы можете видеть, что мы сделали это хорошо, не используя карбид вольфрама или специальные приборы.
Источник: crazyinvent.com
Металлическое кольцо в бутылке с колой: сверлим бутылку
Это то, что называется Невозможный объект.
Эти типы объектов не являются буквально невозможными, конечно, так как все они так или иначе созданы.
Эти вещи являются осязаемыми иллюзиями, которые можно держать и проверять вблизи. Кажется, они не поддаются логике и кажутся «невозможными». Они отлично подходят для подарков, интересны для обсуждения и представляют собой интересную задачу.
Предмет, который я здесь сделал, представляет собой цельнометаллическое кольцо толщиной 1/4 дюйма через два отверстия в горловине бутылки для кокса. На бутылке или кольце нет видимых швов.
Шаг 1: Видео
Это было вдохновлено большим проектом Джека Хоувелинга на YouTube, где он помещает деревянное кольцо в бутылку с колой: Невозможное кольцо через стеклянную бутылку.
Я задавался вопросом, как трудно было бы создать в основном то же самое, но с металлическим кольцом вместо дерева.
Я сделал видео процесса создания. Проверьте это, если вы заинтересованы:
Шаг 2: Что вам нужно
Шаг 3: Обезжиривание кольца
Первое, что я сделал, положил оцинкованное кольцо в уксус до полного растворения покрытия.
Это важно, потому что, хотя вы можете технически сваривать покрытие, оно выделяет токсичный газ, который чрезвычайно опасен.
Таким образом, это самый простой способ сделать такие детали оборудования, как этот, безопасными для сварки.
Я купил это кольцо в местном хозяйственном магазине. У них также были никелированные кольца, которые имеют более блестящий и почти желтоватый оттенок, но это покрытие не может быть растворено в уксусе. Общее эмпирическое правило – никогда не сваривать сквозные покрытия. Так что, что вы не можете безопасно растворить, вы должны размолоть до голого металла.
Шаг 4: Просверлите отверстия в бутылке
Крышка от бутылки была очень осторожно поднята из нескольких точек, чтобы снять ее, не деформируя. Таким образом, мы можем добавить это позже. Затем я выпил колу.
Я установил доску на своем сверлильном станке, к которой я зажал бутылку кока-колы.
Доска была прикреплена к моему столу для сверлильного станка, и бутылка с распылителем использовалась, чтобы держать зону бурения влажной.
Сверло было настроено на более низкую скорость, и в верхней части горлышка бутылки было сделано два отверстия с использованием стеклянного
сверла 5/16 дюйма. Вам нужно идти довольно медленно и позволить буровому долоту удалять лишь немного за раз,
Шаг 5: Вырезать кольцо
Металлическое кольцо разрезали пополам с помощью переносной ленточной пилы.
Шаг 6: Отверстия в горлышке бутылки
Я использовал алмазную шлифовку в своем вращающемся инструменте, чтобы отшлифовать внутренние края отверстий в бутылке, чтобы кольцо могло свободно проходить и вращаться вверх и вниз, не застревая.
Это было сделано с частыми туманами воды от пульверизатора.
Шаг 7: Приварить кольцо
Половинки колец были прикреплены к моему металлическому сварочному столу, одна половина проходила через отверстия в бутылках.
Затем кольцо было приварено несколькими небольшими точечными сварками вокруг обоих соединений.
Шаг 8: Подготовить кольцо
Используя твердосплавную шлифовальную насадку в своем вращающемся инструменте, я тщательно шлифовал сварные швы, чтобы придать форму кольца.
Затем я заточил все вокруг кольца и намеренно сделал его немного грубым, чтобы придать всему виду довольно изношенный вид.
Шаг 9: Отполировать кольцо
Некоторая автомобильная полировка металла использовалась с парой тряпок, чтобы быстро полировать и полировать металлическое кольцо вручную.
Шаг 10: Вымыть бутылку
Меня часто спрашивают КАК сделать дырочку в бутылке для создания основания лампы.
Вот короткий мастер класс, как это делаю я.
Вам понадобится :
* Винная бутылка с широким горлышком и завинчивающейся крышкой
* Патрон для лампы E14
* электрический шнур с выключателем
* Матовая ЭНЕРГОСЕБЕГАЮЩАЯ лампочка с цоколем Е14, мощностью 7-8W
* Перка для металла
* Шуруповерт
* Cверло для стекла и керамики
* Надфиль алмазный (рекомендация forcon )
* Баночка с водой
* Ножницы
* Клей пистолет
* Очки защитные (рекомендация ntl )
* Защитная маска
Меня часто спрашивают, как сделать дырочку для шнура в бутылке.
Для этого надо приобрести в хозяйственном магазине специальное сверло по стеклу и керамике. Для Отверстия, я использую сверло перо №6 или №8.
Так же Вам понадобиться дрель или шуруповерт.
Вот несколько фоток с теми материалами, которые Вам понадобятся.
Порядок работы
:
Берем бутылку и обматываем место, где будет расположена дырочка малярным скотчем 2-3 раза.
Отмечам место сверления крестиком. Обратите внимание, что на бутылках есть швы, лучше не сверлить непосредственно в шов бутылки. Сместите место сверления на 1-2 см.
Начинаем процесс сверления. Окунаем сверло в воду и Стараемся держать сверло очень ровно на средних оборатах начинаем сверлить. Самое главное- ни в коем слечае не давить на бутылку. Действуйте уверенно, но не жестко.
Сверление займет минут 10-15. Сверло-перо, как бы будет выцарапывать стекло.
Во время сверления, реглярно опускаем сверло в воду и капаем на место сверления.
Псоле того, как сверло прошло насковзь, еще некоторое время аккуратно рассверлите дырочку, совершая легкие вращательные движения. Это сделает срез дырочки более гладким.
Обычным надфилем или грубой наждачкой обработайте край среза.
Вот что должно получиться:
Теперь берем шнур с выключателем
И продеваем его сквозь дырочку, вытягивая вверх.
Хочу сразу оговориться, что если Вы планируете задекорировать бутылку, то порядок работы, должен быть таким:
Сначала делаете отверстие, потом декорируете бутылку, потом собираете все вместе.
Теперь несколько слов про патроны для лампочек.
Я использую патроны для лампочек с размером цоколя Е14. Мощностью 40W обычная лампочка или 7-8W энергосберегающая. Я предпочитаю энергосберегающие лампы, они не нагревают абажур.
Патроны бывают двух видов «без юбочки» и с «юбочкой». Нам нужны патроны с юбочкой и крепежным кольцом.
Вот НЕ правильные патроны, БЕЗ «юбочки»
ПРАВИЛЬНЫЙ патрон с «юбочкой» и кольцом.
Теперь берем крышку от бутылки (меня не было свободной, так что в качестве примера взята обычная крышка).
Делаем на ней отметку с серединкой. Измеряем диаметр патрона, и выбираем соответствующую перку по металлу.
Что же делать, если перки по металлу нет? Предлагаю такой способ: Шилом по кругу пробиваете дырочки, часто и близко друг к другу и потом ножницами хозяйственными или надфилем пропиливаете.
Все дырка готова и мы начинаем собирать все вместе.
Выводим шнур сквозь горлышко бутылки.
Соединяем шнур и патрон.
Продеваем патрон сквозь дырку в крышке. Нижняя «юбочка» патрона не даст крышке спадать. Для надежности по кругу юбочки капаем из клея пистолета и крепим крышку к юбочке.
Закрываем бутылку крышкой. Все наш патрон надежно закреплен.
Верхним прижимным кольцом, Вы впоследствии прикрепить абажур к патрону.
Внимание, бывают ситации, что крепление абажура в диаметре больше, чем закрепительное кольцо. Что делать? Надо сделать прокладочку уранивающую диаметр абажура и диаметр крепительного кольца.
Ваша фантазия по декорированию, бутылки и абажров остается в ваших руках! Творите и у Вас все обязательно получится!
С помощью этого учебного пособия вы узнаете как просверлить отверстие в стекле. Вместо того, чтобы выбросить свой стакан, превратите его во что-нибудь красивое и практичное. Бутылка из мусорного ведра может превратиться в настоящее сокровище. Но сначала, вам нужно научиться сверлению отверстий в стекле или зеркале.
В данной статье мы рассмотрим способы сверления в стекле, и разберем ошибки.
Вот некоторые правила, которые нужно соблюдать при сверлении закаленного стекла:
- Будь осторожным!
- Будь терпеливым.
- Будь умным.
Если при сверлении стекла в домашних условиях вы в чем-то сомневаетесь, перейдите к правилу №1.
Шаг 1: Будьте осторожны
Соблюдайте следующие правила безопасности при сверлении стекла:
- Прежде, чем приступить к серьезному проекту, потренируйтесь на ненужных стеклянных бутылках.
- Обезопасьте себя, – наденьте защитные очки, чтобы защитить глаза от возможного разлета стеклянных осколков.
- Наденьте защитные перчатки, чтобы защитить руки от порезов, если вдруг сосуд треснет или разобьется во время сверления. Это случается довольно часто.
- Будьте терпеливы, – не форсируйте работу сверла. Позвольте инструменту качественно сделать свою работу.
- Не спешите, – это просто напоминание о терпении.
Шаг 2: Неудачи
Первые попытки просверлить отверстие в бутылке, скорее всего потерпят неудачу. Не пытайтесь просверлить дно. Стекло дна имеет слишком большое внутреннее напряжение, что может привести к растрескиванию. Также не пытайтесь просверлить бутылку насквозь, – это плохая идея, т.к. она скорее всего треснет. Некачественное или изношенное сверло тоже может привести к аварии.
Работая сверлом с твердосплавным наконечником для плитки и стекла нельзя сильно нажимать на сверло, иначе бутылка сразу даст трещину. Для сверления предпочтительнее воспользоваться алмазным трубчатым сверлом.
Такие сверла можно приобрести на Amazon.
Шаг 3: Инструмент и материалы
Сверлить можно и с помощью дрели, но лучше для этой цели использовать сверлильный станок.
Можете приобрести себе вот такой станок за 59,99 долларов . Он сделает вашу жизнь проще.
- Подушка (во время сверления подкладывается под бутылку).
- Сверлильный станок (предпочтительнее дрели, гораздо устойчивее и проще в обращении).
- Алмазное трубчатое сверло диаметром 6 мм; или
- Сверло с твердосплавным наконечником для плитки и стекла.
- Кожаные перчатки для защиты рук от осколков стекла (так, на всякий случай).
- Вода.
- Стеклянная бутылка.
Отдайте предпочтение алмазному трубчатому сверлу.
Шаг 4: Сверлим стеклянный череп
Всегда ищите более тонкое место для сверления на стеклянной таре. Если, например, взять бутылку в виде стеклянного черепа, то ее дно имеет очень большую толщину, поэтому сверлить его нет никакого смысла (стекло просто расколется). Зато задняя нижняя часть стеклянного черепа имеет толщину не более 6 мм, поэтому сверлить нужно в этом месте.
Подложите подушку (можно использовать, например, старую толстовку) на стол сверлильного станка, чтобы уменьшить давление на стекло, создаваемое сверлом во время сверления. Это также защитит стекло от царапин.
Процесс сверления.
- Поместите подушку на стол сверлильного станка.
- Вставьте в патрон сверлильного станка алмазное трубчатое сверло диаметром 6 мм.
- Проверьте глубину сверления, чтобы убедиться, что вы просверлите стекло полностью.
- Установите бутылку под сверло тем местом, которое вы хотите просверлить.
- Крепко держите бутылку рукой, предварительно надев на руку перчатку.
- Включите сверлильный станок и начинайте сверлить, не прилагая большого усилия к рукоятке подачи шпинделя.
- Поливайте водой место сверления каждые 20 секунд, чтобы смыть пыль и охладить стекло.
- Охлаждайте стекло водой пока полностью не просверлите стенку бутылки.
- Смойте стеклянную пыль.
Вся работа займет у вас не более 2 минут.
Вам понадобится
- — пневматический пистолет;
- — дрель с алмазным или закаленным стальным сверлом;
- — скипидар;
- — серная кислота;
- — вода;
- — песок или глина;
- — шаблон из дерева, пенопласта, стекла, металла или другого материала;
- — наждачный порошок.
Инструкция
Самый быстрый способ: возьмите с хорошо заряженным баллоном. Встаньте на расстоянии нескольких метров, тщательно прицельтесь и выстрелите в бутылку. Вылетевший шарик пробьет бутылку из- насквозь, не разбив ее. Учтите, что отверстий будет два, причем довольно маленького диаметра.
Чтобы просверлить в бутылке отверстие нужного диаметра, сначала приготовьте приспособление для надежной фиксации посуды, например, коробку, в которой она будет плотно сидеть. Возьмите алмазное сверло по керамике и очень осторожно, не давя, сверлите. Обязательно продумайте систему охлаждения. Это может быть постоянно поступающая вода (здесь понадобится помощник) или специально подготовленный охладитель. Чтобы его изготовить, сделайте шаблон из дерева, пенопласта или другого материала, высверлив в нем отверстие нужного диаметра, и прикрепите его воском к бутылке. Наполните ямку наждачным порошком (его можно получить из наждачной бумаги или абразивного круга), перемешанным со скипидаром.
Чтобы просверлить отверстие в стеклянной бутылке стальным сверлом, перед употреблением нагрейте его добела и смочите в серной кислоте.
Чтобы просверлить отверстие большого диаметра, возьмите трубку из цветного металла (алюминий, латунь, медь, бронза) длиной 2,5-5 см и используйте ее в качестве сверла. К стеклу прикрепите кружок из пенопласта, стекла, дерева, металла или другого материала нужного диаметра, в него будет упираться трубка при сверлении. Насыпьте в открытый конец трубки смоченный водой наждак и медленно сверлите, на небольших оборотах. Следите, чтобы наждачная паста всегда была между краями трубки и стеклом.
Если вы хотите обойтись без сверления, возьмите глину или мелкий песок. Тщательно отмойте поверхность от жира и грязи при помощи ацетона, спирта или бензина. Насыпьте мокрый песок или глину, размешанную до тестообразного состояния, в виде горки высотой около 10 мм. Сделайте воронку палочкой или другим инструментом, при этом диаметр просвечивающего стекла внутри ямки должен соответствовать диаметру желаемого отверстия. Расплавьте в металлической баночке свинец, олово или другой припой, залейте его в полученной лунку. Отверстие получится с гладкими краями, но учите, что этот способ подходит для стекла не толще 3 мм.
