Художественная ковка металла своими руками картинки
Автор perminoviv На чтение 4 мин Просмотров 58 Опубликовано
Красивые и качественные кованые изделия всегда вызывают восторг и немалый интерес. В последнее время, все больше и больше людей хотят овладеть огненным делом.
Мастера такой древней профессии – кузнецы.
Обучится кузнечному ремеслу возможно разными способами. А после, можно обустроить в гараже или сарае место для ковки металла и разбавлять дизайн жилья коваными предметами своими руками.
В интернете, или книгах можно найти различные фото элементов ковки металла или уже готовых изделий, которые можно использовать за основу.
Про кузнецов
Занимается таким искусством кузнец художественной ковки – специально обученный мастер по обрабатыванию металла с целью создания различных красивых изделий для дома.
Это могут быть подсвечники, дизайнерские украшения, перила лестниц, ворота, двери и многое другое.
Каждый кузнец должен уметь делать:
- Сварку,
- Ковку,
- Литье,
- Термическую обработку.
Также, мастер должен знать свойства обработки металла, режимы нагревания стали, технику безопасности, методы обработки металла.
У многих возникает вопрос, какой человек наиболее подходит для такой работы? Конечно, сильный человек с хорошим зрением, способностью переносить высокие температуры, трудоголик и стойкий к физическим нагрузкам.
Мастер должен владеть фантазией и желанием делать долговечные предметы. Многие находят музу при просмотрах ковки металла в картинках или видеозаписях.
Учтите, многие кузнецы сталкиваются с заболеваниями спины, поскольку много времени проводят в наклонном положении.
Важность профессии
Как и любая другая профессия, кузнечное ремесло появилось много-много лет назад и сразу заняло место одной из важнейших профессий.
Такие мастера ценились в хозяйстве и в искусстве.
Разумеется, что на сегодняшний день значимость такого мастера не так высока, поскольку изготавливать металлические изделия может не только кузнец. Однако, различные декоративные предметы – элементы декора – могут быть выполнены только руками.
Кузнечному ремеслу можно обучиться многими способами и встретить такого мастера можно в каждом регионе страны, ведь кто, как не он, разбавит обыденность в обстановке дома?
Кузнецы, должны создавать уникальные вещи, чтобы добавлять дому уюта и утонченности. При этом, не обязательно заполнять коваными изделиями весь дом – нужен небольшой штрих, который и станет «изюминкой».
Чуть ниже представлен процесс художественной ковки металла своими руками в картинках.
С древних времен каждый кузнец владел своими секретами обработки металлов.
В наши дни можно использовать стандартные методы работы с металлическими материалами в небольших мастерских или цехах.
Многие мастера при работе с предметами прибегают к сварке металлов.
Для сварки металла лучше всего иметь спецодежду, а также другие средства защиты.
Ковка по металлу, фото показывающее как можно сделать кованые ворота для частного дома.
При помощи сварки можно также сделать небольшие элементы на изделии.
На фото видно мастера в работе, который при помощи сварки работает с металлом.
Холодная ковка металла, фото изображающее уже созданные по заготовках детали.
Кованые изделия-результаты
Картинки ковки металлов показывают только мастеров в работе с большими предметами, а ниже предоставлены фотографии уже готовых уникальных предметов для украшения домов.
Металлические розы всегда пользуются популярностью среди людей, желающих поставить кованое изделие у себя в жилье.
Довольно часто можно встретить своего рода навесные декорации, используемые в качестве украшений или дополнений на кованые решетки к дверям, окнам или оградам.
Немаловажную роль в доме играют и кованые подсвечники – своего рода символы достатка хозяина.
Уникальные подсвечники для дома, выполнены мастером своего дела.
Такой небольшой паучок внесет в ваш дом эффект уникальности.
Уникальные кованые вставки способны разнообразить любой интерьер.
Иногда кованые украшения, можно использовать и в «других» целях.
Кованые ворота всегда считались украшением для особняков богатых людей – в наше время доступны каждому желающему.
Металлические фонари – непростое украшение для дома, которое радует глаз вечерами.
Часто, что в старинных домах, что в современных постройках можно увидеть фонари выполнены из металла, как символ роскоши и долговечности.
Особой популярностью пользуются подставки для цветов в виде велосипедов.
Птицы-украшения из металла, подходят в абсолютно любой сад.
Вот такое простое кованое украшение можно сделать своими руками.
Картинки ковки металла многим помогают найти что-то новое, что могло бы в будущем украсить их дом, а многих подталкивают к изучению такого ремесла.
ООО Аэлита
Мастеркая художественной ковки
Компания ООО «Аэлита» имеет огромный опыт в любых работах, связанных с художественной ковкой и сваркой металла.
Мы занимаемся производством и монтажом высококачественных металлоконструкций от простых сварных и кованых эксклюзивных: навесов, козырьков, металлических ворот, заборов и ограждений, лестниц и много другое. Большой опыт позволяет нам в кратчайшие сроки выполнять задачи по производству металлических конструкций.
Наша мастерская занимается изготовлением кованых изделий любой сложности, как по вашему эскизу так и по разработанному нашими художниками: кованые цветы, предметы интерьера, декоративные мостики и беседки, ограждения балконов и лестниц, заборы, ворота и калитки, козырьки и навесы, дымники и флюгеры, и многое другое.
Изделие художественной ковки можно выбрать из каталога готовых работ или создать индивидуальный разработанный эскиз. Кованые решетки, ворота, заборы, калитки служат красивой защитой Вашего дома. Наша кузня использует технологии изготовления ручной горячей и холодной ковки.
Инструмент и оборудование на нашем производстве:
Основные устройства, применяемые в художественных мастерских — это горн и наковальня. В качестве оснастки выступает ручник, а при крупных работах применяется кувалда. Для держания раскалённого металла применяются наборы клещей — серийные и специальные. Последние изготавливаются кузнецом-художником самостоятельно.
При художественной ковке необходимы зубила, бородки, подбойки, а также скруглённые молотки. В качестве дополнительного инструмента применяются оправки, обжимки, наконечники, шпераки и подсечки, а также плиты — пробойные, формовальные, правильные и гвоздильные. Для операций по холодной обработке металла используются инструменты для чеканки, разгонки, рифления и зернения, а для тонкой работы — напильники, резцы, шаберы и штампы.
Операции применяемые в художественной мастерской:
• Высадка.
• Протяжка.
• Скругление граней.
• Продевание.
• Оформление уступов.
• Гибка.
• Пробивка.
• Рубка.
• Скручивание-торсирование. Плоский, торсированный или круглый прут скручивается в спираль. Скручивание производится в холодном или нагретом состоянии — в зависимости от толщины стержня.
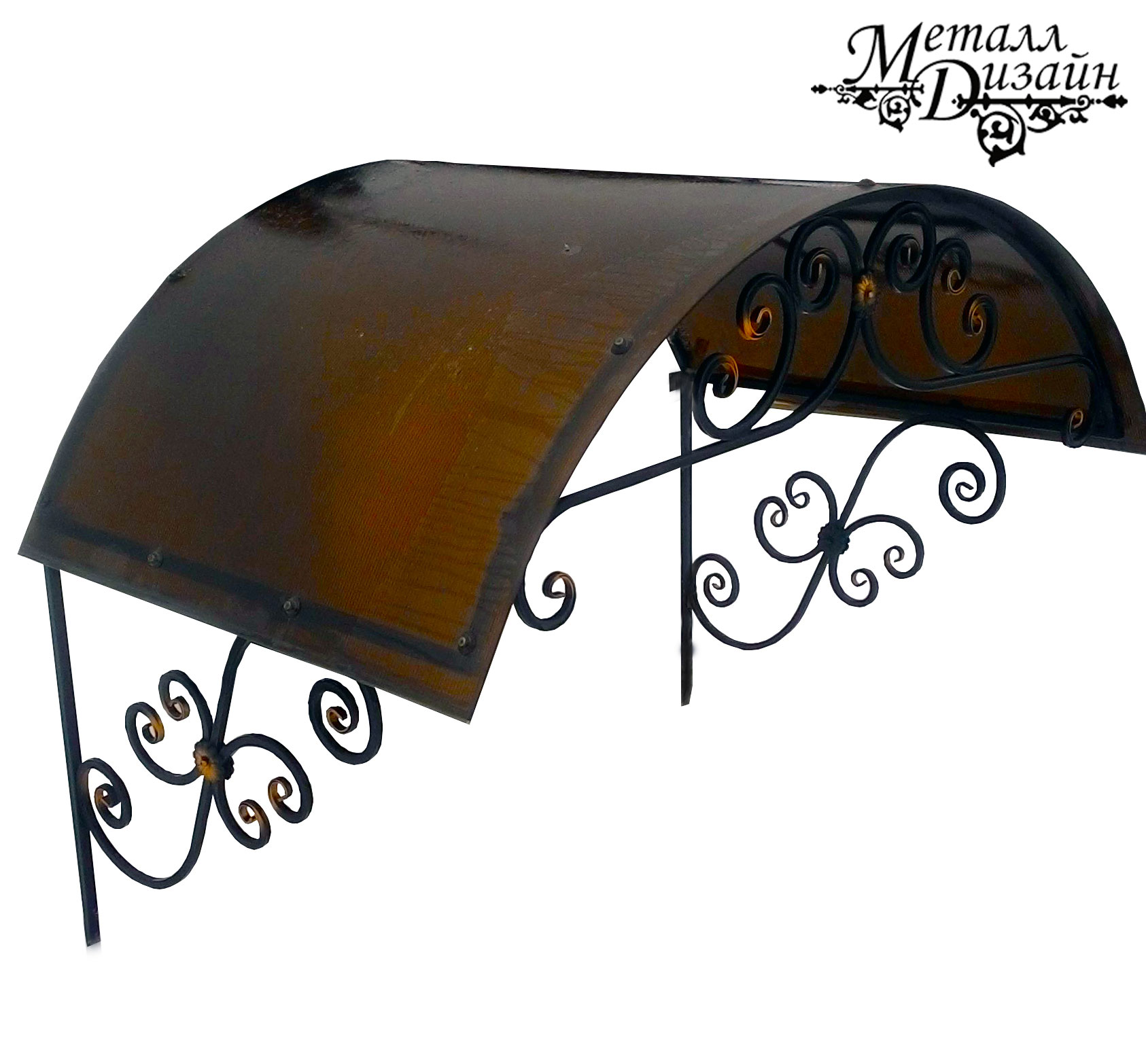
• Шишки. Проволока свёртывается в спираль — в форме шишки.
• Волюты-спирали.
• Свёртка колец. Заготовка свёртывается в кольцо необходимого диаметра. Свёртывание производится в холодном или нагретом состоянии — в зависимости от толщины заготовки.
• Пересечение внахлёст.
• Рассекание материала.
• Скобы.
• Чеканка.
Благодаря слаженному коллективу, наша мастерская кузница способна выполнять большие объемы авторских работ по художественной ковке.
Мы можем изготовить не только сварные и кованые изделия из нашего каталога, но и любые изделия по Вашему индивидуальному заказу. Наши работы представлены в разделе портфолио.
Всё то что представлено на сайте это малая часть того что мы можем сделать для Вас. Выезд мастера на замеры в любое удобное для Вас время.
Если вы решили заказать ворота, ограждения, металлическую лестницу или заказать индивидуальное художественное изделие обращайтесь по телефонам: +7 (812) 915-56-32, 915-56-23
Кованые изделия в Тюмени — художественная ковка: фото, цены, каталог
Вас привлекает художественная ковка в Тюмени? Мечтаете приобщиться к массивному и утонченному искусству, дополнив интерьер или экстерьер своего дома виртуозно выполненными шедеврами из металла? Обратитесь к нам.
Виды ковки
В своей работе мы используем различные методы придания металлу художественного вида. При этом наши кованые изделия приобретают тот шарм, который присущ только ковке вручную – технологии наших предков, надежность и востребованность которой доказана веками. Кузнецы компании «Сибирь» в зависимости от заказа создают изделия методом горячей и холодной ковки.
Горячая ковка
Горячая ковка представляет собой технологию обработки разогретого металла с помощью набора ручных кузнечных инструментов или пресса. Вы не получите типовое изделие – только эксклюзивное, выполненное мастером вручную. Его индивидуальность будет ограничена только полетом фантазии кузнеца и вашей дизайнерской идеей.
Холодная ковка
Холодная ковка – это современный вид обработки металла без нагревания. Конечно, такой способ не даст возможности получить уникальное изделие. Он идеально подходит для экономичных кованых изделий, которые не требуют эксклюзива. Плюсами такого метода можно назвать то, что заказ мастера компании «Сибирь» выполнят быстро и по доступной цене.
Применение художественной ковки
Придайте интерьеру своего дома или квартиры изысканность и представительность, аристократизм и утонченность! У нас вы можете заказать кованые изделия, подходящие к общему дизайну помещения. Оригинальная мебель, люстры, эксклюзивные статуэтки и многое другое способны украсить любое пространство. Стили их выполнения и ассортимент настолько разнообразны, что оригинальные композиции из металла займут достойное место в вашем доме.
Если вы владелец частной усадьбы, тогда непременным ее атрибутом могут стать ворота, лестницы, беседки, заборы и ограждения выполненные нашими мастерами. Мы уверенно гарантируем качество, надежность и долговечность наших изделий, которые станут гармоничным украшением вашего участка.
Стоимость кованых изделий
Цена на наши услуги по ковке изделий зависит от многих факторов:
- Сложности и объема работы;
- Эксклюзивности заказа;
- Количества и характеристик используемого материала.
В любом случае, наша цена на изделия из металла конкурентоспособна и доступна.
Если вы решили заказать художественную ковку в Тюмени или купить готовые кованые элементы, свяжитесь с нами. Специалисты компании «Сибирь» обязательно помогут воплотить в жизнь любые ваши дизайнерские идеи.
Изделия холодной ковки из стали, художественная ковка на заказ
Изделия художественной ковки, фото.
Артикул И-31.
>>Ещё предметы интерьера
Изделия холодной ковки из стали
Кованые изделия изготавливаются двумя принципиально разными методами — горячей или холодной ковкой. Исторически

Однако в дальнейшем, благодаря достижениям технического прогресса, были сконструированы и созданы станки для так называемой холодной ковки, то есть для штамповки стальных изделий без нагревания. Этот метод позволяет получать
Художественная ковка — искусство очень широкого диапазона не в последнюю очередь благодаря сочетанию возможностей, которые предоставляет холодная ковка, с возможностями ковки горячей. Конечно, сегодня, как и в Средневековье, для создания красивых кованых изделий одного только оборудования, даже очень современного, недостаточно. Он кузнецов по-прежнему требуются высокий эстетический вкус, орлиный глазомер, незаурядное мастерство и большой опыт.
Интерьер. Люстры. Ковка.
Артикул И-15.
Мы относимся к числу компаний, кузницы которых работают только по индивидуальным заказам — притом, что изделия холодной ковки (фото на странице) в принципе могут производиться нами и серийно на продажу. Соответствующая аппаратура у нас имеется. Но мы принципиально создаём только те вещи, что нужны именно Вам и именно сейчас. Всё только индивидуально и только под заказ. То же самое, и даже в большей степени, относится к горячей ковке — здесь всё индивидуализировано на 100%. Изделий с одинаковым дизайном мы не создаём. Если только речь не идёт о нескольких изделиях из одного заказа. Но и тут полного совпадения быть не может по определению.
Заказанная нам ковка из стали выполняется только нами, без перепоручения изготовления даже малой части изделия иным кузнечным цехам и компаниям. Тем более, что, если Вас интересует кованая сталь, ковка любых изделий из этого материала может быть выполнена нами быстро и без проблем благодаря наличию достаточного числа кузнецов и техническому оснащению кузниц.
Это будут прочные изделия, весьма надёжно защищённые от коррозии тщательной грунтовкой и составами, не допускающими появления ржавчины. Они будут служить Вам, создавая вокруг эстетику и комфорт, очень долго — при номинальной гарантии от нас сроком 5 лет.
Тема страницы: изделия холодной ковки из стали, художественная ковка на заказ.