Пескоструй своими руками: как собрать полезный инструмент
ПОДЕЛИТЕСЬ
В СОЦСЕТЯХ
Перед чистовой отделкой поверхности ее требуется очистить от загрязнений и старого покрытия. Каждый, кто хоть раз подготавливал стены к покраске либо снимал остатки ржавчины с металла, представляет, сколько сил и времени отнимает данный процесс. Если делать это вручную, результат не всегда получается удовлетворительным. Пескоструйный аппарат – прибор, полирующий поверхность песком. Изготовить пескоструй своими руками – задача не такая и сложная.
Пескоструйный аппарат – это прибор, с помощью которого можно очистить любую поверхность песком
Что собой представляет пескоструйный аппарат: из каких элементов состоит
Пескоструй – это аппарат, подающий под большим давлением струи песка, которые очищают и полируют поверхности. Использование прибора позволяет не только качественно, но и быстро избавиться от загрязнений или, например, матировать стекло.
Пескоструйный аппарат состоит из компрессора, ресивера, емкости, пистолета и соединительных шлангов
Особенно пригодится прибор для небольших автомастерских, для хозяев, которые любят придавать старым вещам новый вид, а также просто для владельцев частных домов, где постоянно требуется наводить порядок. Наиболее удобным для работы считается пескоструйный пистолет с рециркуляцией, позволяющий использовать абразив повторно.
Факт! Конечно, всегда присутствует возможность приобретения на строительной торговой площадке готового прибора. Но стоимость устройств довольно высокая, а найти детали в гараже, чтобы изготовить самодельный пескоструйный аппарат своими руками, – незатратно и просто.
Как сделать пескоструй своими руками? Существует несколько способов. Для этого применяются 2 основные конструкционные схемы, главное отличие которых – механизм подачи абразивного песка в выходной такт. Несмотря на это, оба варианта требуют наличия практически одинаковых деталей для создания значимых узлов. Итак, в целом пескоструи состоят из таких элементов:
- компрессор – основная деталь, нагнетающая воздух;
- ресивер – элемент, который чаще всего изготавливается на основе газового баллона;
- емкость небольшого объема – выполняется из огнетушителя или фреонового баллона, именно сюда помещается пескоструйный песок;
- пистолет, через который и будет осуществляться подача абразива;
- соединительные шланги.
Пескоструй промышленного типа состоит из таких же компонентов как и бытовой
Все специалисты, изготавливающие самодельные пескоструйные аппараты, акцентируют внимание на том, что если хочется, чтобы прибор работал дольше, то требуется оборудовать его влагоотделителем. Если речь идет о поршневом компрессоре, деталь следует установить на входном такте подачи воздуха в систему фильтрации масла.
Что нужно знать о принципе работы самодельного пескоструя
Какой бы ни был выбран тип конструкции, прибор должен формировать на выходе струю воздушно-абразивной смеси. Напорная система работает благодаря высокому давлению подачи выбранного абразива в выпускной патрубок, где происходит смешивание с воздушным потоком, подающимся из компрессора. Если говорить об эжекторном устройстве, стоит знать, что здесь работа осуществляется с использованием эффекта Бернулли, основанном на создании вакуума, который и засасывает песок.
Существует огромное количество схем и выполненных своими руками чертежей пескоструйных аппаратов, позволяющих изготовить их самостоятельно. Каждый изобретатель предпочитает использовать различные ненужные детали, которые находятся под рукой, но все конструкции будут работать по схожему принципу.
Перед тем как сделать пескоструйный аппарат своими руками, нужно понять механизм работы инструмента, подготовить все необходимые детали конструкции. Если правильно собрать элементы, самодельный аппарат ничем не будет уступать серийному. Зачастую удается сконструировать прибор с минимальными затратами.
По принципу работы пескоструйный аппарат очень похож на краскопульт
Это интересно! Принцип работы пескоструя очень похож на механизм действия краскопульта, главная задача которого – распыление лакокрасочных материалов. Тем не менее один прибор никогда не сможет заменить другой.
Главный элемент, который понадобится для пескоструйного аппарата, – компрессор. Именно благодаря ему в магистралях конструкции создается поток воздуха под нужным давлением. Когда воздух проходит по главному шлангу сквозь рукав для забора песка для пескоструйного аппарата, создается вакуум, способствующий тому, что абразивная смесь всасывается в основную магистраль, где и соединяется с воздушной струей.
Затем уже смесь из воздуха и абразива доходит до сопла – отверстия, через которое и осуществляется подача песка на поверхность под высоким давлением. Из этого следует, что, помимо компрессора, требуется дополнить конструкцию шлангами нужного диаметра, соединительными штуцерами, кранами и дозаторами. Чтобы обеспечить бесперебойное питание рабочего прибора, понадобится электрический кабель.
Пескоструйное сопло – элемент, формирующий абразивную струю с нужными для работы характеристиками. Своими руками можно изготовить керамическое сопло, потому как для основы идеально подходят отработанные свечи зажигания, из которых предварительно вынимается электрод. На серийных приборах присутствует стальной элемент, имеющий внутреннее карбидно-борное или карбидно-вольфрамовое покрытие. В многочисленных отзывах пользователей отмечено, что такие детали очень редко долго служат владельцам.
Пескоструйное сопло формирует с нужными для работы характеристиками абразивную струю
Пескоструй своими руками: типы приборов и преимущества самостоятельного изготовления
Перед тем как переходить к созданию чертежей пескоструя своими руками, следует больше узнать о самом приборе и основных видах инструмента, а также взвесить все за и против относительно самостоятельного изготовления. В целом все приборы можно разделить на 3 большие группы:
- Всасывающие. Подойдут для выполнения несложных работ по очистке поверхностей. Принцип действия чрезвычайно прост: воздух засасывает песок из емкости, после чего смесь подается на сопло. Это наиболее простой вариант для домашнего изготовления.
- Прибор, работающий по принципу вакуума. Основное преимущество пескоструйного пистолета с рециркуляцией абразива – возможность многоразового использования вещества, вышедшего сквозь сопло. Песок в этом случае повторно засасывается в резервуар через специальную камеру.
- Пневматический пескоструй. Устройство отличается огромной мощностью и подает абразив под большим давлением. С помощью инструмента можно легко очистить даже самые загрязненные поверхности и запущенные ржавые детали.
Факт! Пневматический пескоструй рекомендуется использовать не только тогда, когда требуется обработать сильнозагрязненные поверхности, но и в том случае, если планируется очистить большую площадь.
Зачастую конструкции очень сложные, поэтому самостоятельно их изготавливают редко.
Пескоструйные аппараты можно разделить на всасывающие, вакуумные и пневматические
Перед тем как сделать пескоструйный аппарат, следует изучить достоинства и недостатки такой работы. Преимущества самостоятельного изготовления:
- при наличии всех комплектующих и навыков сборки инструмента создание устройства не займет много времени;
- есть возможность сэкономить на покупке серийного товара;
- если применять качественные комплектующие, прибор получается даже надежнее заводского варианта.
Среди минусов самостоятельного изготовления выделяются такие нюансы:
- собирать инструмент может только человек, обладающий соответствующими навыками;
- если приобрести некачественные детали, прибор долго не прослужит;
- неправильно подобранное и установленное сопло не только усложнит работу, но и снизит эффективность.
Применение качественных комплектующих при изготовлении пескоструйного аппарата своими руками обеспечит надежность изделия
Главным недостатком считается то, что если при сборке не учесть всех моментов, неправильно или ненадежно собрать соединения, то присутствует риск получения травмы из-за разрыва клапана или резервуара с абразивом. Если перед тем, как своими руками начать собирать прибор, посоветоваться со специалистом в этой области, создать грамотный и подробный чертеж под руководством того, кто уже выполнял подобную работу, то получится надежный помощник по дому.
Какие понадобятся комплектующие: как выбрать компрессор для пескоструйного пистолета
Компрессор – наиболее важная деталь, потому как работать пескоструйный аппарат без данного элемента не будет. Поэтому к выбору следует подходить обдуманно, хотя бы по той причине, что стоит устройство довольно дорого.
Следует помнить, что именно от этого комплектующего будет зависеть производительность прибора. Многие не советуют изготавливать своими руками компрессор для пескоструя, мощность которого составляет 500 л/мин. Оптимально, когда показатель находится на уровне 700 литров. Необходимо также учесть, что эта мощность должна сохраняться и при давлении 8 бар. Основными элементами, влияющими на соотношение уровня давления и объема, являются:
Самой важной деталью в работе пескоструйки является компрессор
- диаметр абразивного и воздушного шланга;
- материал, используемый для изготовления сопла;
- длина магистрали;
- тип и вид абразивного материала.
Важный критерий, от которого зависит выбор и работа компрессора, – диаметр сопла. Чем показатель больше, тем выше давление; тем быстрее, соответственно, получится очистить поверхность. Следует также обращать внимание и на показатели давления – здесь все зависит от типа обрабатываемого материала.
В таблице показано, какого давления будет достаточно для обработки различных поверхностей:
Тип поверхности | Необходимое давление, бар |
Бетон, искусственный камень | 3-5 |
Металлические поверхности | 8 |
Поверхности, устойчивые к механическим воздействиям | 12 |
Лучше брать аппарат с определенным запасом мощности, потому как не всегда получается предварительно продумать, где придется использовать пескоструй, тем более что можно сделать прибор любой мощности.
Основные типы компрессоров для пескоструйного аппарата
В аппаратах для пескоструйной обработки используется в основном 2 типа компрессоров:
- винтовые;
- поршневые.
В большинстве случаев при самостоятельном изготовлении отдают предпочтение поршневым вариантам. Эти компрессоры отличаются высокой производительностью, но вот воздух в магистраль подается определенными толчками. Для устранения такой проблемы дополнительно устанавливается ресивер.
В устройствах для пескоструйной обработки применяются винтовые и поршневые компрессоры
Некоторыми пользователями также отмечается, что у поршневых приборов иногда случаются проблемы с подачей масла. Это приводит к появлению влаго-масляного конденсата. Следствием такого нюанса становится образование комков в абразивном материале, из-за чего возможен выход инструмента из строя.
Принцип работы пескоструйного аппарата с винтовым компрессором несколько иной. Здесь в основе прибора лежат 2 шестерни червячного типа, вращающиеся в разные стороны. Главное преимущество состоит в отсутствии шума и лишних вибраций. Именно по этим причинам, если планируется собирать пескоструйный мини-аппарат для домашнего использования, лучше выбирать именно винтовой компрессор.
По типу питания компрессоры делятся на дизельные и электрические. Каждый из вариантов отличается своими преимуществами и недостатками. Если планируется собрать небольшой мобильный прибор, лучше отдать предпочтение дизельному варианту, основное преимущество которого – отсутствие привязки к сети 220 В.
Соответственно, устройство будет удобно переносить по участку, например, для снятия краски с забора или ворот. Другое преимущество дизельного компрессора – способность автоматически управлять оборотами двигателя. Это дает возможность регулировать и экономить расход топлива.
При самостоятельном изготовлении пескоструйки отдают предпочтение поршневым компрессорам
Достоинство электрического компрессора – меньшие затраты на топливо, но постоянно присутствует подвязка к наличию розетки электросети. Использовать его можно при любых температурах, в то время как для работы дизельного прибора в морозных условиях придется дополнительно приобретать установку холодного старта и предварительного подогрева. Дизельные механизмы очень не любят низкие температуры.
Статья по теме:
Краскопульт для водоэмульсионной краски: разновидности и советы по выбору
Разновидности распылителей для водоэмульсионки. Рейтинг лучших моделей. Рекомендации по выбору и использованию краскопультов.
Если хочется максимально сэкономить, можно сделать устройство своими руками, используя подручные комплектующие. В частности, для работы подойдут готовые компрессорные головки, которые снимают с тормозного пневматического прибора таких автомобилей, как ЗИЛ и МАЗ. Зачастую их можно найти на старых разборках, на барахолках или на сайтах объявлений. Для нормальной работы головки потребуется оборудовать ее ресивером, а также рамой для удобного крепления остальных элементов конструкции.
Какие детали пригодятся в качестве комплектующих для изготовления пескоструйки своими руками
Перед тем как сделать пескоструй, следует позаботиться о наличии необходимых деталей, большую часть которых всегда можно найти в своем гараже, кладовой или мастерской. Недостающие предметы стоит поискать на барахолках либо в строительных магазинах. Одной из важных составляющих является емкость, откуда абразивный песок будет подаваться в магистраль. Большая часть умельцев предпочитает для этой цели применять старый газовый баллон.
Важно! Если для работы берется газовый баллон, следует внимательно посмотреть, чтобы на нем отсутствовали признаки ржавчины, вмятины и другие повреждения. Помимо использования баллона в качестве емкости для абразива, он может пригодиться для изготовления ресивера на компрессор, однако при разборке необходимо соблюдать максимальную технику безопасности.
Без наличия всех необходимых деталей собрать пескоструйку не получится
Чтобы емкость свободно наполнялась абразивом, требуется к баллону приварить фрагмент трубы. Для удобства в верхней части следует зафиксировать горловину, которая будет играть роль воронки для засыпания песка. Понадобится также и другое оборудование для пескоструя:
- Шаровые краны.
Лучше выбирать наиболее надежные и долговечные материалы проверенных производителей с хорошей репутацией.
- Армированный резиновый шланг. Оптимальным вариантом считается рукав диаметром 14 мм, который рассчитан на высокое давление и постоянное трение абразивного песка.
- Газовый шланг. Диаметр изделия должен быть не меньше 1 см. Именно по этому шлангу в систему будет подаваться сжатый воздух, который еще не смешался с абразивным материалом.
- Штуцеры и зажимы цангового типа. Нужны для того, чтобы фиксировать шланги к другим элементам системы.
- Фум-лента или другой уплотнитель. Все соединения требуют надежной герметизации, потому как пескоструй работает под постоянным высоким давлением.