Художественная ковка на заказ в Курске с доставкой, фото, цена
Художественная ковка металла, декоративная ковка в Курске — древнейшее кузнечное искусство, которое высоко ценится и в наши дни. Сочетание красоты, удобства и долговечности всегда актуальны. Художественная ковка преобразит любой интерьер, придаст ему аристократичность, изысканность, утончённость, индивидуальность и характерность. Профиль работы нашей кузнечной мастерской в Курске — эксклюзивные кованые изделия, выполненные вручную, по эскизами и индивидуальным проектам. Многовековой опыт и традиции искусства, дополненные научными достижениями практически не ограничивают возможности ассортимента и дизайна кованых изделий. Всевозможные стили и дизайн интерьера могут быть воплощены в жизнь мастерами кузнечного дела в нашей мастерской художественной ковки в Курске. Благодаря всему этому сегодня у Вас есть отличная возможность получить неповторимый и благородный стиль всего интерьера.
Обычно такой текст можно прочитать на сайте любой кузнечной мастерской. Плюс демонстрация дипломов с выставок, где их раздают всем, кто арендовал хотя бы 3м2 для своих изделий.
На самом деле за последние лет 20 художественная ковка резко продвинулась вперед. Если смотреть на работы 20-летней давности, которые в то время казались высшим пилотажем кузнечного мастерства с применением «секретов художественной ковки», то сейчас они уже вызывают некое недоумение из-за качества обработки металла, неаккуратности и тд. Появились металлические производства с набором оборудования, литых и штампованных элементов из Китая, которые делают те же кованые ворота просто на заглядение. Причем большая часть кузнечных завитков, волют уже делается на холодную на специальных прессах и они более аккуратные и одинаковые, чем из под рук кузнеца, ковавшего их на горячую. Такой вид сборки назвали «холодной ковкой». Нет никаких «высокохудожественных ударов по наковальне» и ручной работы. Все секреты прописаны в книгах и выложены в интернете. Уже никому не нужны вручную сделанные подковы и гвозди. Клиентам нужны красивые кованные ворота, калитки в Курске , которые не обязательно должны разговаривать и стоить по 50 тыс долларов за штуку, нужны красивые кованые решетки, через которые не смотришь, как из клетки. Нужен каминный кованый набор, чтобы он был красивый и им можно было пользоваться по назначению. И не важно, каким способом это сделано. Главное, чтобы было красиво и доступно по цене. Наш основной клиент — средний класс. Это не значит, что мы не можем сделать кованные изделия нереальной красоты и сложности — можем. Каждую нашу работу мы можем сделать еще лучше и красивее. Но художественная ковка не может быть дешевой.
Мы делаем ровно настолько красиво и качественно, насколько готов заплатить клиент. Когда вам говорит сварщик, что он у себя в гараже сделает ТАКИЕ же кованные ворота или мангал, или кованый козырек но в 2 раза дешевле, чем наша мастерская художественной ковки в Курске на Трикотажке на ул. Энергетиков, 2 — не верьте, что они будут ТАКИЕ ЖЕ. Вы заплатите деньги, потом будете долго ждать свой заказ, потом будете сильно разочарованы полученным результатом, если вообще его получите.
Художественная ковка не может быть дешевой и стоить ниже себестоимости металла, кокса и электроэнергии, необходимой для того, чтобы сделать ваш заказ. Самое главное, что хочет видеть заказчик в конечном изделии художественной ковки — это вещь «как не у всех» за адекватные деньги. Но эта вещь не должна быть корявой (хотя и встречаются заказчики, которые просят сделать по-грубее, но их единицы), с огромными кляксами сварки, плохо покрашенная. Та же кованная беседка и лестница из нашей мастерской будет аккуратной, металл обработан «как яичко», узоры реально одинаковы и ровно лежащие по плоскости и качественно покрашена кузнечной краской на выбор. А если еще доплатить, то вы можете получить в нашей мастерской изделие, на котором просто не найдете ни одного сварочного шва, оно будет как литое. Именно поэтому мы имеем высококлассных специалистов по обработке металла и , главное, оборудование, которое позволяет сделать кованные изделия в Курске любой сложности и качества по запросу клиента и в соответствии с оплатой за это изделие. Нельзя сейчас сделать хорошие изделия без мощного электрического молота, дорогих сварочных аппаратов, все возможных станков и приспособлений для прессования и изменения металла.
Мы можем сделать кованый столик или скамейку, которые сами полетят в космос и поразят своей красотой инопланетян, но нужно понимать, что они и стоить будут как крыло Боинга. Но мы можем сделать и по-проще, но это тоже будет красиво, но наповал уже поразить жену или соседей не получится. Мы можем повторить любой рисунок или фото из интернета, можем разработать сами и даже прорисовать эскиз на компьютере. Мы общаемся с клиентами, позволяем им самим проявить творчество. Объясняем что можем, а что пусть сделает дядя Вася в гараже, но переделывать за ним мы не будем.
И еще нужно понимать, что хоршие и дорогие кованные изделия не делаются быстро. Сложно предугадать точный срок исполнения, как правило он удлиняется от планированного и чем качественнее и сложнее должны быть кованные ворота и калитка, тем срок исполнения дольше. Кузнецы и сборщики — прежде всего люди, которые могут болеть, получить травму (это частое явление), уставать, а заменить их некем. Хороших мастеров осталось мало, так как художественная ковка , например, в нашем регионе — это уже реально роскошь и многие мастерские умирают, а вместе с ними уходят на покой и мастера, а учеников не было. А в ковке, конечно, и талант очень важен, и знания работы с металлом.
Вот так без пафоса мы постарались кратко объяснить вам что такое художественная ковка в Курске, Москве, Белгороде, Воронеже, Орле и других городах. И про свою мастерскую. Если Вы еще хотите изделия из художественной ковки — тогда милости просим. Вы получите кованное изделие своей мечты или по своим финансовым возможностям. Но оно будет ваше и радовать вас и вашу собаку, которой будет очень приятно выходить на прогулку не просто в калитку из профлиста, а в настоящую кованную красивую калитку. Кстати для нее (для собаки) мы можем сделать отличный кованный вольер или хотя бы будку. У нее же тоже есть мечта про комфортабельное жилье.
Кстати , заодно дадим ответ на вопрос — почему кованый фонарь, или кованый почтовый ящик или красивый кованый каминный набор стоят так дорого, там же металла очень мало. Да потому, что сделать такое изделие по сложности и по времени сродни изготовлению тех же кованных ворот. Времени и усилий кузнеца нужно вряд ли гораздо меньше. Маленькое кованое изделие не всегда легче сделать, чем стандартные кованые качели или кованую лестницу.
И еще один практический совет заказчику художественной ковки в Курске или Москве. Начните немного интересоваться художественной ковкой до того, как вы решили её заказать для своего дома. Просмотрите большее количество работ в картинках, эскизах и готовых декоративных изделий из металла в фотографиях. Смотреть фотогалереи на сайтах — это очень полезно для развития собственного кругозора и единственный способ найти что-то такое, что вам понравится или хотя бы интересную идею, концепцию. Узнайте по фотографиям, какая художественная ковка бывает, какие варианты, образцы, как уже решались другими людьми задачи похожие на ваши. Вы ведь не первый человек которому нужно сделать хорошую лестницу, красивые перила, беседку, балкон, забор, ворота, крыльцо или навес возле дома. И тогда беседа с нашими специалистами не будет выглядет на уровне — «хочу что-то как не у всех». Нам нужно понимать, от чего будет отталкиваться. Попытайтесь получить, пусть поверхностное, но как можно более широкое представление. Какое направление в дизайне, какой стиль ковки вам вообще нравится. Поговорите с архитекторами и дизайнерами и сделайте наоборот. Шутка, но с долей правды. У архитекторов свои предрассудки и свои тараканы — лучше не идти в их кильватере.
Гребите к своему берегу. Ковка в Курске вообще и наш сайт поможем вам в этом. Ведь не зря же мы размещаем все эти красивые фотографии на нашем сайте ковки. Это не только наши работы, но и то, что нам самим нравится в работах других и мы можем повторить эти работы или взять за основу идею. Мы не делаем художественную ковку «как для себя» мы ее сделаем так, чтобы она понравилась вам. За это вы и платите нам деньги.
Мы делаем любые изделия из металла любой сложности в сегменте художественной ковки, а так же и не кованные металлические изделия. Гаражные ворота, металлические лестницы, навесы. Все это представлено в соотвествующих разделах сайта.
Вы можете заказать любые изделия художественной ковки в нашей мастерской.
Изделия холодной ковки в Екатеринбурге, цена, фото
Холодная ковка представляет собой процесс изготовления изделий без нагревания металла. Нужная форма получается в результате механической обработки. Причем такие изделия намного прочнее и надежнее тех, что изготовлены путем литья или штамповки.
Холодная ковка может быть нескольких видов:
- Осадка – производство под высоким давлением. Это позволяет создать элементы, которые будут широкими и невысокими.
- Протяжка – нагревание металлического элемента и обработка его молотком.
- Прошивка – проделывание отверстий в изделии.
- Штамповка – изменение формы или размера заготовок.
- Прессование – увеличивается плотность металла и изменяется его форма.
- Волочение – позволяет получить разные варианты изделия: трубы, проволоку и т.п.
- Прокатка – деформация элементов, которая происходит путем трения об них специальными валиками.
Таким способом создают изделия холодной ковки:
- Решетки для окон или дверей в жилых помещениях;
- Декоративные украшения фасада: перила, козырьки и прочее;
- Детали для заборов, ворот и других ограждений;
- Части мебели: ножки, подлокотники и др.;
- Декор: подставки, кронштейны, решетки и др.
Холодная ковка предполагает создание заготовок, которые впоследствии соединяется между собой с помощью сварки. Изделия холодной ковки не обладают особой уникальностью и стоят недорого. Однако, из этих небольших элементов можно сделать дизайнерскую, неповторимую вещь.
Данный метод позволяет производить большое количество идентичных элементов за короткий промежуток времени. Основными приемами ковки являются:
- Сгибание – это сгибание в разных направлениях, будь-то свиток, кольцо или пружинка.
- Скручивание – представляет собой скручивание материала до продольной оси. Таким образом, получаются витые элементы.
- Расплющивание – сжимание элементов.
- Чеканка – нанесение рисунка на изделие. Делается это с помощью давления специальными инструментами.
Основные различия холодной и горячей ковки
Самое главное и важное отличие холодной от горячей ковки является продолжительность работ. На создание изделий путем горячей ковки потребуется потратить много времени и сил. Для этого нужно нагреть материал так, чтобы из него можно было слепить любой элемент.
Также горячей ковка предполагает собой наличие большого помещения, кузнечного горна. Поэтому такой вид работ не подойдет для индивидуальных работ.
Холодная ковка намного проще, с помощью пресса, изгибания и сварки можно воссоздать любое изделие. Для проведения работ не потребуется много места, поэтому таким видом работ можно заниматься любому человеку.
Но, несмотря на простоту и легкость холодной ковки, горячая – это искусство. Красивые и неповторимые идеи, изящный и дорогой вид и индивидуальность каждого элемента.
Холодная ковка представляет собой работу с металлом в условиях комнатной температуры. Ее основные этапы: вырезка элементов, изгиб и сварка.
Основными преимуществами холодной ковки являются:
- Отсутствие высоких температур.
- Высокая прочность изготавливаемых изделий.
- Высокоточные изделия, которые не требуют дополнительной подгонки в размерах.
- Изготовленные элементы не требуют дополнительных обработок.
- Все работы не оставляют грязи, следов и гари.
Самым большим плюсом можно назвать большой ассортимент изделий. Из кованых элементов получаются ворота, решетки, мангалы, цветочницы, принадлежности для камина, части мебели, заборы, светильники и многое другое.
Изготовление кованых элементов
Весь процесс работ выполняется тремя основными путями:
- Вытяжка – здесь используются прессовочные или раскаточные станки, с помощью которых заготовка удлиняется, и одновременно, уменьшая сечение. На станках возможно придание деталям определенной текстуры, в результате чего получаются декоративные лапки или пики.
- Кручение – в данном случае происходит скручивание стального прута или полосы, при этом возможна одновременная обработка нескольких таких элементов. Для такого эффекта необходимо зажать в тиски концы одного прута, а другой крутить вокруг оси. Таим способом, можно получить изящный фонарик иди другой декоративный элемент.
- Гнутье – все работы на данном этапе производятся по шаблонам не специальных станках. Изделие подвергается различным изгибам, что не дает возможности получить одинаковые элементы.
ручная уникальная ковка металла и другая. Что это такое? Скульптуры и другие изделия, их сборка своими руками
Художественная ковка славится во всем мире. Из материала данной статьи вы узнаете, что она собой представляет, откуда появилась, какой бывает, где используется.
Что это такое?
Художественная ковка – обработанный металл с полученной изящной формой. Это произведенные эстетичные предметы быта, элементы архитектуры, созданные посредством ковки разного типа.
В сравнении с традиционными изделиями они имеют художественную ценность. Многие из них являются произведениям искусства. Они вносят особый изыск в интерьер и фасад дома, придомовую территорию.
Отличаются основательным и добротным, вместе с тем респектабельным и изящным внешним видом. Предполагают покраску и ежегодную обработку поверхности.
В отличие от традиционной ковки у нее есть декоративные элементы. Это могут быть всевозможные растительные орнаменты, силуэты животных и птиц, сложнейшие узоры и цветы.
История
Историческое начало современная художественная ковка получила в период появления первых государств в Иране, Египте, Месопотамии. Ковали металл коренные жители Северной и Южной Америки и иные народности.
В ту эпоху металл обрабатывался для производства оружия, изделий бытового назначения. Постепенная популяризация началась в XIV веке, когда металлические изделия стали украшать кованым декором.
Первая ковка была не столь детализированной, но ценилась достаточно высоко. Металлические кованые изделия могли себе позволить лишь представители знати.
Со временем мастерство достигло максимального уровня. Архитектура металла достигла наивысшего уровня в эпоху Ренессанса. Из элемента обыденной жизни она стала инструментом эстетичного убранства интерьеров и экстерьеров.
Ее стали использовать для решения задач безопасности. Она стала применяться в производстве ограждений, заборов и ворот. Наряду с этим, ею стали оформлять камины и лестницы.
Во времена СССР она уступала литью. Сегодня художественная ковка вернула свои позиции и по достоинству оценена в разных сферах использования.
Преимущества и недостатки
Кованые металлические изделия обладают рядом достоинств. В их производстве используют разные металлы. Они красивы, долговечны, практичны.
Обладают отменными защитными функциями, прочны и оригинальны. Каждая работа уникальная и неповторимая. При этом обработка металла позволяет создавать изделия с разной степенью сложности рисунка.
Кованые изделия из металла отлично сочетаются с разными видами строительных материалов. Они инертны к механическим повреждениям.
Производятся по массовому и индивидуальному виду работ.
Наряду с этим, довольно трудоемки, отличаются высокой стоимостью и долгими сроками производства. Индивидуальный вид работ требует создания чертежей, что занимает определенное время.
Без должной обработки изделия подвержены ржавлению. Однако далеко не все виды изделий удобно окрашивать. Некоторые объекты сложно и ковать, и красить, ввиду чего коррозия не заставляет себя долго ждать.
Виды
Производство кованых изделий – процесс длительный. Он включает ряд этапов начиная с разработки дизайна, эскиза, компьютерного моделирования.
Художественную ковку изготавливают из золота, серебра, железа, латуни, стали, меди. Лучшие материалы те, в составе которых содержится низкоуглеродистое волокно.
Благодаря разнообразию выбора увеличивается спектр возможностей для воплощения самых нестандартных изделий. Каждый вид металла податлив в работе и имеет свои особенности.
-
Латунь имеет характерную желтовато-золотистую окраску. Ее получают, соединяя медь и цинк. Она хорошо окрашивается и лакируется.
- Меди присущ коричнево-красный оттенок. При этом за счет полировки можно варьировать цвет металла. Из всех других разновидностей ее используют реже.
- Чугун – результат соединения железа и углерода.
В отличие от иных видов используется для производства массивных конструкций. Отлично поддается патинированию и покраске в любой цвет.
-
Стальные композиции разнятся. Бывают традиционными, воронеными, нержавеющими. Вторые аналоги создают путем окунания в масло с последующим обжигом. Третьи – продукт соединения хрома, титана, никеля.
-
Титан (цинк-титан) – один из лучших материалов, для податливости подвергающийся химическому травлению. Обладает уникальной текстурой.
- Золото и серебро – дорогостоящие металлы, применяемые для производства миниатюрных изделий.
При этом золото нередко используется в качестве напыления, из серебра делают уникальные аксессуары для интерьера.
По типу используемой технологии бывает ручной, массовой.
При этом базовые отличия между холодной и горячей заключаются в невысокой устойчивости первой и потребности в проведении сварочных работ для сборки в единую конструкцию.
Свободная
Данная разновидность предусматривает нагрев болванки до состояния пластичности с последующим формированием. Формировку выполняют посредством молота либо специального инструментария.
Пока материал находится в мягком пластичном виде, ему задается декоративная форма. Делается это вручную на всех этапах работы. При этом не применяются штампы, мастер не опирается на шаблонные эскизы.
Итог работы зависит от мастерства специалиста. После создания формы он остужает раскаленный металл. Далее идет этап декорирования, где, помимо красок, применяют лак.
Из-за ручного труда затраты на ковку существенно выше, чем у изделий, выполненных по другим технологиям. Такие изделия считаются эксклюзивными.
После обработки металл остается плотным, стойким к воде и погодным колебаниям. Ручная ковка выполняется дольше других опытным кузнецом. При этом заготовка свободно размещается на наковальне.
Ее придерживают одной рукой, а второй ударяют ручным либо механическим молотом.
Холодная
Холодный способ технологии есть не что иное, как изменение формы заготовки на специализированном оборудовании без предварительного нагревания.
Является достойной альтернативой литью либо штамповке. При этом готовые изделия имеют более высокую прочность. Методика предусматривает использование пресса и обязательную повторную обработку.
В работе используется минимум инструментов. Данная работа под силу даже малоопытному мастеру. Недостатком полуавтоматической техники является отсутствие возможности коррекции, если допущен брак.
В таком случае требуется повторный нагрев. А исправление дефекта может создать проблемы в других разогретых местах. Это увеличивает общее время, затраченное на работу.
Штамповка
При штамповании может использоваться холодная либо нагретая заготовка. В ходе обработки ее помещают в штамповальную форму, затем подвергают статическому давлению либо бьют молотом.
Методика штамповки применяется в производстве тиражированной продукции. Как и холодная техника, она неуникальна.
Такие изделия производят машинным способом по готовым лекалам.
Штамповочное производство автоматизировано. В ходе процесса деталь формуют за счет заполнения пустой полости штампа. Изделия отличаются высокой точностью и поверхностной чистотой.
При этом исключены даже мелкие заусенцы и обломы по краям. Металл подается в одном направлении до конкретных пределов. В сравнении с горячей ковкой возможности формообразования меньше.
Обзор элементов узоров
Кованые элементы разнятся габаритами и формами. Наиболее распространенными элементами ковки являются металлические прутья и проволока.
Помимо них, в производстве используют другие детали, которые создают из ключевых элементов. Одной из них является спираль, которую создают из прутка либо проволоки. Тип спирали бывает одно- и двухсторонним.
Соединение 2-х двусторонних завитков позволяет создать двойную спираль. Вид пространственной спирали схож со шнеком, имеющим рельефный край.
Диаметр кольца больше в середине узора, из-за чего его нередко называют китайским фонариком. Данные элементы формируют из пары прутьев либо толстой проволоки.
А также распространенными элементами являются геометрические орнаментальные фигуры, визуально напоминающие различные завитки. Их называют волютами.
Простые завитки могут иметь одно- и разнонаправленную вогнутость. Плоские завитушки куют из металлических полос. Они напоминают объемные спирали.
Распространенная деталь – чеканка, которую изготавливают посредством зубила, создавая уникальный орнамент с объемом.
Крутни – детали из скрученной в 1 сторону проволоки. К другим элементам относят навершия, представляющие собой прутья с острыми концами в месте верхушки. Ими украшают верхние части оконных решеток и оград.
А также мастера нередко прибегают к приему кернения, выдавливая уникальные детали с рельефом. Наиболее распространенные элементы – растительные узоры, надписи.
Нередко украшением кованых изделий являются оголовки. Визуально они напоминают чаши с конической, цилиндрической, сферической формы. Кроме них, декором являются листья и виноградные грозди.
Декоративными деталями являются кованые цветы, розы, фигуры животных (например, львов), подсвечники, шишки, ветки растений.
Произведенные элемент собирают в единую конструкцию методом горячего сваривания либо клепания, напоминающего принцип холодной сварки.
Инструменты и оборудование
Чаще всего в работе используют угольный горн и наковальню (инструменты, которыми пользуются кузнецы в творческих мастерских). Оснасткой является ручник, с крупными объектами работают кувалдой.
Размягченный металл удерживают клещами, применяя серийные наборы либо особенные инструменты в зависимости от типа работ. Инструментарий второго типа мастера делают сами для удобства ковки.
В список необходимого оборудования входят меха для раздува углей, молот, трубогиб. Сегодня в производстве используют муфельные печи и нагреватели индукционного типа.
В набор инструментария могут входить бородки, напильники, резцы, обжимки, подсечки. Многие мастера в работе пользуются инструментами для рифления и чеканки.
Основные приемы
Чтобы металлическое изделие имело нужную форму, мастерам приходится прибегать к использованию разных приемов обработки.
Высадка
Высадка укорачивает длину детали, одновременно увеличивая ее поперечное сечение. Это прием горячей техники, при котором размягченную деталь помещают на наковальню в вертикальном положении. Далее ее бьют по верхнему краю, формируют изгибы.
Протяжка
Операция протяжки противоположна предыдущему приему. С ее помощью удлиняют детали, прибегая к разгонке, расплющиванию, раскатыванию. Используется для заготовок разного типа (округлых, плоских, в виде кольца, с пустым телом).
Округление
Под данной процедурой подразумевается скругление краев профильных деталей. Изначально выполняют расковку углов до сечения восьмигранника. Затем деталь обжимают либо отбивают молотком, выполняя окончательную обработку.
Продевание
Эта методика выполняется при использовании ручного способа ковки металла. Создается эффект металлического плетения, в котором прутья визуально продеты друг в друга. Это достигается путем создания отверстий, необходимых для характерного рисунка.
Отделка уступов
Данный прием используется в технических и декоративных целях. Подразумевает закрепление деталей между собой с образованием уступов и изменение сечения на конце поковки. К этому прибегают лишь по необходимости, используя кувалду.
Гибка
Данный процесс есть не что иное, как формирование элементов посредством специального инструмента (вилки).
Оно используется, когда понадобилось сделать витой декор (петельный, спиралевидный, завитковый).
Сборка
Сборку конструкции выполняют разными способами. Например, это делают посредством газо- и электросварки, используя клепки, вставляя их в заранее подготовленные отверстия.
В других случаях прибегают к принципу кольцевания. Методика предполагает соединение элементов кольца со спайкой в нужных местах.
Отдельные композиции соединяют методом чеканки. При этом одну деталь вчеканивают в другую.
Для работы в условиях мастерской используется монтажный стол с доступом со всех сторон. При соединении конструкции своими руками в домашних условиях используют трансформируемый стол.
В ходе работы одни части куются полностью, другие выполняются отдельно. Чтобы не делать лишней работы, этот нюанс предусматривают на этапе проектирования будущего изделия.
Изделие, имеющее единичный растительный мотив, соединяется сваркой либо потайным клепанием. А также возможна комбинация обоих приемов. Такое соединение будет функциональным.
Соединительные места надлежит закрыть близ расположенным декором. Например, можно замаскировать стыки коваными листьями, цветами, геометрическим орнаментом, что свойственно стилистике барокко.
Когда нужно собрать конструкцию с идентичными декоративными элементами, поступают иначе. В таком случае для соединения выбирают скобы или хомуты.
Классический прием – выбор клепки с головкой в виде цветочного бутона или распустившегося цветка. Для композиций с выразительными соединениями это лучший выход. Приемами соединения могут стать плоды деревьев.
При замочной сварке выполняют осаживание концов и разрубку одного из них. Скругление при стыковочном соединении позволяет добиться чистоты шва.
Метод фальцевания заключается в скручивании смежных кромок. При двойном загибе мастер сгибает край для крепления, второй использует в качестве декора, придавая нужную форму.
В домашних условиях соединение выполняется посредством слесарных методик. Кто-то собирает композицию болтами и гайками.
Другие применяют проволоку, прикручивая ею детали к основе.
Декор
Художественную ковку украшают не только коваными элементами, но и специальными покрытиями. За счет них она обретает большую эстетичность и привлекательность внешнего вида.
Секреты украшения поверхностей заключаются в использовании подходящей краски. Например, это может быть покрытие патиной. Оно придает особый эффект даже самым простым композициям, существенно повышает респектабельность интерьера либо экстерьера.
Данный прием предполагает создание эффекта состаренности поверхности. Такая покраска отлично смотрится на кованых воротах, ажурной металлической мебели в доме либо саду.
Для покраски используют специальные красители с особым составом. Вещество наносят кистью, распылителем (краскопультом), ватным тампоном либо иным способом.
Перед покраской конструкцию подвергают зачистке. Покрытие выполняют составами для металлов. При этом фактура краски может быть не только стандартной, но и необычной.
Интересный декор – рельефное покрытие с молотковым эффектом. Визуально оно смотрится так, словно поверхность усеяна рытвинами от отбойного молота.
Покрасочный материал отлично маскирует мелкие недочеты ковки, что особенно актуально для мастеров с небольшим опытом работы. Нанести ее можно кистью и даже валиком.
Распространенный материал – кузнечная краска из полимеров, дающая качественное и долговечное покрытие металла. Она быстро высыхает даже при низкой температуре. Поэтому активно используется для покраски уличных конструкций.
А также кованые композиции можно серебрить и золотить, делать бронзовыми. Форма выпуска того или иного красителя бывает жидкой или порошковой. Разновидности второго типа напыляют на основание и запекают.
Красиво смотрится и металл, окрашенный цветом и лаком с серебряными либо золотыми блестками. Эффект довольно необычен и свеж. Сегодня таким декором украшают небольшие мостики и лавочки в городских скверах.
Помимо привычных вариантов на алкидной, масляной основе, ковку покрывают резиновыми красками на основе битумной смолы. Подготовка поверхностей под них минимальна, а расход больше других аналогов.
Что касается тематики декора, то в приоритете 3 ветви направлений: геометрические узоры, растительные и животные элементы. В большинстве случаев декор объемен и не единичен. При этом используемые детали выполнены в едином размере.
К декоративным приемам относится и комбинирование металлов в авторских изделиях. А также это может быть деталь с разным цветом металла (например, цветок со стальными лепестками и черной сердцевиной).
Что можно выковать?
Использование разных методов ковки существенно увеличивает сферы применения. Например, по технике холодной ковки создают ювелирные украшения.
Для обустройства интерьеров производят всевозможную интерьерную и кухонную мебель (боковины кровати, туалетные и прикроватные столики, банкетки). Художественной ковкой украшают окна, делая на них красивые решетки.
Популярные изделия – вазоны, люстры и подсвечники с ковкой, одежные вешала. Экстерьерная продукция – кованые ворота, декор на забор, ограждения на балкон.
Кроме того, художественная ковка используется для небольших архитектурных форм. Например, это могут быть элементы навесных маркиз и козырьков, перила террас и веранд, декор летних беседок, садовых скамеек.
Ковку применяют при обустройстве качелей, подвесных кресел, уличных фонарей, мангалов, мостов и урн. С ее помощью ограждают могилы умерших родственников. Из нее получаются уникальные печные наборы.
Декоративная ковка отлично смотрится в ландшафте парковых зон, дачных и садовых участков. Она уместна среди скульптур из мрамора, гармонично контрастирует с зелеными насаждениями французских и английских парков.
В современном строительстве пользуются популярностью кованые калитки, вмонтированные в стену, либо расположенные отдельно. Нередко художественной ковкой декорируют цветники и малые изгороди.
Из них получаются уникальные подставки и полки для цветов и красивые кресла, ножки обеденных столиков. Кружевными конструкциями обрамляют зеркала. Ковка применяется в производстве подставок под обувь, ее элементы есть у прихожих.
Из них получаются красочные перголы и перекрытия арок. Порой кованые конструкции представляют собой коридоры для вьющихся растений.
А также конструкции являются украшением акцентных зон жилища. В этом плане они могут нести исключительно декоративную функцию.
изображений, фотографий и картинок из холоднокованого железа
паяльник 25w фото
картинка паяльника на бутане
паяльник 300w фото
утюг на термотрансферной бумаге фото
Предыдущий Следующий 1 / 50 Фото товары: Связанные ключевые слова: кузнечный мир чугунное литье железные украшения чугунные гири стандартная кузнечная ось центральные кузнечные инструментыЧто такое ковка? Различные виды ковки в подержанном производстве
Ковка, метод формирования металла с использованием сжимающих локализованных сил, был основным методом изготовления металла со времен древних жителей Месопотамии. С момента своего возникновения в плодородном полумесяце ковка претерпела значительные изменения, в результате чего процесс стал более эффективным, быстрым и долговечным. Это связано с тем, что сегодня ковка чаще всего выполняется с использованием кузнечных прессов или молотковых инструментов, которые приводятся в действие электричеством, гидравликой или сжатым воздухом. Некоторыми из распространенных материалов, используемых для ковки, являются углеродистая сталь, легированная сталь, микролегированная сталь, нержавеющая сталь, алюминий и титан.
Изображение предоставлено Shutterstock.com/Drpixel
Какова цель ковки?
Целью ковки является создание металлических деталей. По сравнению с другими методами производства, ковка металла позволяет производить одни из самых прочных изготавливаемых деталей. Когда металл нагревается и прессуется, мелкие трещины заделываются, а любые пустоты в металле закрываются.
Процесс горячей штамповки также разрушает примеси в металле и перераспределяет такой материал по металлоконструкциям.Это значительно уменьшает включения в кованой детали. Включения представляют собой составные материалы, имплантированные внутрь стали во время производства, которые создают точки напряжения в конечных кованых деталях.
В то время как примеси следует удалять в процессе начального литья, ковка дополнительно очищает металл.
Другой способ, с помощью которого ковка упрочняет металл, заключается в чередовании его зернистой структуры, которая представляет собой поток зерен металлического материала при его деформации. Благодаря ковке можно создать благоприятную структуру зерна, что сделает кованый металл более прочным.
Процесс ковки очень многоцелевой и может использоваться как для мелких деталей размером всего несколько дюймов, так и для крупных компонентов весом до 700 000 фунтов. Он используется для производства важных деталей самолетов и транспортного оборудования. Ковка также используется для укрепления ручных инструментов, таких как долота, заклепки, винты и болты.
Какие бывают виды ковки?
Ударное воздействие при ковке деформирует и формирует металл, что приводит к непрерывному потоку зерен. Благодаря этому металл сохраняет свою прочность.Дополнительные эффекты этого уникального потока зерна включают устранение дефектов, включений и пористости в продукте. Еще одним преимуществом ковки являются относительно низкие затраты, связанные с умеренными и длительными производственными циклами. После создания кузнечного инструмента изделия можно изготавливать на относительно высоких скоростях с минимальными простоями. Существует два основных вида ковки: горячая и холодная.
Горячая штамповка
Горячая ковка требует, чтобы металл был нагрет выше его температуры рекристаллизации.Это может означать нагрев металлов до 2300 градусов по Фаренгейту. Основным преимуществом горячей ковки является снижение энергии, необходимой для правильной формовки металла. Это связано с тем, что чрезмерное нагревание снижает предел текучести и улучшает пластичность. Изделия горячей штамповки также выигрывают от устранения химических несоответствий.
Нужна компания по горячей штамповке? Компания Thomas’ Supplier Discovery имеет проверенный список компаний, занимающихся горячей штамповкой в США и Канаде.