Большинство необходимых деталей можно найти в своем гараже
Типы и виды абразивов для обработки поверхностей
Основным расходным материалом для работы является абразив, под воздействием которого и происходит чистка поверхности. Просто отобранный с берега реки песок для этой цели не подойдет, потому как имеет неоднородный состав, а его частицы отличаются неодинаковым размером и формой. Все это впоследствии будет влиять на качество обрабатываемой поверхности. Кроме того, большие песчинки в процессе очистки разбиваются и превращаются в пыль, а сам абразив очень быстро приходит в негодность, поэтому его требуется постоянно обновлять.
В первую очередь нужно запомнить, что для качественной очистки подойдут лишь специальные виды абразива. Зачастую это не только песок, но и другие подходящие материалы искусственного и естественного происхождения. Выбор варианта будет зависеть от специфики работы. Главными в этом случае являются такие параметры:
- твердость;
- размер;
- форма.
Интересный факт! В большинстве стран запрещено применять обычный кварцевый песок для работы пескоструя, потому как частицы кварца при ударе о металл превращаются в пыль, которая способна вызывать тяжелые легочные заболевания. Помимо воздействия на здоровье пескоструйщика, пыль может навредить окружающим, даже находящимся далеко от места работ.
![]()
В пескоструйных аппаратах применяют такие виды песка как речной, карьерный и промышленный кварцевый
В целом устройство пескоструйного аппарата предполагает использование таких типов песка, как:
- Обычный речной. Материал требуется просеять для получения однородного состава.
- Карьерный. Несколько мельче речного, но, помимо просеивания, материал требует дополнительной промывки.
- Промышленный кварцевый. Производная от обычного песка, полученная путем просеивания и разделения на фракции. По стоимости в 3 раза дороже речного.
- Особый дробленый абразив. Получен в результате дробления кварцевых горных пород. Высокую эффективность работы в этом случае обеспечивает остроугольная форма зерен, оказывающая хорошее воздействие на поверхность.
Что можно использовать, кроме песка, для изготовления своими руками пескоструйной камеры
Кроме песка, для работы аппарата подойдут и другие виды расходников:
- Никель и купершлак.
Одни из самых популярных вариантов для пескоструя, которые получаются из отходов производства меди и никеля. Стоимость такая же, как у обработанного песка, но они прочнее и тверже.
- Стальная и чугунная дробь. Не только наиболее дорогой вариант, но и самый прочный. Применяется для быстрой, но грубой обработки поверхностей.
- Гранатовый песок. Тверже обычного песка, но такой же непрочный. Стоит дорого и редко используется для работы.
- Стеклянная и нержавеющая дробь. Пескоструйное стекло применяется в основном для очистки поверхностей из нержавеющей стали.
- Электрокорунд. Твердая кристаллическая форма оксида алюминия. Практически не повреждается и подходит даже для самых загрязненных поверхностей.
Стальная и чугунная дробь является самым прочным абразивом
Если просматривать фото пескоструев, можно обратить внимание на то, что камера представляет собой конструкцию прямоугольной формы. Чаще всего это ящик, сваренный из металлического уголка, который обшит тонкими стальными листами толщиной до 1 мм. Для того чтобы легче было контролировать количество абразива в процессе работы, лучше всего по длинной стороне расположить стеклянное или пластиковое смотровое окно.
На передней стенке камеры выполняются 2 симметричных отверстия диаметром 100-120 мм, в которые вставляются специальные плотные перчатки. Следует учитывать, что они будут постоянно подвергаться воздействию абразива, поэтому замена данных элементов не должна вызывать сложностей.
Дно камеры выполняется из армированной сетки, под которой располагается желоб для использованного абразива. Удобную работу обеспечивает освещение. Для этого достаточно взять 2 лампы необходимого размера. Пистолет для пескоструйного аппарата помещается внутрь камеры, а воздух подводится при помощи шланга, подсоединенного снаружи. Таким образом, материал не будет вылетать за пределы, что даст возможность использовать его повторно. По сути, такой вариант исполнения позволяет создать пескоструйный пистолет с системой рециркуляции абразива.
Полезный совет! Если планируется чистить нестандартные изделия большой формы, боковые грани советуют затянуть прочным брезентом.
Чтобы камера получилась максимально удобной, не следует делать работы на глаз – лучше предварительно подготовить чертеж.
Кроме песка используют никель и купершлак, гранатовый песок, стеклянную и нержавеющую дробь, а также электрокорунд
С чего начать процесс изготовления пескоструйного аппарата своими руками
Самое простое, что можно попробовать изготовить своими силами, – пескоструйный пистолет. Этот вариант представляет собой конструкцию с рукояткой, наконечником и двумя штуцерами: один служит для того, чтобы подводить сжатый воздух, второй – для засасывания песка внутрь системы. Если планируется интенсивно эксплуатировать прибор, лучше все-таки приобрести готовый пистолет для пескоструйной обработки. Если же аппарат предполагается применять от случая к случаю, вполне можно попробовать создать конструкцию из предметов, которые находятся под рукой.
Чтобы пользоваться прибором было комфортно, следует начать с выбора сопла для пескоструйного аппарата. Оно представляет собой насадку, через которую выстреливает поток воздуха, смешанный с абразивом. Если имеются навыки работы и нужные инструменты, можно постараться и выточить деталь самостоятельно, но большинство предпочитает покупать готовый элемент, сделанный из карбида вольфрама или бора. В среднем детали рассчитаны на 100 и более часов работы, в то время как чугунных или керамических элементов хватает на 2-3 часа эксплуатации.
Важно! При покупке или самостоятельном изготовлении сопла следует учитывать, что материал должен быть рассчитан на воздействие абразивного песка, которое увеличивается из-за высокой скорости подачи. По этим причинам требуется, чтобы материал выдерживал механическое трение.
В соответствии с размером сопла производится пистолет для пескоструя, к которому затем подсоединяются штуцеры и рукоять. Наиболее примитивная конструкция собирается из нескольких фитингов для водопроводных труб, тройника, а также пластикового бака для песка.
Очень часто для изготовления сопла используют свечи зажигания
В упрощенном варианте в качестве емкости выступает разрезанная пластиковая бутылка, зафиксированная в верхней части конструкции. Подобного рода установку несложно собрать всего за несколько часов. Ход работ будет выглядеть таким образом:
- в бутылку засыпается песок;
- пистолет подсоединяется к бутылке;
- к пистолету подводится сжатый воздух из компрессора.
Как сделать пескоструй своими руками из газового баллона
В сети можно найти большое количество видео «Пескоструи своими руками», которые показывают, как делать приборы из газового баллона. Именно такой вариант исполнения считается не только долговечным, но и надежным. Важно во время работы придерживаться инструкций, чтобы избежать несчастных случаев. Для изготовления потребуется использовать такие детали:
- газовый баллон из-под пропана или фреона;
- мощный компрессор производительностью не менее 500 л/мин и мощностью от 3 кВт;
- шаровые краны, регулирующие подачу воздуха и абразивного песка;
- фрагмент водопроводной трубки из стали с резьбой и заглушкой, которая будет применяться в качестве воронки для поступления песка, оптимальный диаметр – 2 дюйма;
- тройник с резьбой, маркированной «ДУ 15»;
- резиновый двухметровый рукав диаметром 14 мм;
- шланг сечением 10 мм, длиной не менее 5 метров;
- 5-метровый газовый рукав, диаметр которого 10 мм;
- зажимы и фитинги для шлангов, лучше взять с запасом;
- сопло;
- пескоструйную насадку для компрессора;
- фум-ленту для надежной герметизации и уплотнения стыковочных узлов.
Пескоструйные приборы выполненные из газового баллона считаются не только долговечными, но и надежными
Сопло, как уже указывалось, можно приобрести либо изготовить самостоятельно из автомобильной свечи или металлического прутка. Главное – помнить, что от этой детали будет зависеть 80% удобства и качества работы: именно благодаря соплу в пескоструе обеспечивается необходимое давление.
Если кратко, то для изготовления сопла потребуется кусок металлического прутка длиной 3 см и диаметром 1 см. Первые 2 сантиметра длины растачиваются до 2,5 мм, оставшийся отрезок должен иметь больший диаметр – примерно 6-6,5 мм.
Пошаговая сборка пескоструйки своими руками: видео
После того как подготовлены все детали, необходимые для изготовления, приступают непосредственно к сборке. Для начала требуется полностью освободить баллон от газа. Для этого следует открутить вентиль и ждать, пока газ полностью выйдет. Нужно быть предельно внимательным, потому как если этот этап проигнорировать, то возможны неприятные последствия. Чтобы быть уверенным, что газ полностью вышел из баллона, рекомендуют вставить шланг, предварительно подключенный к компрессору. Затем проводится полное выкачивание газовой смеси.
После того как бак абсолютно опустеет, в нем нужно выполнить 2 отверстия: одно – на дне баллона (диаметром 1,2 см), второе – на противоположной стороне. Именно во второе отверстие и будет устанавливаться кран сечением 2 дюйма. Сюда же крепится труба такого же диаметра. Дальше выполняются следующие действия:
Сопло прикрепленное к шлангу обязательно нужно закрепить с помощью хомута
- На дно баллона, туда, где будет собираться песок, приваривается стальной тройник ДУ-15. Герметичность соединения обеспечит только качественная сварка.
- Для устойчивости конструкции следует приварить треногу или закрепить колеса. Второй вариант поможет значительно облегчить транспортировку прибора с места на место.
- После завершения работ по изготовлению каркаса приступают к крепежу небольших комплектующих.
На каждую резьбу помещается фитинг, все функциональные узлы уплотняются фум-лентой. Важно следить за тем, чтобы все соединения были герметичными.
- На открытые концы установленного тройника монтируются резьбовые втулки. Один из выходов патрубка закрывается при помощи шланга 14 мм, а второй – медной трубкой диаметром 10 мм. На медный патрубок крепится армированный рукав.
- К вентилю на баллоне подсоединяется штуцер 14 мм. Затем нужно взять шланг 14 мм и зафиксировать его (с использованием цангового зажима) у баллона, другой край крепится на хомут к тройнику.
- На оставшийся свободный конец тройника монтируется рукав, объединяющий тройниковый смеситель с соплом.
На последнем этапе компрессор соединяется со смесителем при помощи 10-миллиметрового шланга, после чего можно пробовать подключать установку и начинать эксплуатацию. Если потребуется увеличить мощность подачи песка, к емкости прикрепляется дополнительный штуцер, другой конец которого присоединяется к компрессору.
Пескоструй своими руками из огнетушителя: краткая инструкция
При использовании баллона для огнетушителя получается практически такой же прибор, как в случае с газовым баллоном, только более компактного размера. Минусом подобной конструкции является небольшая емкость для песка, которую потребуется постоянно наполнять. Значительными преимуществами считаются компактные размеры и удобная транспортировка приспособления.
Факт! Сделать пескоструй из огнетушителя намного проще ввиду того, что вентиль выкручивается гораздо легче, чем в случае применения газового баллона.
![]()
Как и в конструкции из газового баллона, потребуется в днище огнетушителя проделать отверстие для засыпки песка. Потом к выполненному отверстию прикрепляется резьбовой фитинг. Для придания устойчивости конструкции рекомендуют приварить к баллону металлические ножки. Этот прием также поможет обеспечить подключение шланга снизу.
Для создания полноценной конструкции потребуется приобрести комплект фитингов и кран. В целом готовая установка будет выглядеть таким образом:
- на выходе из баллона от огнетушителя устанавливается кран;
- с левой стороны выполняется выход, куда будет подключаться компрессор;
- справа подготавливается выход для рукава пескоструя.
Также для создания пескоструйки из огнетушителя потребуется приобрести комплект фитингов и кран
Затем необходимо подключить к аппарату компрессор, а также установить купленный или изготовленный своими руками пистолет для пескоструя. Полученный небольшой прибор считается идеальным вариантом для выполнения мелких работ.
Как установить пескоструй на «Керхер» и другие альтернативные варианты изготовления
Изобретатели, которые любят самостоятельно собирать инструменты из подручных средств или других приборов, предлагают в работе использовать самые различные материалы. Таким образом, им удается изготавливать устройства разных видов, например, пескоструйный пистолет с мешком для сбора песка, позволяющий применять абразив несколько раз подряд, или разнообразные аппараты рециркуляционного типа. При этом зачастую в работе используются приборы, предназначенные совсем для других целей.
Одним из хороших примеров является самодельный пескоструй, изготовленный на основе мойки высокого давления. Чаще всего для работы берется оборудование фирмы «Керхер». В итоге получается собрать беспылевой пескоструйный аппарат, позволяющий эффективно очистить даже сложные загрязнения.
Мойка в процессе работы создает высокое давление воды, при этом актуально, что расход жидкости – минимальный. Для того чтобы получить эффективно работающую беспылевую установку, потребуется собрать пескоструйную насадку на выходную трубу. Помимо этого, понадобятся и другие комплектующие:
Одним из вариантов самодельного пескоструя, является устройство изготовленное на основе мойки высокого давления
- самодельное или керамическое сопло;
- качественный армированный шланг;
- узел для смешивания, можно использовать обыкновенный тройник, главное – выбрать деталь нужно диаметра;
- блок регулировки подачи, который представляет собой цилиндрический дозатор;
- труба для забора песка, дополненная трактом подачи воздуха в закрытую емкость с абразивом.
Готовый пескоструй водяного типа из мойки будет работать по эжекторной системе. В этом случае вода под высоким давлением в процессе быстрого прохождения сквозь блок смешивания создает вакуум в узле подачи абразивного материала. После этого песок вместе с водой выбрасывается под высоким давлением.
Среди особенностей использования подобного прибора можно выделить следующий момент: несмотря на небольшой расход воды, абразив подается очень интенсивно. Это позволяет не только чистить поверхности, но и матировать стекла.
Полезный совет! Чтобы устройство, сделанное из мойки высокого давления, стабильно подавало абразив, нужно использовать мелкий песок равномерной дисперсии. Для бытовых работ подойдет мелкий, просеянный речной песок.
С помощью пескоструя изготовленного из «Керхера»можно не только чистить поверхности, но и матировать стекла
Как сделать инструмент из продувочного пистолета и краскопульта
Другой вариант – пескоструй из продувочного пистолета, отличающийся высокой эффективностью, но при этом небольшими габаритами. Особенно прибор ценится автолюбителями, занимающимися кузовными работами. Для изготовления подготавливают следующие детали:
- продувной пистолет пневматического типа;
- тройник для сантехнических работ;
- шаровый кран, при помощи которого будет регулироваться подача абразива;
- выходное сопло с прижимной гайкой.