Холодная ковка
Холодная ковка обычно относится к ковке металла при комнатной температуре, хотя возможна любая температура ниже температуры рекристаллизации.Многие металлы, такие как сталь с высоким содержанием углерода, просто слишком прочны для холодной ковки. Несмотря на это препятствие, холодная ковка вытесняет свой более теплый эквивалент, когда речь идет о стандартах контроля размеров, однородности продукта, чистоте поверхности и загрязнении. Холодная ковка включает в себя множество методов ковки, включая гибку, экструзию, холодное волочение, чеканку и холодную высадку. Однако за эту повышенную универсальность приходится платить, поскольку для холодной ковки требуется более мощное оборудование и может потребоваться использование промежуточных отжигов.
Нужна компания по холодной штамповке? У Thomas’s Supplier Discovery есть проверенный список компаний холодной штамповки в США и Канаде.
Для получения более подробной информации о любом из этих процессов, пожалуйста, прочитайте наше Полное руководство по горячей и холодной штамповке.
Горячая ковка используется для изготовления автомобильных деталей.Изображение предоставлено Shutterstock.com/Aumm graphixphoto
Какие существуют процессы ковки?
Помимо базовой горячей и холодной ковки, существует множество специальных процессов.Этот широкий спектр процессов можно сгруппировать в три основные зонтичные группы:
Вытяжка уменьшает ширину
продукт и увеличивает длину. Осадочная ковка увеличивает ширину изделий и уменьшает длину. Компрессионное формование обеспечивает поток ковки в нескольких или заданных направлениях.
Эти три категории подразумевают множество различных методов ковки металлов.
Процесс ковки
Штамповка получила свое название от процесса опускания молота на металл, чтобы придать ему форму штампа.Матрица – это поверхность, соприкасающаяся с металлом. Существует два вида штамповки: штамповка в открытых и закрытых штампах. Матрицы обычно имеют плоскую форму, а некоторые из них имеют поверхности особой формы для специализированных операций.
Процесс открытой штамповки
Когда плоские штампы, не имеющие предварительно вырезанных профилей, участвуют в ковке, процесс ковки называется ковкой в открытых штампах (или кузнечной ковкой). Открытая конструкция позволяет металлу течь везде, кроме места соприкосновения с матрицей.Для достижения максимальных результатов правильное перемещение заготовки, которая должна составлять более 200 000 фунтов. в весе и 80 футов в длину, имеет важное значение. Это полезно для мелкосерийного художественного кузнечного дела или для формовки слитков перед вторичной формовкой. Ковка в открытых штампах создает детали с лучшей устойчивостью к усталости и прочностью и снижает вероятность ошибок или отверстий. Его также можно использовать для более мелкого размера зерна, чем другие процессы.
Процесс ковки в закрытых штампах
Ковка в закрытых штампах, иногда называемая штамповочной ковкой, использует пресс-формы.Эти формы прикреплены к наковальне, в то время как молоток заставляет расплавленный металл течь в полости матрицы. Множественные удары и/или полости штампа часто используются при ковке сложной геометрии. Высокие первоначальные затраты на оснастку делают ковку в закрытых штампах дорогой для мелкосерийных операций, но процесс ковки становится рентабельным по мере увеличения количества производимых деталей. Ковка в закрытых штампах также обеспечивает исключительную прочность по сравнению с альтернативными методами. Общие области применения штамповки в закрытых штампах включают производство автомобильных компонентов и аппаратных средств.
Процесс ковки на прессе
При ковке на прессах основным формообразующим фактором является сжатие. Металл находится на стационарной матрице, в то время как пресс-форма оказывает постоянное давление, достигая желаемой формы. Время контакта металла с штампами значительно больше, чем при других типах ковки, но преимущество процесса ковки состоит в том, что он может одновременно деформировать все изделие, а не определенный участок. Еще одним преимуществом ковки на прессе является возможность производителя отслеживать и контролировать конкретную степень сжатия.Применения ковки на прессе многочисленны, поскольку нет никаких ограничений на размер продукта, который может быть создан. Ковка на прессе может быть горячей или холодной.
Процесс ковки в рулонах
Прокатная ковка — это процесс увеличения длины стержней или проволоки. Производитель помещает нагретые металлические стержни между двумя цилиндрическими валками с канавками, которые вращаются и прилагают постепенное давление для придания металлу формы. Точно сформированная геометрия этих канавок придает металлической детали желаемую форму.Преимущества этого метода ковки включают устранение облоя и благоприятную структуру зерна. Хотя в кузнечном производстве используются валки для производства деталей и компонентов, он по-прежнему считается процессом ковки металла, а не процессом прокатки. Прокатная ковка часто используется для изготовления деталей для автомобильной промышленности. Он также используется для ковки таких вещей, как ножи и ручные инструменты.
Процесс ковки с осадкой
Ковка с осадкой — это процесс ковки, при котором диаметр металла увеличивается за счет сжатия.Кривошипные прессы, особенно высокоскоростные машины, используются в процессах ковки с высадкой. Кривошипные прессы обычно устанавливаются в горизонтальной плоскости для повышения эффективности и быстрого обмена металла с одной станции на другую. Также используются вертикальные кривошипные прессы или гидравлические прессы. Преимущества этого процесса заключаются в том, что он обеспечивает высокую производительность до 4500 деталей в час и возможность полной автоматизации. Он также производит мало или вообще не производит отходов.
Процесс изотермической ковки
Изотермическая ковка — это процесс ковки, при котором материалы и штамп нагреваются до одинаковой температуры.Название происходит от «iso», что означает «равный». Этот метод ковки обычно используется для ковки алюминия, который имеет более низкую температуру ковки, чем другие металлы, такие как сталь. Температура ковки алюминия составляет около 430 °C, а стали и жаропрочных сплавов может составлять от 930 до 1260 °C. Преимущество заключается в том, что форма, близкая к чистой, снижает требования к механической обработке и, следовательно, снижает процент брака, а металлическая деталь обладает высокой воспроизводимостью. Еще одно преимущество заключается в том, что для изготовления поковок можно использовать машины меньшего размера из-за меньших потерь тепла.Несколькими недостатками являются более высокие затраты на материал штампа для работы с температурами и давлением и требуемые системы равномерного нагрева. Он также имеет низкую производительность.
Какое оборудование используется для ковки?
Самый популярный вид кузнечного оборудования – молот и наковальня. Идея молота и наковальни до сих пор используется в кузнечном оборудовании с молотом. Молоток поднимают, а затем опускают или толкают в заготовку, которая опирается на наковальню. Основные различия между отбойными молотками заключаются в том, как они приводятся в действие, наиболее распространенными из которых являются воздушные и паровые молоты.Отбойные молотки обычно работают в вертикальном положении. Это связано с тем, что избыточная энергия, которая не выделяется в виде тепла или звука, то есть энергия, которая не используется для придания формы заготовке, должна быть передана в основание. Также требуется большая машинная база для поглощения ударов.
Для преодоления некоторых недостатков отбойного молота используется противоударная машина или ударник. И молоток, и наковальня движутся в противоударной машине, а заготовка удерживается между ними. Здесь избыточная энергия становится отдачей, позволяя машине работать горизонтально и иметь меньшую базу.Это создает меньше шума, тепла и вибрации. Это также создает совершенно другую схему потока. Эти машины используются для ковки в открытых или закрытых штампах.
Пресс используется для ковки на прессах. Двумя основными типами являются механические и гидравлические прессы. Механические прессы функционируют с использованием кулачков, кривошипов и рычагов для выполнения заранее заданных и воспроизводимых ударов молотком. Из-за характеристик этого типа системы в разных положениях хода доступны разные усилия. В результате эти прессы быстрее своих гидравлических аналогов на 50 ходов в минуту.Их мощности варьируются от трех до 160 МН. Гидравлические прессы используют давление жидкости и поршень для создания усилия. Преимущества гидравлического привода перед механическим заключаются в его гибкости и превосходной производительности. Недостатки заключаются в том, что это более медленная, крупная и дорогая машина в эксплуатации.
В процессах ковки, автоматической горячей штамповки и высадки используется специализированное оборудование.
Резюме
Это руководство дает общее представление о том, что такое ковка, и о различных процессах ковки.Чтобы узнать больше о других методах изготовления металла, прочитайте наше руководство здесь. Для получения дополнительной информации о сопутствующих услугах обратитесь к другим нашим руководствам по продуктам или посетите платформу поиска поставщиков Thomas, чтобы найти потенциальные источники или просмотреть сведения о конкретных продуктах.
Источники
Другие изделия из металла
Больше из Изготовление и изготовление на заказ
Штамповка – обзор
3.2.6 Катаные боковые рельсы специального профиля
Если посмотреть на историю стрелочных переводов с поворотным носовым рельсом в Китае, технологический процесс боковых рельсов претерпел эволюцию от обработки обычных рельсов до обработки с высоким содержанием марганца. стальное литье, штамповка рельсов AT и прокат специального профиля.Рельсы крыла, сделанные из обработанных общих рельсов, использовались на первых разгонных стрелочных переводах в Китае. Этот тип бокового рельса характеризуется простотой производственного процесса, большим количеством резки в основании рельса, недостаточным запасом прочности (требуются арматурные стержни на шейке наружных рельсов), небольшим расстоянием для преобразовательного оборудования и плохой поперечной устойчивостью. Он был принят для высокоскоростных стрелочных переводов в Германии. Однако, несмотря на стабильные точечные рельсы этой конструкции, как показали динамические испытания с реальными автомобилями в Китае, боковые рельсы имеют большое поперечное смещение.Рельсы крыла, литые из высокомарганцовистой стали, использовались для высокоскоростных стрелочных переводов в Японии и Франции, а также для первых перекрестков поворотной носовой части в Китае. Преимущества включают возможность обеспечения достаточного расстояния для оборудования электрического преобразования и хорошую структурную стабильность (в частности, сильную целостность).
Недостатки включают быстрый преждевременный износ верхней части боковых рельсов в условиях грузового движения и плохие характеристики при сварке с обычными рельсами на месте. Исследования этого типа крыла крыла были приостановлены, поскольку он не соответствовал условиям эксплуатации в Китае.Технология производства боковых рельсов специального сечения с АТ-рельсами методом штамповки является уникальной технологией в Китае, которая широко использовалась в ускоренных стрелочных переводах в течение последнего десятилетия, как показано на рис. 3.6. Преимущества включают хорошую структурную стабильность и возможность обеспечения достаточного расстояния для электрооборудования. К недостаткам относятся меньшая прочность и твердость лонжеронов после термической обработки, повышенный риск вертикального износа в верхней части лонжеронов и риск хрупких изломов.
Рисунок 3.6. Кованый боковой рельс специального сечения и излом остряка.
Для трех типов боковых рельсов стрелочный стержень в первой точке тяги на поворотном носовом рельсе может выступать из стенки рельса или основания рельса. На ранних стрелочных переводах в Китае стрелочный стержень проходил через отверстия в решетке рельса. Однако в случае плохого состояния стрелочного перевода может возникнуть сильная вибрация, что может привести к вертикальному столкновению отверстий боковых рельсов. Кроме того, в случае большого смещения стрелочных переводов для стрелочных переводов CWR стрелочный стержень может столкнуться со стенкой отверстий в стенке рельса, что приведет к образованию трещин или отверстий.Поэтому позже от этой технологии отказались. Этот режим установки также был принят для высокоскоростных стрелочных переводов на расходящейся линии в Германии. Доказано, что при использовании этого режима установки стрелочный перевод находится в хорошем состоянии и имеет меньшую вибрацию, а смещение при расширении остряка уменьшается благодаря эффективной соединительной конструкции на конце пересечения. Однако отверстия в стенке рельса также могут иметь трещины. На основе кованых боковых рельсов в Китае были разработаны конверсионные направляющие рельсы фланцевого типа для ускорения стрелочных переводов.
Для этого типа стрелочного рельса фланцевая пластина изготавливается горячей ковкой в основании стрелочного рельса, стержень переключения проходит от основания рельса и соединяется с фланцевой пластиной, что приводит к преобразованию стрелочных переводов. Эта структура отличается сильной блокирующей способностью, стабильной конструкцией и простым производственным процессом. Однако в условиях эксплуатации с большой нагрузкой на ось, высокой скоростью и большим объемом и плотностью движения в Китае некоторые остроконечные рельсы ломаются вдоль переходной полки, как показано на рис. 3.6. Кроме того, поскольку положение соединения стержня переключателя и фланца относительно низкое, точечный рельс подвержен деформации во время преобразования, и стержень электрической индикации не может определить правильное замыкание рельса. Таким образом, сбой в обнаружении закрытия ставит под угрозу безопасность стрелочных переводов.
Чтобы решить проблему надежности конструкции в первой точке тяги на стрелочном рельсе, в Китае был разработан катаный боковой рельс специального профиля (сокращенно TY) с использованием тех же материалов, что и другие стрелочные рельсы, как показано на рисунке 3. 7. Этот тип рельса, с одной стороны, повышает прочность и устойчивость бокового рельса, а с другой стороны, он оставляет достаточно места для электрического блокировочного блока и стопорного крюка, экономит переходной фланец, поднимает точку соединения стопорного крюка и точечный рельс, решает проблему обнаружения отказа и упрощает производственный процесс за счет отмены процесса термообработки (требуется только процесс механической обработки). Таким образом, прокатные боковые рельсы специального профиля применяются для высокоскоростных стрелочных переводов в Китае благодаря всестороннему сравнению.
Рисунок 3.7. Крыльчатка катаная специального профиля.
Влияние многоэтапной термической обработки на различные технологические процессы стали 18CrNiMo7-6
Влияние термической обработки на микроструктурные свойства
На рисунке 4 показаны оптические микрофотографии, показывающие влияние отдельных этапов термообработки на микроструктуру после механической обработки ( Этапы 0–5, образцы S1–S6, таблица II). Образец после механической обработки (этап 0, S1) имел смесь типичной перлитной и ферритной микроструктуры.Нормализация (этап 1) проводилась при температуре выше, чем температура аустенитного превращения (Ac3), а охлаждение на воздухе (AC) приводило к получению смеси бейнитной и ферритной микроструктуры. На следующем этапе отжиг с последующим АС (этап 2) уменьшил твердость материала и снял внутренние напряжения. Высокая температура во время закалки (этап 3) привела к образованию большего количества аустенита, но закалка в масле (OQ) в конечном итоге привела к образованию игольчатых мартенситных пластин. Это еще больше ускорилось во время обработки при отрицательных температурах (этап 4), в результате которой была получена более тонкая игольчатая мартенситная структура.Отпуск (Этап 5) обеспечил приемлемую ударную вязкость за счет снижения твердости и сохранения мартенситной микроструктуры.
Оптические микрофотографии, показывающие влияние отдельных этапов термообработки на микроструктуру после механической обработки
На рисунке 5 показаны оптические микрофотографии, показывающие влияние отдельных этапов термообработки на микроструктуру горячей штамповки (этапы 0–5, образцы S7–S12). , Таблица II). Горячештампованный образец (Этап 0, S7) имел смесь бейнитно-ферритной микроструктуры, и также были отчетливо видны крупные первичные аустенитные зерна.Эта микроструктура сохранялась как после стадий нормализации, так и после отжига. Стадия закалки с последующим OQ позволила получить игольчатые мартенситные пластины, которые еще больше ускорились во время обработки при отрицательных температурах, что привело к более тонкой игольчатой мартенситной структуре. Эта микроструктура сохранялась до стадии отпуска. Аналогичным образом, на рисунке 6 показаны оптические микрофотографии, показывающие влияние отдельных этапов термообработки на микроструктуру холодной ротационной штамповки (этапы 0–5, образцы S13–S18, таблица II).Образец, подвергнутый холодной штамповке (этап 0, S13), показал смесь перлитно-ферритной микроструктуры, аналогичную образцу после механической обработки (этап 0, рис. 4). Как на этапах нормализации, так и на этапах отжига была получена бейнитно-ферритная микроструктура, и на этих микрофотографиях можно было наблюдать прежние границы аустенитных зерен (этапы 1 и 2 на рисунке 6).
Стадия закалки с последующим OQ позволила получить игольчатые мартенситные пластины, которые еще больше ускорились во время обработки при отрицательных температурах, что привело к более тонкой игольчатой мартенситной структуре.Это сохранялось до конца отпуска. В целом образец, полученный методом холодной штамповки, показал микроструктурную эволюцию, очень похожую на образец после механической обработки до и после термообработки.
Оптические микрофотографии, показывающие влияние отдельных этапов термообработки на микроструктуру горячей штамповки
Рис. 6Оптические микрофотографии, показывающие влияние отдельных этапов термообработки на микроструктуру холодной штамповки
Мелкозернистая однородная микроструктура всегда предпочтительнее ленточной микроструктуры для достижения изотропных механических свойств.В этой работе полосчатая микроструктура наблюдалась в образце после механической обработки (этап 0, рис. 4) и после холодной ротационной штамповки (этап 0, рис. 6). Но многоступенчатая термообработка преобразовала эту полосчатую микроструктуру в отпущенную мартенситную микроструктуру независимо от вышеупомянутых технологических маршрутов (этап 5 на рисунках 4 и 6). С другой стороны, горячая ковка устранила полосчатую микроструктуру (этап 0, рис. 5), а затем термообработка привела к образованию аналогичной отпущенной мартенситной микроструктуры (этап 5, рис. 5).Таким образом, способ горячей штамповки сам по себе эффективен для устранения полосчатой микроструктуры, тогда как многоступенчатая термообработка требуется как для способов механической обработки, так и для способов холодной ротационной штамповки.
На рисунке 7 показано влияние термической обработки на поток зерен и микроструктуру горячештампованного компонента. Фактическая горячештампованная деталь имеет форму симметричного плоского цилиндрического диска, поэтому на макрофотографиях показана только половина детали до и после термообработки. Макрофотография, показывающая компонент до термообработки, показала течение материала по направлению к внешнему диаметру (Рисунок 7(а)) и после термообработки не наблюдалось никаких изменений в потоке зерна (Рисунок 7(b)).Оптические микрофотографии, сделанные из центра детали (местоположения микрофотографий обведены черным цветом) до и после термообработки (рис. 7(c) и (d) соответственно), показали полное отсутствие полосчатой микроструктуры. Аналогичным образом на Рисунке 8 показана эффективность термической обработки в отношении потока зерен и микроструктуры компонента холодной штамповки. Макрофотография, показывающая половину симметричного компонента холодной штамповки (этап 0, рис. 8(a)) указывает на значительную разницу в потоке материала с верхней и нижней сторон по сравнению с центром, в частности, полоса, показывающая разницу в потоке зерна, была наблюдается в поперечном направлении.Полосчатая микроструктура была видна на оптической микрофотографии (рис. 8(c)). Термическая обработка устранила полосчатую микроструктуру (рис.
8(d)) и, в свою очередь, улучшила текучесть зерна (рис. 8(b)).
Влияние термической обработки на ( a , b ) течение зерна (длина шкалы 1 см) и ( c , d ) микроструктуру фактической горячештампованной детали6 Рис 6 Рис. . 8
Эффективность термообработки на ( a , b ) поток зерен (длина шкалы 5 мм) и ( c , d ) микроструктуру фактического холоднокованого компонента
Важно отметить, что перлитно-ферритная микроструктура получается с помощью способов механической обработки и холодной ротационной штамповки, тогда как путь горячей ковки приводит к бейнитно-ферритной микроструктуре.Однако термообработка превращает их в одну и ту же конечную микроструктуру , т. е. ., в более тонкую игольчатую микроструктуру отпущенного мартенсита. Для всех трех компонентов мартенситная микроструктура была получена на шаге 3 и затем сохранялась до конца термообработки. В частности, эта термообработка устранила полосчатую микроструктуру как в компонентах, подвергнутых механической обработке (Рисунок 4), так и в компонентах холодной штамповки (Рисунок 6), и одновременно улучшила поток зерен компонента холодной штамповки (Рисунок 8).
Для лучшего понимания эффективности этой термической обработки в отношении эволюции микроструктуры во время этих трех производственных маршрутов был проведен анализ EBSD, и основное внимание было уделено трем ключевым точкам: , т.е. ., Этап 0, Этап 3 и Этап 5. На рисунке 9 показаны контрастные полосовые изображения образцов после механической обработки, горячей штамповки и холодной штамповки на шагах 0, 3 и 5. Различные исходные микроструктуры (этап 0) всех трех производственных процессов были преобразованы в мартенситную микроструктуру на этапе 3, и никаких дальнейших изменений не наблюдалось на этапе 5.
Рис. 9Контрастные изображения, демонстрирующие влияние выбранных этапов термообработки на различные производственные процессы
На рисунке 10 показаны фазовые карты вышеупомянутых образцов, на которых ОЦК и орторомбическая кристаллическая структура обозначены желтым и красным цветами соответственно. Любая обнаруженная фаза с долей менее 1% считалась шумом и поэтому не учитывалась при анализе. Основной фазой, наблюдаемой в стали 18CrNiMo7-6, был феррит ОЦК (97.от 8 до 99,9%) на шаге 0. На этапе 3 сформировалась мартенситная микроструктура ОЦК (от 98,8 до 99,6 %). Как правило, в закаленных образцах стали наблюдалась мартенситная микроструктура ОЦК или ОЦТ в зависимости от концентрации углерода. Микроструктура обычно была ОЦК, , т. е. ., c / и отношение 1, когда концентрация углерода была <0,6 мас.% [29], и то же самое наблюдалось для стали 18CrNiMo7-6, содержащей ~ 0,18 мас.% углерода. Мартенситная микроструктура оставалась основной фазой как при механической обработке (97,8%) и горячей штамповки (99,9%) на этапе 5, однако для маршрута холодной ротационной штамповки наблюдалась значительная разница, свидетельствующая о наличии фаз ОЦК-мартенсита (75,1%) и орторомбического цементита (7,9%). Здесь следует отметить, что индексация образца S18 составила всего ~ 83% и, следовательно, была большая вероятность того, что неиндексированные точки могли принадлежать либо мартенситной, либо цементитной фазам.
Это заметное образование цементита, наблюдаемое в S18, требует дальнейшего изучения.Однако на это может повлиять более низкая температура закалки (800 °C), используемая в этом случае, чем обычный диапазон температур закалки сердцевины (от 830 °C до 870 °C) для этой стали.
Фазовые карты (желтым цветом ОЦК, красным ромбическим), показывающие влияние выбранных этапов термообработки на различные производственные процессы (цветной рисунок онлайн)
На рис. 11 показано влияние выбранных этапов термообработки на средний эффективный размер зерна, полученный в результате различных производственных процессов.Эффективный размер зерна, определенный по углу разориентации θ >15 град, наблюдался наибольшим в образце после механической обработки (~ 7,60 мкм мкм в перлитно-ферритной микроструктуре) и немного меньше как для горячештампованного (~ 6,40 мкм м в бейнитно-ферритной микроструктуре) и холодноштампованные (~ 6,31 мкм м в перлитно-ферритной микроструктуре) образцы. Эти различные исходные микроструктуры были преобразованы в игольчатую мартенситную микроструктуру на этапе 3, где наблюдалось значительное уменьшение среднего эффективного размера зерна для всех трех способов обработки (~ 3.04, ~3,34 и ~3,37 мк м для маршрутов механической обработки, горячей штамповки и холодной ротационной штамповки соответственно). На шаге 5 формирование отпущенной мартенситной микроструктуры привело к небольшому увеличению среднего эффективного размера зерна для способа механической обработки (~ 3,36 μ мкм), но незначительному уменьшению как для способов горячей штамповки, так и для способов холодной ротационной штамповки (~ 3,1 и ~ 3,06 мк м соответственно). На рисунке 12 показаны карты обратной полюсной фигуры (IPF) в плоскости ND–RD, указывающие на случайную ориентацию этих зерен для всех трех производственных маршрутов.Следует отметить, что изменение микроструктуры, а также эффективного размера зерна от шага 0 до шага 3 не показало никакого изменения в соответствующей ориентации зерен.
Независимо от технологической схемы эта термообработка приводила к одинаковой отпущенной мартенситной микроструктуре со средним эффективным размером зерна в диапазоне от ~ 3,06 до 3,36 мкм мкм.
Влияние выбранных этапов термообработки на средний эффективный размер зерна, полученный при различных производственных технологиях
Рис.12Карты IPF, показывающие ориентацию эффективных зерен на выбранных этапах термообработки на различных производственных маршрутах
На рисунке 13 показано влияние выбранных этапов термообработки на долю площади эффективных зерен, полученных при различных производственных процессах. Рекристаллизованные, субструктурированные и деформированные зерна показаны синим, желтым и красным цветами соответственно на картах площадей и на сводном графике. Деформированные зерна содержат большое количество дислокаций и характеризуются углом разориентации ≤ 5 град. Рекристаллизованные зерна представляют собой недеформированные зерна, не содержащие запасенной упругой энергии и определяемые углом разориентации ≥ 15 град. Субструктурированные зерна представляют собой метастабильные зерна с меньшим количеством дислокаций и характеризуются углом разориентации в диапазоне от 5 до 15 градусов. Первоначальный маршрут обработки заготовки привел к образованию большого количества рекристаллизованных зерен (~ 90,5%) в образце после механической обработки (этап 0). Шаг 3 вводил деформацию решетки из-за образования мартенсита, что приводило к увеличению плотности дислокаций.Это привело к увеличению количества как субструктурированных, так и деформированных зерен (от ~ 49,2 до 65,3 и от ~ 14,5 до 17,2% соответственно), которые сохранялись на этапе 5. При горячей штамповке (Этап 0) динамическая рекристаллизация привела к образованию значительного количества рекристаллизованных и субструктурированных зерен (~ 40,8 и 58,3% соответственно). При термообработке (Этап 3 и Этап 5) структурная деформация за счет ОК привела к образованию значительного количества деформированных зерен (~ 11.
5 до 14,4 %) за счет рекристаллизованных и субструктурированных зерен (~ 34 до 35,7 и ~ 51,6 до 52,8 % соответственно). С другой стороны, образец холодной ротационной штамповки (этап 0) содержал в основном неструктурированные зерна (~ 88,1%) из-за отсутствия динамической рекристаллизации при низкой температуре. Хотя при такой низкой температуре динамической рекристаллизации не происходило, но энергии, создаваемой адиабатическим теплом от деформации материала, казалось достаточно, чтобы перестроить дислокации в ячеистые структуры с более низкой энергией, что привело к образованию в основном субструктурированных зерен.После термической обработки (Этап 3 и Этап 5) субструктурированные зерна были значительно рекристаллизованы (от ~ 29 до 29,9 %), а деформация, вызванная OQ, одновременно увеличила количество деформированных зерен (от ~ 9,07 до 13 %). В дополнение к этому, суммарный график показывает, что эта термообработка приводит к почти одинаковой доле площади зерен (от ~ 29 до 34% рекристаллизованных, от 51,6 до 61,9% неструктурированных и от 9,07 до 14,4% деформированных зерен) для обеих горячештампованных зерен.
и маршруты холодной ротационной штамповки, но немного отличаются для маршрута механической обработки (~ 17.5% рекристаллизованных, 65,3% неструктурированных и 17,2% деформированных зерен).
Влияние выбранных этапов термообработки на долю площади эффективных зерен, наблюдаемое на различных производственных маршрутах (цветной рисунок онлайн)
На рисунке 14 показаны карты KAM, представляющие распределение деформации на выбранных этапах термообработки при различных производственных маршрутах. Пластическая деформация компонентов в состоянии после их изготовления (Этап 0) и на различных этапах термообработки (Этап 3 и Этап 5) измеряется с использованием метода локальной разориентации.Карта KAM измеряет локальные разориентации между отдельными точками измерения и, таким образом, представляет деформацию сканируемой области. Красный и синий цвета обозначают самый высокий и самый низкий уровни разориентации, соответственно, для этих сканированных областей, как показано на шкале. Как видно, распределение деформации было самым низким (обозначено в основном синим и зеленым цветами) в компоненте после механической обработки, за которым следуют компоненты, полученные методом холодной ротационной штамповки и горячей штамповки, соответственно. Во время термообработки на этапе 3 деформация была вызвана мартенситным превращением, что привело к повышенному уровню деформации (обозначено преимущественно желтым цветом).На этом этапе компонент холодной ротационной штамповки показал самый низкий уровень деформации. На шаге 5 уровни деформации были дополнительно увеличены (обозначены в основном желтым и красным цветами), что привело к одинаковому распределению деформации, несмотря на различия в геометрии конечных компонентов для всех трех производственных маршрутов. Эти уровни деформации могут быть дополнительно соотнесены с соответствующими средними эффективными размерами зерна, где деформация, возникающая во время термообработки, вызывает существенное измельчение зерна.

Карты средней разориентации ядра (KAM), представляющие распределение деформации на выбранных этапах термообработки при различных производственных маршрутах (цветной рисунок онлайн)
Следует отметить эволюцию кристаллографической текстуры во время термической обработки этих трех готовых компонентов. Карты функции распределения ориентации (ODF) используются для представления текстуры в этой работе. Как правило, наиболее важным сечением ODF является сечение ϕ 2 = 45 градусов для материалов ОЦК, где Φ , ϕ 1 и ϕ 2 2 2 2 2 2 2 2 обозначение.[30] Основными текстурными волокнами BCC материалов являются γ -волокно (111 || ND), α -волокно (110 || RD), η -волокно (001 || RD), ζ -волокно (110 || ND) и ε -волокно (110 || TD), а основными компонентами текстуры являются Goss, Brass, Cube, E1, E2 и F1, которые вложены в редуцированное пространство Эйлера, как видно в двух основных сечениях ФРО ϕ 2 = 0 град и ϕ 2 = 45 град. [31] В этой работе оба сечения ϕ 2 = 0 градусов и ϕ 2 = 45 градусов были построены для трех компонентов в состоянии после изготовления (этап 0) и во время выбранных этапов термообработки (этап 3 и этап 5).Контурные линии были нарисованы с шириной шага 2, а отдельные масштабные линейки были нанесены под соответствующими картами ODF, показывающими силу текстуры для отдельных шагов.
На рисунке 15 показаны карты ODF образца после механической обработки и во время термообработки. В образце после механической обработки (этап 0) наблюдались в основном компоненты текстуры Госса (G) и латуни (B) с максимальной прочностью текстуры 6,54. Волокно γ эволюционировало во время этапа 3, и произошло значительное снижение прочности текстуры (1.75) наблюдалось. Присутствие волокна γ вместе с компонентами текстуры E1, E2 и F стало очень заметным на этапе 5 с небольшим увеличением прочности текстуры (3.32). На рис. 16 показаны те же карты ODF для образца горячей штамповки. Образец горячей штамповки (шаг 0) содержал в основном компоненты текстуры Госса, латуни и куба (С) с максимальной прочностью текстуры 3,11. Волокно η было проявлено на шаге 3, но исчезло на шаге 5. Никаких других заметных текстурных волокон или компонентов на этапе 5 не наблюдалось.Прочность текстуры не претерпела существенных изменений после термообработки (2,43 и 3,9 для этапа 3 и этапа 5 соответственно). На рис. 17 показаны те же карты ODF для образца холодной ротационной штамповки. В образце холодной ротационной штамповки наблюдались в основном компоненты текстуры Госса и Куба с максимальной прочностью текстуры 9,6 (Этап 0). После термической обработки компоненты Госса и Куба были сохранены, но на этапе 3, по-видимому, не образовались волокна текстуры, что привело к резкому снижению прочности текстуры до 2.37. Гибридное волокно между компонентами текстуры Брасса и Госса наблюдалось на этапе 5 без изменения прочности текстуры (2,44 на этапе 5). Важно отметить, что волокно γ представляет собой волокно с характерной текстурой в рулонном материале BCC.
[31] В этом исследовании волокно γ наблюдалось только после термообработки образца после механической обработки (этап 5 на рисунке 15). Отсутствие волокна γ , особенно в горячештампованных и холодноштампованных образцах, может быть связано с деформацией, возникшей во время операции ковки с последующей термической обработкой.