В качестве резервуара для абразивного материала подойдет легкий баллон от огнетушителя или даже обыкновенная пластиковая бутылка. После соединения всех деталей прибор подключается к компрессору.
На основе краскопульта также можно изготовить пескоструйный аппарат
Еще один популярный вариант изготовления заключается в использовании в качестве основы краскопульта. Помимо него, следует подготовить и другие элементы:
- рукоятку, оснащенную механизмом подачи воздуха;
- клапан для смешивания, который берется из пистолета-краскопульта;
- емкость для абразива;
- тройник;
- шаровый кран-регулятор.
Начать работу необходимо с проточки пистолета краскопульта, чтобы была возможность использования сопла нужных размеров. После подготовки детали к пистолету подсоединяется тройник для смешивания. В конце крепятся шланги, обеспечивающие поступление и циркуляцию. Пуск подачи абразива осуществляется при помощи кнопки курка. Объема маленького резервуара хватит для очистки небольших деталей или поверхностей на протяжении получаса.
Следуя инструкциям, можно создать мощный пескоструй для масштабных работ или сделать устройство попроще. В этом случае все зависит от навыков и деталей, которые имеются в наличии. Перед выбором конкретной конструкции лучше сразу определиться с фронтом работ, которые планируется решать при помощи прибора.
Прорывной процесс сваривает металл и стекло с помощью сверхбыстрых лазеров
Традиционно сварка ограничивалась материалами со схожими свойствами, поэтому даже алюминий и сталь трудно объединить. Но теперь ученые из Университета Хериот-Ватт заявляют о революционном методе, который может сваривать такие разные материалы, как стекло и металл, благодаря сверхбыстрым лазерным импульсам.
В настоящее время металлы можно приваривать к металлам, а стекло к стеклу, но эти два соединения плохо сочетаются.Для плавления им требуются разные температуры, и они по-разному расширяются в ответ на тепло. Есть и другие методы изготовления, чтобы заставить их склеиваться, но они не такие аккуратные.
«Возможность сваривать стекло и металлы станет огромным шагом вперед в гибкости производства и дизайна», — говорит Дункан Хэнд, директор Центра инновационного производства EPSRC в лазерных производственных процессах, разработавшего новую технологию. «В настоящее время оборудование и изделия, в состав которых входят стекло и металл, часто скрепляются клеями, которые неудобно наносить, а детали могут постепенно сползать или двигаться.Дегазация также представляет собой проблему — органические химические вещества из клея могут постепенно выделяться, что может привести к сокращению срока службы изделия». алюминий, нержавеющая сталь и титан. Ключом к процессу стал инфракрасный лазер, излучающий импульсы в масштабе нескольких пикосекунд – триллионных долей секунды.
«Свариваемые детали находятся в тесном контакте, и фокусируется через оптический материал, чтобы обеспечить очень маленькое и очень интенсивное пятно на границе раздела двух материалов — мы достигли мегаваттной пиковой мощности на площади всего в несколько микрон в поперечнике», — объясняет Хэнд.«Это создает микроплазму, похожую на крошечный шар молнии, внутри материала, окруженного сильно ограниченной областью расплава. сварные швы остались неповрежденными, поэтому мы знаем, что они достаточно прочны, чтобы выдерживать экстремальные условия».
В настоящее время группа работает со специалистами над разработкой прототипа системы лазерной обработки, чтобы метод можно было коммерциализировать для производства.
Источник: Университет Хериот-Ватт
Бутылочное дерево своими руками — C.ПЛОТ
Добро пожаловать на задний двор моих родителей! Да, это бутылочное дерево высотой 10 футов, сделанное из стального круглого стержня разного диаметра в комплекте с цветными бутылками, которые моя мама собрала у друзей и несколько купила в Интернете. Стальной круглый стержень можно купить в местном магазине металлопроката. По словам моего отца, стальной круглый стержень нельзя купить в хозяйственных магазинах с большими ящиками.
Вот несколько фотографий бутылочных деревьев в античном магазине роз, которые я нашел в старом Интернете: просто помещаются на мертвую ветку.
Розы красивые и вкусно пахнут, но в детстве я запомнил магазин антикварных роз бутылочными деревьями, причудливым искусством и изображением арки в горшке.
Откуда появилось бутылочное дерево?
Оказывается, идея бутылочного дерева возникла с тех пор, как были изобретены стеклянные бутылки. Согласно этому сайту, это было в 1600 г. до н.э. в Египте и Месопотамии. Как гласит история, люди верили, что шум ветра в бутылке был звуком духов, запертых внутри.(Помните Аладдина?) Естественно, следующим шагом будет надевание на бутылку крышки, запирающей внутри злых духов, которые, конечно же, уничтожаются светом солнечного дня (кто знал, что вампиры раньше были такими маленькими :). Так люди держали бутылки у своих подъездов, чтобы защитить свой дом от злых духов, так и родилось бутылочное дерево.
На самом деле несколько лет назад я купил маме бутылочную щетку на День матери, думая, что этого будет достаточно для ее фиксации на бутылочной елке. Хотя дерево, которое я ей подарил, не выглядело так…
Оно было примерно 1/20 размера и имело всего 5 веточек.Дерево получило трагический футбольный мяч по голове (веткам) и так и не восстановилось. Моя мама решила, что настоящее дерево не может жить в этом месте, и подумала, что идеально подойдет стальное дерево. (Было несколько разбитых бутылок, но их довольно легко заменить!) Моя семья думает, что наш задний двор — это футбольное поле.
Вот дерево вдохновения моей мамы. Это дерево было создано художницей из Миссисипи по имени Стефани Дуайер.
А вот и красивое дерево из бутылок, сделанное своими руками на нашем заднем дворе…
*Эта кирпичная стена используется как футбольные ворота.Вы можете понять, почему дерево должно быть очень прочным!
Крупный план ее тщательно обработанных ветвей:
Моя мама и ее дерево из бутылок…
Дерево моей мамы около 10 футов в высоту и вмещает 60 бутылок. По ее оценкам, это стоило около 300 долларов за материалы. 150 долларов за металл и 150 долларов за цветные бутылки. Прозрачные и зеленые — это просто старые винные бутылки, которые она собрала у друзей. Вы можете купить винтажные стеклянные бутылки на Amazon по 2,95 доллара за штуку. Вот оранжевая стеклянная бутылка, бирюзовая бутылка и фиолетовая бутылка.300 долларов звучит дорого, но, честно говоря, такое бутылочное дерево трудно даже найти в продаже. У меня есть ощущение, что доставка будет сложной, так как этот присоска не разбирается на части. Вот супер простое дерево из бутылок от Amazon. Он вмещает всего 10 бутылок, но по-прежнему удерживает дух и излучает сияние!
Что вы думаете о бутылочном дереве как о дворовом искусстве? Это, безусловно, добавляет красочный блеск на заднем дворе. На него приятно смотреть, он прочный и это отличный способ переработки использованных винных бутылок! Есть ли у вас дворовое искусство в саду? Вы когда-нибудь задумывались о том, чтобы сделать бутылочное дерево своими руками? Если вы ищете дерево из бутылок своими руками и у вас есть еще вопросы, я буду рад ответить на дополнительные вопросы или, скорее всего, спросить моих родителей… напишите мне по электронной почте craftaway (at) gmail (dot) com.
Ученые только что придумали, как сваривать металл со стеклом, что может революционизировать производство автомобилей , частично стекло/частично металл дворняга цельная.
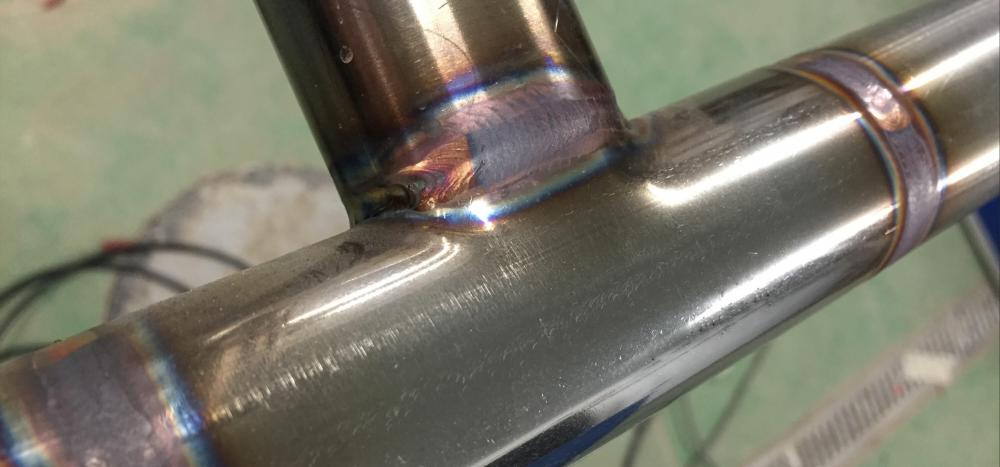
Профессор Дункан П. Хэнд и его исследовательская группа разработали процесс под названием «сверхбыстрая лазерная микросварка», в котором используются очень-очень короткие импульсы инфракрасного лазерного излучения для сплавления двух разнородных материалов. Система Heriot-Watt проверила метод на кварце, боросиликатном стекле, сапфире и алюминии, титане и нержавеющей стали.
Профессор Хэнд описал процесс Phys.org :
«Процесс основан на невероятно коротких импульсах лазера.Эти импульсы длятся всего несколько пикосекунд — пикосекунда в секунду подобна секунде по сравнению с 30 000 лет.
Свариваемые детали располагаются в тесном контакте, а лазер фокусируется через оптический материал, чтобы обеспечить очень маленькое и очень интенсивное пятно на границе раздела двух материалов — мы достигли мегаваттной пиковой мощности на площади всего в несколько микрон в поперечнике.
Это создает микроплазму, похожую на крошечный шар молнии, внутри материала, окруженного сильно замкнутой областью расплава.
Мы проверили сварные швы при температуре от -50°C до 90°C, и сварные швы остались неповрежденными, поэтому мы знаем, что они достаточно прочны, чтобы выдерживать экстремальные условия».
В настоящее время большинство автомобильных стекол удерживается на месте с помощью клея, что усложняет производство и может выделять газ и разрушаться по мере старения автомобиля. Возможность напрямую сваривать панели, скажем, из стекла и алюминия, может открыть множество интересных возможностей для проектирования и производства автомобилей.
Конечно, это также поднимает вопрос о замене: может ли местная кузовная мастерская заменить окно, если одно из них сломается, или потребуется закупать совершенно новую панель с вваренным окном? Будут ли разные скорости теплового расширения проблемой для этих гибридных частей тела?
Я уверен, что для ответа на эти вопросы будут проведены всевозможные тесты, и до запуска в производство еще далеко, но это, безусловно, интересно.
Ранчо Бутылочного дерева Элмера Лонга, Оро-Гранде, Калифорния
Знаки и найденные предметы смешиваются с выброшенными стеклянными бутылками.
Оро-Гранде, Калифорния
Элмер Лонг был изобретательным мастером по изготовлению металлолома. Он заполнил свой передний двор густым лесом бутылочных деревьев. Более 200 деревьев, сделанных из вертикальных металлических труб, ощетинены выброшенными стеклянными бутылками на каждой сваренной ветке. Ранчо Элмера Лонга «Бутылочное дерево» хорошо известно благодаря своему расположению вдоль побережья Ю.S. Маршрут 66, к западу от Барстоу.
Родившийся в 1946 году, Лонг переехал с семьей в калифорнийскую пустыню в 1970 году, где женился, а затем вырастил двух сыновей. Отец Элмера всегда собирал старые бутылки; Элмер унаследовал это сокровище и продолжал пополнять его. По образованию сварщик, Элмер работал на цементном заводе, поэтому у него были навыки, необходимые любому ремесленнику. Свою первую бутылочную елку он возвел в 2000 году. В тот же день Элмер заметил, что путешественники с шоссе 66 съезжают по дороге, чтобы сфотографировать его необычное искусство.
В 2002 году Элмер полностью посвятил себя созданию леса из бутылок, и массив увеличился в плотности и масштабе. Он жил в доме за ним и продолжал расширять и модифицировать ранчо почти до дня своей смерти 22 июня 2019 года. Посетители всегда могли свободно бродить по этому месту, а сзади есть деревянный колодец желаний для пожертвований.
Ранчо Элмера Лонга «Бутылочное дерево» удобно расположено вдоль шоссе 66.
Корпус бомбы среди бутылочных деревьев.
Трубы бутылочного дерева расположены плотно, с достаточным пространством для туристов, чтобы пройти между большинством из них и полюбоваться его работой. Некоторые скульптуры украшены бутылками по цвету, винтажу или бренду. Большинство из них представляют собой бутылки из-под пива или ликера. В некоторых из них установлены стеклянные и керамические изоляторы для опор электропередач.
Элмер также включил предметы потребления — старые металлические игрушки, старые радиоприемники, колесные диски, ручные пишущие машинки, ржавеющие инструменты и приспособления. Некоторые вещи кажутся более продуманными, чем другие.Старый джип с проеденными сиденьями… искусство или полезность?
Это отличная придорожная достопримечательность, бесплатная и открытая (как и большинство мест народного творчества), привлекающая благодарные взгляды. Парковка — это просто широкая немощеная обочина по обеим сторонам этого длинного объездного участка относительно малонаселенного шоссе. Мы припарковались за забором, чтобы можно было беспрепятственно фотографировать. Во время нашего посещения ранчо с бутылочными деревьями прибыла еще дюжина путешественников, все из-за пределов США. Некоторые видели это на YouTube.
Бутылки цветочные на приваренных ветках.
Это очевидный рай для фотографов и селфи. Элмер посыпал старые дорожные знаки, облупившуюся доску меню ресторана A&W и различные артефакты петролианы. На трубе насажена старинная учебная бомба — возможно, заявление о войне или заявление о наличии боеприпасов в высокогорной пустыне, счастливой для летных испытаний.