Влияние выбранных этапов термообработки на эволюцию текстуры обработанных образцов стали
Рис. 16Влияние выбранных этапов термообработки на эволюцию текстуры горячекованых образцов стали избранные этапы термической обработки для изменения текстуры образцов холоднокованой стали
Текстура ОЦК была видна во всех трех заводских компонентах, но она была замаскирована во время термообработки из-за мартенситного превращения.Это ясно видно из рисунков 15–17. В целом было признано, что динамическая рекристаллизация была ответственна за ослабление текстуры, и то же самое наблюдалось для горячештампованного образца (максимальная прочность текстуры ~ 3,1 MUD). Термическая обработка привела к незначительному изменению доли рекристаллизованных зерен в горячештампованном образце без изменения текстуры слабой деформации (максимальная прочность текстуры ~ 3,9 MUD). Точно так же образец после механической обработки показал среднюю прочность текстуры (максимальная прочность текстуры ~ 6.5 МР), который снова уменьшился за счет рекристаллизации при термообработке (максимальная прочность текстуры ~ 3,3 МР). С другой стороны, образец холодной ротационной штамповки показал очень сильную текстуру деформации (максимальная прочность текстуры ~ 9,6 MUD) из-за полного отсутствия динамической рекристаллизации. После термической обработки зерна значительно рекристаллизовались, что привело к значительному ослаблению текстуры (максимальная прочность текстуры ~ 2,4 MUD). Здесь следует отметить, что независимо от производственных маршрутов, отпущенная мартенситная микроструктура маскировала развитую текстуру в термообработанных компонентах, что приводило к почти одинаковой прочности текстуры (максимальная прочность текстуры ~ 2.
от 4 до 3,9 MUD).
На рисунке 18 показано влияние этапов термообработки на среднюю твердость, полученную всеми тремя способами производства. Образцы после механической обработки и холодной штамповки (Этап 0) имели схожую перлитно-ферритную микроструктуру, однако упрочнение в образце холодной штамповки привело к меньшему эффективному размеру зерна и, следовательно, более высокой средней твердости 233 HV по сравнению с твердостью 155 HV. образца после механической обработки. Горячештампованный образец (Этап 0) с бейнитно-ферритной микроструктурой показал значительно более высокую твердость 296 HV.Эта разница в твердости была сведена к минимуму во время нормализации (Этап 1), где горячештампованный образец показал незначительное снижение средней твердости до 284 HV, но образцы после механической обработки и холодной ротационной штамповки показали значительное увеличение средней твердости, 294 и 309 HV соответственно. Это связано с изменением микроструктуры с перлитно-ферритной на бейнитно-ферритную. Во время отжига (этап 2) внутреннее напряжение было снято, а средняя твердость всех трех образцов уменьшилась до диапазона от 219 до 232 HV.После закалки с последующим ОК (этап 3) микроструктура трансформировалась в гораздо более твердую мартенситную фазу с уменьшением эффективного размера зерна, что привело к последующему увеличению средней твердости до диапазона от 423 до 450 HV. Эта высокая твердость сохранялась до конца термической обработки (от 415 до 459 HV, наблюдаемая на этапах 4 и 5), хотя образование отпущенной мартенситной микроструктуры на этапе 5 несколько снижало средние значения твердости. Следует отметить, что образцы после механической обработки, горячей штамповки и холодной ротационной штамповки показали эффективный размер зерна ~ 3.36, ~ 3,1 и ~ 3,06 мкм м соответственно, а после термообработки соответствующим образом наблюдалась их конечная твердость (440, 423 и 417 HV соответственно), что свидетельствует о применимости зависимости Холла-Петча. Подобное поведение наблюдалось исследователями в других местах.
[20,21] Можно сделать вывод, что мартенситное превращение и улучшенная микроструктура вместе улучшали твердость компонентов после термической обработки.
Влияние этапов термической обработки на среднюю твердость, полученную при различных производственных процессах
Влияние термической обработки на механические свойства
На рисунке 19 показано поведение при растяжении компонентов в исходном состоянии до (этап 0) и после (этап 0). Шаг 5) термическая обработка.Было обнаружено, что деформация одинакова для всех испытаний на растяжение в зависимости от состояния материала, что указывает на хорошую повторяемость свойств на растяжение и однородность материала. Наблюдалась заметная разница между напряженно-деформированным поведением как горячештампованных, так и холодноштампованных образцов. Кривые напряжение-деформация показали типичную постепенную текучесть, но разные значения YS и UTS. Образцы холодной штамповки показали более высокий срок службы из-за относительно более высокого деформационного упрочнения, тогда как более высокая пластичность образцов горячей штамповки привела к более высокому показателю UTS. После термической обработки закаленный и отпущенный мартенсит привел к сравнимым характеристикам напряжения и деформации и увеличению значений YS и UTS независимо от производственных процессов. Считалось, что это связано с измельчением зерна и последующим увеличением твердости. На рисунке 20 представлены средние значения YS и UTS для трех компонентов в состоянии после их изготовления до и после термообработки. Более крупнозернистая структура и меньшая твердость образца после механической обработки привели к значительно более высоким значениям YS и UTS, чем образец, полученный методом холодной штамповки.Термическая обработка привела к одинаковым YS и UTS как для образцов после механической обработки, так и для образцов холодной штамповки, что было связано с их аналогичной мартенситной микроструктурой после отпуска и сопоставимой твердостью. Горячештампованный образец показал немного другое поведение при растяжении, , т.е. ., самый низкий предел текучести, но самый высокий предел текучести, из-за его более высокой пластичности по сравнению с другими образцами.
После термической обработки в горячештампованном образце наблюдалось значительное увеличение YS, но незначительное увеличение UTS, что можно объяснить улучшенной микроструктурой, более высокой твердостью и улучшенным потоком зерна.
Поведение при растяжении ( a ) после механической обработки, ( b , c ) горячей штамповки и ( d , e ) после холодной ротации для вращения.
Рис. 20Значения среднего предела текучести (YS) и предела прочности при растяжении (UTS), демонстрирующие влияние термической обработки на различных производственных маршрутах
На рисунке 21 показаны усталостные свойства этих компонентов в состоянии после их изготовления до и после термической обработки.Усталостная долговечность каждого испытательного образца была нанесена на кривую S-N, а затем была определена тенденция (показанная пунктирной линией) для каждого производственного маршрута, чтобы понять изменение усталостного поведения до и после термообработки. Следует отметить, что большинство усталостных образцов разрушились до достижения предела усталостного цикла, однако несколько образцов из технологических маршрутов механической обработки и горячей штамповки достигли предела износа (, т.е. . черными пунктирными кружками).Как и ожидалось, термическая обработка привела к увеличению усталостной долговечности для всех трех производственных маршрутов из-за улучшения микроструктуры. После термической обработки образец после механической обработки показал самую высокую усталостную долговечность, за которой следовали образцы, полученные как горячей штамповкой, так и холодной ротационной штамповкой. В частности, образец холодной ротационной штамповки показал существенно высокую усталостную прочность (от 750 до 1000 МПа) со значительным улучшением усталостной долговечности после термической обработки.
Усталостное поведение образцов после механической обработки, горячей и холодной штамповки до и после термической обработки (образцы биения показаны черными пунктирными кружками)
Процесс многостадийной холодной штамповки для изготовления Высокопрочный входной вал с одним корпусом Материалы
(Базель). 2021 февраль; 14(3): 532.
Young Hoon Moon
2 Факультет машиностроения, Пусанский национальный университет, Пусан 46241, Корея; rk.ca.nasup@noomhy
2 Факультет машиностроения, Пусанский национальный университет, Пусан 46241, Корея; rk.ca.nasup@noomhyПоступила в редакцию 29 декабря 2020 г.; Принято 18 января 2021 г.
Лицензиат MDPI, Базель, Швейцария. Эта статья находится в открытом доступе и распространяется на условиях лицензии Creative Commons Attribution (CC BY) (http://creativecommons.org/licenses/by/4.0/).Abstract
Разработан многоэтапный процесс холодной штамповки, дополненный анализом методом конечных элементов (МКЭ) для изготовления высокопрочного однокорпусного входного вала с длинным корпусом и без отдельных частей. МКЭ показал, что однокорпусной входной вал изготовлен без дефектов и изломов. Эксперименты, такие как испытания на растяжение, твердость, кручение и усталость, а также определение микроструктуры, были проведены для сравнения свойств входного вала, изготовленного предлагаемым способом, со свойствами, полученными с использованием процесса механической обработки. Предел прочности при растяжении увеличился на 50%, а крутящий момент увеличился на 100 Нм, что подтверждает, что входной вал, изготовленный с использованием предлагаемого процесса, превосходит вал, обработанный с использованием процесса механической обработки. Таким образом, это исследование обеспечивает проверку концепции проектирования и разработки многоэтапного процесса холодной штамповки для изготовления однокорпусного входного вала с улучшенными механическими свойствами и скоростью извлечения материала.
Ключевые слова: входной вал , многостадийный процесс холодной штамповки, термоусадочная посадка, испытание на кручение, испытание на усталость
1.Введение
Различные автомобильные детали изготавливаются несколькими способами. Среди них изделия, изготовленные механической обработкой, имеют высокоточные размерную форму и состояние поверхности. Однако у этого метода есть несколько проблем, таких как низкая эффективность материала и неэффективность метода удаления стружки. Следовательно, автомобильная промышленность в настоящее время сосредоточена на замене процесса механической обработки процессом формовки металла для получения более высоких механических свойств, производительности и восстановления материала [1].
Первичный вал является важной автомобильной частью системы рулевого управления с электроприводом (MDPS). Его основная функция заключается в передаче движущей силы и крутящего момента на карданный шарнир. Следовательно, он требует превосходных механических свойств и геометрических допусков. Как правило, первичный вал изготавливается механической обработкой, так как его длина превышает 200 мм и он имеет сложную форму. Другой процесс изготовления входного вала включает отдельное изготовление его верхней и нижней частей методом холодной штамповки с последующим их соединением.Однако эти процессы не могли обеспечить требуемый геометрический допуск и избежать дефектов, таких как выпадение и сборка.
Ковка неуклонно набирает обороты в качестве основного процесса формовки металла, поскольку его параметры обработки, такие как рабочая температура и окружающая среда, могут быть отрегулированы для получения требуемых свойств материала. В частности, холодная штамповка, выполняемая при температуре ниже температуры рекристаллизации, имеет превосходную точность размеров и обеспечивает превосходные механические свойства.Это связано с дислокациями, генерируемыми высоким напряжением течения. Однако это высокое напряжение текучести требует высокой нагрузки, и можно изготовить лишь ограниченное разнообразие форм. Следовательно, ранее использовался процесс холодной ковки или в сочетании с горячей ковкой [2,3,4,5,6]. Фуджикава и др. В работе [7] описан метод сочетания горячей и холодной штамповки для изготовления ШРУСов и шлицевых валов для автомобилей. Используя эту комбинацию, можно легко изготавливать сложные и высоконагруженные изделия.Однако добавление термической обработки и обработки травлением в процесс делает его сложным и дорогим. Следовательно, важно исследовать другие методы, сохраняющие простоту и экономичность процесса.
Многоэтапная холодная ковка без термической обработки применялась исследователями. Этот процесс распределяет нагрузку и повышает точность формы. Панг и др. [8] применили многоэтапную холодную ковку для изготовления полых длинных валов силовых передач.Ку и др. [9] успешно заменили традиционную многоступенчатую теплую ковку многоступенчатой холодной ковкой для изготовления шарниров равных угловых скоростей. Изготовленные изделия показали отличные механические свойства. Таким образом, многоступенчатая холодная штамповка может быть основным кандидатом для эффективного изготовления входных валов. Кроме того, важно спрогнозировать результаты процесса и конструкции штампа, чтобы увеличить срок службы штампа при проектировании процесса. Обычно это выполняется с помощью анализа методом конечных элементов (FEA).McCormack и Monaghan [10] предложили наиболее подходящую конструкцию штампа для изготовления болтов с шестигранной головкой, проанализировав результаты формования по отношению к углу головки с помощью FEA. Соранансри и др. [11] разработали матрицу с соответствующей термоусадочной посадкой, которая использовалась для увеличения срока службы матрицы при изготовлении конических зубчатых колес методом ковки.
При проектировании процесса прогнозирование внутреннего разрушения продукта также является важным фактором. Для процесса объемного формования внутреннее разрушение можно предсказать с помощью уравнения вязкого разрушения.Кокрофт и Латам [12] предложили уравнение вязкого разрушения для пластической деформации как функцию максимального основного напряжения. Чен и др. [13] и Oh et al. [14] предсказал вязкое разрушение в процессах экструзии и волочения путем объединения уравнения вязкого разрушения Кокрофта-Латама с МКЭ. Вязкое разрушение происходит, когда гидростатическое напряжение (среднее напряжение) неотрицательно или критическое значение повреждения превышается в центре материала [15,16]. Уравнение Кокрофта-Латама [12] и уравнения гидростатики могут предсказывать внутренние трещины, такие как шевронные трещины, появляющиеся в длинных изделиях.Ли и др. [17,18] синтетически изготовили высокопрочный болт, удлиненный в направлении экструзии, и использовали многоэтапный процесс холодной штамповки для улучшения его механических свойств с термоусадкой и уравнением вязкого разрушения. Таким образом, многостадийная холодная штамповка является наиболее подходящим процессом для изготовления высокопрочных изделий с высокой производительностью и коэффициентом восстановления материала. Следовательно, важно спроектировать штамп с подходящей горячей посадкой, чтобы увеличить срок службы штампа, используя уравнение пластического разрушения для прогнозирования внутренних дефектов продукта.
Это исследование обеспечивает проверку концепции многоэтапного процесса холодной штамповки для изготовления высокопрочных однокорпусных входных валов большой длины без отдельных деталей. Процесс состоит из шести этапов и был разработан с использованием моделирования методом конечных элементов. Значение термоусадочной посадки было скорректировано для увеличения срока службы штампа и прогнозирования разрушения штампа. Уравнение Кокрофта-Латама и анализ гидростатического напряжения использовались для прогнозирования вязкого разрушения. На основании анализа были изготовлены штампы и проведена ковка. Были проведены различные эксперименты для сравнения этого вала с валом, полученным с использованием обычного процесса механической обработки. Для подтверждения улучшения механических свойств были проведены испытания на растяжение и твердость. Кроме того, для сравнения долговечности были проведены испытания на кручение и усталость. Дифракция обратного рассеяния электронов (EBSD) также использовалась для характеристики микроструктурного преобразования в материале. Кроме того, МКЭ использовался для сравнения этих результатов с результатами процесса, при котором верхняя и нижняя части изготавливаются отдельно.Результаты анализа сравнивали на основе предыдущих экспериментальных результатов.
2. Материалы и методы
2.1. В исследовании использовалась штамповка стали
SWRCCh55F, которая в основном используется в различных автомобильных деталях, производства POSCO. Его проанализированный химический состав указан в . Многоэтапная ковка была разработана для работы в шесть этапов для производства цельного изделия. Размер сырья определялся исходя из требуемых размеров конечного продукта. Диаметр сырья был установлен на 22.5 мм по диаметру корпуса конечного изделия. Длина исходного материала была определена равной 176,7 мм. В этом случае может возникнуть бочкообразность из-за большой длины изделия. Чтобы предотвратить бочкообразность, сначала выдавливали нижнюю часть длины в три этапа, а затем в два этапа выдавливали верхнюю часть. Рассчитано, что коэффициент уменьшения площади составляет 47% и 45% в верхней и нижней части соответственно. Эти значения меньше, чем коэффициент уменьшения общего процесса экструзии, который составляет 75% [19].Окончательная схема процесса показана на . Шаг 1 является предварительным этапом для нижней экструзии. Шаги 2 и 3 предназначены для нижней экструзии, а шаги 4 и 5 — для верхней экструзии. Последний шаг, шаг 6, состоит из формирования многоугольников в верхней части и сплайнов в нижней части. показана экспериментальная установка шестиступенчатого формовочного станка (HBF-416), принадлежащая SUNG JIN FO-MA INC, и штампы, использованные в исследовании.