В ветреный день бутылки издают звуки — приятные или жуткие, в зависимости от вашего вкуса в случайно свистящей музыке из бутылок.Хотя мы не сталкивались с опасностями во время нашего визита, имейте в виду, что бутылки иногда разбиваются, и есть много потертых и ржавых безделушек на уровне голени.
Так что действуйте осторожно, делайте снимки и оставляйте пожертвования!
55 идей для сварочных проектов, которые можно построить для дома или продать
0Последнее обновление
Независимо от того, являетесь ли вы сварщиком-любителем или профессионалом, проекты «сделай сам» могут доставить массу удовольствия. Но еще лучше, когда у вас есть проверенные планы, чтобы вы знали, что ваш труд окупится.
У нас есть список из 55 проектов, как малых, так и больших, от простых до более сложных, предназначенных для использования в помещении и на открытом воздухе. Каждый проект был сделан по крайней мере один раз, но обычно несколько раз. Они снабжены подробными инструкциями и фотографиями, а некоторые содержат видеоролики, демонстрирующие, как именно их выполнять.
Списки разделены на проекты для начинающих и продвинутых. Просмотрите и выберите следующий предмет для изготовления.
Рекомендуется: Щелкните, чтобы увеличить оглавление ниже, чтобы получить полный обзор.
Сварочные проекты для начинающих
1. Проект сварки головоломки в форме подковы
Если вы любите головоломки, эта классическая головоломка в виде подковы — идеальный вариант для вас. Я до сих пор не могу снять это кольцо, но если вы будете следовать инструкциям, это простой проект, и вы можете быть умнее меня и разделить их.
2. Ваза-кашпо в деревенском стиле
Такой простой проект может быть действительно эффективным в нужном месте. Мне нравится деревенский вид, и, учитывая время, необходимое для его изготовления, это был бы отличный выбор для изготовления вашего дома.Инструкции см. здесь.
3. Проект «Сварные портреты»
У каждого есть любимый персонаж или человек, который его вдохновляет, и у вас даже может быть его фотография на стене. Раскройте свои творческие способности с помощью этих инструкций для портретной съемки и воплотите их в жизнь, которую можно сваривать. Невероятно, насколько реалистично они выглядят всего с несколькими сварными швами.
4. Держатель для винных бутылок
Если у вас завалялась старая цепь, очистите от нее свой сарай и превратите в вот такой подстаканник для вина.Он отлично выглядит и очень удобен для надежного удержания бутылки с вином. Как видно из инструкции, это просто сделать, и на это у вас уйдет менее получаса.
5. Угловой стол
Угловые столы — идеальный вариант для использования пространства. Мне нравятся стабилизирующие стержни между концевыми рамами. Это делает его очень прочным и придает ему стильный вид. Прочтите эти инструкции , чтобы изготовить его самостоятельно.
Промежуточные сварочные работы
6.Идея проекта «Светящийся цветок»
Вы можете добавить сияния в свой сад с помощью этой умной ложки . Это простой проект, который будет потрясающе смотреться на вашем заднем дворе. Попробуйте изготовить это для себя.
7. Тележка для хранения дров
Никому не нравится таскать к камину ведра дров. Вместо этого следуйте инструкциям для этого проекта. Он не только служит тележкой; он также может служить вашей внутренней деревянной полкой.
8.Простой набор лестниц
Прочтите эти инструкции, чтобы понять, насколько легко может быть изготовлена лестница. Отображаются только две лестницы , но гладкая компоновка даст потрясающий результат, сколько бы вам ни понадобилось в вашем доме.
9. Подвесные полки
Эта система подвесных полок невероятно прочна и придает современный промышленный вид любому месту, где она установлена. Это простая дизайн, простая в изготовлении и очень эффективная. Я впечатлен.
10.Маленькая садовая шпалера Arc
У вас есть навыки сварки? Дайте своим виноградным лозам место для роста с помощью этой садовой шпалеры. Это базовый дизайн, который выглядит великолепно и обеспечит зону роста, необходимую для разведения ваших лоз.
11. Шпалера в форме домика
Для некоторых крупных лоз, таких как маракуйя или виноград, эта решетка в форме домика станет потрясающим дополнением вашего сада. Это выглядело бы исключительно с покрывающими его виноградными лозами, и это идеальная высота, чтобы обеспечить легкий доступ.Следуйте инструкциям здесь.
Передовые сварочные проекты
12. Увеличенный проект «Атом»
Можете ли вы представить, что их миллион миллиардов в одной пылинке? Невероятный! Попробуйте сварить один из этих гигантов, следуя инструкциям здесь, и вы сможете полюбоваться конструкцией атома в расширенном виде.
13. Микрогорелка для кружек
Надоело, что кофе остывает? Чтобы сделать эту микрогорелку специально для вашей кружки, не требуется много времени.Наслаждаться горячим кофе теперь можно в любое время суток. Просто следуйте этим инструкциям.
14. Тележка сварочная Проект
Это любимый проект каждого нового владельца сварщика. Очень удобно иметь тележку, на которой можно перемещать сварочный аппарат, а не таскать его туда-сюда вручную или с помощью импровизированной тележки, не предназначенной для сварщика. Следуйте инструкциям здесь.
15. Проект сварки стальных розеток
Все мы знаем, как много значит для некоторых людей покупка цветов, но я нахожу это пустой тратой денег, учитывая, как недолго они живут.Создание этой потрясающей розы произведет неизгладимое впечатление, которое не исчезнет, как садовая роза. Если его не подарить, он может стать прекрасным дополнением к вашей каминной полке. Инструкции см. здесь.
16. Creative Log Burner Fireguard
Видеть, как их малыш сжигает себя – худший кошмар для каждого родителя. Следуйте этому дизайну, и у вас будет уникальная самодельная противопожарная защита, которая поможет обезопасить ваших детей. Другая идея состоит в том, чтобы взять эту конструкцию и использовать ее для сварки собачьей клетки.
17. Экран для камина из нержавеющей стали, проект
Взгляните на инструкции для этого экрана для камина, если вы хотите сделать его для себя. Это просто, но имеет привлекательный вид и полезно для защиты вашего камина от проникновения нежелательных рук.
18. Велосипед-тандем
Я мечтал о тандемном велосипеде, и теперь это может стать реальностью благодаря этому самодельному велосипеду. Ознакомьтесь с инструкциями и посмотрите, сможете ли вы создать такую же крутую.Ваша семья и друзья будут в восторге.
19. Багги для картинга
Этот проект выглядит очень забавно. Это может показаться немного большим, чтобы погрузиться в него, но с несколькими подержанными предметами вы будете удивлены, насколько доступно и легко это сделать, если вы будете следовать инструкциям.
Табуреты, скамьи и стулья
20. Простой табурет
Иногда лучше меньше. Простой, чистый дизайн этого табурета позволяет быстро выполнить проект, который окажется прочным и эффективно привлечет любого желающего сесть на него.
21. Конический барный стул
Темно-коричневый и черный всегда хорошо сочетаются друг с другом, особенно в этом барном стуле. В конструкции используются угловые секции для привлекательного внешнего вида, который снижает вес без ущерба для прочности.
22. Подвесной табурет
Эти впечатляющие табуреты могут стать вашими, если вы хотите получить сварку с этим дизайном. Они полностью сделаны из металлолома, который вы можете найти в местной свалке, и на них очень удобно сидеть.
23.
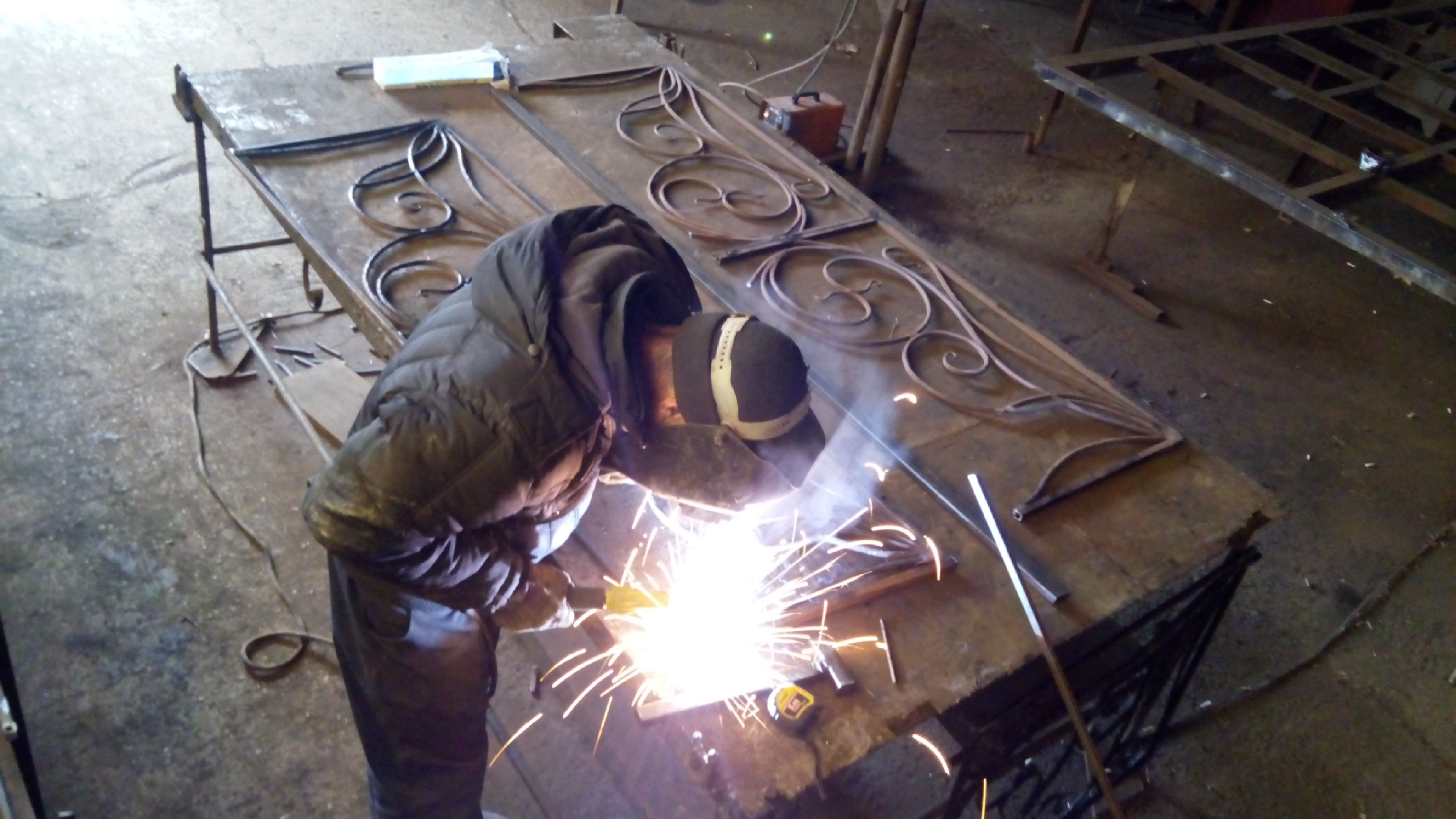
Если вы увлекаетесь искусством или вам нужен предмет интерьера, эта скульптурная скамейка может быть именно тем, что вам нужно. Он уникален, прочен и на удивление прост в изготовлении. Ознакомьтесь с инструкциями здесь.
24. Табурет с регулировкой высоты
В моем местном магазине Pizza Hut они есть во всех магазинах. Они отлично подходят для быстрой адаптации для людей разного роста. Это еще один из наших быстрых сварочных проектов для начинающих с четкими инструкциями, которым нужно следовать, и который оказывается исключительным.
25. Кресло-качалка-гамак
Многим людям нравится отдыхать в гамаке, но влезать в него и выходить из него может быть проблематично, а у некоторых людей просто нет подходящего места в доме, чтобы повесить его. Эта конструкция кресла-качалки, напоминающая гамак, может решить обе проблемы. Его не нужно вешать, и он качается, чтобы помочь вам включиться и выключиться.
26. Стильный табурет
Обычно, если на скамеечке для ног меньше одной ноги, это портит ее назначение. На этот раз его прочность остается неизменной, в то время как он имеет уникальный внешний вид, который будет выделяться в комнате.Прочтите инструкции , чтобы изготовить его самостоятельно.
Столы и письменные столы
27. Набор столов с парными блоками
Иногда здорово иметь дополнительные столики или табуреты у дивана, когда к вам приходят друзья, но зачастую такой проблемой может стать пространство. Этот продуманный дизайн позволяет аккуратно вставить один стол под другой, а также добавить пару дополнительных столов или табуретов. Это блестящая идея.
28. Журнальный столик
Столы могут стоить целое состояние, если у вас есть дети.Этот журнальный столик из поддонов недорог и выдержит большинство брошенных на него вещей. Даже следы от горячих кружек только добавляли бы деревенского вида. Ознакомьтесь с инструкциями здесь.
29. Современный уличный стол
Конструкция этого стола намного проще, чем кажется. Если вам нравится мебель современной формы с теплым земным видом, это был бы идеальный вариант для вас, чтобы попробовать .
30. Уникальный квадратный журнальный столик
Эти кофейные столики невероятно просты по своему дизайну, но создают потрясающий вид, который создает иллюзию большего пространства в вашей гостиной, обеспечивая при этом достаточно места для стола.Попробуйте этот сварочный проект для начинающих и дайте нам знать, что из этого получилось.
31. Полный обеденный стол
Вам нужен новый полный столовый набор? Если вы хотите создать что-то потрясающее без особых затрат, ознакомьтесь с этими инструкциями , чтобы воплотить этот стол в жизнь у себя дома. Вы можете создать четыре одноместных стула или две скамейки для сидения, если вам не нравится смешанный вариант.
32. Стол-тройник
Если вам нужно серьезное место на столе или вы хотите заполнить пустую часть вашего дома или рабочего места, этот стол-ти подойдет. В инструкциях показано, насколько он прочен, но это простой проект.
Освещение
33. Потрясающий уличный свет
Это один из моих любимых дизайнов в списке, который мы составили. Это просто сделать, но создает эффектный вид, который вы можете повесить на свой собственный дом. Попробуйте сами.
34. Звездный свет
Будь то Рождество или вы ищете световое украшение для своего дома, этот звездный свет — блестящий проект.Привнесите немного творчества в свой дом с таким проектом ручной работы, как этот, без необходимости придумывать дизайн. Просто следуйте этим инструкциям.
35. Дерево со свечами
Это как рождественская елка, только лучше. Он имеет простой минималистский вид с естественным сиянием огня и не оставляет следов елочных иголок на ковре. Ознакомьтесь с дизайном здесь.
36. Шарик и цепь
Кто в последнее время причинял тебе боль? Следуйте этим инструкциям для решения вашей проблемы. Это не самый тяжелый мяч, который можно таскать с собой, но он преподаст любому урок, если он будет прикручен к ним на один день. (Мы, конечно, шутим, но из этого получился бы интересный арт-объект.)
Декор
37. Гигантский паук
Я не фанат пауков, но этот размером с крышу впечатляет. С несколькими изгибами, несколькими сварными швами и старым шаром для боулинга за 5 долларов из местного секонд-хэнда вы можете установить его и на крыше. Ознакомьтесь с дизайнами здесь.
38. Многоножка
Не знаю, что страшнее, паук или эти многоножки.В любом случае, дизайнер проделал отличную работу, и вы можете следовать его инструкциям, чтобы сделать что-то для себя.
39. Многоугольная чаша из нержавеющей стали
Нужна ваза для фруктов или декоративный элемент для скамейки? Этот проект получится превосходным, если у вас есть доступ к пластине из нержавеющей стали. Здорово приступить к такому умному проекту, как этот, когда кто-то проделал всю тяжелую работу за вас и придумал дизайн, а при наличии правильных инструментов и поддержки это может стать хорошим сварочным проектом для начинающих.
40. Ваза из нержавеющей стали
Эта ваза, похожая на многоугольную чашу выше, имеет впечатляющий дизайн, который дополнит любые добавленные к ней цветы, но при этом будет великолепно смотреться как самостоятельный предмет. Прочтите инструкции , чтобы сделать это для вашего следующего предприятия.
41. Ваза для улицы
Эта напольная ваза сделана из клетчатой пластины, которая выглядит потрясающе, но вариант из нержавеющей стали также был бы отличным вариантом. Выберите свой любимый материал и приступайте к сварке с помощью этих инструкций.
42. Букет цветов
Вы изо всех сил пытаетесь найти идеи подарков для особенного человека в вашей жизни? Или, может быть, вы слишком заняты в мастерской, чтобы пойти и купить что-нибудь? Какой бы ни была проблема, решите ее с помощью этого креативного цветочного дизайна. Им понравится красноречивая конструкция, и они не будут возражать против того, что вы проведете несколько часов в мастерской, чтобы закончить ее.
43. Биплан из нержавеющей стали
Мне нравится конечный результат биплана. Несмотря на то, что в инструкциях это заканчивается краской, я обожаю чистую отделку из нержавеющей стали и лично протравлю/отполирую ее и оставлю как есть.Независимо от того, как вы хотели бы закончить, прочитайте инструкции и гордитесь тем, что приобрели этот шедевр для себя.
Ямы для костра и печи
44. Дровяная печь
Я люблю эту маленькую красавицу. Он небольшой, но с длинным дымоходом, который отводит дым и одновременно создает достаточно тепла, чтобы согреться холодным утром. Он идеально подходит для нагревания чайника или приготовления пищи на плите. Следуйте этим инструкциям, чтобы изготовить его самостоятельно.
45.Дровяная печь для пиццы
Кто не любит свежую пиццу, приготовленную на дровах? Немного доработав два старых танка и немного металлолома, вы можете получить свой собственный. Следуйте этим инструкциям, чтобы узнать, как это сделать.
46. Мангал треугольный проект
Эта жаровня немного меньше, чем та, что выше, но имеет элегантную отделку и не занимает слишком много места. Ознакомьтесь с дизайном, чтобы начать сборку, и сообщите нам, как все прошло, в разделе комментариев ниже.
47.Яма для костра
В каждом доме должно быть место для костра для вечеринок на свежем воздухе и семейных посиделок. В этом дизайне достаточно места, чтобы разжечь здоровенный огонь. Следуйте этим простым инструкциям, чтобы сделать его для себя, и ваша семья и друзья будут счастливы.
48. Коптильня
Большинство людей любят копченое мясо. Получите собственное копчение с помощью этих инструкций, и вы сможете наслаждаться копчением любимой пищи в любое время. Он также отводит тепло зимой, что является дополнительным бонусом.
49. Турбинная пожарная яма
Дизайн этой ямы для костра невероятен. Если вы хотите попробовать это для своего следующего проекта, прочтите эти инструкции и создайте атмосферу для следующей зимней вечеринки. С помощью нескольких модификаций конструктор усовершенствовал турбину, чтобы она вращалась без тушения пожара.
Мебель и дом
50. Угловой диван
Стоимость приличного секционного дивана в розничном магазине астрономическая.Если у вас есть сварочный аппарат с несколькими кусками стали, вы можете сделать эту простую основу, чтобы создать свою собственную экономичную версию купленных в магазине. Вы можете найти все, что вам нужно, чтобы построить его в этих инструкциях.
51. Душ из нержавеющей стали
Если вам нравятся душевые кабины из нержавеющей стали, но вы хотите получить удовольствие от изготовления собственного душа с минимальными затратами, взгляните на этот дизайн, чтобы изготовить его самостоятельно. Инструкции предназначены для завершения всего душа.
52. Беседка
Если вы готовы к более серьезному испытанию, инструкции к этой Беседке превратят картину в реальность на вашем участке. Это не работа одного человека, но с помощью друга или двух, это будет на одном дыхании.
53. Перила из нержавеющей стали
Если вам нужны блестящие перила для вашего проекта, прочтите эти инструкции – это простое руководство к фантастическому результату. В этом примере мне нравится полированная отделка, но вы можете оставить ее с любой отделкой, которая лучше всего подходит для вашего дома.
54. Дверца из нержавеющей стали
Эта дверь впечатляет своими сварочными работами и представляет собой продвинутый сварочный проект. Вы можете использовать сварку TIG, MIG или дуговую сварку, но следуйте этим инструкциям, и результат будет аналогичен этому примеру.
55. Перегородка из стали и стекла
Это еще один крупный проект, если вы любите игру. Я видел такие перегородки раньше, и они всегда мне нравились. Такой простой, но подробный набор инструкций заставляет меня попробовать это сделать самому.
Заключительные мысли
Спасибо, что прочитали наш список из 55 проектов по сварке своими руками. С небольшим количеством онлайн-руководств, подобных этому, вы можете быть уверены в том, что сможете создавать удивительные творения в пределах собственного дома.
Дайте нам знать ваши комментарии ниже, особенно если вам понравилось создавать некоторые из этих замечательных проектов. Мы хотели бы услышать от вас.
Если вас интересует бизнес-аспект сварки, мы рекомендуем прочитать нашу статью «Руководство по открытию сварочного бизнеса» и наш пост «6 идей подработки для сварщиков»
Избранное изображение предоставлено: BonNontawat, Shutterstock
Газовая сварка — обзор
16.3.1.12 Газовая сварка и резка
Газовая сварка осуществляется пламенем, образующимся при сжигании примерно равных объемов кислорода и ацетилена, подаваемых при равных давлениях из газовых баллонов к сварочной горелке. Температура пламени составляет примерно 3100°C, что достаточно для плавления стали и других металлов. Присадочный металл, если требуется, добавляется путем ручной подачи стержня в переднюю кромку сварочной ванны при перемещении горелки вдоль стыка. Продукты горения обеспечивают достаточную защиту от атмосферы при сварке стали.При сварке других металлов, таких как чугун, нержавеющая сталь, алюминиевые и медные сплавы, флюсы используются для очистки и защиты металла от окисления.
Оборудование Сварочная горелка имеет две ручки управления с накаткой, которые регулируют расход кислорода и ацетилена таким образом, чтобы получить нейтральное или слегка окисляющее или восстановительное пламя, в зависимости от применения. Горелка имеет ввинчиваемое сопло из набора сопел с отверстиями разного диаметра, которые производят пламя соответствующего размера и, следовательно, необходимое тепловложение для свариваемого металла и толщины.Шланги кислорода и топливного газа подсоединяются между сварочной горелкой и газовыми баллонами, газы проходят через пламегасители и регуляторы давления. Пламегасители представляют собой предохранительные устройства, которые предотвращают попадание пламени обратно в цилиндры в случае обратного воспламенения. Для использования в мастерских газовые баллоны обычно устанавливаются попарно на тележке, которую можно перемещать в нужное место.
Присадочный металл и флюсы Химический состав присадочного металла указан в BS 1453: 1972 и включает ферритные стали, чугун, аустенитные нержавеющие стали, медь и медные сплавы и алюминиевые сплавы.Ферритные стали не требуют использования флюса, но для других материалов доступны собственные флюсы.
Области применения Газовая сварка используется в основном для ремонта и технического обслуживания, особенно при ремонте кузовов автомобилей и сельскохозяйственных орудий, хотя она постепенно заменяется небольшим оборудованием для сварки TIG и MIG. Газовая сварка в определенной степени используется для работы с листовым металлом (т. е. для нагревательных и вентиляционных каналов) и до сих пор используется для выполнения корневых проходов в трубах, где она особенно полезна для перекрытия зазоров.
Два применения, где газовая сварка имеет явные преимущества перед другими процессами, это сварка и ремонт отливок из серого чугуна и наплавка дорогими сплавами. Отливки из серого чугуна можно успешно сваривать при использовании высоких температур предварительного нагрева до 600°C и газовой сварки с чугунными присадочными прутками. Наплавка дорогостоящих износостойких сплавов, таких как кобальт-хром-вольфрамовые сплавы или сплавы на основе карбидов хрома или вольфрама, может осуществляться с минимальным плавлением основного металла, так что разжижение наплавляемого сплава и последующее снижение исключается износостойкость.Газовая сварка также успешно применяется в ювелирном деле с помощью миниатюрных горелок и небольших газовых баллонов.
Ацетилен является единственным горючим газом, подходящим для газовой сварки из-за его благоприятных характеристик пламени как при высокой температуре, так и при высокой скорости распространения. Другие горючие газы, такие как пропан, пропилен или природный газ, дают недостаточно тепла для сварки, но используются для резки, пайки и пайки. Они также используются для правки пламенем деформированных деталей и для предварительного нагрева перед сваркой и последующего нагрева после сварки.
Газовая резка Газовая резка, иногда называемая газопламенной или кислородной резкой, включает активное экзотермическое окисление разрезаемой стали, когда материал предварительно нагревается кислородно-топливным газовым пламенем до температуры воспламенения около 900°С. С. Оборудование для газовой резки такое же, как и для сварки, за исключением того, что требуется специальное режущее сопло. Сопло имеет наружное кольцо отверстий, через которые подается подогревающая газовая смесь, и центральное отверстие, через которое поступает струя кислорода.Экзотермическая реакция окисления стали образует жидкий шлак оксида железа и через несколько секунд, в зависимости от толщины металла, происходит прошивка. Оксид железа и расплавленный металл вытесняются из реза потоком кислорода. Движение резака по заготовке обеспечивает непрерывное резание, и резаком можно управлять вручную или с помощью моторизованной каретки. Таким способом можно резать сталь толщиной до 300 мм.
Стойкие к окислению стали, такие как нержавеющая сталь, можно резать специальными методами, включая введение железного порошка или других запатентованных порошков в поток кислорода.Эти порошки реагируют с тугоплавкими оксидами хрома и снижают их температуру плавления и повышают их текучесть, что позволяет проводить резку. Для получения дополнительной информации см. ссылку 40.
Нержавеющие стали, цветные металлы и сплавы обычно режут с помощью процесса плазменной резки, который не зависит от экзотермической реакции.
Возможна ручная газовая резка, а точность резки можно повысить за счет использования небольшого колеса, установленного на резаке.Колесо может быть свободно вращающимся или моторизованным. Для общей резки и профилирования (включая резку фасок на кромках листа) обычно используется механизированная резка. Для механизированной резки широко распространены электронные устройства слежения, состоящие из фотоэлемента, который повторяет контур чертежа и направляет режущее сопло с помощью приводных двигателей, которые регулируют движение каретки и траверсы, к которой прикреплена горелка.
Имеются машины для резки с числовым программным управлением, которые используют программы, хранящиеся или перфорированные на магнитной ленте, которые посылают соответствующие сигналы на приводные двигатели.
Основные термины сварки
Ниже приведены мои нетехнические определения для некоторых
Основные сварочные термины. Они хороши для домашних любителей и тех, кто только собирается
в сварочное поле. Большинство людей не хотят садиться и изучать всю сварку.
словарный запас, и я их не виню, я тоже. Но если ты выучишь это,
вы будете на голову выше большинства новичков.
Щелкните здесь, чтобы просмотреть наши сварочные печи и перейти к
узнайте о преимуществах правильного хранения расходных материалов для сварки!
Arc Blow — это дуга ходить везде, где вы НЕ хотите, чтобы это идти.Это происходит только в DC, бывает много сваривается в угол и, как полагают, каким-то образом вызвано магнетизмом. Иногда помогает переместить рабочий зажим в другое положение на стали.
Дуга Резка — может выполняться стержнем 6010 или 6011 на повернутой машине. до «деформации 10». (очень жарко) Можно использовать и другие стержни, но эти два лучший. Это место, где вы прорезаете сталь, используя силу дуги. Это не самый красивый разрез, но сойдет в крайнем случае, когда у вас нет факела.
Дуга Строжка — резка стали или металла дугой из углеродистой стали. электрод. Электрод представляет собой твердый углерод, обернутый в медь для обеспечения проводимости. То Стингер имеет сжатый воздух, и при нажатии кнопки он выбрасывает воздух на расплавленный режется металл. Машина повернута на «деформацию 10», что означает, что вы используют МНОГО ампер (тепло).
Например, когда мы пошли в работа, где 5 резервуаров из нержавеющей стали высотой около 10 этажей имели почти каждый сварной шов завалил рентген.Мы выдолбили сварной шов снаружи, а затем приварили их заново. Мы затем выдолбили сварные швы внутри и снова приварили к нашему предыдущему сварному шву.
Толстый нержавеющая сталь не может быть разрезана факелом, и даже если бы это было возможно, жара заставила бы его деформация. Дуговая строжка концентрирует тепло в месте разреза.