Скорость удара составляла 140 мм/с.
Схема процесса многоэтапной холодной штамповки.
Экспериментальная установка для многоступенчатой холодной штамповки и используемые штампы.
Таблица 1
Химический состав сырья.
Материал | Химический состав (%) | Swrch 45F | C | SI | MN | S | S | |||||
---|---|---|---|---|---|---|---|---|---|---|---|---|
0.![]() | 0.1-0.35 | 0,6–0,9 | 0,030 Макс. | 0,035 Макс. |
2.2. Механические характеристики
Испытания на растяжение были проведены для изучения изменений механических свойств, таких как предел прочности при растяжении (UTS) и относительное удлинение. Образец был получен из шлицевой части входного вала в нижней части, и размеры образца в соответствии со стандартом ASTM (E8/E8M) показаны в [20]. Испытания на растяжение были проведены в трех повторностях с использованием Zwick-Z250N с предварительной нагрузкой 5 МПа, постоянной скоростью траверсы 10 МПа/с по модулю упругости и пределом текучести при комнатной температуре.Для сравнения использовались свойства валов, изготовленных традиционным способом. Твердость входного вала измеряли с помощью микротвердомера Vickers (Matsuzawa, Akita Pref, Япония) (AMT-X7FS, тип B, нагрузка: 29,4 Н (300 гс)) в месте, показанном на b.
( a ) Размер образца для испытания на растяжение, ( b ) точки сбора данных для испытания на микротвердость по Виккерсу и ( c ) размеры образца для испытания на усталость.
Испытания на кручение и усталость были проведены для изучения улучшения прочности на кручение и усталости соответственно.Испытание на кручение проводилось в двух различных условиях с использованием машины для испытания на кручение (MET-100H) (Cowon, Seoul, Korea) при постоянной скорости 100°/мин при комнатной температуре. В одном состоянии образец испытывали до разрушения, а в другом — до момента 200 Нм. Установленный крутящий момент 200 Нм учитывает запас прочности 100 Нм, что является максимальным крутящим моментом, получаемым МСПД [21]. Для сравнения деформации использовали 3D-лазерный сканер (DS-3040, диапазон погрешности: 6 мкм). Испытания на усталость под осевой нагрузкой проводились с использованием машины для испытаний на усталость (ACEONE, Инчхон, Корея) при комнатной температуре для измерения предела выносливости обработанных и кованых изделий. c показаны размеры образцов, использованных в испытании на усталость, которые были изготовлены из обработанного вала в соответствии со стандартом ASTM (D7791-17) [22]. Условия теста указаны в . Предел выносливости измерялся на основе 1 000 000 циклов, что является пределом выносливости обычной стали [23, 24]. Кроме того, анализ испытаний на усталость был выполнен с использованием ANSYS (Ansys, Canonsburg, PA, USA) с использованием результатов испытаний на растяжение и усталость.
Таблица 2
Экспериментальные условия для испытания на усталость.

Продукт был разрезан в плоскости нормального направления (ND) для проверки на наличие внутренних дефектов и повреждений, а также для сравнения анализов и экспериментальных результатов. Для наблюдения за характеристиками течения металла образец монтировали в горячем состоянии и механически полировали до 1 мкм с использованием бумаги SiC и алмазных суспензий. Проведено макротравление (нитал 10%). Места наблюдения были установлены на четыре точки в конечном продукте с использованием стереомикроскопа (Carl Zeiss, Оберкоэн, Германия) (SteREO Discovery.V20) при 4,7-кратном увеличении.
Эволюцию микроструктуры наблюдали с помощью EBSD, оксфордской симметрии с JEOL (JSM-7900F) (JEOL Ltd, Токио, Япония) [25,26]. Образцы монтировались в горячем состоянии, механически полировались на бумаге SiC и доводились до зеркального блеска алмазными суспензиями (размером до 0,25 мкм) и коллоидным кремнеземом. Условия измерения EBSD: ускоренное напряжение 15 кВ, ток зонда 15 нА, наклон образца 70°, размер шага сканирования 0,08 мкм, площадь измерения 79. 4 × 56,9 мкм 2 . Карта средней разориентации ядра (KAM) и границы зерна (GB) была получена из программы постобработки (Aztec, CHANNEL 5) (2.0, Oxford Instruments, Abingdon-on-Thames, England).
3. Анализ методом конечных элементов (МКЭ)
Моделирование с использованием программы МКЭ необходимо для обеспечения надлежащего проектирования нового процесса. Коммерческие программы МКЭ DEFORM-2D (10.0, Scientific Forming Technologies Corporation, Огайо, США) и -3D (программа для МКЭ жесткого пластика) (10.0, Scientific Forming Technologies Corporation, Огайо, США) использовались для прогнозирования дефектов и повреждений изделий и штампов. DEFORM-2D применялся для моделирования шагов с 1 по 5, поскольку деталь, изготовленная на этих этапах, имеет осесимметричную структуру. DEFORM-3D был применен к шагу 6, потому что неосесимметричная структура и сложная форма изготовленной детали включали многоугольник и сплайн. Он был построен как модель на четверть с учетом его симметричной формы. Условия анализа указаны в .К кулоновскому трению прибавляли коэффициент трения между материалом и матрицей [15]. Было проведено испытание на сжатие, чтобы получить механические свойства для FEA и значение критического повреждения для прогнозирования вязкого разрушения [27]. Испытание проводили на универсальной испытательной машине (Zwick-Z205N) (Zwick Roell Group, Ульм, Германия) с постоянной скоростью 0,05 мм/с при комнатной температуре. На поверхность образца наносили смазку для уменьшения трения. Кривая напряжение-деформация, полученная в результате испытания на сжатие, применялась для моделирования вязкого разрушения.Критическое значение повреждения 519 МПа было получено из уравнения вязкого разрушения, т.е. уравнения Кокрофта-Латама, как показано на рис. Прогноз вязкого разрушения и распределение гидростатического напряжения показаны на рис. Анализ вязкого разрушения показал, что критическая величина повреждения была равномерно распределена при 519 МПа для всех процессов. Кроме того, в изделии распределялось отрицательное гидростатическое напряжение, которое не должно иметь дефектов во всех процессах.
( a ) Подогнанная кривая текучести «напряжение-деформация», полученная в результате испытания на сжатие, ( b ) результаты испытаний на осадку для различных уменьшений высоты.
Численные результаты прогнозирования ( a ) вязкого разрушения и ( b ) гидростатического напряжения (среднее напряжение).
Таблица 3
Условия процесса для FEA.
Процесс Условия | Значение |
---|---|
Усталость | 1 000 000 циклов |
Частота | |
10 HZ | |
Коэффициент напряжения (Σ мин / Σ Max ) | −1 |
Амплитуда напряжения обрабатываемого изделия | 200–300 МПа |
Амплитуда напряжения кованого изделия | 300–500 МПа |
Процесс Условия | Значение | ||
---|---|---|---|
симметричная модель деформации-2D | Symmetry | ||
Симметричная модель деформации-3D | квартал (90 °) | ||
Начальный диаметр образца | 22.![]() | ||
Начальный образец Длина | 176,7 мм | ||
трение | μ = 0,055 | ||
Punch Velocity | 140 мм / с | ||
Температура образца | 20 ° C | ||
Температура штампа | 20 °C | ||
Температура окружающей среды | 20 °C |
Прогноз разрушения штампа важен при проектировании штампа и технологических процессов. Как правило, штамп с подходящей термоусадочной посадкой может увеличить срок службы штампа и предотвратить его разрушение. Важно проверить максимальное главное напряжение, так как разрушение в основном вызвано повторными растягивающими напряжениями [28,29]. Матрица, используемая в основном в промышленности, состоит из вставки, натяжного кольца и корпуса для эффективного использования. Вставка, расположенная внутри матрицы, имеет наибольшее распределение нагрузки. Кольцо напряжения установлено в центре матрицы, чтобы предотвратить разрушение вкладыша из-за сжимающих напряжений.Гильза расположена снаружи штампа, чтобы дополнить общую нагрузку. В этом исследовании материалы, использованные для вставки, натяжного кольца и корпуса, представляли собой карбид вольфрама (WC), AISI h23 и AISI 4140 соответственно. Подробные механические свойства каждого компонента матрицы перечислены в .
Таблица 4
Свойства материала ковочных штампов.
8Материал удивления | эластичный модуль | 9040 |
---|---|---|
468 GPA | 2683 MPA | 2683 MPA |
Стресс-кольцо (AISI H23) | 215 GPA | 1380 МПа |
Корпус (AISI 4140) | 205 ГПа | 1110 МПа |
Важно подобрать подходящую термоусадочную посадку, поскольку матрица может быть усилена в зависимости от термоусадочной посадки нагрузочного кольца. Был проведен анализ вставной матрицы, как показано на а. Предел текучести штампа вставки был менее 2683 МПа, но он имел относительно высокое значение на этапах 5 и 6. Этап 6, который характеризуется высоким абсолютным напряжением, использовался для подбора подходящей горячей посадки. Как показано на b, основное напряжение вставки и нагрузочного кольца распределяется равномерно, когда термоусадочная посадка находится в диапазоне 0,3–0,7%. Показано, что соответствующая термоусадочная посадка может предотвратить разрушение штампа и увеличить срок службы штампа. В этом исследовании 0.Была применена 5% термоусадочная посадка.
Численные результаты ( a ) распределения максимального главного напряжения, полученные в результате анализа напряжения штампа и ( b ) сравнения напряжения штампа между различными термоусадочными посадками.
4. Результаты и обсуждение
На основе МКЭ была изготовлена и установлена на форму штамп с усадкой 0,5%, как показано ранее на рис. Изделие разрезали вдоль плоскости ND, чтобы наблюдать за поверхностью и внутренней частью. Мы подтвердили отсутствие повреждений на поверхности и внутри изделия, как показано на рис.Течение металла наблюдалось без каких-либо дефектов в силу его симметрии и плотности, а также без изломов и разрывов, как показано на в. показывает скорость извлечения материала в процессах. Коэффициенты восстановления обработанных и кованых изделий составляют 31,3% и 80,3% соответственно. Скорость восстановления материала кованого изделия примерно в 2,56 раза выше, чем при обычном процессе механической обработки. Экспериментальные и численные результаты подтвердили, что предложенный процесс успешно изготовил однокорпусный входной вал с улучшенной скоростью извлечения материала и без дефектов.
Вид на ( a ) поверхность изделия, ( b ) внутреннюю часть изделия и ( c ) поток металла изготовленного изделия.
Таблица 5
Сравнение степени извлечения материала между процессами.
Обработанный входной вал | 9040 | |||
---|---|---|---|---|
9024 | 9049 | 9048 | 70248 | 70248 3 |
180 248 | 70257 | |||
Окончательный объем продукта (мм 3 ) | 56 430 | 56 430 | ||
Степень извлечения материала (%) | 31.![]() | 80,3 |
Как видно из кривых напряжение-деформация в , UTS обработанного изделия составил 500 МПа; и наоборот, у поковки 750 МПа. Таким образом, многоэтапный процесс холодной штамповки может производить входной вал с более высокой прочностью, чем при механической обработке, что подтверждается улучшением UTS примерно на 50%. Как показано на рисунке, твердость кованого изделия улучшилась примерно на 45% по сравнению с обработанными изделиями. Полигональные (№1) и сплайновые (№5) области с высоким эффектом формообразования демонстрируют относительно высокие значения твердости.Исходя из этих результатов, предложенный многоэтапный процесс холодной штамповки позволяет изготавливать однокорпусные входные валы с улучшенными механическими свойствами.
Сравнение результатов испытаний на растяжение кованых и обработанных изделий.
( a ) Контурные графики и ( b ) сравнительный график результатов испытаний на твердость по Виккерсу для обработанных и кованых изделий.
Испытание на кручение проводилось до тех пор, пока в изделии не произошло разрушение, как показано на а. Крутящий момент обработанного изделия составил 125, 215 и 230 Н·м при углах закручивания 10°, 20° и 30° соответственно, а кованого изделия – 225, 320 и 330 Н·м соответственно.Крутящий момент кованого изделия был примерно на 100 Нм выше, чем у обработанного изделия при том же угле закручивания. Крутящий момент 200 Нм применялся для проверки изменения размеров входного вала, и результаты были численно подтверждены с помощью 3D-лазерного сканера (Laser Design Inc., Миннеаполис, Миннесота, США). Как показано на б, максимальная деформация обработанного изделия при скручивании составила 0,6096 мм, а кованого – 0,2470 мм. При одинаковой нагрузке деформация обработанного изделия составила примерно 2.в 47 раз выше, чем у кованого изделия. Как и результаты испытаний на растяжение и твердость, входной вал, изготовленный методом ковки, имеет более высокие свойства при кручении и сопротивление деформации кручению, чем вал, изготовленный с использованием процесса механической обработки.
( a ) Кривые крутящий момент-угол для сравнения обработанных и кованых изделий по результатам испытания на кручение и ( b ) результаты трехмерного сканирования, полученные до и после испытания на кручение.
Результаты испытаний на усталость показаны на a.Предел выносливости обработанного изделия составил 200 МПа, кованого – 300 МПа, что примерно на 50 % выше. Результаты испытаний на усталость были применены для дополнительного МКЭ для анализа усталостной долговечности при крутящем моменте 100 Нм, который в основном поступает от MDPS и распределяется в направлении экструзии полигональной области. Как показано в b, мы подтвердили, что разрушение происходит при измерении менее 1000 циклов в положении А обработанного изделия, тогда как на кованом изделии разрушение не происходило при 1 000 000 циклов.Для увеличения усталостной долговечности обработанного входного вала в положении А следует применить дополнительную высокочастотную термообработку. Эти результаты показали, что предел выносливости кованого входного вала увеличился на 100 МПа по сравнению с механически обработанным входным валом, что значительно улучшило усталостную долговечность без дополнительного процесса термообработки.
( a ) Сравнение обработанных и кованых изделий на основе их амплитуды напряжения – кривой количества циклов, полученной в результате испытания на усталость, и ( b ) результатов анализа усталости.
показывает карту контрастности полосы, карту KAM и карту GB сырья и кованых изделий. Сырье было получено путем горячей прокатки, и образец демонстрирует типичные характеристики среднеуглеродистой стали, такие как ферритная и перлитная микроструктуры (а). Для образца, деформированного методом многостадийной холодной штамповки, зерна были вытянуты в направлении экструзии (г). KAM представляет собой среднее значение разностей локальной ориентации между отдельными точками измерения и соседними точками измерения. Величина КАМ увеличивается с увеличением плотности дислокаций или накопленной в образце энергии внутренних деформаций. Средние значения КАМ сырья и поковок составили 0,28 (б) и 0,91 (д) соответственно. Для кованых изделий среднее значение увеличивается на 225 %, что свидетельствует о накоплении внутренней энергии деформации и плотности дислокаций. Если угол разориентации ГБ больше 15°, он называется большеугловой границей зерна (HAGBs, синяя линия), а если он меньше 15°, он называется малоугловой границей зерна (LAGBs). , красная (2–5°) и зеленая линия (5–15°).Почти все зерна сырья представляли собой равноосные зерна феррита, окруженные HAGB (в). Зерно кованого изделия было разделено образованием LAGB и HAGB из-за большой пластической деформации (f).
Сравнение карты контрастности полос ( a , d ), карты KAM ( b , e ) и карты GB ( c , f ) LAGB2 ( c , f ) < 5°, красные линии и 5° ≤ θ < 15°, зеленые линии) и HAGB (15° ≤ θ , синие линии): ( a – c ) сырье и ( d – ф ) кованое изделие.