Сплав — элемент, добавляемый к металлу. Примером может служить мягкая сталь с хромом (сопротивление ржавчина) и никель (делает его менее восприимчивым к окислению, то есть ржавчине), который делает форму из нержавеющей стали.(наиболее распространенная нержавеющая сталь 304)
Чередование Текущий — реверсирует вперед и назад от положительного к отрицательному по синусоиде. волна. Это приводит к нестабильности дуги в большинстве сварочных процессов, поэтому постоянный ток является предпочтительным.
Сила тока — измеряет ток и то же самое, что ток, который является вашим теплом.
Дуга — это то, что между конец электрода и основной металл. Сопротивление вызывает нагрев.
Автоматический Сварка — это сварка, выполняемая оборудованием типа роботов.
Резервное копирование Полоса — полоса или отрезок стали, соединенные встык до открытого зазора между два куска стали. Сварочные электроды 6010 можно использовать для открытой стыковой сварки, но 7018 не может и требует подложки для обеспечения поверхности для электрода. приварить к. Некоторые резервные полосы отрезаются, а некоторые остаются на месте.
Бусина — осажденный присадочный металл на рабочей поверхности и в ней, когда проволока или электрод расплавляется и вплавляется в сталь.Стрингерная бусина представляет собой узкую бусину, имеющую только тянущее движение или легкое колебание, в то время как бусина плетения шире и больше колебание.
Скос — угол, срезанный или отшлифованный на краю заготовки чтобы обеспечить большее проникновение для более прочного сварного шва.
Взорванный — что ты будет, если сварить или порезать емкости с дымом. ЗАПРЕЩАЕТСЯ сваривать или резать какие-либо контейнер, если он не новый или вы не знаете, что он был очищен и сертифицирован по безопасности! Контейнеры могут быть токсичными, легковоспламеняющимися или взрывоопасными.
Щетка — сталь ручная щетка с проволочной щетиной, дисковая щетка для ручной шлифовальной машины, чашечная щетка для ручной шлифовальной машины, или дисковая щетка для настольной шлифовальной машины. Они используются для очистки прокатной окалины, окисления, грязь, масло и т.п. со стальных поверхностей. Чистота имеет первостепенное значение на обрабатываемую деталь, чтобы убедиться в отсутствии дефектов сварки. Важно использовать нержавеющую стальная щетка и щетка из мягкой стали правильно.
Наплавка — строительство
поверхность стальной детали, такой как зубья звездочки, поверхность
направляющее колесо (удерживает гусеницу на месте на гусеничных транспортных средствах, таких как бульдозеры
или краны), или ковш на фронтальный погрузчик.В большинстве случаев это намного дешевле
иметь сварщика построить компонент, чем это было бы заменить часть. Наращивать
сварные швы обычно выполняются электродами с твердой поверхностью.
Это тоже хороший способ
для нового студента-сварщика, чтобы научиться правильному повторному запуску и врезке.
Разоренный Out — непрохождение испытания сварных швов из-за дефектов сварных швов. «Он разорил на своих тестовых пластинах и не был принят на работу.»
Стык — просто то, что он sez ‘… две части столкнулись друг с другом.Только верх и Нижняя поверхность может быть сварена. Без хорошего проплавления этот шов не имеет прочность многопроходного углового шва или скошенного шва.
Крышка — последний валик разделочного шва, он может быть выполнен с переплетением движений вперед и назад, или со стрингерами, связанными друг с другом.
А также то, что вам нужно надеть на голову при вертикальной сварке МиГ или любом другом процессе над головой, чтобы не допустить появления горячих искр с головы. (см. Кассинг.) Головные уборы сварщика имеют небольшой козырек и такие высокие им нужен световой сигнал, чтобы самолеты не врезались в них. Это так их можно поворачивать и натягивать на ухо при сварке трубы и головы наклонен. Вы ДАЖЕ не хотите, чтобы капля расплавленного металла попала вам в ухо! Ты можно буквально услышать, как он шипит, когда вы страдаете от ожога. Сварочные шапочки могут Выиграйте любой конкурс уродливых шляп со всеми сумасшедшими точками польки, пейсли и другими сумасшедшими конструкции.
Кардинальный грех сварки — см. подрезку.
Коалесценция — ах, это когда из металла или стали сплавляется (соединяется) кузнечик.
С покрытием Электрод — это флюс на присадочном металле сварочного прутка. Они использовали использовать голые стержни только в горизонтальном положении. Кто-то заметил, что ржавый стержень работал лучше, чем новый, поэтому они начали экспериментировать с разными покрытия на разных стержнях. Они обнаружили, что некоторые покрытия производят экранирование. газ, который защищал сварочную ванну от загрязнений в атмосфере.Загрязнители вызвать пористость и продольное растрескивание. Сварочная ванна защищает сварной шов был гладким и прочным и мог использоваться в разных положениях, а не только плоский. Я могу только представить, сколько раз эти голые стержни застревали!
Вогнутость — Это когда валик углового сварного шва провисает внутрь от поверхности корня к основанию.
Расходный материал
Вставка — это место, где присадочная проволока или стержень находится в зазоре, и вы ввариваете его в зазор.
основной металл вместе с проволокой или стержнем.Он становится единым целым со сварным кузнечиком.
Выпуклость — это когда валик углового сварного шва выступает наружу от корня
к лицу.
Угловое соединение — одно из пяти основных сварных соединений. Это Это когда края двух пластин соприкасаются друг с другом под углом 90 градусов. Это обычно обеспечивает канавку для заполнения, обеспечивающую хорошее проникновение.
Защитное стекло или накладка — линзы из прозрачного стекла или пластика в капюшоне или защитных очках предохраняющий линзу №5 (для резки) или №10,11,12 (для сварки) от попадания брызгать на них.Хватает, черт возьми, я должен, когда студент забывает вставить это когда они меняют объектив. Затем они свариваются с ним, и брызги разрушают # стекло, которое недешево! Вы должны часто менять накладки, так как они ограничивают вид, когда они забрызганы или поцарапаны.
Трещина — Где сварной шов трескается или распадается. Хорошим примером может служить сварка чугуна. Если он не подвергается правильному предварительному и последующему нагреву или если используется неправильный электрод, это треснет БОЛЬШОЕ ВРЕМЯ.Иногда трещина проходит прямо перед сварным швом. бассейны во время сварки.
Вы должны предварительно нагреть, нагреть и запустить чугунный стержень, который имеет содержание никеля. Уловка, чтобы предотвратить распространение трещины, состоит в том, чтобы сверлить отверстие до и после трещины, которую вы собираетесь сварить. Запустите сварку, а затем заполнить отверстия. Отверстия препятствуют распространению трещины.
Кратер — В конце сварного шва вы прожигаете сталь без нанесения наполнителя. металла, который оставляет углубление в основном металле.Выполняя перезагрузку, вы хотите чтобы начать в конце трещины, приварите обратно к тому месту, где сварной шов остановился, а затем двигайтесь в том же направлении, в котором вы сваривали. Это предварительно нагревает и дает хорошую врезку в шарик, который вы только что положили.
Критическая температура — Это когда основной металл переходит из солидуса в ликвидус, когда вы нагреваете его во время сварочный процесс. Именно в тот момент, когда он превращается из сплошной массы, таять и становиться жидким.Это отличный термин для обсуждения на коктейле. вечеринка, чтобы вы выглядели умнее, ОСОБЕННО, если ваша аудитория мало что знает о сварка!
Ток — В электрической цепи протекает ток электричества. То, что вы свариваете, сопротивляется потоку и образует тепло. AMPS являются измерением вашего тока. Чтобы получить немного больше технических характеристик, ток отрицательный. заряженные электроны, проходящие через проводник, которым обычно является проволока.
Цилиндр р — В чем мы храним кислород и ацетилен для резки и ЗАЩИТНЫЙ ГАЗ для Сварочные процессы MIG и TIG.Они бывают разных размеров, и вы хотите исследовать перед покупкой. Если вы получите слишком мало одного, вы очень устанете пополнять это все время.
Дефект — Что-то не так со сваркой. Основными дефектами являются продольные трещины, пористость, шлаковые включения и «кардинальные трещины». Грех сварки… Подрез.
Глубина плавления — Насколько глубоко ваш присадочный металл проникает в металл с поверхности.
Постоянный ток — Сварка постоянным током — это самая гладкая сварка, дающая наименьшее количество брызг.То
ток течет в одну сторону, от минуса к плюсу. (от катода к аноду)
Это
похоже на то, когда вы включаете водяной шланг, и вода вытекает. С постоянным током
ток ВСЕГДА течет в одном направлении. Однако вы можете изменить свой сварочный
приводит к изменению полярности.
Электрод постоянного тока отрицательный — электричество вытекающий из сварочного стержня или проволоки рассеивается в заготовке, поэтому дает меньшее проникновение. Около 1/3 тепла приходится на конец стержня и 2/3 на заготовке.Это то, что вы хотите использовать для тонких металлов.
Прямой Токовый электрод положительный — электричество, протекающее В сварочный стержень или проволоку и, следовательно, больше нагревается на конце стержня или проволоки. Это дает вам 2/3 тепла на стержне и 1/3 на заготовке, что дает большее проникновение для толстых металлы, потому что сила дуги проникает в сталь перед нанесением присадочного металла.
Пластичность — Металл гнется и остается согнутым, не ломаясь.
Рабочий цикл — Это то, как долго машина может работать за десятиминутный период времени, прежде чем он перегревается.
10% = 1 минута из каждых 10.
20% = 2 минуты из каждых 10.
Включено до 100%, что будет работать все время без остановки.
Для
машина на фабрике или строительной площадке, вам нужен 100% рабочий цикл.
Для
ваша хобби-мастерская, вы можете обойтись 20 или 30%.
Даже в самых загруженных Фабрика через десять минут будет нерабочее время.Если вы свариваете электроды, вы можете бежать чуть больше минуты. Тогда ты поднимешь капюшон, проверь что делают все остальные, подумай о том, что ты собираешься делать этой ночью, сколоть шлак, почистить сварной шов, проверить который час, поменять стержни и НАКОНЕЦ вернуться к сварке.
Краевое соединение — Внешний край двух пластин встык на 90 градусов параллельно друг другу.
Подготовка кромок — До при сварке кромки листа или трубы необходимо обеспечить прочный сварной шов.Это может быть вырезан факелом или скошен, обработан шлифовальным станком, напильником или всеми тремя способами.
Электрод — Электроды бывают либо покрытые флюсом, либо просто голые провода. В поле Электрод называется «стержень» при электродуговой сварке и «проволока» при Дуговая сварка MIG и порошковой проволокой.
Существует МНОГО различных типов электродов.
В Использовались голые стержни времен Второй мировой войны, которые можно было использовать только в горизонтальном положении. Это было ОЧЕНЬ легко втыкать эти стержни, и я могу только представить, как это должно быть неприятно приходилось ими пользоваться.Однажды парень заметил, что ржавый прут, который он подобрал, приварился. лучше новых.
Эксперименты с различными типами покрытий как кремний и калий, было установлено, что флюс на стержне не только помогает он горит лучше, но производит защитный газ, защищающий сварочную ванну от атмосфера.
Держатель электрода — Ручной зажим, удерживающий сварочный стержень и проводит электричество из стержня в ОТРИЦАТЕЛЬНОМ ЭЛЕКТРОДЕ ПОСТОЯННОГО ТОКА, или в стержень в ПОЛОЖИТЕЛЬНОМ ПОЛОЖИТЕЛЬНОМ ЭЛЕКТРОДЕ ПОСТОЯННОГО ТОКА.
Лицо — На пластине или сварки труб есть КОРНЕВОЙ ПРОХОД, ГОРЯЧИЙ ПРОХОД, ЗАПОЛНИТЕЛЬНЫЙ ПРОХОД и ЗАКРЫТИЕ. Корень проникает через заднюю часть пластины, колпачок находится на поверхности, которую вы сварка, которая является лицом.
Вентилятор : Сварочные аппараты имеют вентилятор для охлаждения машины и предотвращения ее перегрева. (см. РАБОЧИЙ ЦИКЛ) Некоторые вентиляторы работают постоянно, в то время как другие работают «по требованию», что означает, что при необходимости и отключается, когда не требуется.
(Хорошо бы продуть выключайте сварочный аппарат сжатым воздухом не реже одного раза в месяц. Это держит пыли от скопления пыли и возможного нарушения работы внутренних электрических систем. Все машины имеют вентиляционные отверстия, и каждое отверстие необходимо продуть.)
Черные металлы Металл . Железо получают из руды, добываемой на Земле. Смотри как Сталь сделана. Черный означает, что металл представляет собой железо или железо со сплавами.
Наполнитель Металл — это металл, добавляемый в сварочную ванну.Сварку можно делать как с присадочный металл. Тонкий металл иногда сваривают, расплавляя два основных металла. вместе.
Внезапный ожог — Это ожог от производимого излучения от УЛЬТРАФИОЛЕТОВЫХ лучей сварочной дуги. Он может сжечь кожу подобно к солнечным ожогам и даже к волдырям на роговице. Вы не понимаете этого до нескольких часов спустя когда тебе кажется, что кто-то трет тебе в глаза горячий песок.
Два моих студенты слишком близко прижались друг к другу, и я сказал им двигаться, но они сказали, что у них все в порядке.Да что я знаю? Я только делал это 30 чертовски лет по сравнению с их тремя-четырьмя месяцами!
Хорошо, в ту ночь они были в отделении неотложной помощи получают мазь для глаз и хорошее отделение неотложной помощи за 300 долларов законопроект.
Вы никогда не должны находиться там, где можно увидеть свет сварочной дуги без защитные линзы, даже если они находятся сбоку от ваших глаз. В моем магазине мы громко объявляем «СЛЕДИТЕ ЗА ГЛАЗАМИ!» прежде чем зажечь дугу, чтобы предупредить тебе закрыть глаза.
Угловой сварной шов — король сварных швов, потому что он используется во многих приложениях, в основном используется на тройниках. . (См. СОЕДИНЕНИЯ.)
Два куски металла, соединенные встык под углом 90 градусов, валик проходит наполовину каждый кусок. В зависимости от толщины может понадобиться одна бусинка или несколько бусинок. ПРИВЯЗАННЫЕ друг к другу.
Угловой сварной шов — Поверхность или верхняя часть сварка.
Угловой сварной шов — От пересечения стыка до конец сварки.Для каждой тарелки будет ножка.
Угловой сварной шов Toe — это конец сварного шва на конце ноги. Опять будет один за каждую тарелку.
Корень углового сварного шва — Место начала сварного шва на пересечении соединяемых плит.
Угловой сварной шов — Расстояние от корень к лицу.
Приведенные выше определения УГЛОВОЙ СВАРКИ см. в Miller’s Tig.
Страница сварки для хорошей иллюстрации…
http://www.millerwelds.com/education/TIGhandbook/pdf/TIGBook_Chpt7.pdf
Поток Измеритель — Давление в баллоне с ЗАЩИТНЫМ ГАЗОМ может достигать 2400 фунтов. за дюйм. Расходомер снижает его до рабочего давления, обычно от 20 до 25 кубов в час.
Флюс :
Очищает поверхность и при сжигании
образует ЗАЩИТНЫЙ ГАЗ, который защищает сварочную ванну или ванну от атмосферных воздействий.
загрязнения, вызывающие ДЕФЕКТЫ.
Дуговая сварка порошковой проволокой (FCAW) — Длинная тонкая плоская полоса проходит через серию штампов, пока не начнет скручиваться. По сторонам.Затем добавляется FLUX, и он проходит через штампы, пока не будет свернутый в трубчатую проволоку.
Аналогичен СТАЛЬНОЙ ПРОВОЛОКЕ, в рулонах и используется аналогично MIG, обычно устанавливается на ОТРИЦАТЕЛЬНЫЙ ОТРИЦАТЕЛЬНЫЙ ЭЛЕКТРОД ПОСТОЯННОГО ТОКА. Когда проволока расплавляется, чтобы стать ПРИПОЛНИТЕЛЬНЫМ МЕТАЛЛОМ, ФЛЮС горит и образует ЗАЩИТНЫЙ ГАЗ.
Следовательно, не требуется ЗАЩИТНЫЙ ГАЗ, поэтому его можно использовать в местах со сквозняком или даже на ветру, в отличие от его двоюродного брата МИГ.
Испытание на свободный изгиб — Также называется управляемым изгибом тест, это разрушительный тест.Купон вырезается из контрольной пластины, сварной шов шлифуется, затем купон (обычно шириной 1 ½ дюйма и длиной 7 дюймов) сгибается в ДЖИГ. Затем производится ВИЗУАЛЬНЫЙ ОСМОТР на наличие трещин и дефектов.
Это
является одним из способов демонстрации КВАЛИФИКАЦИИ для получения сертификата. Сварка – это одно
одной из самых требовательных профессий, потому что сварщик всегда должен показать свою квалификацию.
У меня 30 лет стажа работы в цехе, профсоюзе металлургов, образование,
но если бы я пошел на работу, скажем, в электростанцию, к сварщику,
поле всего пару лет, я бы еще сдать тест с ними!
Критически требовательные рабочие места требуют квалификации РЕНТГЕНОВСКОГО ИЗЛУЧЕНИЯ, которые являются неразрушающими, но показывают все!
Дым — Являетесь ли вы опытным МАСТЕРОМ или НОВИЧКОМ, вы всегда должны быть осторожны с парами при резке и сварке.
Из ОЦИНКОВАННЫХ пары цинка, вызывающие тошноту, до более опасного газа фосгена, который может выделяться от УФ-ЛУЧЕЙ вокруг некоторых чистящих растворов ДЫМ может быть опасным!
Всегда убедитесь, что у вас есть надлежащая вентиляция, особенно в закрытых помещениях!
Предохранитель — Если вы покупаете сварочный аппарат для использования дома, убедитесь, что у вас есть предохранитель, чтобы все не сгорело. В старых домах убедитесь, что проводка были обновлены, иначе вы можете вызвать пожар, если они перегреются.
Фьюжн — Как сказано в СЛИЯНИИ, слияние — это плавление и становление единым с основой. металл или ОСНОВНОЙ МЕТАЛЛ вы свариваете кузнечика.
Это тоже слово за то, что доктор хочет сделать с моей лодыжкой, которую я сломал, когда упал с трех рассказы. Хочет взять кусок моей бедренной кости и присоединить к лодыжке. Беда то есть бедро заживает дольше, чем чертова лодыжка! Итак… этот маленький операции не будет.Черт, мне все равно больно, только когда я не сплю!
Оцинкованный — Электрохимический процесс, при котором низкоуглеродистая сталь погружается в жидкий цинк для
сделать его антикоррозийным. Я был удивлен, узнав, что это делается уже 150 лет!
Когда
вы свариваете оцинкованную сталь, вы должны сначала прожечь цинковое покрытие, а затем
он производит ДЫМ, который может вызвать у вас тошноту, как будто вас ударили кулаком в
кишки.
Употребление молока до, во время и после сварки должно помочь, но
надлежащая вентиляция и не дышать им вообще лучше всего.
Газометаллическая дуга Сварка (GMAW) — см. «MIG»
Газовая дуговая сварка вольфрамом — см. «TIG»
Сварка разделкой — Когда требуется очень прочный сварной шов, например, когда две колонны соединены вместе в высотном здании, важно чтобы получить максимальное проникновение и сплавление. Это делается путем разрезания фаски, чтобы что вы можете сваривать твердое тело от КОРНЯ до ПОВЕРХНОСТИ ОСНОВНОГО МЕТАЛЛА.
Тепло
Затронутая зона — то, что многие сварщики не учитывают, но должны.В любой момент
вы свариваете металл или сталь, вы нагреваете область рядом со сварным швом. После этого
то нагревается, то остывает с разной скоростью в зависимости от температуры в цехе
или поле.
На стройках зимой это может быть очень быстро.
Как нагрев, так и охлаждение могут влиять на свойства в зависимости от того, какое основание
металл, который вы свариваете.
Зона термического влияния на низкоуглеродистой стали обычно
ничего страшного. Однако, если вы свариваете, например, чугун без должного
предварительный нагрев и последующий нагрев он треснет прямо на глазах.
Инвертор — Относительно новый, я впервые услышал о них около 13 лет назад. Источник питания для сварочные аппараты, которые намного эффективнее обычных трансформаторов машины используют, а значит, гораздо меньшие единицы.
Когда я впервые начал сваривать тридцать лет назад в магазине черного железа я использовал сварочный аппарат, похожий на большой атомная бомба с ящиком наверху. Он был не менее четырех футов в ширину, два фута в глубину и около метра в высоту.
Сегодня у них есть машины, которые могут все
что можно было бы, плюс некоторые, и они размером с небольшой чемодан, что намного
удобнее для магазина и поля.
Железные рабочие — Там здесь несколько значений. Первый — это союз, в котором я тоже принадлежу, Международный Ассоциация мостовых, строительных, декоративных и арматурных рабочих. В виде Название предполагает, что мы работаем над конструкциями, от высотных офисных башен до к плотинам, электростанциям и т. д.После 3-летнего стажировки я стал структурным сварщик. Есть и другие банды (бригады), такие как Raising Gang, Plumb Gang, Bolt-up. Банда и Разная банда. Хотя я работал над ними всеми, я потратил большую часть мое время в различных сварочных бригадах, поскольку сварка — моя настоящая любовь!
Это это также термин для машины, как ОГРОМНОЙ, так и достаточно маленькой, чтобы быть портативной на рабочих местах. Он может резать металл, резать углы и пробивать отверстия. Ты собираешься инвестировать минимум около пары тысяч для модели меньшего размера.даже не хочу думать, сколько стоят большие.
Прерывистая сварка: Очень распространенный ошибка при сварке — сварка слишком много! Многие сварщики, особенно новичок в торговле, полагаю, что «чем больше сварной шов, тем лучше он будет держаться». ЭТО НЕ ПРАВДА! Много раз один или два дюйма сварного шва каждые пару дюймов будет держаться так же хорошо, как сплошной шов.
На большинстве работ, будь то в магазине или поле, сварные швы будут на чертеже, так что вы будете знать, что именно сделать.Инженеры определяют, какой тип сварки лучше всего подходит для данного соединения.
Существует два типа прерывистых сварных швов. приведу пример из завод по производству черного чугуна, на котором я когда-то работал:
1) «Цепь» На ширина в двадцать футов, мы бы нашли центр, скажем, в десяти футах. Мы бы отметили два дюймов, по одному дюйму с каждой стороны от центра. Затем от центра этого сварного шва мы делали отметку в двенадцати дюймах. На этой отметке мы измерили бы один дюйм на каждом боковая сторона.Таким образом, мы измеряли от центра к центру на каждом сварном шве. В большинстве конструкций, почти все измеряется от центра.
По ту сторону луч, мы бы отразили метки первой стороны.
Очевидно, концы луч не будет выходить в правильной последовательности, поэтому было важно убедиться, что и поместите два дюйма на каждый конец, даже если он был рядом с другими двумя дюймами отметки, которые мы сделали.
2) «Стаггард» После нанесения меток на один стороны луча, мы бы поместили другую сторону между метками на первом боковая сторона.
Эти сварные швы достаточно прочны, чтобы их удерживать, и сваривать их слишком сложно. эти суставы прочные. Когда слишком усердные сварщики переваривают сварку, они несколькими способами…
- Они нагревают основной металл, который может измениться его свойства отрицательно.
- Они тратят лишнее время. В магазине и поле «Время — ДЕНЬГИ!»
- Они тратят материалы впустую, используя
стержни, которые стоят все больше и больше с каждым годом.
приспособление — приспособление удерживайте металл или сталь, над которой вы работаете, на месте во время изготовления.Они может быть стальным, зажатым тисками или С-образным зажимом, болтами, приваренными к столу, или очень сложные рамки. Позиционеры в крупных производственных цехах удерживают заготовку, вращают, вращаться или вращаться, чтобы можно было выполнять сварку в плоском или горизонтальном положении.
Соединение — Пересечение, где встречаются две разные секции ОСНОВНОГО МЕТАЛЛА. Быть в списке под СВАРОЧНЫМИ СОЕДИНЕНИЯМИ. На электростанции они спрашивали, сколько соединений мы сварили каждый день.
Было много разных типов, таких как балка к балке, балка к колонне, х брекеты и т.д.Хотя это не был точный отчет, он заставил бригадира представление о том, что делается.
Отличная глава о СУСТАВАХ принадлежит Миллеру
Tighandbook…
http://www.millerwelds.com/education/TIGhandbook/pdf/TIGBook_Chpt7.pdf
Замочная скважина — При сварке открытых стыковых швов или швов с открытым разделочным швом с помощью STICK, MIG или TIG, откроется «замочная скважина». Когда стороны тарелки сгорают на каждом На стороне СВАРОЧНОЙ БАССЕЙНА образуется отверстие, обеспечивающее хорошее СОЕДИНЕНИЕ и ПРОНИКНОВЕНИЕ.
Замочная скважина не должна быть слишком большой, иначе СВАРОЧНАЯ БАССЕЙН водопад из задней части сустава.
Если замочная скважина становится слишком большой, остановите сварки немедленно, дайте пластине остыть и выполните надлежащую регулировку, чтобы исправить проблема. (Слишком много тепла, неправильный угол наклона удилища или слишком долгое пребывание в луже. может быть причиной.)
Профсоюзы — хороший сайт со списком профсоюзов
http://www.trcp.org/unions.aspx.
В
мой опыт работы металлургом, я бы сказал, что у вас больше всего шансов сварить
в следующем…
Котельщики
Железо Рабочие
Трубомонтажники
Трубопроводчики
Листовой металл
Рабочие
Лиды — Это линии от машины к чему вы свариваете те, которые несут ток. Они представляют собой множество медных проводов, вплетенных в один для проведения электричества, затем покрытый непроводящей резиной или пластиком сворачивать.
Важно убедиться, что на проводах нет разрывов или разрывов. обнажение оголенного провода, который может вызвать искрение на заземленной поверхности. Помимо шока или опасность возгорания, было бы особенно плохо, если бы он вошел в контакт с находящимся под давлением газовый баллон!
Liquidis — Слово, которое заставляет вас казаться умным, когда вы означает самую низкую температуру, при которой сталь или металл находятся в жидком состоянии. Угадайте, что такое «твердое» называется? (См. SMART TALK)
Машинная сварка — Оборудование работает сварной шов, пока человек наблюдает, чтобы убедиться, что он работает правильно.Они также будут визуальный осмотр завершенного сварного шва. Будь то робототехника или машинная сварка, большинство компаний предпочитают тех, кто действительно занимался сваркой в полевых условиях, потому что они «чувствовать» это.
Сварщики-подмастерья действительно могут почувствовать приварить TIE-IN к стали. Когда я ПРОВОДЯ СВАРКУ С 7018, я буквально чувствую стержень немного поддается, когда он срастается со сталью.
Руководство Сварка — Сварку выполняет человек.В SMAW (палке) держат ЖАЛО и манипулирование СВАРОЧНЫМ ЭЛЕКТРОДОМ для управления СВАРОЧНОЙ БАССЕЙНОМ. В MIG они используют провод подачи пушки Mig, чтобы сделать то же самое. В TIG они используют горелку и ручную подачу присадочной проволоки.
Скорость плавления — Сколько стержня (электрода), проволоки или стержня TIG расплавляется за определенное время.
Точка плавления — А-а-а, кузнечик, вот куда уходит металл
от SOLIDUS к LIQUIDUS.См. УМНЫЙ РАЗГОВОР.
MIG (GMAW или газовый металл Дуговая сварка) — Технически это может называться GMAW, но в цеху и в полевых условиях все, что я когда-либо слышал, было Mig.
Для сварки MIG используется сплошная стальная проволока, скрученная на катушке и пропускается через сварочный провод с вкладышем в нем. Водители толкают, тянут или и то, и другое для подачи проволоки через провод к СВАРОЧНОМУ ПИСТОЛЕТУ.
Используется несколько различные смеси, но чаще всего я использовал чистый углекислый газ, или смесь инертного газа аргона и СО2 (обычно 75/25.75% аргона, 25% CO2) для защиты сварочной лужи от атмосферы.
Страница 2 — Основные условия сварки
.Это Список условий сварки предоставлен Keen Ovens, лидером в области хранения сварочных материалов. печи.
Добавить комментарий