показывает долю площади (длина угла разориентации, деленная на измеренную площадь, мкм/мкм 2 ), изменение LAGB и HAGB во время деформации для количественного сравнения [30,31]. Значения фракций LAGBs (2–15°) и HAGBs (15–180°) сырья составляли 0,09 и 0,16 мкм -1 соответственно, а кованого изделия — 2,89 и 0,64 мкм -1 , соответственно. Это подтвердило, что значение фракции кованого продукта было выше, чем у сырья.По мнению ряда исследователей [32, 33], за последовательностью измельчения зерен следует накопление дислокаций, образование LAGB, увеличение углов разориентации, поглощение дислокаций на HAGB и установление стационарного состояния. Следовательно, исходя из этих результатов EBSD, многоэтапный процесс холодной штамповки может быть эффективным для измельчения зерна входных валов и эффективного производства высокопрочных изделий с большим количеством LAGB и HAGB.
Сравнение площадной доли углов разориентации для сырья и поковки.
Было проведено дополнительное численное исследование, как показано на для сравнения отдельно изготовленного первичного вала, состоящего из верхней и нижней частей, и однокорпусного входного вала. Был разработан многоэтапный процесс холодной штамповки, и применялось такое же напряжение текучести материала (а). Судя по результатам, отдельный процесс входного вала может производить продукт без дефектов. Для раздельного производства верхняя и нижняя части были обработаны для сборки, а затем соединены штифтом (AISI D2) после процесса ковки.Мы использовали численный тест на кручение для исследования и сравнения кривых момент-угол процессов. По результатам, полученным от изделия механической обработки, наблюдалась разница между численными и экспериментальными результатами для начала испытаний, как показано на рис. Общая тенденция моделирования вполне соответствовала экспериментальному результату. Таким образом, условие моделирования считается приемлемым для испытания на кручение. Мы заметили, что значение крутящего момента отдельно изготовленного входного вала было выше, чем у обработанного входного вала, и ниже, чем у однокорпусного входного вала. В результате было подтверждено, что однокорпусный входной вал, изготовленный с помощью многоэтапного процесса холодной штамповки, превосходит существующие процессы с точки зрения механических свойств, скорости извлечения материала и производительности. Для улучшения расходуемости и масштабируемости могут быть проведены дальнейшие исследования с использованием легких материалов для улучшения реализации процесса [34].
Численный анализ процесса отдельного входного вала и сравнение кривых крутящий момент-угол, полученных в результате численного и экспериментального испытаний на кручение.
5. Выводы
В данной статье был предложен многоэтапный процесс холодной штамповки для изготовления высокопрочного однокорпусного входного вала большой длины и высокой степени извлечения материала. По результатам анализа конечных элементов и экспериментальных данных процесс был успешно разработан, и однокорпусный входной вал может быть качественно изготовлен с высокой прочностью, твердостью, крутящим моментом и пределом выносливости. Были получены следующие выводы:
На основе анализа конечных элементов было предсказано, что однокорпусный входной вал не имеет внешних и внутренних дефектов с помощью уравнения Кокрофта–Латама и анализа гидростатического напряжения, и что срок службы штампа можно увеличить с помощью подходящей горячей посадки для предлагаемый процесс.Предлагаемый процесс имеет степень извлечения материала 80,3%, что в 2,56 раза выше, чем у обычного процесса механической обработки.
Были изготовлены численно спроектированные и проверенные штампы для многоступенчатой холодной штамповки, чтобы проверить их применение при изготовлении высокопрочного входного вала с одним корпусом. Однокорпусный первичный вал был успешно изготовлен без дефектов.
По результатам испытаний на растяжение и твердость механические свойства улучшились примерно на 45–50%, а долговечность, полученная по результатам испытаний на кручение и усталость, также увеличилась.Предлагаемый процесс может быть эффективным для измельчения зерна входных валов и эффективного производства высокопрочных изделий с большим количеством LAGB и HAGB.
Дополнительный МКЭ был успешно проведен для сравнения отдельно изготовленного входного вала, состоящего из верхней и нижней частей, и однокорпусного входного вала, изготовленного по предлагаемому процессу. Результаты подтвердили, что входной вал с одним корпусом превосходит входные валы, изготовленные по существующим технологиям, с точки зрения значения крутящего момента.
Вал первичный однокорпусный изготовлен из обычного металла СВРЧ55Ф. Легкие материалы, такие как алюминий или титан, все чаще применяются в некоторых частях электромобиля для уменьшения веса автомобиля и повышения энергоэффективности. Следовательно, легкие материалы могут применяться в процессе холодной штамповки для изготовления автомобильных деталей, таких как высокопрочный входной вал, для улучшения механических свойств и снижения веса автомобиля.
Благодарности
Работа выполнена при поддержке SUNG JIN FO-MA INC.Авторы также признательны Вун Хак Ли за проведение экспериментов.
Вклад авторов
Концептуализация, A.R.J. и С.К.Х.; методология, A.R.J. и С.К.Х.; программное обеспечение, A.R.J. и MSJ; курирование данных, A.R.J. и С.К.Л.; написание — подготовка первоначального проекта, A.R.J. и С.К.Х.; написание-обзор и редактирование, С.К.Х.; проверка и исследование, Y.H.M. Все авторы прочитали и согласились с опубликованной версией рукописи.
Финансирование
Это исследование было проведено при поддержке Корейского института промышленных технологий как «Разработка интеллектуальной корневой технологии с дополнительными модулями (KITECH EO-20-0017)».
Заявление о доступности данных
В ходе этого исследования были созданы или проанализированы новые данные. Обмен данными не применим к этой статье.
Конфликт интересов
Авторы заявляют об отсутствии конфликта интересов.
Сноски
Примечание издателя: MDPI остается нейтральным в отношении юрисдикционных претензий в опубликованных картах и институциональной принадлежности.
Литература
1. Ланге К. Некоторые аспекты развития холодной штамповки до высокотехнологичной прецизионной технологии.Дж. Матер. Процесс. Технол. 1992; 35: 245–257. doi: 10.1016/0924-0136(92)-I. [Перекрестная ссылка] [Академия Google]2. Юн Дж. К. Магистерская диссертация. Пусанский национальный университет; Пусан, Корея: 2004. Исследование процесса и конструкции штампа для процессов холодной штамповки сетчатой формы для цилиндрического зубчатого колеса с внутренним профилем кулачка. [Google Академия]3. Кнуст Дж., Подшус Ф., Стонис М., Беренс Б.А., Овер Мейер Л., Ульманн Г. Оптимизация заготовки для процессов горячей штамповки с использованием генетических алгоритмов. Междунар. Дж. Адв. Произв. Технол. 2016; 89: 1623–1634.doi: 10.1007/s00170-016-9209-9. [Перекрестная ссылка] [Академия Google]5. Чанг Ю.Л., Хун Ф.Ю., Луи Т.С. Новая инфракрасная термообработка алюминиевого сплава 7075 горячей штамповки: микроструктура и механические свойства. Материал. 2020;13:1177. doi: 10.


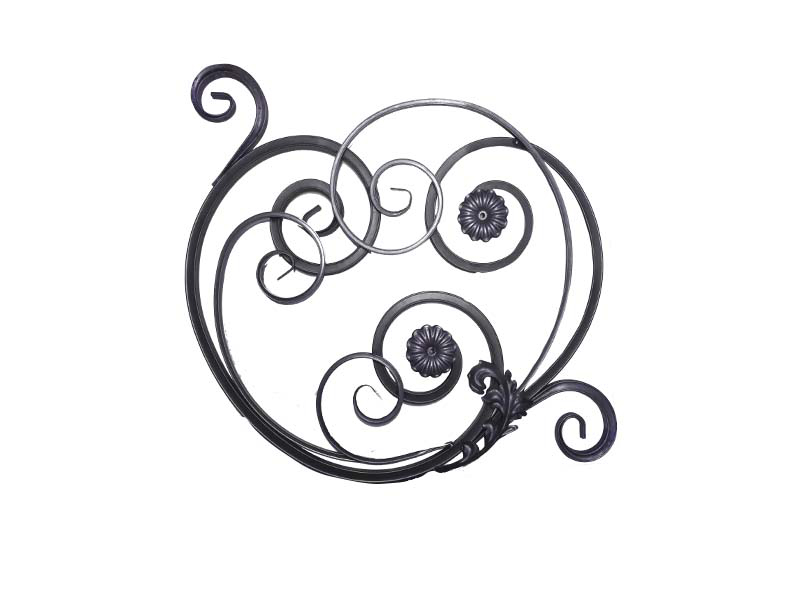

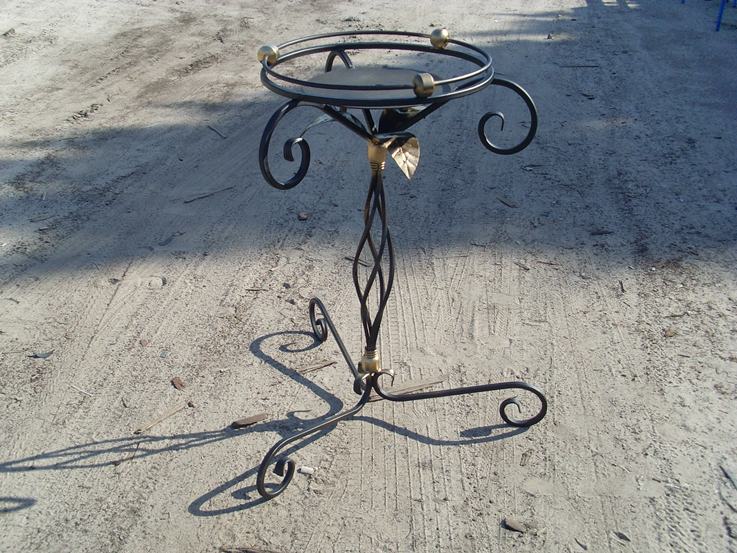

Forged vs.Литой алюминий | Queen City Forging
Существуют различия между кованым и литым материалом. Основное различие между ковкой и литьем заключается в том, что в процессе ковки материал заготовки не расплавляется для создания новой формы. При литье металл плавится и заливается или заливается в форму, изготовленную в форме желаемого изделия. При ковке деформация материала в твердой форме, часто путем удара молотком или прессованием материала, создает желаемую форму. Оба процесса имеют определенные преимущества, которые могут привести к тому, что один или другой будет использоваться для создания компонента в зависимости от стоимости и требований к использованию службы. Алюминий и алюминиевые сплавы подчиняются тем же металлургическим принципам, что и другие металлы, которые определяют, какой процесс обеспечивает преимущество для данного предмета конечного использования.
Когда металл плавится и производится отливка, может получиться изделие сложной формы, ограниченное только изготовлением формы и динамикой течения и затвердевания металла. Это позволяет литью экономно изготавливать компоненты с внутренними камерами и внешними элементами, что снижает количество последующих операций удаления металла, выполняемых для завершения готовой детали.Недостатком является возможность загрязнения в то время, когда металл находится в жидком состоянии из-за попадания в жидкость примесей. Образующиеся при плавке слитков и добавок примеси могут быть недостаточно отфильтрованы из жидкого металла при его перетекании в форму. Небольшие кусочки каналов, ведущих к форме, или сама форма также могут отслаиваться или ломаться, попадая в жидкость. Турбулентность при протекании жидкого металла через сложные камеры может привести к образованию пустот и внутренних, скрытых областей незаполнения. Ликвидация сплава, когда металл находится в жидкой форме, может привести к непостоянству свойств материала от одной области отливки к другой. Дефекты, такие как разрывы или трещины, могут образовываться, когда масса различных участков охлаждается с разной скоростью по мере затвердевания металла.
заключается в добавлении энергии деформации для дальнейшего уточнения и улучшения металлургии создаваемой формы. За счет приложения механической и термомеханической энергии деформации первоначально отлитые слитки алюминия формуются и переформовываются, изменяя внутреннюю микроструктуру.Любые включения или концентрации сплава диспергируются, а любые пустоты дробятся и устраняются. Энергия ковки вызывает рекристаллизацию микроструктуры, создавая повышенную прочность и прочность . Поковки обычно не могут производить такие сложные формы, как отливки. Это часто требует дополнительных отделочных операций, что увеличивает стоимость использования поковок по сравнению с отливками. Однако улучшенные свойства кованых изделий перевешивают проблемы стоимости, когда безопасность, надежность и стоимость отказа компонентов являются самыми большими проблемами.
Дополнительным преимуществом ковки является возможность формирования сплавов, консолидированных из порошков металлов и других добавок. Сплавы и матричные материалы этого типа производятся и консолидируются в виде порошков, поскольку составные элементы не могут быть успешно расплавлены и отлиты. Термомеханическая энергия часто является наиболее практичным средством консолидации порошков в твердую форму. Процессы деформации, такие как ковка, затем используются для дальнейшего придания этим материалам в твердом состоянии более полезных, почти чистых форм, что обеспечивает повышенную экономию при использовании этих более дорогих материалов.Таким образом, ковка обеспечивает способность и удобство использования материалов, которые обеспечивают свойства, которые будут соответствовать будущим задачам проектирования.
Кованые изделия будут предпочтительным выбором, когда компоненты должны обладать максимальными свойствами и долговечностью в эксплуатации, когда необходимо минимизировать вес и массу, а выход из строя может быть дорогостоящим или катастрофическим. Другие процессы стремятся заявить о «деформируемых свойствах», но только процесс ковки может последовательно и надежно их обеспечить.
Калькулятор холодной штамповки| Продукты и поставщики
Схема экспериментальной установки; 1 ± охлаждающая камера, 2 ± литейная форма (пластик), 3 ± ПЗС-камера и микроскоп, 4 ± компьютер.
A:-Faktor 495 кабели, Flachband- 502-, коаксиальный 502-, Long 576 Резисторы PTC 16, 104, 309 канал, 592 канал связи… … Spannungs- 69-, 456 Ubertragungs- керамический конденсатор 121 форма сердечника 127, 616, 626 Кирхгоффше … … анализ 19, 26 узловых компьютеров 484 узловых правил 9 …
… 19 -, блок электростанции L 18 -, температура и количество охлаждающей воды L 20 -, соотношение охлаждающей воды L … … Коэффициент проницаемости N 19 диафрагменная техника F 23 диатерм D 2 плотность D 45 H 1, B 46, W 14 уплотнения K 23 -, на статических поверхностях K 22 -, исполнения K 23 -, уплотнения контактов … … метров W 33 цифровые компьютеры Y 1 Y 9 …
Гора Рейн (2006а, С. 340) называет четыре формы мотивационного выхода: обучение оказывается (1) ненужным или (2) недействующим, (3) результат обучения не имеет безопасных последствий, (4) потенциальные последствия недостаточно важны или проявляются прискорбно. Но хотя укрупненная модель когнитивной мотивации может достаточно хорошо объяснить, почему люди выполняют определенное действие или пропускают его, она описывает человека как охлаждающего, приближающегося к компьютеру.
С ним выражается особая форма настройки ПК для достижения более высоких тактовых частот и, таким образом, повышения эффективности компьютера.… производство тепла неизбежно, так как вторичная последовательность этого перевооружения перехватывается дорогостоящими системами охлаждения, т.е. …
… явно указывает на то, что должники могут безоговорочно представлять себя в консультации в этой форме, потому что джентльмен … Примечательно, что упоминается так же мало, как «охлаждение компьютеров» после конкретных пожеланий или ожиданий должников спросить.
1995 г., он дал двум типам ненаправленную потребляемую энергию в виде тепла от компьютерных систем.Протекал с одной стороны через компьютеры с помощью охлаждающего воздуха, который вводился в ложные …
Под вежливо-эстетическими и романтическими идеалами под ними подразумеваются джентльмены и эгоисты, жестокие деспоты, фанатики и холодные компьютеры. … голландский для патологического Zwischenglied Schizophrenic of the Schizoiden с грубой многогранной схемой плесени в …
… машина 394 система координат механического интерфейса 740 связующая среда 382 соединительные средства 390 сопротивление сцепления 33, 36 размер зерна 376 корреляция измерение расхода 178, 194 корреляция компьютеры 195 Korrelogramm 401 Korrelogrammauswertung … … 347 шариковый винт 123 смазочно-охлаждающие жидкости 390 искусственный к … … угол 676 защелка 447 время ожидания 603, 608 координата ротора 684 форма канавки ротора 668 время прохождения …
…более 3500 сплавов черных и цветных металлов, а также калькуляторы метрического перевода и веса металла .
Добавить комментарий